The world of orthopedic implants is on the cusp of a materials revolution. While titanium often steals the spotlight with its exceptional strength and biocompatibility, a lesser-known contender is quietly proving its mettle: 316L powder. This versatile material, already a workhorse in various industries from aerospace to chemical processing, is emerging as a game-changer in the quest for stronger, more durable, and patient-friendly orthopedic solutions. Its unique combination of properties and affordability makes it a compelling choice for a wide range of implant applications.
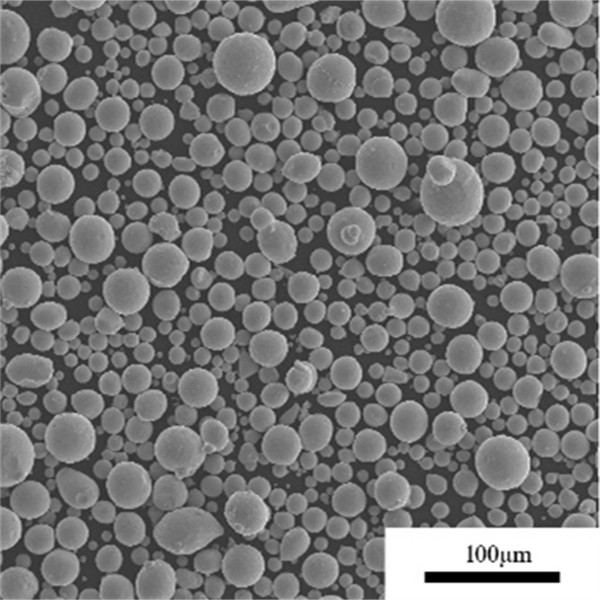
1. Biocompatibility: A Harmonious Partnership with the Human Body
First and foremost, any material destined for implantation within the human body must play nice with our intricate biological systems. It’s not enough to simply be strong – the material must coexist peacefully with tissues and fluids without triggering adverse reactions. 316L stainless steel, specifically the low-carbon variant (denoted by the “L”), excels in this regard, offering a level of biocompatibility that rivals even the most advanced materials:
- Resistencia a la corrosión: 316L’s high chromium content, along with the addition of molybdenum, creates a robust passive oxide layer on its surface, effectively shielding it from the corrosive environment within the body. This inherent resistance to corrosion is absolutely crucial for long-term implant stability, minimizing the risk of metal ion release into surrounding tissues, which could lead to inflammation, allergic reactions, or even implant loosening.
- Excelente biocompatibilidad: Decades of clinical use in various medical devices, from stents to bone plates, have demonstrated 316L’s exceptional biocompatibility. It elicits minimal immune response, meaning the body recognizes it as inert and doesn’t mount an attack. This makes it suitable for long-term implantation with a low risk of rejection, inflammation, or other adverse events that could compromise implant success.
2. Strength and Durability: Built to Endure the Test of Time
Orthopedic implants face a demanding task: supporting the human body in motion, day in and day out, for years on end. They must withstand the constant stresses of walking, running, lifting, and even just bearing the weight of the body without failing. 316L powder rises to the challenge, offering a unique combination of strength and durability that makes it suitable for a wide range of applications:
- High Tensile Strength: 316L implants can withstand significant tensile forces – the kind that pull on an object – without deforming or fracturing, ensuring their structural integrity even under strenuous activity levels. This is particularly crucial for load-bearing implants like hip and knee replacements, where the implant must bear the brunt of the body’s weight and the forces generated during movement.
- Excellent Fatigue Resistance: The repetitive stresses of daily life – think of the thousands of steps you take each day – can take a toll on implants, leading to fatigue and potential failure over time. 316L’s exceptional fatigue resistance, meaning its ability to withstand repeated cycles of stress without weakening, ensures long-term performance, minimizing the risk of premature implant failure and the need for costly and burdensome revision surgeries.
3. Precision Engineering: Shaping the Future of Implants
The advent of additive manufacturing, commonly known as 3D printing, has opened up new frontiers in implant design and fabrication, allowing engineers to break free from the limitations of traditional subtractive manufacturing methods. 316L powder is a key enabler of this revolution, offering a level of precision and design flexibility that was previously unimaginable:
- Diseños intrincados: 3D printing with 316L powder allows for the creation of implants with complex geometries and internal structures, mimicking the intricate architecture of natural bone. This includes features like porous scaffolds that encourage bone ingrowth for enhanced stability, as well as internal channels for drug delivery, allowing for targeted treatment directly at the implant site.
- Patient-Specific Solutions: Tailor-made implants, perfectly matched to a patient’s unique anatomy, are now within reach, thanks to the power of 3D printing and the versatility of 316L powder. This means surgeons can create implants that optimize fit, function, and patient comfort, minimizing the risk of complications and improving long-term outcomes. This is particularly valuable in complex cases involving trauma, bone deformities, or revision surgeries, where off-the-shelf implants simply won’t suffice.
4. Cost-Effectiveness: Making Quality Healthcare Accessible
While advanced materials and manufacturing techniques often come with a hefty price tag, potentially limiting access to life-changing treatments, 316L powder offers a compelling advantage: it delivers exceptional performance at a fraction of the cost of other high-performance materials.
- Producción rentable: 316L powder is relatively inexpensive compared to other implant-grade materials like titanium, while still offering excellent biocompatibility, strength, and durability. This cost advantage, coupled with the efficiencies of additive manufacturing, which minimizes waste and allows for on-demand production, makes 316L powder a cost-effective solution for producing high-quality orthopedic implants. This is particularly important in a healthcare landscape where cost containment is paramount, allowing for wider access to advanced treatments without compromising on quality or patient safety.
5. Applications: Where 316L Powder Shines
The unique properties of 316L powder – its biocompatibility, strength, durability, precision engineerability, and cost-effectiveness – make it suitable for a wide range of orthopedic applications, spanning from simple fracture fixation to complex joint replacements:
- Trauma Fixation: 316L powder is increasingly used to create plates, screws, rods, and other devices used to stabilize fractures and promote bone healing. Its strength and fatigue resistance ensure reliable fixation, while its biocompatibility minimizes the risk of adverse reactions. The ability to create patient-specific implants using 3D printing is particularly valuable in complex trauma cases, where precise anatomical fit is crucial for optimal healing.
- Implantes vertebrales: Spinal fusion cages, interbody devices, and other implants used in spinal fusion procedures are also being manufactured using 316L powder. These implants require a high degree of precision to ensure proper alignment and stability of the spine, and the design flexibility offered by 3D printing with 316L powder allows for the creation of implants that perfectly match the patient’s anatomy, promoting successful fusion and long-term pain relief.
- Joint Replacements: While titanium and cobalt-chrome alloys are often the go-to materials for joint replacements due to their exceptional wear resistance, 316L powder is emerging as a viable alternative for certain applications, particularly in younger, less active patients. Its lower cost makes it an attractive option, and ongoing research into surface treatments and processing techniques is further enhancing its wear resistance, potentially expanding its use in load-bearing joint replacements in the future.
- Implantes a medida: The true power of 316L powder shines in the realm of custom implants, where patient-specific solutions are paramount. From craniomaxillofacial implants used to reconstruct complex facial fractures to bone defect fillers for tumor resections, 316L powder allows surgeons to create implants that precisely match the patient’s anatomy and address their unique needs. This level of customization is revolutionizing orthopedic care, offering hope to patients with complex conditions who previously had limited treatment options.
316L Powder vs. Titanium: A Head-to-Head Comparison
Característica | Polvo 316L | Titanio |
---|---|---|
Biocompatibilidad | Excellent – Well-tolerated by the body with minimal immune response. | Excellent – Considered the gold standard for biocompatibility in orthopedic implants. |
Fuerza | High – Suitable for many applications, but not as strong as titanium. | Very High – Offers exceptional strength-to-weight ratio, ideal for load-bearing implants. |
Resistencia a la corrosión | Excellent – Highly resistant to corrosion due to its chromium oxide layer. | Excellent – Naturally forms a protective oxide layer, making it highly corrosion-resistant. |
Resistencia a la fatiga | Excellent – Withstands repeated stress cycles well, ensuring long-term performance. | Very High – Superior fatigue resistance compared to most other implant materials. |
Coste | Lower – More cost-effective than titanium, making it an attractive option for many applications. | Higher – Higher material and processing costs can make titanium implants more expensive. |
Maquinabilidad | Good – Can be machined using traditional methods, but excels in additive manufacturing. | More Difficult – Requires specialized tooling and expertise for machining. |
Aplicaciones | Trauma, Spine, Some Joints, Custom – Versatile material suitable for a wide range of applications. | Wide Range, Including Load-Bearing Joints – Preferred choice for demanding applications requiring high strength and wear resistance. |
FAQs: 316L Powder for Orthopedic Implants
1. How does the biocompatibility of 316L stainless steel compare to titanium for orthopedic implants?
Both 316L stainless steel and titanium are considered highly biocompatible materials with a long history of safe and successful use in orthopedic implants. They both exhibit excellent corrosion resistance and elicit minimal immune response, making them suitable for long-term implantation. Titanium is often considered the gold standard for biocompatibility, but 316L stainless steel offers a comparable level of biocompatibility at a lower cost.
2. What are the main advantages of using 316L powder in additive manufacturing for orthopedic implants?
316L powder is particularly well-suited for additive manufacturing (3D printing) of orthopedic implants due to its ability to be precisely melted and layered. This allows for the creation of implants with:
- Geometrías complejas: Intricate designs, such as porous scaffolds for bone ingrowth, are possible.
- Patient-Specific Fit: Implants can be tailored to match a patient’s unique anatomy.
- Rentabilidad: Additive manufacturing with 316L powder is generally more cost-effective than traditional subtractive manufacturing methods.
3. Is 316L stainless steel strong enough for load-bearing orthopedic implants?
While 316L stainless steel possesses good strength and fatigue resistance, it is not as strong as titanium. Therefore, it is currently more commonly used in applications with lower load-bearing requirements, such as trauma fixation and spinal implants. However, ongoing research into surface treatments and processing techniques is aiming to enhance the wear resistance of 316L stainless steel, potentially expanding its use in load-bearing joint replacements in the future.
4. What is the future outlook for the use of 316L powder in orthopedic implants?
The future of 316L powder in orthopedics is promising. As additive manufacturing technologies continue to advance and research leads to further improvements in the material’s properties, we can expect to see:
- Adopción más amplia: Increased use of 316L powder for a broader range of orthopedic implants.
- More Innovative Designs: Creation of implants with enhanced functionality, such as drug-eluting implants.
- Improved Cost-Effectiveness: Making advanced orthopedic treatments more accessible to patients.
5. What are the key considerations when choosing between 316L stainless steel and titanium for a specific orthopedic implant?
The choice between 316L stainless steel and titanium depends on the specific requirements of the implant and the patient’s needs. Factors to consider include:
- Load-Bearing Requirements: Titanium is preferred for high-load applications.
- Cost Sensitivity: 316L stainless steel offers a more cost-effective solution.
- Complejidad del diseño: Both materials are suitable for complex designs with additive manufacturing.
- Patient Factors: Surgeon preference and patient allergies (although rare) may also play a role.
FAQs: 316L Powder for Orthopedic Implants
1. Is 316L stainless steel a new material for orthopedic implants?
While 316L stainless steel might seem like a newcomer compared to titanium in the world of orthopedic implants, it actually boasts a long history of use in the medical field. It’s been successfully employed in various applications, including bone plates and screws, for decades. What’s new is the increasing use of 316L polvo in conjunction with additive manufacturing, opening up a new realm of possibilities for implant design and customization.
2. Why is corrosion resistance so crucial for orthopedic implants, and how does 316L powder measure up?
Corrosion resistance is paramount for any material implanted within the human body. Corrosion can weaken the implant, leading to premature failure, and release metal ions into surrounding tissues, potentially causing inflammation or allergic reactions. Fortunately, 316L stainless steel excels in this area. Its high chromium content, along with molybdenum, creates a tenacious passive oxide layer on its surface, effectively shielding it from the body’s corrosive environment. This ensures long-term implant stability and minimizes the risk of adverse reactions.
3. What makes 316L powder particularly well-suited for 3D printing of intricate implant designs?
3D printing, also known as additive manufacturing, involves building up an object layer by layer from a powdered material. 316L powder possesses ideal characteristics for this process. It melts consistently and predictably when subjected to the laser or electron beam used in 3D printing, allowing for precise control over the build process. This level of control is essential for creating complex geometries, such as porous structures that mimic natural bone, which are difficult or impossible to achieve with traditional manufacturing methods.
4. How does the cost-effectiveness of 316L powder benefit both healthcare providers and patients?
In an era of increasing healthcare costs, finding cost-effective solutions without compromising on quality is paramount. 316L powder offers a compelling advantage in this regard. The material itself is less expensive than titanium, and the additive manufacturing process minimizes waste, further reducing production costs. This translates into more affordable implants, making advanced orthopedic treatments accessible to a wider patient population.
5. What does the future hold for 316L powder in the evolving landscape of orthopedic care?
The future of 316L powder in orthopedics appears bright. As research continues to refine its properties and explore new surface treatments, we can anticipate its use expanding beyond its current applications. Furthermore, the ongoing advancements in additive manufacturing technology will unlock even greater design freedom, leading to more sophisticated and personalized implants. 316L powder is well-positioned to play a key role in the ongoing evolution of orthopedic care, bringing us closer to the goal of restoring mobility and improving the quality of life for countless individuals.
If you want to know everything, this guide will help:
Orthopedic Implant Powders: 10 Powerful Reasons for Industry Revolution