In the competitive landscape of modern manufacturing, precision reigns supreme. Nowhere is this truer than in the realm of powder metallurgy, where the quality of your kovový prášeks directly dictates the performance, reliability, and overall success of your final products. Whether you’re crafting high-performance aerospace components, intricate medical implants, or cutting-edge automotive parts, achieving and maintaining exceptional powder characteristics is non-negotiable.
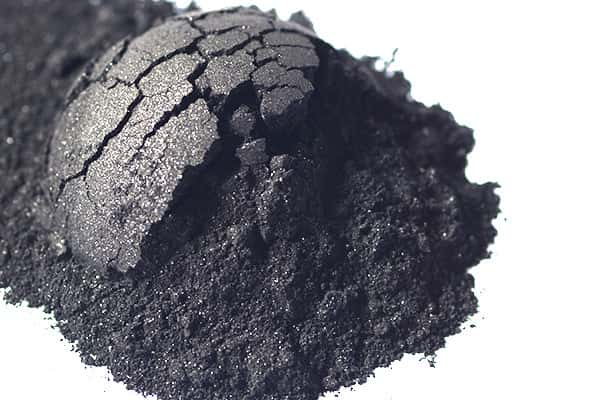
This isn’t simply about meeting industry benchmarks; it’s about exceeding expectations, pushing the boundaries of what’s possible, and unlocking the full potential of your manufacturing processes. This comprehensive guide delves into five proven strategies to elevate the quality of your metal powders, empowering you to reach new levels of precision, performance, and consistency in your powder metallurgy operations.
Why Powder Quality Matters: The Foundation of Superior Products
Before we embark on the journey of powder quality optimization, let’s take a step back and truly appreciate why powder quality is the unsung hero, the silent workhorse, behind every successful powder metallurgy operation:
- Enhanced Flowability: The Smooth Operator of Powder Metallurgy: Imagine pouring sugar into a bowl – the way it flows smoothly and evenly, filling every nook and cranny. That’s the power of good flowability. In powder metallurgy, consistent particle size and shape translate into this same smooth, predictable flow, ensuring uniform filling of molds and dies, minimizing the risk of air pockets, and ultimately reducing defects during the consolidation process.
- Improved Packing Density: Building a Solid Foundation: Think of a well-packed suitcase – more items fit neatly when they’re packed tightly together. Similarly, higher packing density in powder metallurgy means more particles can occupy a given volume. This results in denser, stronger, and more uniform components with fewer voids, cracks, or imperfections, leading to superior mechanical properties and overall product integrity.
- Superior Mechanical Properties: The Strength Behind the Structure: The mechanical properties of your final product – its strength, ductility, toughness, fatigue resistance – are directly influenced by the quality of the powder used to create it. Finer, more uniform powders, free from impurities, contribute to a stronger, more robust microstructure, resulting in components that can withstand demanding applications and deliver exceptional performance.
- Enhanced Surface Finish: The Aesthetics of Precision: In a world where first impressions matter, a smooth, polished surface finish can make all the difference. Finer metal powders contribute to smoother surface finishes on your final products, reducing the need for extensive post-processing steps like grinding or polishing. This not only saves time and resources but also enhances the aesthetic appeal of your components.
- Increased Dimensional Accuracy: Precision from Start to Finish: Dimensional accuracy is paramount in many industries, ensuring components fit together seamlessly and function flawlessly. Consistent powder properties lead to more predictable shrinkage during the sintering process, the critical step where powder compacts are heated to bond the particles. This predictability translates into components with higher dimensional accuracy and tighter tolerances, meeting even the most stringent industry standards.
5 Proven Strategies to Elevate Your Metal Powder Game
Now that we understand the profound impact of powder quality, let’s roll up our sleeves and explore the five key strategies to transform your approach to powder sourcing, handling, and utilization:
1. Master the Art of Powder Production: Process Parameters are Key
The journey to exceptional powder quality begins at the very heart of the operation: the production process itself. Whether your chosen method is gas atomization, water atomization, centrifugal atomization, or another technique, meticulous control over every process parameter is paramount. Think of it as fine-tuning an orchestra – each instrument must be perfectly calibrated for the symphony to soar.
- Gas Atomization: The Gold Standard of Precision:
- Gas Pressure and Flow Rate: The Sculptors of Particle Size: These parameters are your artistic tools for shaping the particle size distribution and morphology of your powder. Higher gas pressures and flow rates typically lead to finer powders with a narrower size distribution.
- Melt Temperature and Flow Rate: The Architects of Droplet Formation: The temperature and flow rate of the molten metal influence the size of the droplets formed during atomization, which in turn affects the final particle size and solidification behavior.
- Atomization Chamber Design: The Stage for Optimal Flow: The geometry and design of the atomization chamber play a crucial role in ensuring optimal gas flow patterns, efficient mixing of the molten metal and gas jets, and ultimately, the production of high-quality powder with consistent characteristics.
- Water Atomization: Harnessing the Power of Water Jets:
- Water Pressure and Flow Rate: The Force Behind Particle Formation: These parameters determine the velocity and impact energy of the water jets, which directly influence the size, shape, and cooling rate of the atomized metal droplets.
- Melt Pouring Rate and Temperature: A Delicate Dance of Solidification: The rate at which the molten metal is poured into the atomization chamber and its temperature must be carefully balanced to ensure proper droplet formation and solidification behavior.
- Atomization Nozzle Design: Shaping the Water Jet’s Precision: The design of the atomization nozzle, particularly its orifice geometry, plays a critical role in shaping the water jet pattern, influencing the size, distribution, and overall quality of the resulting metal powder.
2. Embrace the Power of Characterization: Knowledge is Your Most Powerful Tool
In the world of powder metallurgy, as in life, you can’t improve what you don’t measure. Thorough, meticulous powder characterization is akin to having a detailed map of your powder’s properties, revealing its strengths, weaknesses, and hidden potential. This knowledge empowers you to identify areas for improvement, optimize your processes, and ultimately, produce superior products.
Characterization Technique | Property Measured | Importance for Powder Quality |
---|---|---|
Particle Size Analysis (PSA) | Particle size distribution, mean particle size | Provides a fundamental understanding of the powder’s size characteristics, crucial for flowability, packing density, and final product properties. |
Skenovací elektronová mikroskopie (SEM) | Particle morphology, surface features, particle size and shape | Allows for visual inspection of individual particles, revealing details about their shape, surface texture, and potential defects. |
X-ray Diffraction (XRD) | Crystal structure, phase composition | Provides insights into the internal structure of the powder particles, revealing information about their crystalline phases, which can influence mechanical and thermal properties. |
Chemická analýza | Elemental composition, purity | Ensures the powder meets the required chemical specifications, identifying any impurities or variations in composition that could impact performance. |
Flowability Testing | Powder flow behavior, cohesiveness | Evaluates how easily the powder flows and its tendency to clump or pack, crucial for consistent feeding and filling in powder metallurgy processes. |
3. The Importance of Proper Handling and Storage: Protecting Your Investment
Imagine purchasing the finest ingredients for a gourmet meal, only to have them spoil due to improper storage. The same principle applies to metal powders. Even the highest quality powders, meticulously produced and characterized, can degrade over time if not handled and stored with the utmost care and attention. Implement these best practices to safeguard your powder investment and ensure its longevity:
- Control Moisture and Humidity: The Silent Enemy of Metal Powders: Moisture is a metal powder’s nemesis, leading to oxidation, clumping, and degradation of its properties. Store powders in a dedicated, climate-controlled environment with low humidity levels, ideally below 50%. Consider using desiccants within storage containers for added protection.
- Prevent Contamination: Cleanliness is Next to Powder Quality: Contamination from foreign particles, dust, or other materials can wreak havoc on powder quality, leading to inconsistencies in processing and defects in final products. Use clean, dedicated containers and handling equipment, and implement strict cleaning protocols to prevent cross-contamination.
- Minimize Exposure to Air: The Shield Against Oxidation: Exposure to air, particularly oxygen and moisture, can lead to oxidation of metal powders, degrading their properties and compromising performance. Store powders in airtight containers, preferably under an inert gas atmosphere like argon or nitrogen, to minimize oxidation and preserve powder quality.
- Handle with Care: Gentle Movements for Powder Perfection: Metal powders, despite their seemingly solid nature, are comprised of tiny particles that can be easily damaged. Avoid dropping or impacting powder containers, as this can cause particle breakage or changes in particle size distribution, leading to inconsistencies in processing.
- First-In, First-Out (FIFO): The Inventory Strategy for Freshness: Implement a First-In, First-Out (FIFO) inventory system to ensure that older powder batches are used before newer ones. This minimizes the risk of powder degradation over time and ensures consistent powder quality in your manufacturing processes.
4. The Power of Powder Conditioning: Optimizing for Success
Think of powder conditioning as the culinary arts of powder metallurgy. Just as a chef carefully prepares ingredients before crafting a masterpiece, powder conditioning techniques further enhance the quality and consistency of your metal powders, optimizing them for peak performance in your specific manufacturing processes.
- Sieving: The Gatekeeper of Particle Size: Sieving is a fundamental yet essential powder conditioning technique that removes oversized or undersized particles from your powder batch. This process ensures a more uniform particle size distribution, improving flowability, packing density, and ultimately, the consistency and quality of your final products.
- Mixing: The Art of Powder Homogeneity: Whether you’re combining powders from different production batches or blending different alloy compositions, thorough mixing is crucial to achieve a homogeneous powder blend with consistent properties. Proper mixing ensures that every component you produce benefits from the same high-quality powder, reducing variability and enhancing overall product reliability.
- Drying: Removing the Unwanted Moisture: Residual moisture, even in small amounts, can hinder powder flowability, promote oxidation, and lead to defects during consolidation. Drying, typically performed using gentle heat under controlled conditions, removes this unwanted moisture, improving the powder’s handling characteristics and ensuring its readiness for processing.
- Sphericalization: Shaping Particles for Optimal Performance: While many atomization processes aim to produce spherical particles, some powders might have irregular shapes that can hinder flowability and packing density. Sphericalization techniques, such as plasma spheroidization or gas-phase condensation, transform these irregularly shaped particles into more spherical forms, enhancing flowability, packing density, and overall powder quality.
5. Partner with Powder Experts: Leverage Their Knowledge and Experience
Navigating the intricate world of powder metallurgy and achieving optimal powder quality can be a challenging endeavor. Don’t hesitate to seek guidance and support from experienced powder suppliers and industry experts who can provide invaluable insights, resources, and solutions tailored to your specific needs.
A knowledgeable powder partner can offer:
- Technical Expertise: Your Guide to Powder Selection and Optimization: Benefit from their deep understanding of powder properties, production processes, and application requirements to make informed decisions about powder selection, process optimization, and troubleshooting.
- Quality Assurance: Peace of Mind with Every Batch: Work with suppliers who adhere to stringent quality control measures and hold relevant industry certifications. This ensures that every batch of powder you receive meets the highest standards of consistency, purity, and performance.
- Application Support: Tailored Solutions for Your Success: Receive guidance and support on powder implementation and optimization for your specific manufacturing processes, ensuring seamless integration and optimal results.
- Research and Development: Access to Cutting-Edge Innovation: Partner with suppliers who are at the forefront of powder technology, constantly researching and developing new alloys, production methods, and powder conditioning techniques to meet the evolving needs of the industry.
Why Choose Xmetto for Your Metal Powder Needs?
You’ve just delved into the critical factors that influence metal powder quality and learned how it directly impacts your manufacturing success. At Xmetto, we share your passion for precision, performance, and pushing the boundaries of what’s possible in powder metallurgy.
Here’s how Xmetto empowers you to elevate your manufacturing with superior metal powders:
- Nekompromisní kvalita: We understand that your products demand the very best. That’s why we go above and beyond to deliver metal powders with exceptional purity, controlled particle size distribution, and optimal flowability, ensuring consistent feeding, uniform consolidation, and superior final product properties.
- Řešení na míru pro vaše jedinečné potřeby: We recognize that every application has its own set of requirements. Our team of experts works closely with you to understand your specific needs, providing tailored powder solutions and expert guidance on process optimization to maximize your manufacturing success.
- A Partner in Innovation: We’re not just a supplier; we’re your collaborative partner in innovation. We’re constantly exploring new alloys, refining production processes, and developing cutting-edge powder conditioning techniques to empower you with the latest advancements in powder metallurgy.
- Dedicated to Your Success: Your success is our top priority. From technical expertise to application support, we’re with you every step of the way, providing the resources, guidance, and partnership you need to achieve your manufacturing goals.
Ready to experience the Xmetto difference and unlock the full potential of your powder metallurgy operations? Contact us today to discuss your specific needs and discover how our high-quality metal powders and expert support can elevate your manufacturing to new heights.
Embracing a Culture of Quality: It’s a Journey, Not a Destination
Improving the quality of your metal powders isn’t a one-time project; it’s an ongoing commitment to excellence, a journey of continuous improvement that permeates every aspect of your manufacturing process. By embracing these strategies, fostering a culture of quality within your organization, and forging strong partnerships with industry experts, you can unlock the full potential of powder metallurgy and elevate your products to new heights of performance, reliability, and innovation.