Production Methods of WMoTaNb Powder
WMoTaNb powder, a refractory metal alloy with exceptional properties, is produced through various methods tailored to achieve specific particle characteristics and purity requirements. This chapter explores the primary techniques employed in the manufacturing of WMoTaNb powder.
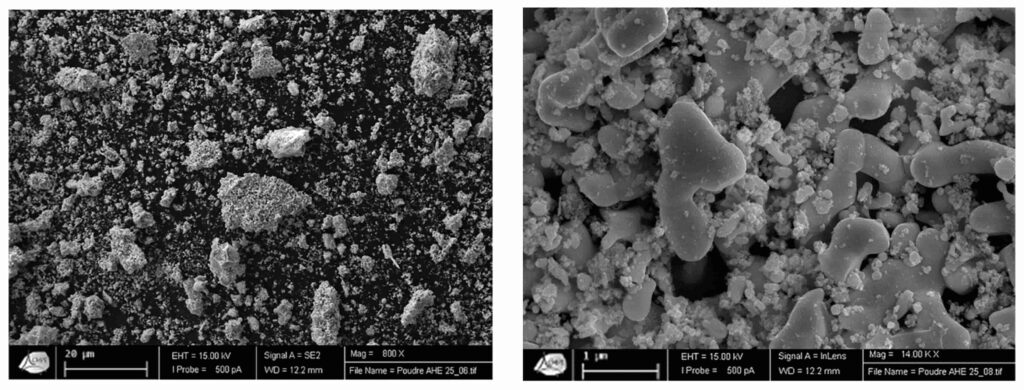
Powder Metallurgy Techniques
Powder metallurgy, a process involving the consolidation of metal powders into desired shapes, is commonly used to produce WMoTaNb powder. Two prominent techniques within this category are:
- In this method, elemental powders of tungsten, molybdenum, tantalum, and niobium are subjected to intense mechanical energy, typically through ball milling. The repeated impact and friction between the powder particles lead to the formation of a fine, homogeneous mixture with a controlled microstructure. Mechanical alloying is particularly effective in producing WMoTaNb powder with a uniform composition and desired mechanical properties.
- A variant of mechanical alloying, ball milling involves the use of a rotating drum containing balls and the metal powders. The impact and abrasion between the balls and powders result in particle size reduction, mixing, and alloy formation. Ball milling is a versatile technique that can be used to produce WMoTaNb powders with varying particle sizes and morphologies.
Plasma Spraying and Arc Melting
Plasma spraying and arc melting are alternative methods for producing WMoTaNb powder. These techniques involve the melting of the metal alloy and subsequent rapid solidification into fine particles.
- In plasma spraying, a high-temperature plasma jet is used to melt the metal alloy, which is then sprayed onto a substrate. The molten material solidifies rapidly, forming a coating or powder. Plasma spraying is suitable for producing WMoTaNb powder with a controlled particle size distribution and surface morphology.
- Arc melting involves the use of an electric arc to melt a metal alloy, which is then solidified into a ingot. The ingot is subsequently crushed and ground to produce WMoTaNb powder. While arc melting is less commonly used for powder production compared to other methods, it can be effective for producing powders with large particle sizes.
Chemische Gasphasenabscheidung (CVD)
Chemische Gasphasenabscheidung (CVD) is a chemical process used to produce WMoTaNb powder through the decomposition of gaseous precursors. In CVD, volatile compounds containing the desired elements are introduced into a reaction chamber, where they decompose under controlled conditions to form the WMoTaNb powder. CVD is a precise technique capable of producing high-purity powders with a controlled microstructure and morphology.
Comparison of WMoTaNb Powder Production Methods
WMoTaNb powder, a refractory metal alloy, exhibits a unique combination of properties that make it highly desirable for a variety of applications. This chapter explores the key characteristics and performance attributes of WMoTaNb powder. The unique properties of WMoTaNb powder make it a versatile material with a wide range of applications across various industries. This chapter explores some of the key areas where WMoTaNb powder is utilized. While WMoTaNb powder offers significant advantages, several challenges and areas for future research remain to be addressed. The market for WMoTaNb powder is driven by its unique properties and diverse applications across various industries. This chapter explores the current market trends, key players, economic outlook, and future growth prospects. The global demand for WMoTaNb powder has been steadily increasing in recent years, driven by factors such as the growth of aerospace and defense industries, advancements in energy storage technologies, and increasing demand for high-performance materials in electronic applications. The consumption of WMoTaNb powder is expected to continue growing, particularly in regions with strong industrial development and emerging economies. The market for WMoTaNb powder is relatively concentrated, with a few major players dominating the industry. These companies often possess advanced manufacturing capabilities, extensive research and development facilities, and strong distribution networks. However, new entrants and smaller players are also emerging, driven by technological advancements and niche market opportunities. The pricing of WMoTaNb powder is influenced by several factors, including production costs, raw material availability, market demand, and competition. Overall, the market for WMoTaNb powder is relatively stable, with prices fluctuating based on supply and demand dynamics. The future outlook for the WMoTaNb powder market is positive, driven by ongoing technological advancements, increasing demand for high-performance materials, and emerging applications in areas such as additive manufacturing and energy storage. The market is expected to experience continued growth, presenting investment opportunities for companies involved in the production, distribution, and application of WMoTaNb powder.
Methode
Vorteile
Benachteiligungen
Powder Metallurgy (Mechanical Alloying, Ball Milling)
Versatile, cost-effective, suitable for large-scale production
Potential for contamination, limited control over particle morphology
Plasmaspritzen
High-quality powder, controlled particle size
Requires specialized equipment, energy-intensive
Arc Melting
Simple setup, suitable for large-scale production
Begrenzte Kontrolle über Partikelgröße und -morphologie
Chemische Gasphasenabscheidung (CVD)
High purity, precise control over microstructure
Complex process, higher cost
Properties and Performance of WMoTaNb Powder
Mechanische Eigenschaften
Thermische Eigenschaften
Korrosionsbeständigkeit
Elektrische Leitfähigkeit
Properties of WMoTaNb Powder
Eigentum
Wert
Härte
Hoch
Stärke
Hoch
Duktilität
Mäßig
Schmelzpunkt
Sehr hoch
Wärmeleitfähigkeit
Gut
Oxidationsbeständigkeit
Ausgezeichnet
Korrosionsbeständigkeit
Gut
Elektrische Leitfähigkeit
Gut
WMoTaNb Powder Applications
Luft- und Raumfahrt und Verteidigung
Energiespeicherung
Elektronik
Biomedizinische
WMoTaNb Powder Applications
Industrie
Anwendungen
Luft- und Raumfahrt und Verteidigung
Rocket nozzles, turbine blades, armor plates
Energiespeicherung
Batteries, supercapacitors
Elektronik
Contacts, connectors, heat sinks
Biomedizinische
Implantate, Prothetik, Zahnrestaurationen
Herausforderungen und künftige Forschungsrichtungen
Production Challenges
Future Research Directions
Herausforderungen und künftige Forschungsrichtungen
Herausforderung
Future Research Direction
Kosten und Skalierbarkeit
Develop more cost-effective and scalable production methods
Powder Handling and Processing
Improve techniques for powder handling, storage, and processing
New Applications
Explore new and emerging applications for WMoTaNb powder
Property Enhancement
Investigate methods to enhance the properties of WMoTaNb powder
Nachhaltigkeit
Develop sustainable production methods and recycling options
Nanostructured WMoTaNb
Explore the properties and applications of nanostructured WMoTaNb powder
Market Trends and Economic Outlook
Global Demand and Consumption Patterns
Key Players and Market Competition
Pricing Trends and Factors Influencing Market Dynamics
Future Growth Prospects and Investment Opportunities
Market Trends and Economic Outlook
Trend
Impact on WMoTaNb Powder Market
Growing aerospace and defense industries
Increased demand for high-temperature and wear-resistant materials
Advancements in energy storage technologies
Increased demand for conductive materials for batteries and supercapacitors
Increasing demand for high-performance materials in electronics
Increased demand for materials with high electrical conductivity and thermal resistance
Technological advancements
Development of new production methods and applications
Emerging economies
Growing demand for WMoTaNb powder in developing regions
Wenn Sie mehr über die breite Palette an hochentropischen Legierungspulvern erfahren möchten, klicken Sie bitte auf die Namen in der Tabelle:.