In the demanding world of high-performance materials, Al 7075 powder stands as a true champion, renowned for its exceptional strength-to-weight ratio and remarkable fatigue resistance. This meticulously engineered aluminum alloy powder, fortified with zinc as its primary alloying element alongside magnesium and copper, consistently pushes the boundaries of what’s achievable in material science. It’s the ultimate choice for applications where compromise simply isn’t an option, where strength, durability, and lightweight design are paramount.
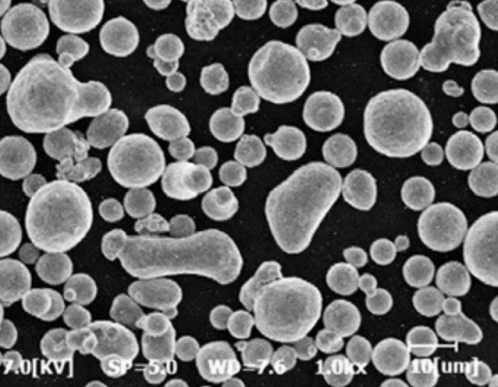
From soaring through the skies in aerospace engineering to navigating the intricate world of medical devices, Al 7075 powder consistently delivers unparalleled performance, exceeding expectations and setting new benchmarks for excellence across a multitude of industries.
But what exactly makes Al 7075 powder such a sought-after material? And how can your business leverage its extraordinary properties to gain a competitive edge in today’s demanding marketplace?
This comprehensive guide delves deep into the remarkable characteristics and diverse applications of Al 7075 powder, revealing how it’s revolutionizing industries and driving innovation across a wide range of sectors.
The Al 7075 Powder Advantage: A Powerful Blend of Strength and Reliability
Al 7075 powder’s dominance in high-performance applications stems from its carefully calibrated composition, a potent blend of properties that sets it apart from conventional materials:
- Exceptional Strength-to-Weight Ratio: Lightweight Dominance: Al 7075 powder boasts an exceptional strength-to-weight ratio, surpassing many other aluminum alloys and even rivaling some steels. This remarkable characteristic makes it ideal for applications where minimizing weight is crucial without compromising structural integrity. This balance of strength and lightweight is particularly valuable in aerospace, automotive, and sporting goods industries, where reducing weight can significantly enhance performance, fuel efficiency, and overall agility.
- Impressive Fatigue Resistance: Enduring the Test of Time: Al 7075 powder exhibits impressive fatigue resistance, meaning it can withstand repeated stress cycles and vibrations without succumbing to fatigue failure. This crucial property is essential for components subjected to cyclical loading, such as aircraft wings, bicycle frames, and high-speed machinery. This ability to withstand repeated stress cycles without weakening makes it incredibly reliable for components operating in demanding environments where longevity and safety are paramount.
- Good Machinability: Precision Engineering at its Finest: While known for its strength, Al 7075 powder also exhibits good machinability, allowing it to be precisely machined using conventional machining processes. This enables manufacturers to achieve tight tolerances, intricate geometries, and complex designs with exceptional accuracy. This ease of machining makes it a favorite among manufacturers, allowing for intricate designs and cost-effective production of high-performance components.
- Heat Treatable for Enhanced Performance: Like many aluminum alloys, Al 7075 powder can be heat-treated to further enhance its mechanical properties. Through controlled heating and cooling processes, its strength, hardness, and stress corrosion cracking resistance can be tailored to meet specific application requirements. This ability to fine-tune its properties through heat treatment makes it incredibly versatile, catering to a wide range of performance needs across various industries.
7 Demanding Applications Where Al 7075 Powder Takes Flight
The exceptional properties of Al 7075 powder have unlocked a world of possibilities across a diverse range of industries. Let’s explore seven demanding applications where Al 7075 powder truly shines:
1. Aerospace Industry: Reaching New Heights of Performance
The aerospace industry demands materials that can withstand extreme conditions, from high altitudes to rapid temperature changes, all while maintaining structural integrity. Al 7075 powder rises to the challenge:
- Aircraft Structures: Lighter for Longer Flights: Al 7075 powder is a critical component in aircraft construction, used for fuselage frames, wing spars, ribs, and other structural components. Its exceptional strength-to-weight ratio contributes to reducing overall aircraft weight, leading to increased fuel efficiency, extended range, and improved payload capacity. By utilizing Al 7075 powder, aircraft manufacturers can achieve significant weight savings, resulting in aircraft that can fly farther, carry more passengers or cargo, and reduce their environmental impact.
- Landing Gear Components: Handling the Impact: Landing gear components endure immense stress during takeoff and landing. Al 7075 powder’s high strength and fatigue resistance make it ideal for manufacturing critical landing gear parts, ensuring safe and reliable operation under extreme conditions. Its ability to withstand the repeated stress of landings and takeoffs, even in harsh weather conditions, makes it essential for maintaining the safety and reliability of aircraft.
2. Defense Industry: Equipping for Mission-Critical Operations
The defense industry relies on materials that can withstand the rigors of combat and demanding environments. Al 7075 powder’s strength and reliability make it a top choice:
- Military Vehicles: Enhanced Protection and Mobility: Al 7075 powder is used in the construction of armored vehicles, military transport, and other defense equipment. Its high strength-to-weight ratio provides enhanced protection while maintaining mobility and agility in the field. This balance is crucial in military applications, where vehicles need to be both heavily armored for protection and nimble enough for maneuverability in challenging terrains.
- Weapon Components: Precision and Reliability Under Pressure: Al 7075 powder’s strength, fatigue resistance, and machinability make it suitable for manufacturing critical weapon components, ensuring accuracy, reliability, and durability in demanding combat situations. Its ability to withstand high pressures and temperatures, along with its resistance to wear and tear, makes it ideal for components that require precision and reliability in high-stress situations.
3. Automotive Industry: Pushing the Limits of Performance and Efficiency
The automotive industry constantly seeks materials that can enhance performance, improve fuel efficiency, and reduce emissions. Al 7075 powder offers a winning combination:
- High-Performance Vehicles: Unleashing Speed and Agility: Al 7075 powder is used in high-performance vehicles, such as sports cars and racing cars, for manufacturing chassis components, suspension parts, and other performance-critical parts. Its high strength-to-weight ratio contributes to reduced weight, improved acceleration, and enhanced handling. By reducing the overall weight of the vehicle, Al 7075 powder allows for faster acceleration, better braking, and more responsive handling, leading to an overall enhanced driving experience.
- Electric Vehicle Components: Lightweighting for Extended Range: As the electric vehicle market grows, lightweighting is crucial for extending range and improving battery efficiency. Al 7075 powder is used in electric vehicle components, such as battery casings and structural parts, to reduce weight without compromising safety or performance. By reducing the weight of the vehicle, Al 7075 powder helps to maximize the range of electric vehicles on a single charge, addressing one of the key concerns of potential electric vehicle buyers.
4. Sporting Goods: Empowering Athletes to Achieve Peak Performance
In the competitive world of sports, athletes constantly seek equipment that can give them a competitive edge. Al 7075 powder delivers:
- High-End Bicycle Frames: Conquering Mountains, Dominating Roads: Al 7075 powder is a premium material for manufacturing high-end bicycle frames, particularly for road bikes, mountain bikes, and BMX bikes. Its exceptional strength-to-weight ratio and fatigue resistance create lightweight, responsive, and durable frames that can handle the demands of competitive cycling. These high-performance frames provide cyclists with a competitive edge, allowing them to climb hills faster, accelerate quicker, and enjoy a more responsive and comfortable ride.
- Rock Climbing Gear: Reaching New Heights with Confidence: Al 7075 powder is used in rock climbing equipment, such as carabiners, cam lobes, and quickdraws. Its high strength, fatigue resistance, and corrosion resistance make it a reliable and safe choice for these critical pieces of equipment. The reliability and strength of these components are crucial for climber safety, providing peace of mind when scaling challenging rock faces.
5. Tooling and Mold Making: Precision and Durability for Manufacturing
Al 7075 powder’s strength, dimensional stability, and machinability make it a valuable material for tooling and mold-making applications:
- Injection Molds: Creating Complex Parts with Precision: Al 7075 powder is used to manufacture injection molds for producing plastic parts. Its high strength and dimensional stability ensure the mold can withstand high injection pressures and maintain tight tolerances, resulting in high-quality plastic parts. The durability and dimensional stability of Al 7075 powder ensure that the molds can produce millions of parts with consistent quality and precision, making it a cost-effective choice for high-volume production runs.
- Die Casting Dies: Withstanding Extreme Temperatures and Pressures: Al 7075 powder’s high strength and thermal fatigue resistance make it suitable for manufacturing die casting dies used to produce metal parts. These dies must withstand extreme temperatures and pressures during the die casting process, and Al 7075 powder’s properties make it an ideal choice for this demanding application. Its ability to retain its strength and dimensional stability at high temperatures ensures the production of high-quality metal parts with excellent surface finish and dimensional accuracy.
6. Medical Devices: Combining Strength and Biocompatibility
The medical device industry demands materials that are strong, lightweight, and biocompatible. Al 7075 powder meets these stringent requirements:
- Surgical Instruments: Precision and Reliability in the Operating Room: Al 7075 powder is used in the manufacturing of surgical instruments, such as forceps, clamps, and retractors. Its high strength, corrosion resistance, and ability to be sterilized make it suitable for these critical applications. The lightweight nature of Al 7075 powder reduces surgeon fatigue during lengthy procedures, while its corrosion resistance ensures the instruments can be sterilized multiple times without degrading, maintaining a sterile environment.
- Prosthetics and Orthotics: Restoring Mobility with Lightweight Strength: Al 7075 powder is used in the manufacturing of prosthetic limbs and orthotic devices. Its high strength-to-weight ratio allows for the creation of lightweight yet durable devices that restore mobility and improve the quality of life for patients. These lightweight prosthetics and orthotics provide greater comfort for amputees and individuals with mobility impairments, allowing for more natural movement and reducing strain on other parts of the body.
7. Electronics Industry: Enabling High-Performance Electronics
Al 7075 powder’s unique properties are also valuable in the electronics industry:
- Heat Sinks for High-Power Electronics: Dissipating Heat Effectively: As electronic devices become more powerful, efficient heat dissipation becomes critical. Al 7075 powder’s good thermal conductivity makes it suitable for manufacturing heat sinks for high-power electronic components, ensuring optimal performance and reliability. These heat sinks efficiently draw heat away from sensitive electronic components, preventing overheating and ensuring optimal performance and longevity of electronic devices.
- Shielding Components: Protecting Sensitive Electronics: Al 7075 powder can be used to create shielding components for sensitive electronic equipment. Its non-magnetic properties and ability to attenuate electromagnetic interference (EMI) make it suitable for protecting electronic components from external interference. This shielding is crucial in preventing data loss, signal disruption, and potential damage to sensitive electronic components caused by external electromagnetic interference.
Comparing Al 7075 Powder to Other Materials
Material | Dichte (g/cm³) | Zugfestigkeit (MPa) | Streckgrenze (MPa) | Dehnung (%) | Ermüdungsfestigkeit (MPa) |
---|---|---|---|---|---|
Al 7075 Powder (T6) | 2.81 | 572 | 503 | 11 | 165 |
Al 6061 Powder (T6) | 2.70 | 310 | 276 | 10 | 97 |
Steel (AISI 4140) | 7.85 | 655 | 415 | 22 | 310 |
Titan-Legierung (Ti-6Al-4V) | 4.43 | 950 | 880 | 14 | 540 |
As the table illustrates, Al 7075 powder (in its T6 temper) offers an exceptional combination of high strength, lightweight, and good fatigue resistance. While its fatigue strength might be lower than that of titanium alloys or some high-strength steels, its significantly lighter weight and competitive cost make it a compelling choice for many high-performance applications. This balance of properties makes it a cost-effective alternative to heavier and more expensive materials like steel and titanium, especially when weight savings, fatigue resistance, and cost-effectiveness are critical factors.
FAQs about Al 7075 Powder
1. What are the key advantages of Al 7075 powder compared to other aluminum alloys?
Al 7075 powder stands out due to its exceptional strength-to-weight ratio, impressive fatigue resistance, and good machinability, making it suitable for demanding applications requiring high strength and lightweight. It’s also heat-treatable, allowing for further enhancement of its mechanical properties to meet specific application needs. This unique combination of properties makes it highly desirable for industries where performance and reliability are paramount.
2. How does heat treatment affect the properties of Al 7075 powder?
Heat treatment processes, such as solution heat treatment and aging, can significantly enhance the mechanical properties of Al 7075 powder, increasing its strength, hardness, and stress corrosion cracking resistance to meet specific application requirements. This ability to tailor its properties through heat treatment makes it highly adaptable to specific applications, enhancing its versatility and appeal to manufacturers.
3. Is Al 7075 powder weldable?
While Al 7075 powder can be welded, it’s generally considered less weldable than other aluminum alloys like Al 6061. Welding can reduce its strength and fatigue properties in the heat-affected zone. If welding is required, specific welding procedures and filler materials should be used to minimize the potential for reduced mechanical properties.
4. What are the common applications of Al 7075 powder in the aerospace industry?
Al 7075 powder is widely used in the aerospace industry for manufacturing critical aircraft components, including fuselage frames, wing spars, ribs, and landing gear parts. Its high strength-to-weight ratio and fatigue resistance make it ideal for these demanding applications, contributing to lighter aircraft with increased fuel efficiency and longer ranges.
5. What makes Al 7075 powder suitable for high-performance sporting goods?
Its exceptional strength-to-weight ratio, fatigue resistance, and corrosion resistance make Al 7075 powder a top choice for high-performance sporting goods, such as bicycle frames, rock climbing equipment, and golf club heads. These properties ensure that the equipment can withstand the rigors of competitive sports while remaining lightweight and responsive, giving athletes a competitive edge.
If you want to know more about aluminum alloy powders:
We recommend this quality blog for you:20+ exciting aluminum alloys