In the ever-evolving landscape of materials science and engineering, the relentless pursuit of stronger, lighter, and more versatile materials has led to groundbreaking innovations. Among these, iron-based alloy powders have emerged as a game-changer, offering an unparalleled combination of desirable properties and transformative potential across a myriad of industries. This comprehensive guide delves into the exciting realm of iron-based alloy powders, exploring their unique characteristics, diverse applications, and the specific advantages of various popular types, empowering you to make informed decisions for your next project.
Why Iron Based Alloy Powders? Unveiling the Advantages
Iron-based alloy powders, meticulously manufactured through the advanced process of powder metallurgy, offer a distinct advantage over traditional materials and manufacturing methods. This innovative approach grants engineers and manufacturers unprecedented control over material properties and component design, paving the way for superior performance, enhanced efficiency, and unparalleled design freedom. Let’s explore the key advantages that have propelled iron-based alloy powders to the forefront of modern manufacturing:
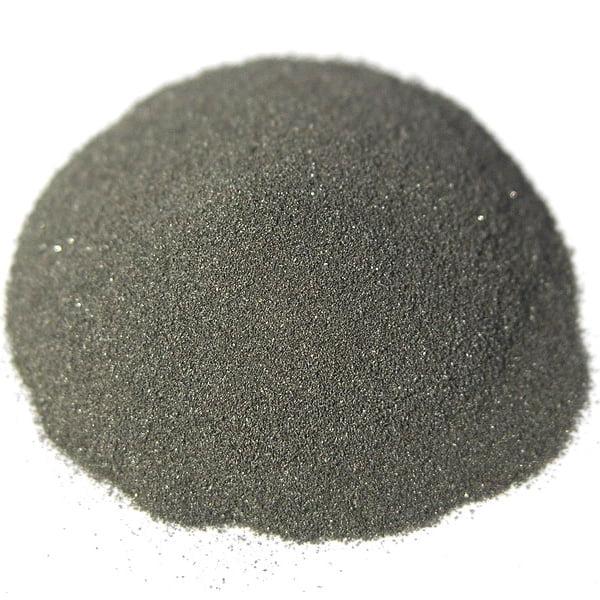
- Vylepšené mechanické vlastnosti: Iron-based alloy powders enable the creation of components with superior mechanical properties compared to their conventionally processed counterparts. This includes significantly higher strength, enhanced hardness, improved wear resistance, and extended fatigue life, making them ideal for demanding applications requiring exceptional durability and reliability.
- Tailored Microstructures: One of the most significant advantages of powder metallurgy is the ability to precisely control the material’s microstructure. By carefully manipulating processing parameters, manufacturers can achieve tailored microstructures with desired grain sizes, phase distributions, and porosity levels, resulting in materials with optimized properties for specific applications.
- Výroba s téměř čistým tvarem: Iron-based alloy powders empower manufacturers to produce components with intricate geometries and complex designs to near-net shape, significantly reducing the need for secondary machining operations. This not only minimizes material waste and machining costs but also opens up new possibilities for design complexity and functional integration.
- Alloying Flexibility: The versatility of iron-based alloy powders extends to their alloying capabilities. By precisely controlling the composition of the powder mixture, manufacturers can fine-tune the properties of the final material to meet specific application requirements. This allows for the creation of alloys with tailored properties, such as enhanced corrosion resistance, improved high-temperature performance, or specific magnetic characteristics.
- Efektivita nákladů: While the initial cost of iron-based alloy powders might be higher than that of traditional materials, the overall cost-effectiveness of powder metallurgy often outweighs the initial investment. Reduced material waste, lower machining costs, and the potential for enhanced performance and extended service life contribute to significant long-term cost savings.
Navigating the World of Iron Based Alloy Powders: A Closer Look at Popular Types
The world of iron-based alloy powders encompasses a diverse range of materials, each meticulously engineered to excel in specific applications. This section provides a closer look at some of the most sought-after types, highlighting their unique properties and common uses:
Prášky z nerezové oceli:
Renowned for their exceptional corrosion resistance, impressive strength, and inherent biocompatibility, stainless steel powders have become indispensable across a multitude of industries, ranging from aerospace and automotive to medical and food processing. Let’s explore some of the most popular types:
- 300 Series Stainless Steel Powders:
- 304 Powder & 304L Powder: These versatile and widely used stainless steel powders offer a balanced combination of good corrosion resistance, excellent formability, and reliable weldability. Their versatility makes them suitable for a wide range of applications, including food processing equipment, chemical processing vessels, architectural components, and household appliances.
- 316L Stainless Steel Powder: This grade of stainless steel powder stands out for its exceptional corrosion resistance, particularly in challenging environments with high chloride concentrations. This makes it an ideal choice for marine applications, such as boat propellers and desalination plants, as well as for chemical processing equipment, medical implants requiring high biocompatibility, and pharmaceutical manufacturing equipment.
- 310 Powder: Known for its remarkable high-temperature performance, 310 stainless steel powder exhibits excellent heat resistance and outstanding oxidation resistance at elevated temperatures. This makes it well-suited for demanding applications in high-temperature environments, such as furnace components, heat exchangers, combustion chambers, and aerospace engine parts.
- 317L Powder: Building on the excellent corrosion resistance of 316L, 317L stainless steel powder takes it a step further, providing superior corrosion resistance in even harsher environments, including those with extremely high chloride concentrations, acids, and alkalis. This makes it an ideal choice for demanding applications in chemical processing, marine environments, pollution control equipment, and oil and gas extraction.
- Other Stainless Steel Powders:
- 17-4PH Stainless Steel Powder: This precipitation-hardenable stainless steel powder achieves an exceptional combination of high strength and impressive hardness through a controlled heat treatment process. This makes it suitable for demanding applications in aerospace components requiring high strength-to-weight ratios, chemical processing equipment handling corrosive fluids, and high-strength fasteners used in demanding environments.
- 420 Powder: Offering a good balance of corrosion resistance and hardness, 420 stainless steel powder is a cost-effective choice for a variety of applications. Its common uses include cutlery, surgical instruments requiring corrosion resistance and sharpness, valve components, and bearings.
- M2 Powder: This high-speed steel powder stands out for its exceptional wear resistance and impressive hot hardness, making it ideal for demanding tooling applications. It is commonly used in cutting tools, drills, dies, and other applications requiring high wear resistance and the ability to maintain hardness at elevated temperatures.
- Stainless Steel OP431 Powder: This precipitation-hardenable stainless steel powder strikes a good balance between strength, toughness, and corrosion resistance, making it a versatile choice for demanding applications. Its common uses include aerospace components requiring a combination of strength and corrosion resistance, medical devices requiring biocompatibility and strength, and high-performance sporting goods.
Prášky z nástrojové oceli:
Engineered to withstand the rigors of demanding tooling applications, tool steel powders are renowned for their exceptional hardness, impressive wear resistance, and remarkable toughness. These properties make them ideal for cutting, shaping, and forming other materials. Let’s explore some of the most popular types:
- H13 Alloy Steel Powder: This hot work tool steel powder is highly sought after for its excellent toughness, impressive wear resistance, and outstanding hot hardness. These properties make it well-suited for demanding applications in die casting dies, forging dies, hot stamping tools, and other tooling applications involving high temperatures and pressures.
- D2 Powder: This high-carbon, high-chromium tool steel powder is renowned for its exceptional wear resistance, making it ideal for applications requiring extended tool life. Its common uses include cutting tools, punches, dies, and wear plates, particularly for applications involving abrasive materials or high-volume production runs.
- T15 Powder: This high-speed steel powder exhibits excellent wear resistance and impressive hot hardness, making it suitable for high-speed cutting tools, drills, end mills, and other applications requiring high cutting speeds and elevated temperatures. Its ability to maintain hardness at high temperatures makes it ideal for high-speed machining operations.
- S2 Powder: This shock-resistant tool steel powder offers a good balance of toughness and wear resistance, making it suitable for tools subjected to impact loads. Its common uses include chisels, punches, hammers, and other tools used in applications involving impact or shock loading.
Other Notable Iron Based Alloy Powders:
Beyond stainless steel and tool steel powders, several other notable iron-based alloy powders cater to specific and demanding applications:
- AerMet100 Stainless Steel Powder: This ultra-high strength steel powder stands out for its exceptional strength-to-weight ratio, making it a top choice for weight-sensitive applications requiring extreme strength. Its common uses include aerospace components, demanding structural applications in motorsport and defense, and high-performance sporting goods requiring lightweight yet strong materials.
- A100 steel alloy powder: This ultra-high strength steel powder is known for its high hardenability and impressive toughness, making it suitable for demanding structural applications requiring high strength and resistance to fracture. Its common uses include gears, shafts, axles, and other critical components requiring high strength and durability.
- 18Ni300 Powder: This maraging steel powder offers an exceptional combination of ultra-high strength, impressive toughness, and good ductility, making it a top contender for demanding applications requiring a balance of strength and toughness. Its common uses include aerospace components, tooling for high-strength materials, and other high-performance applications requiring exceptional mechanical properties.
Selecting the Right Iron Based Alloy Powder: Key Considerations
Choosing the optimal iron-based alloy powder for your specific application requires careful consideration of several factors. By carefully evaluating your application requirements and understanding the properties of different powder types, you can make an informed decision that meets your performance, cost, and processing needs. Here are some key considerations to guide your selection process:
- Mechanické vlastnosti: Start by identifying the critical mechanical properties required for your application. This includes determining the required tensile strength, yield strength, elongation, hardness, toughness, fatigue resistance, and wear resistance. Carefully analyze the loading conditions, operating environment, and expected service life to determine the target values for each property.
- Odolnost proti korozi: Assess the environment in which the component will operate and determine the level of corrosion resistance required. Consider factors such as exposure to moisture, humidity, salt spray, chemicals, acids, alkalis, and high temperatures. Select a powder with appropriate corrosion resistance properties to ensure long-term performance and prevent premature failure.
- Odolnost proti opotřebení: Analyze the wear mechanisms involved in your application and choose a powder with suitable wear resistance properties. Consider factors such as abrasive wear, adhesive wear, erosive wear, and fretting wear. Selecting a powder with appropriate wear resistance can significantly extend component life and reduce maintenance costs.
- Tepelné vlastnosti: Evaluate the temperature range of the application and select a powder with appropriate thermal properties. This includes considering the coefficient of thermal expansion, thermal conductivity, and heat resistance. Matching the thermal properties of the powder to the application requirements can prevent issues related to thermal stress, distortion, and degradation.
- Náklady: While performance requirements should always take precedence, it’s essential to balance them with the cost of the powder and processing. Consider the cost of the powder itself, as well as the processing costs associated with powder metallurgy, such as compaction, sintering, and any required secondary operations.
The Future of Manufacturing: Iron Based Alloy Powders Leading the Charge
Iron-based alloy powders are at the forefront of materials science and advanced manufacturing, enabling the creation of innovative solutions across a multitude of industries. As research and development efforts continue to push the boundaries of this exciting field, we can expect to see even more groundbreaking discoveries and transformative applications of iron-based alloy powders. From aerospace and automotive to medical and energy, iron-based alloy powders are poised to revolutionize industries by enabling the creation of lighter, stronger, more efficient, and more sustainable products.
Let’s summarize the key properties of the discussed iron-based alloy powders in a table for easy comparison:
Typ prášku | Kategorie | Klíčové vlastnosti | Typické aplikace |
---|---|---|---|
304 Powder | Nerezová ocel | Corrosion resistant, formable, weldable | Food processing equipment, chemical processing vessels, architectural components, household appliances |
Prášek 316L | Nerezová ocel | Excellent corrosion resistance, especially in chloride environments | Marine applications, chemical processing equipment, medical implants, pharmaceutical equipment |
310 prášek | Nerezová ocel | High heat and oxidation resistance | Furnace components, heat exchangers, combustion chambers, aerospace engine parts |
317L prášek | Nerezová ocel | Superior corrosion resistance in harsh environments | Chemical processing, marine environments, pollution control equipment, oil and gas extraction |
17-4PH Powder | Nerezová ocel | High strength, hardness (precipitation hardenable) | Aerospace components, chemical processing equipment, high-strength fasteners |
420 Powder | Nerezová ocel | Good corrosion resistance, hardness | Cutlery, surgical instruments, valve components, bearings |
M2 prášek | Nerezová ocel | Excellent wear resistance, hot hardness | Cutting tools, drills, dies, wear plates |
Prášek z nerezové oceli OP431 | Nerezová ocel | Good balance of strength, toughness, corrosion resistance | Aerospace components, medical devices, high-performance sporting goods |
H13 Prášek | Nástrojová ocel | Excellent toughness, wear resistance, hot hardness | Die casting dies, forging dies, hot stamping tools |
D2 Powder | Nástrojová ocel | Výjimečná odolnost proti opotřebení | Cutting tools, punches, dies, wear plates |
T15 prášek | Nástrojová ocel | Excellent wear resistance, hot hardness | High-speed cutting tools, drills, end mills |
S2 prášek | Nástrojová ocel | Shock-resistant, good toughness, wear resistance | Chisels, punches, hammers, impact tools |
AerMet100 Powder | Ultra-High Strength Steel | Výjimečný poměr pevnosti a hmotnosti | Aerospace components, demanding structural applications, high-performance sporting goods |
A100 Powder | Ultra-High Strength Steel | High hardenability, toughness | Gears, shafts, axles, demanding structural applications |
Prášek 18Ni300 | Maraging Steel | Ultra-high strength, toughness, good ductility | Aerospace components, tooling for high-strength materials, high-performance applications |
By understanding the unique characteristics and applications of various iron-based alloy powders, you can leverage their exceptional properties to unlock new possibilities in design, manufacturing, and innovation. Embrace the power of precision and explore the limitless potential of iron-based alloy powders for your next project, pushing the boundaries of what’s possible in materials science and advanced manufacturing.
FAQs: Addressing Common Queries about Iron Based Alloy Powders
1. What are the key advantages of using iron-based alloy powders over traditional manufacturing methods?
Iron-based alloy powders offer several key advantages over traditional manufacturing, including:
- Vylepšené mechanické vlastnosti: Achieve superior strength, hardness, wear resistance, and fatigue life.
- Tailored Microstructures: Precisely control the material’s microstructure for desired properties.
- Výroba s téměř čistým tvarem: Produce complex components with minimal waste and machining.
- Alloying Flexibility: Fine-tune material properties through a wide range of alloying additions.
- Efektivita nákladů: Benefit from reduced waste, lower machining costs, and enhanced performance.
2. What industries benefit most from the use of iron-based alloy powders?
Iron-based alloy powders find applications in a wide range of industries, including:
- Letectví: Lightweight, high-strength components for aircraft and spacecraft.
- Automobilový průmysl: Engine components, transmission gears, and structural parts.
- Lékařský: Implants, surgical instruments, and dental applications.
- Nástroje: Cutting tools, dies, and molds for various manufacturing processes.
- Energie: Components for oil and gas extraction, power generation, and renewable energy.
3. How do I choose the right iron-based alloy powder for my application?
Selecting the optimal powder involves considering:
- Mechanické vlastnosti: Required strength, hardness, toughness, and wear resistance.
- Odolnost proti korozi: Environmental factors like moisture, chemicals, and temperature.
- Odolnost proti opotřebení: Type and severity of wear mechanisms involved.
- Tepelné vlastnosti: Temperature range, thermal expansion, and conductivity.
- Náklady: Balance performance requirements with powder and processing costs.
4. What are the typical processing steps involved in powder metallurgy?
Powder metallurgy typically involves these steps:
- Výroba prášku: Creating the metal powder through atomization or other methods.
- Blending and Mixing: Combining different powders to achieve desired alloy compositions.
- Zhutnění: Pressing the powder into a desired shape using a die.
- Spékání: Heating the compacted part to bond the particles and increase density.
- Dokončovací práce: Optional secondary operations like machining, heat treatment, or surface coating.
5. What are the future trends and advancements in iron-based alloy powder technology?
The field of iron-based alloy powders is constantly evolving. Some key trends include:
- Vývoj nových slitin: Research into new alloy compositions with enhanced properties.
- Aditivní výroba: Increasing use of powder bed fusion and other AM techniques.
- Improved Processing Technologies: Advancements in compaction, sintering, and finishing methods.
- Udržitelnost: Focus on reducing environmental impact and improving resource efficiency.
If you want to know everything, this guide will help:
Iron-Based Alloy Powders: Ultimate Complete Guide to Excellence