Manufacturing Processes for CuSnZn Powder
CuSnZn powder, a versatile alloy with unique properties, is produced through various manufacturing methods. The choice of method depends on the desired particle size, shape, and overall quality of the powder. Here are some of the most common processes:
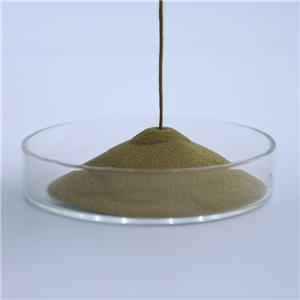
Techniky práškové metalurgie
This is a widely used method where molten CuSnZn alloy is rapidly cooled, breaking it down into tiny droplets that solidify into powder particles.
- The molten alloy is sprayed into a high-velocity gas stream, causing it to atomize.
- The alloy is sprayed into a water spray, resulting in finer particles.
In this process, elemental powders of copper, tin, and zinc are blended and subjected to intense mechanical energy, causing them to bond and form a homogeneous alloy powder.
Plazmový nástřik
- A high-temperature plasma jet is used to melt and atomize a CuSnZn wire or rod, which then solidifies into powder particles.
Další metody
- A CuSnZn alloy can be deposited onto a substrate through electrolysis, followed by mechanical processing to obtain the desired powder.
- CuSnZn compounds can be precipitated from solutions, resulting in fine powder particles.
- Larger CuSnZn alloy pieces can be ground or crushed to obtain powder.
Comparison of Manufacturing Methods for CuSnZn Powder
CuSnZn powder exhibits a unique combination of physical and mechanical properties that make it a versatile material for various applications. These properties are influenced by factors such as composition, particle size, and manufacturing process. Comparison of Physical and Mechanical Properties of CuSnZn Powder CuSnZn powder, with its unique combination of properties, finds applications in a wide range of industries. Its versatility, durability, and corrosion resistance make it a valuable material for various components and products. Applications of CuSnZn Powder CuSnZn powder, like any industrial material, presents potential environmental and health risks if not handled and disposed of properly. It is important to implement appropriate measures to minimize these risks and ensure the safety of workers and the environment. To mitigate environmental and health risks, it is essential to implement the following safety measures: Environmental and Health Considerations of CuSnZn Powder CuSnZn powder continues to be a promising material with a wide range of applications. Ongoing research and development efforts are exploring new possibilities and addressing existing challenges to further enhance its performance and expand its use. Future Trends and Developments in CuSnZn Powder Here are five FAQs tailored for potential users of CuSnZn powder, focusing on their likely concerns and information needs: 1. What are the key properties of CuSnZn powder that make it suitable for bearing applications? CuSnZn powder, often referred to as bronze powder, offers a unique combination of high strength, excellent wear resistance, good fatigue strength, and self-lubricating properties. These characteristics make it ideal for manufacturing bearings, bushings, and wear plates that can withstand high loads and friction. 2. How does the composition of CuSnZn powder influence its specific properties? The precise proportions of copper, tin, and zinc in the alloy determine its final properties. Tin enhances strength and corrosion resistance, while zinc improves castability and machinability. Specific compositions are tailored for applications requiring different balances of strength, wear resistance, and cost-effectiveness. 3. What are the common production methods for CuSnZn powder, and how do they impact powder characteristics? Atomization is the most common method for producing CuSnZn powder, where molten alloy is atomized into fine droplets that solidify into powder particles. This method allows for good control over particle size distribution, which influences the powder’s flowability, packing density, and final product properties. 4. What are the typical sintering temperatures and atmospheres used for CuSnZn powder? CuSnZn powder is typically sintered in a reducing atmosphere, such as hydrogen or a mixture of nitrogen and hydrogen, to prevent oxidation of the tin and zinc components. The sintering temperature range is generally between 750°C and 850°C, depending on the desired density and mechanical properties. 5. What technical resources and support does Xmetto provide to assist with the implementation of CuSnZn powder? Xmetto offers detailed material specifications, processing guidelines, and expert technical support to assist customers with the successful implementation of CuSnZn powder. We can provide guidance on powder selection, sintering parameters, and troubleshooting to ensure optimal performance in your specific application.
Metoda
Výhody
Nevýhody
Atomizace
Produces spherical particles
Requires high-temperature melting and cooling
Mechanické legování
Can produce fine, homogeneous powders
Requires extensive mechanical processing
Plasma spraying
Versatile for various materials
Can produce particles with a wide size distribution
Elektrodepozice
Precise control over composition
Limited to thin layers
Chemické srážení
Fine particle size
Can be difficult to control composition
Comminution
Simple and cost-effective
Can produce particles with irregular shapes
Physical and Mechanical Properties of CuSnZn Powder
Fyzikální vlastnosti
Mechanické vlastnosti
Vlastnictví
CuSnZn Powder
Hustota
8.4-8.9 g/cm³
Pórovitost
Varies depending on manufacturing process
Distribuce velikosti částic
Can be controlled during manufacturing
Tvrdost
Relatively high
Pevnost v tahu
Mírná až vysoká
Tažnost
Dobrý
Odolnost proti korozi
Dobrý
Odolnost proti opotřebení
Vysoký
Applications and Industries of CuSnZn Powder
Electronics and Electrical Components
Friction Materials (Brakes and Clutches)
Povlaky odolné proti opotřebení
Aditivní výroba (3D tisk)
Other Potential Applications
Průmysl
Aplikace
Elektronika
Conductive pastes, electrodes, electrical contacts
Třecí materiály
Brake linings, clutch plates
Nátěry
Hardfacing, corrosion-resistant coatings
Aditivní výroba
Metal powder for 3D printing
Ostatní
Catalysts, magnetic materials, structural components
Environmental and Health Considerations of CuSnZn Powder
Dopady na životní prostředí
Health Risks
Bezpečnostní opatření
Faktor
Potential Impacts
Bezpečnostní opatření
Životní prostředí
Water pollution, air pollution, soil contamination
Proper disposal, pollution control measures
Zdraví
Respiratory problems, skin irritation, eye irritation
PPE, ventilation, hygiene practices
Future Trends and Developments in CuSnZn Powder
Advancements in Manufacturing Techniques
New Applications and Industries
Research and Development Efforts
Challenges and Opportunities
Oblast
Trends and Developments
Výrobní
Nanotechnology, additive manufacturing, sustainable processes
Aplikace
Energy storage, biomedical devices, electronic packaging
Výzkum
Alloy optimization, surface modification, life cycle assessment
Výzvy
Cost, consistency, regulations
CuSnZn Powder FAQs: Addressing Key Concerns for Potential Users
If you would like to know more about the wide range of Copper Based Powder, please click on the names in the table: