In the ever-evolving landscape of materials science, the pursuit of exceptional material properties remains a relentless endeavor. Engineers and scientists strive to develop materials that are not only stronger and lighter but also more durable, capable of withstanding increasingly extreme environments and meeting the stringent demands of modern technologies. At the forefront of this materials revolution stands mechanisches Legieren powder – a transformative technique that’s reshaping industries by enabling the creation of advanced materials with meticulously tailored properties.
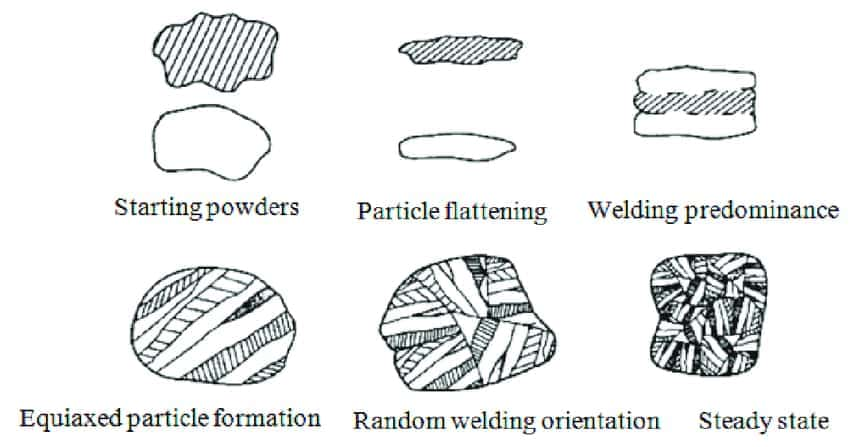
This comprehensive guide delves into the captivating world of mechanical alloying powder, exploring its intricate processes, unveiling its remarkable advantages, showcasing its diverse applications, and providing a roadmap for selecting the ideal supplier to meet your specific needs.
Beyond Simple Mixing: Unraveling the Alchemy of Mechanical Alloying
Imagine a process where distinct elemental powders are carefully selected, precisely weighed, and then introduced into a high-energy ball mill. Inside this seemingly chaotic chamber, filled with hardened steel or tungsten carbide balls, a fascinating transformation unfolds. As the chamber rotates at high speeds, the balls relentlessly collide with the powder particles, generating intense mechanical energy that transcends simple mixing.
This high-energy milling process lies at the heart of mechanical alloying, setting in motion a series of intricate steps that lead to the creation of novel materials:
- High-Energy Impacts: The relentless collisions between the milling balls and powder particles generate localized heat and pressure, inducing significant plastic deformation within the powder particles. This repeated deformation, driven by the high-energy impacts, is the driving force behind the unique microstructural changes observed in mechanically alloyed powders.
- Fracture & Cold Welding: As the powder particles undergo continuous deformation, they eventually fracture, creating fresh, highly reactive surfaces. These newly exposed surfaces readily bond with other fractured particles in a process known as cold welding, effectively merging different elemental powders at the atomic level.
- Nanoscale Alloying: This continuous cycle of deformation, fracture, and cold welding results in the formation of extremely fine grains and a homogeneous distribution of the constituent elements at the nanoscale. This intimate mixing of elements, achieved through the controlled chaos of mechanical alloying, is the key to unlocking the extraordinary properties of these advanced materials.
Unlocking a World of Advantages: Why Mechanical Alloying Matters
Mechanical alloying stands apart from traditional alloying methods, offering a compelling array of advantages that have cemented its position as a cornerstone of modern materials science:
- Expanding the Alloying Horizon: Mechanical alloying transcends the limitations of conventional melting and casting techniques, enabling the creation of alloys that were once deemed impossible. This newfound freedom to combine elements previously incompatible due to melting point disparities or other metallurgical constraints opens up a vast landscape of possibilities for developing materials with unprecedented properties.
- Engineering Superior Properties: The intense mechanical energy and nanoscale alloying achieved through mechanical alloying act as powerful tools for manipulating material properties, leading to significant enhancements:
- Unmatched Strength and Hardness: The ultrafine grain size and high dislocation density, characteristic of mechanically alloyed materials, contribute to their exceptional strength and hardness, exceeding the limits of conventionally processed alloys.
- Exceptional Wear Resistance: The homogeneous distribution of elements and the potential for incorporating hard, wear-resistant phases within the material matrix significantly enhance the resistance to wear and tear, extending the lifespan of components operating under demanding tribological conditions.
- Verbesserte Korrosionsbeständigkeit: By carefully selecting alloying elements and controlling the microstructure, mechanical alloying allows for the creation of materials with superior resistance to corrosion, even in the harshest environments. This is particularly valuable in industries like aerospace, chemical processing, and marine engineering.
- Precision & Control: Mechanical alloying offers a remarkable degree of precision and control over the alloying process. By carefully adjusting milling parameters, such as milling time, ball-to-powder ratio, milling speed, and milling atmosphere, manufacturers can fine-tune the properties of the final powder to meet the specific requirements of a wide range of applications.
Applications Across Industries: Where Mechanical Alloying Excels
The unique combination of properties achievable through mechanical alloying has propelled its adoption across a diverse range of industries, revolutionizing product design and performance:
- Aerospace: Reaching New Heights: Lightweight yet incredibly strong alloys produced through mechanical alloying are critical for crafting high-performance turbine blades, intricate engine components, and critical structural parts. These advanced materials enable significant weight reduction, leading to improved fuel efficiency, increased payload capacity, and enhanced aircraft performance.
- Automotive: Driving Innovation: The automotive industry relies on mechanically alloyed powders to produce wear-resistant and high-strength alloys for demanding applications such as engine parts, transmission gears, and brake components. These materials contribute to increased engine efficiency, improved fuel economy, and enhanced vehicle safety.
- Tooling & Machining: Pushing the Limits of Performance: Hard and wear-resistant materials are essential for tools used in demanding machining operations. Mechanical alloying enables the creation of cutting tools, dies, and molds with exceptional hardness and wear resistance, extending tool life, reducing downtime, and improving overall machining efficiency.
- Medical Implants: Enhancing Biocompatibility and Longevity: The development of biocompatible and corrosion-resistant alloys is crucial for the success of medical implants. Mechanical alloying plays a vital role in producing materials for orthopedic implants, dental implants, and other medical devices, ensuring long-term performance, minimizing the risk of rejection, and improving patient outcomes.
- Energy Storage: Powering the Future: The demand for high-performance energy storage solutions is driving innovation in battery and fuel cell technologies. Mechanical alloying is instrumental in developing advanced electrode materials with enhanced energy storage capacity, increased power output, and improved cycle life, paving the way for more efficient and sustainable energy solutions.
Choosing the Right Partner: Navigating the Mechanical Alloying Landscape
The success of any application relying on mechanically alloyed powders hinges on the selection of a reliable and capable supplier. Navigating the increasingly complex landscape of powder manufacturers requires careful consideration of several key factors:
- Technical Expertise & Industry Experience: Seek out suppliers with a deep-rooted understanding of mechanical alloying principles, demonstrated by their extensive experience in powder processing and a proven track record of delivering high-quality powders tailored to the specific demands of your industry.
- Stringent Quality Control & Comprehensive Characterization: Inquire about the supplier’s quality control protocols at every stage of the production process, from the rigorous testing of incoming raw materials to the meticulous monitoring of milling parameters and the comprehensive characterization of the final powder. Ensure they possess the necessary analytical equipment and expertise to accurately determine particle size distribution, morphology, composition, and other critical properties that directly impact the performance of your final product.
- Customization Capabilities & Collaborative Application Support: Choose a supplier that not only offers a diverse range of standard powder grades but also provides customization options to tailor powder properties to your unique specifications. A true partner will go beyond simply supplying powders, offering collaborative application support, guiding you in material selection, optimizing processing parameters, and providing expert assistance in troubleshooting any challenges that may arise.
- Reliable Production Capacity & Responsive Lead Times: Thoroughly assess the supplier’s production capacity to ensure they can consistently meet your volume requirements and adhere to your desired delivery timelines. Inquire about their inventory management practices, lead times for both standard and custom orders, and their ability to adapt to fluctuations in demand without compromising on quality or delivery schedules.
- Commitment to Ethical Sourcing & Sustainable Practices: In today’s environmentally conscious landscape, it’s essential to partner with suppliers who prioritize ethical sourcing practices, demonstrate a strong commitment to environmental responsibility, and adhere to sustainable manufacturing processes. Inquire about their sourcing policies, waste management strategies, and efforts to minimize their environmental footprint.
Making Informed Decisions: A Comparative Framework
To streamline your evaluation process, utilize this comparative table to assess potential suppliers based on the critical factors outlined above:
Faktor | Lieferant A | Lieferant B | Lieferant C | Xmetto |
---|---|---|---|---|
Technical Expertise & Experience | Limited experience, primarily focused on traditional powder metallurgy techniques | Strong technical background, but limited experience in specific industry needs | Extensive experience in powder metallurgy, but limited expertise in mechanical alloying specifically | Extensive expertise in metal additive manufacturing and a proven track record in delivering high-quality metal powders for demanding applications. |
Quality Control & Characterization | Basic quality control measures in place; limited characterization capabilities | Well-defined quality control processes; access to standard characterization tools | Comprehensive quality control program, but may lack specialized equipment for advanced powder characterization | Stringent quality control protocols at every stage, ensuring consistent powder properties and comprehensive characterization using advanced analytical techniques. |
Customization & Application Support | Limited customization options; basic technical support available | Offers some customization, but primarily focused on standard powder grades | Open to customization, but may have limited application support resources available | Collaborative approach to application support, offering customization options, technical guidance, and problem-solving expertise to optimize your processes. |
Production Capacity & Lead Times | Small-scale production capacity; lead times can be unpredictable | Medium-scale production; lead times generally reliable but can fluctuate | Large-scale production capacity; typically able to meet demanding lead times | Robust production capacity to meet diverse volume requirements and a commitment to timely delivery through efficient logistics and inventory management. |
Ethical Sourcing & Sustainability | Limited transparency in sourcing practices; sustainability initiatives unclear | Committed to ethical sourcing; actively implementing sustainable practices | Strong focus on sustainability; transparent sourcing policies and environmental initiatives in place | Strong emphasis on ethical sourcing practices, environmental responsibility, and sustainable manufacturing processes throughout the supply chain. |
Xmetto: Your Partner in Advanced Materials Innovation
Xmetto verfügt über umfassendes Fachwissen im Bereich der additiven Fertigung von Metallen und bietet umfassende Lösungen, einschließlich fortschrittlicher Metallpulver und modernster 3D-Drucktechnologien. Wir arbeiten mit Unternehmen zusammen, um innovative 3D-Drucklösungen zu implementieren und die digitale Transformation der Fertigung voranzutreiben.
Als führender Anbieter von Metall-AM-Materialien und -Anlagen liefert Xmetto Hochleistungssysteme und Pulver, um die Fertigung der nächsten Generation voranzutreiben. Wenden Sie sich an Xmetto, um zu erfahren, wie wir die additive Fertigung in Ihrem Unternehmen vorantreiben können.
Unlocking the Future: Mechanical Alloying’s Potential to Revolutionize Industries
Mechanical alloying powder represents far more than just an incremental advancement in materials science; it embodies a paradigm shift, unlocking a world of possibilities for creating materials with properties tailored to meet the ever-increasing demands of modern technologies. As industries across the globe strive to develop lighter, stronger, more durable, and more efficient products, mechanical alloying stands as a critical enabler of innovation.
By forging strategic partnerships with reputable suppliers, embracing a culture of continuous improvement, and harnessing the transformative power of mechanical alloying, we can unlock a future where material limitations no longer hinder our ability to solve global challenges in energy, healthcare, transportation, and countless other fields. The journey towards a future shaped by advanced materials has just begun, and mechanical alloying will undoubtedly play a pivotal role in driving progress for generations to come.