Zerstäubung von Metallpulver ist eine Technik zur Partikelgrößenreduzierung, mit der feine Metallpulver mit optimierten Eigenschaften für industrielle Anwendungen hergestellt werden. Bei diesem Prozess wird geschmolzenes Metall durch eine Düse gepresst, um es in gleichmäßige Tröpfchen aufzulösen, die schnell zu Pulverpartikeln erstarren.
Die Zerstäubung ermöglicht die Kontrolle über die Partikelgrößenverteilung, Morphologie, Reinheit und andere Eigenschaften des Pulvers, die für eine hohe Leistung beim 3D-Metalldruck, bei der Herstellung pulvermetallurgischer Teile, bei metallischen Beschichtungsprozessen und mehr entscheidend sind. Dieser Artikel bietet einen umfassenden Überblick über verschiedene Arten von Zerstäubungsgeräten, Arbeitsprinzipien, Designüberlegungen, Anwendungen, Vorteile und Einschränkungen.
Überblick über den Zerstäubungsprozess von Metallpulver
Durch die Zerstäubung von Metallpulver werden große flüssige Metallmengen in feine kugelförmige Pulver mit kontrollierten Eigenschaften umgewandelt. Dies wird erreicht, indem ein geschmolzener Metallstrom durch den Aufprall eines Gas- oder Flüssigkeitsstrahls in feine Tröpfchen zerlegt wird. Beim Abkühlen erstarren die Tröpfchen schnell zu Pulverpartikeln.
Die wichtigsten Schritte in diesem Prozess sind:
- Metallschmelze – Die Rohmetallcharge wird mithilfe eines Induktionsofens, Lichtbogenschmelzens oder anderer Techniken geschmolzen. Zu den üblichen zerstäubten Metallen gehören Aluminium, Titan, Nickel, Eisen, Kobalt, Kupfer usw.
- Versorgung mit geschmolzenem Metall – Das flüssige Metall wird auf optimaler Temperatur gehalten und mithilfe von Tundish, Tiegeln oder Pumpen in die Zerstäubungszone geleitet.
- Zerstäubung – Der geschmolzene Metallstrom wird durch Wechselwirkung mit Hochgeschwindigkeitsgas oder -flüssigkeit in Tröpfchen zerfallen. Es kommen verschiedene Zerstäubungsmethoden zum Einsatz.
- Puder-Kollektion – Das zerstäubte Metallpulver wird gekühlt und für nachfolgende Vorgänge gesammelt. Es können Sieb-, Magnettrenn- und Glühprozesse eingesetzt werden.
- Pulvercharakterisierung – Die Partikelgrößenverteilung, Morphologie, Dichte, Fließfähigkeit und Mikrostruktur des Pulvers werden analysiert.
Die richtige Kontrolle der Prozessparameter wie Metallzusammensetzung, Temperatur, Zerstäubungsflüssigkeitsgeschwindigkeit und Zerstäuberdesign ist entscheidend, um die gewünschten Pulvereigenschaften zu erreichen.
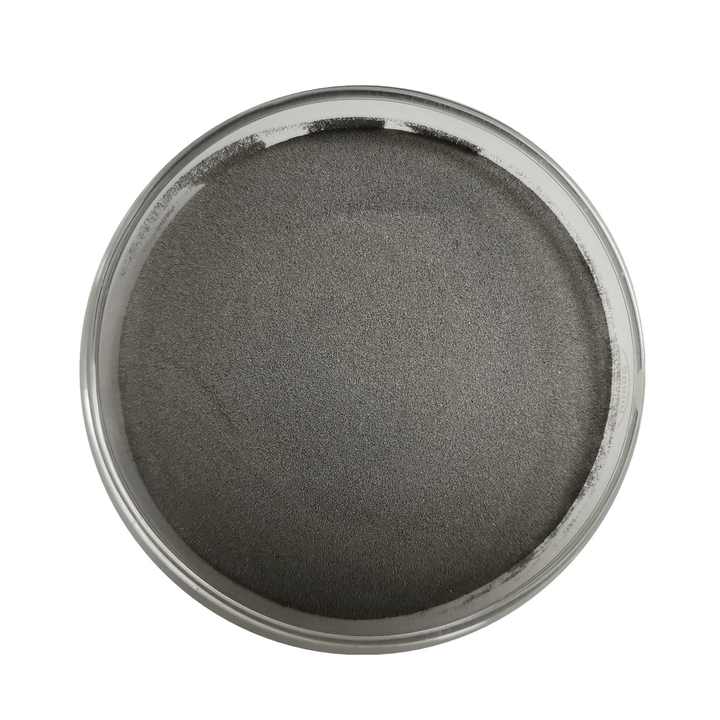
Arten von Zerstäubungsgeräten
Zerstäubungssysteme können basierend auf dem Medium, das zur Zerkleinerung des geschmolzenen Metalls in Tröpfchen verwendet wird, kategorisiert werden:
Gaszerstäubung
Bei der Gaszerstäubung beschleunigt die kinetische Energie des Hochdruckgases den flüssigen Metallstrom schnell und verteilt ihn in feine Tröpfchen. Basierend auf dem Design der Gaszufuhr kann es weiter klassifiziert werden in:
- Druckgaszerstäubung – Verwendet eng gekoppelte Düsen, um Druckluft oder Inertgas seitlich auf den Flüssigmetallstrom zu leiten.
- Gaszerstäubung mit zwei Flüssigkeitsdüsen – Koaxialdüsen leiten das Zerstäubungsgas mit hoher Geschwindigkeit um ein inneres Metallzufuhrrohr herum.
- Gaszerstäubung mit mehreren Düsen – Verwendet eine Reihe konvergent-divergenter Düsen, um Überschallgasstrahlen auf den Schmelzstrom zu richten.
Gaszerstäubte Pulver haben im Vergleich zu wasserzerstäubten Pulvern eine geringere Partikelgröße, eine gleichmäßigere Morphologie und eine höhere Reinheit. Doch der Prozess ist energieintensiv und teuer.
Wasserzerstäubung
Bei der Wasserzerstäubung wird der geschmolzene Metallstrom durch den Aufprall auf Hochdruckwasserstrahlen zerkleinert. Es bilden sich Tröpfchen mit breiterer Größenverteilung. Die Wasserzerstäubung hat im Vergleich zur Gaszerstäubung geringere Kapital- und Betriebskosten.
Je nach Design kann die Wasserzerstäubung Folgendes verwenden:
- Enggekoppelte Wasserzerstäubung – Wasserstrahlen treffen direkt auf das flüssige Metall, das aus dem Tundish austritt.
- Wasserzerstäubung im freien Fall – Der fallende Strom geschmolzenen Metalls wird von Wasserstrahlen unterhalb des Tundish abgefangen.
Wasserzerstäubte Pulver haben unregelmäßigere Partikelformen und eine breitere Verteilung, ideal zum Pressen und Sintern. Aber Wasser führt zu Verunreinigungen.
Zentrifugale Zerstäubung
Bei der Zentrifugalzerstäubung wird geschmolzenes Metall in eine sich schnell drehende Scheibe oder einen Becher gegossen oder gepumpt. Das Metall bildet am Umfang einen dünnen Film, der aufgrund der Zentrifugalkräfte in feine Tröpfchen zerfällt.
Zu den Vorteilen gehören einfaches Design, geringer Gasverbrauch und einfache Skalierung. Der Größenbereich ist jedoch relativ größer als bei der Gaszerstäubung. Wird zur Herstellung kugelförmiger Pulver aus Metallen mit niedrigem Schmelzpunkt wie Zinn, Blei, Zink usw. verwendet.
Ultraschall-Gaszerstäubung
Kombiniert die Gaszerstäubung mit einem an die Düse gekoppelten Ultraschallgenerator. Die hochfrequenten Vibrationen verbessern den Zerfall und die Verteilung des Metalls in feinere Tröpfchen, wodurch ein Pulver im Submikronbereich entsteht.
Sehr effektiv zur Erzeugung nanokristalliner und amorpher Pulvermorphologien. Aber teuer und wartungsintensiv. Wird für spezielle Anwendungen verwendet.
Zerstäubung durch Funkenerosion
Bei dieser elektrischen Zerstäubungstechnik wird eine gepulste Hochstrom-Funkenentladung zwischen dem geschmolzenen Metall und einer Elektrodenspitze angelegt, wodurch ein Plasma entsteht, das das Metall in ultrafeines kugelförmiges Pulver zersetzt.
Ermöglicht die Herstellung sehr feiner, stark kugelförmiger Metallpulver. Aber niedrige Produktionsrate und hohe Kosten. Wird hauptsächlich für Edelmetalle wie Gold, Platin und Palladium verwendet.
Komponenten und Design des Zerstäubers
Zerstäuber bestehen aus einer Vielzahl von Komponenten, die zum effektiven Schmelzen, Gießen, Zerstäuben, Kühlen und Sammeln des Metallpulvers entwickelt wurden.
System zum Schmelzen und Gießen von Metallen
- Induktionsofen – Am häufigsten zum Schmelzen von Metallen wie Stahl verwendet. Ermöglicht eine gute Temperaturkontrolle und eine geringe Verunreinigung der Schmelze.
- Tiegel – Feuerfeste Keramiktöpfe, die zur Aufnahme von Metallladungen verwendet werden. Kann in einem separaten Ofen erhitzt und manuell gegossen oder direkt in das Zerstäubungssystem integriert werden.
- Tundish – Zwischenreservoir für geschmolzenes Metall, das die Gießgeschwindigkeit in den Zerstäubungsabschnitt steuert.
- Fallrohr – Leitet den Fluss des geschmolzenen Metalls präzise in die Zerstäubungszone. Hergestellt aus feuerfestem Metall wie Wolfram, um hohen Temperaturen standzuhalten.
- Pumpen – Wird zur Steuerung der druckgespeisten geschmolzenen Metallabgabe in bestimmten Zerstäuberkonfigurationen verwendet.
Zerstäubungsabschnitt
- Zerstäuberdüse – Spezielle, hochdruck- und temperaturbeständige Düsen zur Erzeugung von Gas- oder Wasserstrahlen zur Zerstäubung.
- Düsenanordnungen – Mehrere Spezialdüsen, strategisch positioniert, um die Tropfenbildung zu optimieren.
- Spinnkomponenten – Scheiben und Becher, die bei der Zentrifugalzerstäubung verwendet werden, rotieren mit sehr hohen Geschwindigkeiten – 10.000 bis 50.000 U/min, angetrieben durch einen Elektromotor.
- Ultraschallgenerator – Wandelt elektrische Signale in hochfrequente mechanische Schwingungen im Düsenbereich um. Wird bei der Ultraschallzerstäubung verwendet.
- Stromversorgung – Stellt den hohen Strom zur Erzeugung eines Lichtbogens für die Funkenerosionszerstäubung bereit.
Pulverhandhabungssystem
- Zyklonabscheider – Trennen Sie feines Pulver mithilfe von Zentrifugalkräften aus den Prozessgas- oder Wasserströmen.
- Beutelfilter – Sammeln Sie sehr feines Pulver, das nicht in Zyklonen abgeschieden wird. Muss häufig ausgetauscht werden.
- Bildschirmklassifikatoren – Größenklassifizierung von Pulver in verschiedene Fraktionen mithilfe von Maschensieben.
- Magnetische Separatoren – Entfernen Sie alle Fremdmetallverunreinigungen aus dem Pulver.
- Förderer – Transportiert Pulver zwischen Geräten. Schnecken-, Band- und Vibrationsförderer werden eingesetzt.
- Hopper – Lagert Pulver zur weiteren Verarbeitung oder Verpackung.
- Staubsaugen – Entfernt verschüttetes Pulver von Geräten und Oberflächen. Kritisch für reaktive Metallpulver.
Instrumentierung und Steuerung
- Temperatursensoren – Entscheidend für die Überwachung und Steuerung der Ofen-/Schmelze- und Düsentemperatur für eine optimale Zerstäubung.
- Drucksensor – Überwachen Sie den Gas- und Wasserdruck in den Düsen, um eine ordnungsgemäße Zerstäubung aufrechtzuerhalten.
- Durchflussmesser – Messen und steuern Sie die Durchflussraten von Zerstäubungsflüssigkeit und Schmelze.
- Drehzahlmesser – Überwacht die Rotationsgeschwindigkeit der Zentrifugalzerstäubungsscheiben.
- Füllstandsensoren – Sorgen Sie für optimale Schmelzwerte in wichtigen Gefäßen. Verhindert Überlauf.
- Not-Halt – Erforderlich für ein schnelles und sicheres Abschalten der Maschine im Störungsfall.
- Kontrollsystem – Die automatisierte Computersteuerung optimiert die Koordination der Parameter und verbessert die Wiederholbarkeit.
Parameter des Metallpulverzerstäubungsprozesses
Die richtige Auswahl der Prozessparameter ist der Schlüssel zur Herstellung von Pulvern mit den gewünschten Eigenschaften. Die folgende Tabelle fasst die wichtigsten Variablen und ihren Einfluss auf die Pulvereigenschaften zusammen:
Parameter | Auswirkung auf die Pulvereigenschaften |
---|---|
Temperatur von geschmolzenem Metall | Höhere Temperaturen verringern die Viskosität und verbessern die Zerstäubung. Kann jedoch die Oxidation und den Verdunstungsverlust erhöhen. |
Zerstäubungsgasdruck | Ein höherer Gasdruck verbessert die Partikelgrößenverteilung und verringert die Durchschnittsgröße. Aber erhöht den Gasverbrauch. |
Zerstäubungsgasdurchflussrate | Eine höhere Durchflussrate verbessert die Partikelgrößenreduzierung. Erhöht aber den Gasverbrauch. |
Zerstäubungsflüssigkeitsgeschwindigkeit | Eine höhere Geschwindigkeit verbessert die Partikelgrößenreduzierung. Abhängig vom Düsendesign. |
Düsendesign | Spezielle Düsen erzeugen feinere Tröpfchen und Pulver. |
Schmelzegießgeschwindigkeit | Höhere Gießgeschwindigkeiten erhöhen die Ausbeute bei kontinuierlichem Betrieb, können jedoch die Partikelgröße verringern. |
Überhitzung der Schmelze | Steigt, wenn die Gießtemperatur über den Schmelzpunkt steigt. Verbessert die Fließfähigkeit. |
Schmelzfiltration | Entfernt Einschlüsse und Verunreinigungen. Verbessert die Reinheit des Pulvers. |
Zerstäubungsabstand | Eine längere Freifallstrecke ermöglicht mehr Zeit für die Tropfenbildung. Reduziert die Satellitenbildung. |
Zusammensetzung schmelzen | Legierungselemente können die Viskosität und Oberflächenspannung verändern und so das Zerstäubungsverhalten und die Pulvereigenschaften beeinflussen. |
Charakterisierung von zerstäubtem Metallpulver
Die Eigenschaften und Qualität des zerstäubten Pulvers bestimmen die Leistung in nachgelagerten Anwendungen. Die wichtigsten bewerteten Merkmale sind:
Partikelgrößenverteilung
Die Verteilung von Pulverpartikeln über verschiedene Größenfraktionen, üblicherweise dargestellt als D10-, D50- und D90-Perzentil. Durch die Gaszerstäubung können weniger als 20 Mikrometer erreicht werden, während durch die Wasserzerstäubung ein gröberes Pulver erzeugt wird.
Partikelform und Morphologie
Gaszerstäubtes Pulver hat stark kugelförmige Partikel, während wasserzerstäubtes Pulver unregelmäßiger ist. Satellitenpartikel weisen auf eine mangelnde optimale Zerstäubung hin. Abgerundetes Pulver hat eine bessere Fließfähigkeit und Packungsdichte.
Chemische Zusammensetzung
Die Element- und Phasenzusammensetzung aus Untersuchungen. Bestimmt den Legierungsgrad. Die Gaszerstäubung erzeugt eine hohe Reinheit, während Wasser reaktive Metalle wie Titan und Aluminium verunreinigen kann.
Scheinbare und Klopfdichte
Indikator für die Effizienz der Pulververpackung. Eine höhere Dichte verbessert die Produkteigenschaften beim Pressen und Sintern. Kann aber den Pulverfluss beeinträchtigen. Werte typischerweise 40-65% Materialdichte.
Strömungseigenschaften
Wichtig für die Handhabung und Weiterverarbeitung. Beeinflusst durch Faktoren wie Partikelform, Größenverteilung, Oberflächenstruktur. Verbessert durch Glühen und Oberflächenbehandlung.
Mikrostruktur
Durch Mikroskopie sichtbare innere Pulverstruktur. Gaszerstäubtes Pulver weist feine Körner und Defekte aufgrund der schnellen Erstarrung auf, während wasserzerstäubtes Pulver gröber ist. Bestimmt das Sinterverhalten.
Anwendungen der Metallpulverzerstäubung
Zerstäubte Metallpulver finden vielfältige Einsatzmöglichkeiten in der modernen Fertigung und verbessern die Produktqualität und -leistung im Vergleich zur herkömmlichen Metallverarbeitung:
Additive Fertigung
- 3D-Druck – Zerstäubte kugelförmige Pulver mit kontrollierter Größenverteilung sind ideal für Pulverbett-Fusionstechniken. Üblicherweise werden Aluminium-, Titan- und Nickel-Superlegierungen verwendet.
- Metallspritzguss – Feinere Edelstahl-, Titan- und Aluminiumpulver verbessern den Sinterprozess und die Bauteildichte.
Pulvermetallurgie
- Pressen und Sintern – Unregelmäßiges, gröberes wasserzerstäubtes Eisenpulver, das für die hohe Produktion von P/M-Teilen mit guten mechanischen Eigenschaften verwendet wird.
- Weiche und harte Magnete – Feinkristalline NdFeB- und SmCo-Pulver ergeben leistungsstarke gebundene und heißgepresste Magnete.
- Reibungsmaterialien – Wasserzerstäubtes Kupferpulver verbessert die Leistung von Bremsbelägen und Kupplungsbelägen.
Oberflächenbeschichtungen
- Thermisches Spritzen – Kugelförmiges Pulver mit kontrollierter Größenverteilung, wichtig für gleichmäßige, dichte Beschichtungen mittels Plasma- oder HVOF-Spritzen. WC-Co, Nickellegierungspulver verwendet.
- Gasphasenabscheidung – Ultrafeines Superlegierungspulver-Ausgangsmaterial, das bei der physikalischen Gasphasenabscheidung mit Elektronenstrahlen für Turbinenbeschichtungen mit verbessertem Schutz verwendet wird.
Andere
- Metallspritzguss – Aus feinen Edelstahl-, Titan- und Aluminiumpulver-Ausgangsmaterialien können kleine, komplexe Komponenten hergestellt werden.
- Hartlötpasten – Zerstäubte Silber-, Gold- und Kupferlegierungen, die bei der Herstellung von Hochtemperatur-Lötverbindungen verwendet werden.
- Funkenerosion – Ultrafeines kugelförmiges Pulver, das als dielektrisches Medium verwendet wird, verbessert die Präzision und Geschwindigkeit der Erodierbearbeitung.
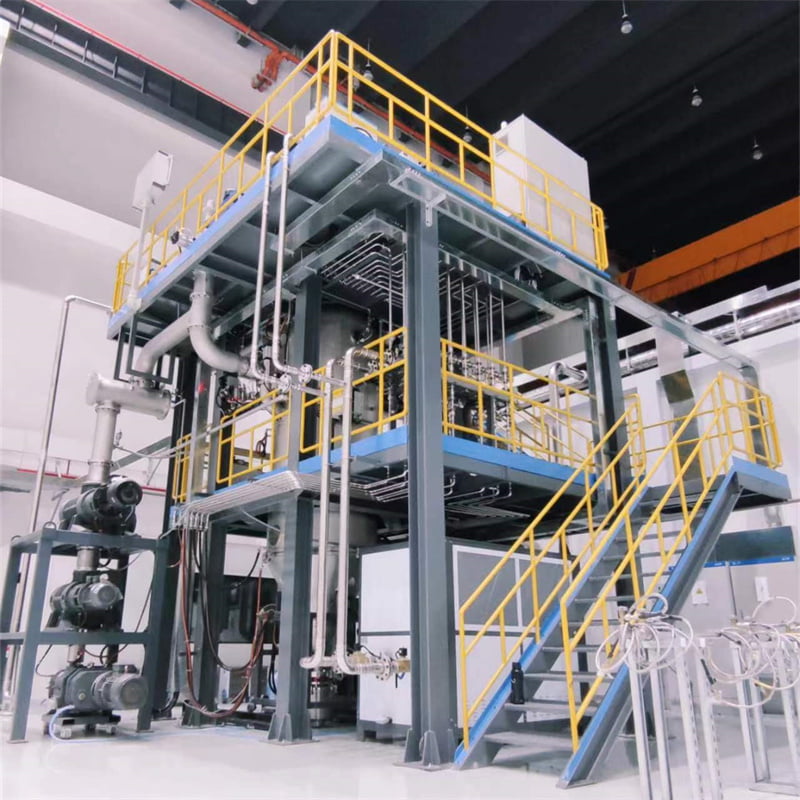
Vorteile der Metallpulverzerstäubung
Im Vergleich zu herkömmlichen Metallverarbeitungsmethoden gehören zu den wichtigsten Vorteilen der Verwendung von zerstäubten Pulvern:
- Verbesserte mechanische Eigenschaften – Feine, homogene Mikrostruktur durch schnelle Erstarrung erhöht Streckgrenze, Ermüdungslebensdauer und Duktilität.
- Präzise Maßkontrolle – Gleichmäßiges, kugelförmiges Pulver ermöglicht eine hohe Dichte und eine präzise Herstellung der Endform. Reduziert die Bearbeitung.
- Höhere Produktivität – Komponenten können durch die Metallpulververarbeitung schneller in Massenproduktion hergestellt werden als durch subtraktive Methoden.
- Größere Gestaltungsfreiheit – Es können komplexe Geometrien hergestellt werden, die durch Gießen oder Bearbeiten nicht möglich sind.
- Minimiert Abfall – Die nahezu endkonturnahe Fähigkeit reduziert den Schrottverlust im Vergleich zur Barrenmetallurgie. Nicht verwendetes Pulver kann recycelt werden.
- Geringerer Energieverbrauch – Der Pulverprozess erfordert eine geringere Temperatur und Energie als die Produktion aus Metallmassen.
- Kundenspezifische Legierungen – Es können spezielle Zusammensetzungen zerstäubt werden, die über Barren nur schwer herzustellen sind.
- Hohe Reinheit – Reaktive Elemente wie Titan können mit geringerer Kontamination zerstäubt werden als herkömmliche Verfahren.
Einschränkungen der Metallpulverzerstäubung
- Im Vergleich zur Massenmetallverarbeitung sind hohe Kapitalinvestitionen für Zerstäubungsgeräte und Pulverhandhabungssysteme erforderlich.
- Zur Herstellung von Produkten aus Pulvern sind zusätzliche nachgelagerte Prozesse wie Verdichten, Sintern usw. erforderlich. Der gesamte Produktionsweg ist komplex.
- Die Herstellung ultrafeiner Pulver im Nanomaßstab kann bei geringeren Durchsätzen schwierig und teuer sein.
- Mögliche Kontamination bei Verwendung der Wasserzerstäubung, insbesondere bei reaktiven Metallen.
- Pulver kann Sauerstoff und Feuchtigkeit absorbieren, was eine schützende Lagerung und Handhabung erfordert.
- Es bestehen Sicherheitsprobleme im Zusammenhang mit Staubexplosionen, Brandgefahr und Toxizität für bestimmte Pulverzusammensetzungen und -morphologien.
- Variabilität der endgültigen Komponenteneigenschaften im Vergleich zu bearbeiteten Produkten. Pulverbedingte Mängel können nach der Konsolidierung auftreten.
- Das Recycling und die Wiederverwendung von Metallpulver sind im Vergleich zu Massenmetallformen begrenzt. Das Material wird nach 1–2 Wiederverwendungszyklen entsorgt.
- Das Fehlen von Industriestandards für neuartige Metallpulver in Bezug auf Eigenschaften, Testmethodik, Qualitätskontrolle und Zertifizierung schafft Hindernisse für die Einführung.
Auswahl eines Metallpulverzerstäubungssystems
Die Auswahl der richtigen Zerstäubungsausrüstung für eine Anwendung hängt von folgenden Faktoren ab:
Produktionsvolumen
- Geringe Produktion – Zerstäuber im Labor- und Pilotmaßstab. Zentrifugal- oder Druckgaszerstäubungssysteme.
- Mittlere Produktion – Kontinuierliche Zerstäuber mit einer Pulverleistung von bis zu 3 Tonnen/Stunde.
- Hohe Produktion – Kundenspezifische Großanlagen mit einer Kapazität von mehr als 10 Tonnen/Stunde.
Pulverförmiges Material
- Nicht reaktive Metalle wie Stahl und Nickellegierungen können die Wasserzerstäubung nutzen.
- Wasserempfindliche Legierungen wie Aluminium und Titan benötigen eine Inertgaszerstäubung.
- Refraktäre Metalle wie Wolfram erfordern spezielle Zerstäubungsmedien und Schutz.
Pulvereigenschaften
- Gaszerstäubung für feineres Pulver unter 30 Mikrometer mit sphärischer Morphologie.
- Wasserzerstäubung für gröberes, unregelmäßiges Pulver zum Pressen.
- Spezialzerstäubung für nanokristallines oder amorphes Metallpulver.
Produktanwendung
- Bei der additiven Fertigung werden sehr feine, kontrollierte Partikelverteilungspulver aus der Gaszerstäubung verwendet.
- Beim Pulverspritzgießen ist feines, kugelförmiges Pulver mit guter Fließfähigkeit erforderlich.
- Für thermische Spritzbeschichtungen ist ein dichtes, kugelförmiges Pulver erforderlich, das sich gut verdichten lässt.
Kapital- und Betriebskosten
- Die Wasserzerstäubung verursacht geringere Geräte- und Betriebskosten, kann jedoch die Pulverqualität beeinträchtigen.
- Die Gaszerstäubung verursacht 10-mal höhere Kapitalkosten, erzeugt aber ein besseres Pulver. Auch die Betriebskosten sind höher.
- Die Zentrifugalzerstäubung ist wirtschaftlich, weist jedoch Größen- und Formbeschränkungen auf.
Pflanzenintegration
- Erfordert ausreichende Infrastruktur für Schmelzvorbereitung, Pulverhandhabung, Lagerung und Transport.
- Schutzsysteme für reaktive Metalle wie Inertgasatmosphäre.
- Automatisierte Kontrollen und Datenüberwachung verbessern die Prozessstabilität.
Führende Hersteller von Metallpulverzerstäubern
Mehrere Unternehmen bieten standardisierte und kundenspezifische Metallpulverzerstäubungssysteme und -komponenten an:
Gaszerstäubungssysteme
- Praxair – Marktführer für Hochdruck-Gaszerstäubungsgeräte. Bietet Systeme im Labor-, Pilot- und Produktionsmaßstab.
- AP&C – ist auf Gaszerstäuber mit direkt gekoppelter Düse für reaktive und hochschmelzende Metalle spezialisiert. Wird häufig für Titan- und Aluminiumpulver verwendet.
- ALD Vacuum Technologies – Entwickelt Mehrdüsen-Gaszerstäuber für mittlere bis hohe Produktion. Im Besitz von Oerlikon Metco.
Wasserzerstäubung
- Gasbarre – Bietet eine eng gekoppelte und frei fallende Wasserzerstäubung für mittlere bis große Mengen.
- Sheffield Atomising Systems – Seit über 50 Jahren auf Freifall-Wasserzerstäubungstechnologie spezialisiert.
Zentrifugale Zerstäubung
- ABB – Großer globaler Ausrüstungsanbieter. Bietet Zentrifugalzerstäubungssysteme im Labor- bis hin zum Produktionsmaßstab.
- Ferrum AG – Führender Anbieter von horizontalen und vertikalen Zentrifugalzerstäubern mit Sitz in der Schweiz.
Ultraschallzerstäubung
- Tekna – bietet Ultraschall-Gaszerstäubersysteme an, die auf ihrer patentierten Induktionsführungstechnologie mit gekoppelten Doppeldrähten basieren
- Ultramet – bietet spezielle Ultraschallzerstäubungsgeräte mit Hochtemperatur-Verflüssigertechnologie
Zerstäubung durch Funkenerosion
- PyroGenesis – bietet das Plasma Atomization System (PAS) zur Herstellung ultrafeiner kugelförmiger Metallpulver.
- Plasma Innovations – liefert die Funkenerosionszerstäubungssysteme mit rotierendem Elektrodenverfahren (REP).
Kostenanalyse von Metallpulverzerstäubern
Die Zerstäuberkosten hängen vom Maßstab, der Produktionsrate, dem Automatisierungsgrad und dem verarbeiteten Pulvermaterial ab. Typische Kapitalkostenschätzungen:
Großserien-Gaszerstäuber | Individuelles Gebäude | 1000 | 10 Millionen |
---|---|---|---|
Kleiner Wasserzerstäuber | Anhänger-/Containersystem | 100 | 750,000 |
Wasserzerstäuber für mittlere Produktion | Schutzsystem | 500 | 2 Millionen |
Großer Produktionswasserzerstäuber | Individuelles Gebäude | 2000 | 5 Millionen |
Pilot-Zentrifugalzerstäuber | Auf Kufe montiert | 50 | 400,000 |
Mittlerer Zentrifugalzerstäuber | Schutzsystem | 500 | 1,5 Millionen |
Labor-Ultraschallzerstäuber | Tischgerät | 5 | 250,000 |
Pilot-Ultraschallzerstäuber | Auf Kufe montiert | 20 | 1 Million |
Funkenerosionszerstäuber | Containersystem | 10 | 2 Millionen |
Betriebskosten
- Die Hauptkosten sind Energie, Arbeit, Wartung und Inertgasverbrauch.
- Der Stromverbrauch der Gaszerstäubung beträgt ca. 500–800 kWh pro Tonne Pulver. Gasverbrauch 5-10 m3 pro kg Pulver.
- Der Energieverbrauch der Wasserzerstäubung ist um ca. 200–400 kWh pro Tonne Pulver geringer. Aber höherer Arbeits- und Wartungsaufwand.
- Stromverbrauch der Zentrifugalzerstäubung ca. 300–500 kWh pro Tonne Pulver. Geringerer Inertgasverbrauch.
- Verschleißteile wie Düsen und Filterbeutel müssen häufig ausgetauscht werden.
Möglichkeiten zur Kostensenkung
- Die Erhöhung des Produktionsmaßstabs und der Pulverproduktion senkt die Kapitalkosten pro kg Pulver.
- Ein höherer Grad an Automatisierung und Überwachung verbessert die Arbeitsproduktivität.
- Das Recycling und die Wiederverwendung von Prozessgasen, Wasser und Abwärme senken die Betriebskosten.
- Vorbeugende Wartungsprogramme minimieren Ausfallzeiten und Wartungskosten.
- Die lokale Versorgung mit Energie, Gasen, Wasser und Nebendienstleistungen senkt die Logistikkosten.
- Der Kauf überholter/gebrauchter Zerstäubungssysteme reduziert den Kapitalaufwand für kleine Hersteller.
Ausrüstung zur Zerstäubung von Metallpulver – Häufig gestellte Fragen
F: Welcher typische Partikelgrößenbereich wird bei der Gaszerstäubung erreicht?
A: Durch Gaszerstäubung können Pulver mit einer Partikelgröße von 1 Mikrometer bis über 100 Mikrometer erzeugt werden. Typische D50-Werte liegen für die meisten Legierungen bei 10–45 Mikrometern. Mit optimierten Düsen und hohen Gasgeschwindigkeiten sind feinere Pulver unter 10 Mikrometer möglich.
F: Wie viel kann ein kleines Gaszerstäubersystem jährlich produzieren?
A: Ein Gaszerstäuber im Pilotmaßstab mit einer Leistung von 10 kg/h, der 5.000 Stunden im Jahr läuft, kann etwa 50.000 kg Pulver pro Jahr produzieren. Ein kleines Produktionssystem mit einer Kapazität von 50 kg/h kann bei voller Produktion etwa 250.000 kg pro Jahr produzieren.
F: Welche Arten von Metallen können zu Pulver zerstäubt werden?
A: Die meisten kommerziellen Legierungssysteme wurden zerstäubt, darunter Edelstahl, Werkzeugstahl, Nickellegierungen, Titanlegierungen, Aluminiumlegierungen, Superlegierungen, Kobaltlegierungen usw. Refraktäre Metalle wie Wolfram und Molybdän stellen eine Herausforderung dar und erfordern spezielle Zerstäubungssysteme.
F: Was ist die beste Zerstäubungsmethode für reaktive Metalle wie Titan?
A: Für reaktive Metalle wie Titan und Aluminium wird die Gaszerstäubung mit einem Inertgas wie Argon oder Stickstoff bevorzugt. Dies verhindert im Vergleich zur Wasserzerstäubung Oxidation und Kontamination.
F: Wie fein kann die Partikelgröße mit der Ultraschallzerstäubung erreicht werden?
A: Ultraschall-Gaszerstäuber können bei Optimierung Metallpulver im Submikron- und Nanobereich mit einer durchschnittlichen Größe von unter 100 Nanometern erzeugen. Die Pulverausstoßrate ist jedoch gering.
F: Kann Metallpulver nach der Verwendung in der additiven Fertigung recycelt werden?
A: Ja, nicht verwendetes Pulver kann in AM-Prozessen wiederverwendet werden. Das Pulver kann jedoch nur ein bis zwei Mal recycelt werden, bevor sich die Eigenschaften verschlechtern. Anschließend muss das Pulver zur weiteren Wiederverwendung erneut zerstäubt werden.
F: Wie geht man mit feinem reaktiven Pulver am besten um?
A: Inerte Handschuhboxen verwenden, Pulverbehälter verschließen und Kontakt mit Luft/Feuchtigkeit vermeiden. Einige reaktive Materialien erfordern möglicherweise eine Oberflächenbehandlung. Typischerweise wird wasserzerstäubtes Aluminiumpulver beschichtet, um Oxidation zu verhindern.
F: Warum ist hochreines Inertgas für die Gaszerstäubung wichtig?
A: Hohe Reinheit minimiert die Kontamination. Feuchtigkeit und Sauerstoff können reaktive Legierungen beim Zerstäuben oxidieren. Fremdgase können im Pulver eingeschlossen werden und zu Mängeln in den Endeigenschaften des Teils führen.
F: Wie einfach ist die Wartung und Reparatur eines Gaszerstäubers?
A: Die routinemäßige Wartung ist unkompliziert. Aber größere Reparaturen wie der Düsenaustausch können Tage dauern und erfordern Personal mit spezieller Schulung. Zusätzliche Düsenbaugruppen sollten für einen schnellen Austausch als Reserve bereitgehalten werden.
F: Welche Sicherheitsprobleme bestehen bei der Herstellung von Metallpulver?
A: Beim Umgang mit feinem Pulver besteht immer die Gefahr einer Staubexplosion. Weitere Bedenken sind Gefahren durch unter Druck stehendes Gas, Hochspannungsstrom, erhöhte Temperaturen und der Umgang mit geschmolzenem Metall, der Schutzausrüstung und Schulung erfordert.