Overview of Atomized Metal Powder
Atomized metal powder is a form of metal produced by atomizing molten metal into very fine droplets. The droplets rapidly solidify into powder particles in the shape of spheres or irregular granules.
Atomized metal powders have advantages over other forms of metal powders due to their fine grain structure and uniform particle shape. They are widely used in manufacturing industry with applications including:
Key Details About Atomized Metal Powder
- Produced by atomizing molten metal into fine droplets that solidify into powder
- Particles are small spheres or irregular granules in the micrometer range
- Uniform particle size and shape compared to other metal powder production methods
- Fine grain structure improves properties like strength and corrosion resistance
- Common base metals include iron, copper, aluminum, nickel, cobalt
Types of Atomization Processes
There are two main types of atomization processes used to produce atomized metal powder commercially:
Air Atomization
- Molten metal stream is broken into droplets by high pressure air or inert gas
- Produces powders with particle sizes from 5-250 microns
- Lower production rate but able to make finer powders
- Irregular particle shapes like ellipsoids
Atomizace vody
- Molten metal stream is disintegrated by high pressure water
- Larger particles from 50-1000 microns
- Higher production rate due to faster heat transfer
- Spherical particle morphology
Proces | Velikost částic | Rychlost výroby | Tvar částice |
---|---|---|---|
Air Atomization | 5-250 microns | Dolní | Nepravidelné |
Atomizace vody | 50-1000 microns | Vyšší | Sférické |
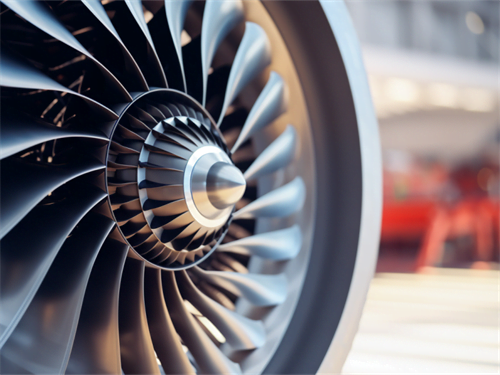
Characteristics of Atomized Metal Powders
Atomized metal powders have unique characteristics that make them suitable for manufacturing applications:
Distribuce velikosti částic
- Narrow distribution with majority of particles in micron size range
- Controlled by atomization parameters like gas flow rate and pressure
- Finer particles have higher surface area to volume ratio
Tvar částice
- Spherical or rounded irregular shapes
- Affects powder flow and packing density
- More spherical particles have better flowability
Čistota
- High purity with low oxygen and nitrogen levels
- Avoid contamination from atomization medium
- Crucial for metallurgical properties
Hustota
- Near theoretical density for most metals
- Porosity depends on solidification rate
- Denser particles improve compaction and sintering
Charakteristický | Popis |
---|---|
Distribuce velikosti částic | Narrow, micron-range |
Tvar částic | Spherical or rounded irregular |
Čistota | High, low oxygen/nitrogen |
Hustota | Near theoretical density |
Applications and Uses of Atomized Metal Powders
Atomized metal powders are used across manufacturing industries due to their properties and quality:
Prášková metalurgie
- Press and sinter process to produce finished parts
- High purity gives better mechanical properties
- Uniform particle size improves compaction
Aditivní výroba kovů
- Used as feedstock for 3D printing methods like selective laser sintering
- Spherical shape gives better powder flowability
- Fine size allows very high resolution prints
Povrchové nátěry
- Thermal spraying to deposit thick coatings on surfaces
- Small particle size allows uniform coating
- Oxide-free surface improves coating adhesion
Brazing Filler Metals
- Joining of metals by capillary flow of filler powder
- Controlled particle size prevents clogging
- Low oxygen content prevents defects
aplikace | Výhody |
---|---|
Prášková metalurgie | Vysoká čistota, jednotná velikost |
Aditivní výroba | Spherical shape, fine size |
Povrchové nátěry | Small size, oxide-free |
Brazing fillers | Controlled size, low oxygen |
Specifikace a normy
Atomized metal powders must meet certain specifications and standards for quality control:
Distribuce velikosti částic
- Typically given by D values (diameter below which X% particles exist)
- D10, D50, D90 values define spread of distribution
- D50 is median particle size
Zdánlivá hustota
- Measures powder packing density and flowability
- Higher density indicates more spherical particles
- Reported as g/cm3 or % of theoretical density
Hall Flowrate
- Time for 50g powder to flow through standardized funnel
- Lower time indicates better flowability
- Below 25 seconds is good flow
Sítová analýza
- Fraction of powder retained on specific mesh sizes
- Indicates spread of particle sizes
- Performed from 325 mesh down to pan
Chemie
- Base metal purity by ICP analysis
- Oxygen and nitrogen levels by inert gas fusion
Parametr | Typická specifikace | Zkušební metoda |
---|---|---|
Distribuce velikosti částic | D10, D50, D90 | Difrakce laseru |
Zdánlivá hustota | g/cm3 or % theoretical | Hallův průtokoměr |
Hall flowrate | Seconds for 50g to flow | ASTM B213 |
Sítová analýza | % retained on each mesh | ASTM B214 |
Chemie | Base metal, O, N wt% | ICP, inert gas fusion |
Úvahy o návrhu
The atomization process and powder characteristics must be designed appropriately for the intended application:
Atomization Method
- Air or inert gas for finer particles needed in additive manufacturing
- Water atomization for coarser particles suitable for pressing
Velikost částic
- Finer particles have higher sintering activity but lower flowability
- Larger particles compact better but limit resolution of prints
Tvar částice
- Irregular shapes have higher surface area while spherical improve flowability
- Angular particles provide better mechanical interlocking
Hustota
- Higher density improves compaction and shrinkage control
- Some porosity can help relieve stresses during sintering
Čistota
- Oxygen and nitrogen levels must be minimized
- Other impurities can affect mechanical properties
Parametr | Design Guidelines |
---|---|
Atomization method | Air/gas for fine, water for coarse |
Velikost částic | Finer have higher sintering activity |
Tvar částic | Spherical improve flow, irregular provide interlocking |
Hustota | Higher density improves compaction |
Čistota | Minimize O, N and other impurities |
Instalace, provoz a údržba
Proper installation, operation, and maintenance of atomization equipment is critical:
- Installation should be done according to manufacturer specifications with proper utilities and ancillary equipment in place
- Operation procedures must be strictly followed especially for startup, shutdown, and changeovers between alloys
- Critical process parameters like temperature, pressure, flowrates should be continuously monitored and controlled
- Preventative maintenance schedule should be implemented including inspections, replacements of wear parts like nozzles, and overhauls
- Regular cleaning cycles to avoid buildup of material in gas pipes, water lines, crucible, and collection system
- Safety systems must be kept in good working order especially emergency stops, fire detection and suppression
- Training programs for employees should focus on safe handling of molten metal, quality control testing, and troubleshooting procedures
Proper installation, operation, and maintenance will maximize production volume and minimize downtime. This helps improve the productivity, quality, and safety of atomized metal powder production.
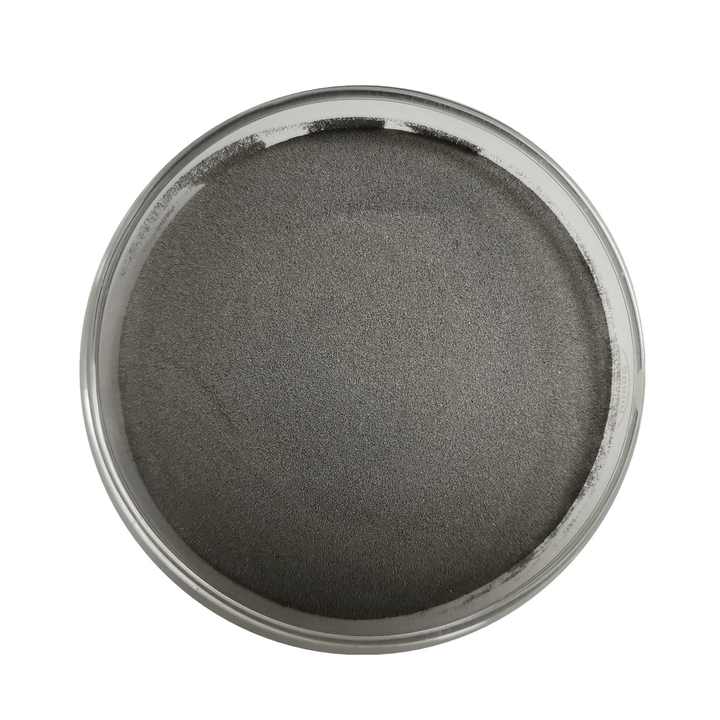
Choosing an Atomized Metal Powder Supplier
It is important to select a reputable supplier when purchasing atomized metal powder:
- Experience and technical expertise in atomization process
- Ability to produce a range of alloys, particle sizes and shapes
- Quality control testing meets industry standards
- Reasonable minimum order quantities and lead times
- Inventory of standard powders for quick delivery
- Capability to tailor properties or develop custom alloys
- Understanding of intended application and technical requirements
- Samples available for evaluation prior to purchasing
- Competitive pricing for both high and low volumes
- Location and logistics suitable to meet delivery schedule
- Responsiveness for technical questions and follow-up requests
Choosing a supplier with advanced capabilities and strong customer service will help ensure a consistent and reliable supply of high quality atomized metal powder.
Pros and Cons of Atomized Metal Powder
Atomized metal powder has both advantages and limitations compared to other forms of metal:
Výhody
- Uniform particle size and shape
- Good flowability due to spherical morphology
- High purity enables great metallurgical properties
- Near theoretical density improves compaction
- Fine microstructure from rapid solidification
- Lower sintering temperature than milled powder
- Used in additive manufacturing and other advanced processes
Omezení
- Higher cost compared to milled powder
- Limited alloy availability compared to wrought forms
- Particle size range not suitable for some applications
- Minimum order quantities may be higher
- Lower production rate than mechanical atomization
- Requires handling and safety precautions for fine powder
Parametr | Výhody | Omezení |
---|---|---|
Vlastnosti částic | Uniform size/shape, good flow | Omezený rozsah velikostí |
Čistota | High purity, fine microstructure | |
Vlastnosti | High density, low sintering temperature | |
Výrobní | Used in AM, advanced processes | Limited alloys, higher cost |
Zpracování | Requires precautions for fine powder |
Analýza nákladů
Atomized metal powder is more expensive than other metal powder production methods, with pricing dependent on:
- Base metal – more expensive for reactive metals like titanium, tantalum
- Purity – high purity powder commands premium pricing
- Particle size – finer powder is more costly due to lower yield
- Order quantity – prices decrease significantly at higher volumes
- Processing – additional steps like sieving, blending, annealing add cost
Typical pricing ranges:
Kov | Velikost částic | Cenové rozpětí |
---|---|---|
Iron and steel | 15-150 micron | $1-3 per lb |
Hliník | 25-250 micron | $3-8 per lb |
Měď | 15-120 micron | $6-15 per lb |
Slitiny niklu | 10-75 micron | $10-25 per lb |
Titan | 45-150 micron | $50-150 per lb |
Pricing also depends on supplier capabilities, raw material costs, and market conditions. Work with qualified suppliers to obtain competitive pricing for your specific material requirements and order volumes.

FAQ
What are the main advantages of atomized metal powder?
The main advantages are uniform particle size and shape, high purity, good flowability, near theoretical density, and fine microstructure. These benefits make atomized powder suitable for additive manufacturing, powder metallurgy, thermal spraying, and other applications.
How is atomized powder different from other metal powder production methods?
Atomized powder has more uniform particle characteristics compared to milled powder. It also has higher purity and density versus electrolytic powder and powder made by chemical reduction. The rapid solidification in atomization also results in finer microstructures.
What precautions are required when handling atomized powder?
Fine metal powders can be a dust explosion hazard. Precautions include grounding and bonding systems, non-sparking tools, dust collection, protective gear for workers, and exclusion of ignition sources. Powders may also require controlled atmospheres and special packaging.
What is the typical particle size range for atomized powder?
Air atomized powder is commonly 5-150 microns while water atomized powder is 50-1000 microns. Size can be controlled by adjusting atomization parameters. Finer sizes have higher surface area while coarser powders compact better.
How is atomized metal powder used in additive manufacturing?
The uniform particle shape allows excellent flowability in powder bed processes like selective laser sintering. The fine particle size enables very high resolution while retaining bulk properties of the alloy. High purity minimizes defects in final parts.
What methods detect impurities in atomized powder?
Chemical analysis using ICP can detect trace levels of impurities. Oxygen and nitrogen content is measured by inert gas fusion analyzers. Sieve analysis determines contamination from oversize particles. SEM and optical microscopy can detect satellite particles.
How does porosity in atomized powder affect properties?
Minimal porosity is desired for good compaction and sintering. But some optimized porosity can help relieve stresses during thermal processing. Post-production annealing can also be used to increase powder density.
Why is high purity important for atomized powder properties?
Impurities like oxygen and nitrogen can significantly degrade mechanical performance and microstructural development. Even ppm levels must be controlled to achieve the best strength, ductility, corrosion resistance in final parts.
What safety equipment is used for molten metal atomization?
Safety gear includes reflective clothing, face shields, heat resistant gloves, metal splash aprons, and leather jackets. Good ventilation is needed to control fumes. Automatic fire suppression systems are also critical.
How often is maintenance required on atomization equipment?
Preventative maintenance should be done at scheduled intervals, such as replacing consumable parts after a certain number of hours of operation. Additional maintenance is required as needed, indicated by process changes, output variations, or component failures.