In the ever-evolving landscape of materials science, few substances rival the versatility and performance of AlSi12 powder. This exceptional aluminum-silicon alloy powder, meticulously engineered with approximately 12% silicon, is transforming industries far and wide, from the high-performance demands of automotive manufacturing to the cutting-edge advancements in aerospace engineering.
But what exactly elevates AlSi12 powder to such a prominent position? And how can your business leverage its unique attributes to gain a competitive advantage in today’s demanding marketplace?
This comprehensive guide will delve deep into the remarkable properties and diverse applications of AlSi12 powder, illuminating its remarkable ability to enhance product performance, streamline manufacturing processes, and unlock a world of possibilities for innovation.
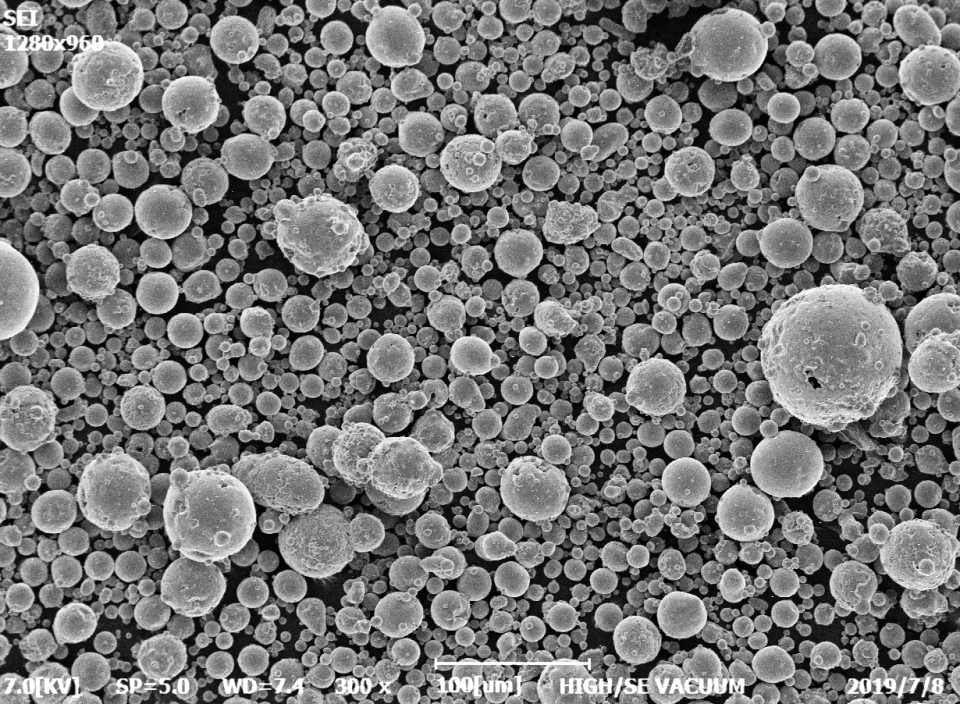
Understanding the AlSi12 Advantage: A Winning Combination of Properties
The unparalleled versatility of AlSi12 powder stems from its meticulously balanced composition, a harmonious blend of properties that makes it a superior choice compared to traditional materials:
- Exceptional Castability: The secret to AlSi12 powder’s exceptional castability lies in its fine particle size and spherical morphology. These characteristics, combined with its low melting point, contribute to exceptional flowability, allowing it to fill even the most intricate mold cavities with ease. This translates to superior castability, enabling manufacturers to produce complex shapes with intricate details and thin walls, significantly reducing the need for costly and time-consuming secondary machining operations.
- Impressive Strength and Ductility: A Powerful Synergy: Don’t let its lightweight nature fool you; AlSi12 powder punches well above its weight class when it comes to strength and ductility. The alloy exhibits impressive tensile strength and yield strength, making it a suitable choice for structural components and parts subjected to significant mechanical stress. Moreover, its good ductility allows for deformation under stress without succumbing to fracture, making it ideal for applications requiring formability and the ability to withstand impact.
- Enhanced Wear Resistance: Built to Endure: The strategic addition of silicon to the alloy is not merely a matter of chance; it’s a calculated move to significantly enhance its wear resistance. This makes AlSi12 powder the go-to choice for applications involving constant friction and abrasion, such as demanding engine components, high-stress gears, and long-lasting bearings.
- Low Thermal Expansion: Maintaining Dimensional Stability: In the world of materials, thermal expansion can be a significant challenge, but AlSi12 powder takes this hurdle in stride. It exhibits remarkably low thermal expansion compared to other aluminum alloys, making it dimensionally stable across a wide temperature range. This stability is paramount for applications where components are exposed to fluctuating temperatures, ensuring consistent performance, preventing warping or distortion, and minimizing the risk of thermal stress-related failures.
- Good Machinability: Precision Engineering at its Finest: While AlSi12 powder excels in casting intricate shapes, it also proves its mettle in machinability. It can be readily machined using conventional machining processes, allowing manufacturers to achieve precise dimensional control and create intricate features with tight tolerances. This versatility makes it an ideal material for applications demanding both complex geometries and high precision, from automotive components to aerospace parts.
7 Ways AlSi12 Powder is Transforming Industries
The unique combination of properties exhibited by AlSi12 powder has unlocked a world of possibilities across a vast spectrum of industries. Let’s explore seven key applications where AlSi12 powder is making a significant and lasting impact:
1. Automotive Industry: Driving Efficiency and Performance to New Heights
The automotive industry is in a perpetual state of evolution, driven by the relentless pursuit of lighter, more fuel-efficient, and higher-performing vehicles. AlSi12 powder has emerged as a key enabler in this evolutionary journey:
- Engine Components: The Heart of Automotive Performance: AlSi12 powder has found a prominent place in the heart of modern vehicles, used extensively for manufacturing critical engine components such as cylinder heads, engine blocks, pistons, intake manifolds, and more. Its lightweight nature contributes significantly to reducing overall vehicle weight, a crucial factor in improving fuel efficiency and reducing emissions. Moreover, its high strength and wear resistance ensure these critical components can withstand the demanding conditions within an engine, guaranteeing durability and longevity.
- Transmission Components: Seamless Power Delivery: The smooth and efficient transfer of power from the engine to the wheels is paramount for a refined driving experience. AlSi12 powder plays a vital role in achieving this seamless power delivery by being the material of choice for manufacturing gears, synchronizer rings, and other essential transmission components. Its excellent wear resistance and robust mechanical properties ensure smooth shifting, minimize friction losses, and extend the operational lifespan of the transmission system.
- Brake Components: Confidence in Every Stop: When it comes to safety, braking performance is non-negotiable. AlSi12 powder contributes to enhanced braking systems by being used in the production of brake calipers, pistons, and other critical brake system components. Its lightweight nature reduces unsprung weight, contributing to improved handling and ride comfort. At the same time, its high strength and good thermal conductivity ensure reliable and consistent braking performance, reducing stopping distances and enhancing overall safety.
2. Aerospace Industry: Reaching New Heights of Innovation and Efficiency
In the realm of aerospace engineering, where every gram counts, weight reduction is paramount. AlSi12 powder, with its impressive strength-to-weight ratio, has emerged as a game-changer:
- Aircraft Components: Lighter for Longer Flights: From the structural brackets and fuselage components that form the backbone of an aircraft to the fuel system parts and interior fittings that enhance passenger comfort, AlSi12 powder is used to manufacture a wide array of aircraft components. Its primary contribution lies in reducing the overall weight of the aircraft, a crucial factor in improving fuel efficiency, extending range, and reducing the environmental impact of air travel.
- Drone Technology: Taking Flight with AlSi12: The rapidly evolving field of drone technology demands lightweight yet robust materials to push the boundaries of flight performance. AlSi12 powder fits this bill perfectly, finding applications in the manufacturing of drone frames, propellers, and other critical components. Its lightweight nature directly translates to longer flight times and increased payload capacity, enabling drones to perform more complex tasks and cover greater distances.
3. Additive Manufacturing: Shaping the Future of Production, One Layer at a Time
Additive manufacturing, more commonly known as 3D printing, has revolutionized the way we design and manufacture products. AlSi12 powder, with its unique characteristics, has become a popular choice in this transformative technology:
- Prototyping and Rapid Tooling: Accelerating the Design Process: AlSi12 powder empowers manufacturers to rapidly prototype complex designs and create custom tooling with unprecedented speed and flexibility. This accelerated design process reduces lead times, allowing companies to bring innovative products to market faster and respond to evolving customer demands with agility.
- Lightweight Structures: Pushing the Boundaries of Design: The ability to precisely control the deposition of AlSi12 powder in additive manufacturing opens up a world of possibilities for creating intricate geometries and complex lattice structures. This enables the production of lightweight yet incredibly strong components, finding applications in aerospace, automotive, and other industries where weight reduction is critical without compromising structural integrity.
4. Powder Metallurgy: Engineered for Performance, Crafted with Precision
Powder metallurgy, a process that involves compacting metal powders into desired shapes, benefits greatly from the unique characteristics of AlSi12 powder:
- Gears and Bearings: Engineered to Withstand the Test of Time: Gears and bearings are the unsung heroes of countless mechanical systems, operating under immense pressure and constant friction. AlSi12 powder, with its exceptional wear resistance and robust mechanical properties, stands as the ideal material for manufacturing these critical components. Its use ensures longevity, reduces maintenance requirements, and enhances the overall reliability of machinery.
- Filters and Porous Structures: Controlling Flow with Precision: By carefully controlling the sintering process in powder metallurgy, manufacturers can create porous structures with defined pore sizes using AlSi12 powder. These porous structures find applications in various fields, from filtration systems for gases and liquids to heat exchangers and even biomedical implants. The ability to tailor the porosity and pore size distribution opens up new possibilities for creating materials with unique properties, such as controlled permeability for filtration applications or interconnected porosity for bone ingrowth in orthopedic implants.
5. Electronics Industry: Enabling Miniaturization and Performance in Harmony
As electronic devices continue their relentless march towards miniaturization and increased processing power, managing heat dissipation becomes a paramount concern:
- Heat Sinks and Spreaders: Keeping Electronics Cool Under Pressure: AlSi12 powder’s good thermal conductivity makes it a star player in the world of thermal management for electronics. It’s used to manufacture heat sinks and spreaders, essential components designed to efficiently dissipate heat generated by electronic components, preventing overheating, ensuring optimal performance, and extending the lifespan of these sensitive devices.
6. Tooling and Mold Making: Precision and Durability for High-Performance Manufacturing
The demanding world of tooling and mold making requires materials that can withstand repetitive cycles, high pressures, and abrasive wear. AlSi12 powder rises to the challenge, offering a compelling combination of properties:
- Injection Molding Tools: Shaping the World of Plastics: Injection molding is a cornerstone of modern manufacturing, used to create a vast array of plastic products. AlSi12 powder is used to create the precision tools that shape these products, offering good dimensional stability, excellent wear resistance, and the ability to maintain tight tolerances throughout high-volume production runs.
- Die Casting Dies: Precision Metal Casting: Die casting is another critical manufacturing process used to produce complex metal parts with high precision. AlSi12 powder’s high strength and remarkable resistance to thermal fatigue make it a suitable choice for manufacturing die-casting dies, ensuring the dies can withstand the demanding conditions of repeated cycles, high temperatures, and pressure without degrading or losing dimensional accuracy.
7. Other Applications: Exploring New Frontiers of Innovation
The versatility of AlSi12 powder knows no bounds, and its applications continue to expand into new and exciting fields:
- Sporting Goods: Enhancing Performance, Reducing Weight: From lightweight yet durable bicycle frames that enhance cycling performance to precisely weighted golf club heads that improve swing mechanics, AlSi12 powder is making its mark in the sporting goods industry. Its ability to reduce weight without sacrificing strength or durability makes it a sought-after material for creating high-performance equipment.
- Medical Devices: Biocompatible and Reliable: Advancements in medical technology demand biocompatible materials that can withstand the harsh environment within the human body. Biocompatible grades of AlSi12 powder have emerged as valuable players in this field, used in orthopedic implants, surgical instruments, and other medical devices where strength, lightweight, and biocompatibility are paramount.
Comparing AlSi12 Powder to Other Materials
Material | Density (g/cm³) | Tensile Strength (MPa) | Thermal Expansion (10⁻⁶/°C) |
---|---|---|---|
AlSi12 Powder | 2.65 – 2.75 | 180 – 240 | 22 – 24 |
Aluminum Alloy 6061 | 2.70 | 310 | 23.6 |
Steel (AISI 1018) | 7.87 | 440 | 11.7 |
As clearly illustrated in the table, AlSi12 powder presents a compelling case for its adoption, offering a unique combination of low density and commendable strength. This makes it a lightweight yet robust alternative to traditional materials like steel and some aluminum alloys. While its tensile strength might be lower than some of its counterparts, its exceptional castability, remarkable wear resistance, and low thermal expansion make it a superior choice for a wide range of applications where these properties are paramount.
FAQs about AlSi12 Powder
1. What makes AlSi12 powder particularly suitable for the automotive industry?
AlSi12 powder’s low density makes it ideal for creating lightweight engine and transmission components, crucial for improving fuel efficiency in vehicles. Its high strength-to-weight ratio ensures these components don’t compromise on structural integrity, while its excellent wear resistance guarantees longevity in demanding engine conditions.
2. How does AlSi12 powder contribute to the advancement of additive manufacturing?
AlSi12 powder’s flowability and packing density are critical for successful metal 3D printing, allowing for the creation of intricate designs and complex geometries unattainable through traditional manufacturing processes. This opens up new possibilities for lightweight, high-strength components in industries like aerospace and automotive.
3. What advantages does AlSi12 powder offer in powder metallurgy compared to other materials?
AlSi12 powder’s ability to be compacted and sintered into near-net shapes reduces the need for extensive machining, making it a cost-effective choice for producing gears, bearings, and other high-wear components. Its inherent wear resistance ensures these parts can withstand demanding operating conditions, extending their lifespan.
4. Why is AlSi12 powder used in electronics and thermal management applications?
AlSi12 powder exhibits good thermal conductivity, making it suitable for use in heat sinks and spreaders for electronic devices. Its inclusion in these components helps dissipate heat efficiently, preventing overheating and ensuring optimal performance of sensitive electronics.
5. What are the key advantages of AlSi12 powder that make it a popular choice across industries?
AlSi12 powder offers a unique combination of advantages: lightweight, high strength, excellent castability, good machinability, impressive wear resistance, and cost-effectiveness. This blend of properties makes it a versatile material suitable for a wide range of applications, driving innovation across various industries, from automotive and aerospace to electronics and medical devices.
If you want to know more about aluminum alloy powders:
We recommend this quality blog for you:20+ exciting aluminum alloys