In the high-stakes realm of materials science, where strength, durability, and performance are paramount, Polvo de aleación de acero A100 emerges as a true game-changer. This exceptional material, meticulously engineered through the advanced process of powder metallurgy, is rapidly gaining traction across a multitude of industries. Why? Because A100 steel alloy powder empowers manufacturers to push the boundaries of what’s possible, crafting components that not only withstand extreme conditions but also deliver unparalleled performance, exceeding expectations in even the most demanding applications.
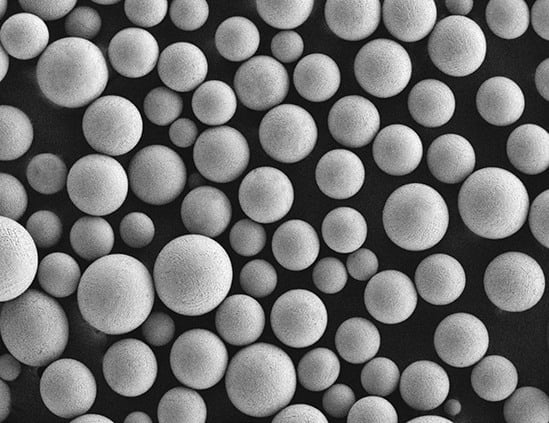
Join us as we embark on an exhilarating journey into the world of A100 steel alloy powder. We’ll delve deep into its unique composition, unravel the secrets behind its impressive properties, and explore the diverse applications where this powerhouse material is making a tangible difference, revolutionizing industries and setting new benchmarks for performance.
Deconstructing the Powerhouse: Understanding A100 Steel Alloy Powder
A100 steel alloy powder isn’t just another steel; it’s a carefully orchestrated symphony of elements, meticulously balanced to achieve a level of performance that sets it apart from the competition. Belonging to the family of high-strength, low-alloy steels, A100 is renowned for its remarkable toughness and weldability, making it a versatile choice for a wide range of applications. But what truly distinguishes A100 is its unique chemical composition, a carefully calibrated blend of elements that work synergistically to deliver exceptional results:
- Hierro (Fe): The very foundation of A100’s strength, iron provides the base structure upon which its exceptional properties are built. This abundant element forms the backbone of the material, providing inherent strength and stability.
- Carbono (C): Don’t let its small percentage fool you; carbon plays a pivotal role in A100’s performance. This crucial element enhances the steel’s hardness and tensile strength, making it exceptionally resistant to deformation and permanent change under stress, ensuring components maintain their integrity even under heavy loads.
- Manganeso (Mn): A multi-faceted contributor, manganese enhances A100’s hardenability, allowing it to achieve its impressive strength and toughness through heat treatment. Furthermore, manganese acts as a deoxidizer during the steelmaking process, ensuring a cleaner, more refined microstructure for enhanced performance.
- Cromo (Cr): While not present in large quantities, chromium provides A100 with a touch of corrosion resistance, enhancing its ability to withstand environmental exposure and resist the degrading effects of moisture, chemicals, and other corrosive agents. This added protection extends the lifespan of components, especially in demanding environments.
- Molibdeno (Mo): A key player in A100’s performance, molybdenum enhances its hardenability, ensuring it can achieve its optimal strength and toughness through heat treatment. Moreover, molybdenum boosts A100’s toughness, making it more resistant to fracturing under impact or shock loading, and enhances its resistance to creep, the gradual deformation that can occur under sustained stress at elevated temperatures.
This meticulously calibrated blend of elements, combined with the precision and control offered by powder metallurgy, transforms A100 steel alloy powder into a material capable of exceeding expectations in the most demanding applications.
Powder Metallurgy: The Secret Weapon Behind A100’s Performance
Unlike traditional steelmaking methods that involve melting and casting, which can introduce impurities and limit control over the material’s microstructure, A100 steel alloy powder is produced through the innovative process of powder metallurgy. This intricate and carefully controlled process involves a series of distinct steps, each designed to optimize the material’s properties and unlock its full potential:
- Atomización: The journey begins with molten steel, which is transformed into a fine powder through a highly controlled atomization process. This involves breaking down the liquid steel into tiny droplets, which solidify rapidly into fine particles with specific size and shape characteristics, ensuring uniformity and consistency in the starting material.
- Blending: Precision is key; the precisely measured elemental powders are thoroughly blended to ensure a completely homogeneous composition. This step is crucial for achieving consistent material properties throughout the final product, eliminating variations that could compromise performance.
- Compaction: The blended powder is then carefully loaded into a die and subjected to extremely high pressure, compacting it into a “green” compact with the desired shape. This high-pressure compaction process brings the powder particles into close contact, creating the initial bonds that will be solidified during sintering.
- Sinterización: The green compact is then placed in a controlled atmosphere furnace and heated to a specific temperature, below the melting point of the base metal. This high-temperature sintering process causes the powder particles to bond together through solid-state diffusion, forming a dense, near-net-shape component with the desired properties.
This meticulous multi-step process, a hallmark of powder metallurgy, gives manufacturers unparalleled control over the material’s microstructure and properties, resulting in:
- Exceptional Purity and Homogeneity: Powder metallurgy minimizes the risk of impurities and ensures a uniform distribution of alloying elements throughout the material. This homogeneity is crucial for consistent and predictable performance, ensuring that every batch of A100 steel alloy powder meets the highest standards.
- Near-Net-Shape Components: The ability to form complex shapes directly from powder, bypassing traditional casting and machining limitations, reduces the need for costly and time-consuming secondary operations. This not only saves time and resources but also allows for the creation of intricate geometries that would be difficult or impossible to achieve through other manufacturing methods.
- Tailored Microstructures: Powder metallurgy empowers manufacturers to fine-tune the microstructure of A100 components with a level of control unmatched by other techniques. By carefully controlling parameters like powder particle size, compaction pressure, and sintering temperature, manufacturers can optimize grain size, distribution of strengthening phases, and porosity to achieve very specific mechanical and physical properties tailored to the application’s exact demands.
Why Choose A100 Steel Alloy Powder? Unveiling the Advantages
A100 steel alloy powder isn’t just another material option; it’s a strategic investment in performance, durability, and reliability, offering a compelling combination of advantages that can significantly enhance your products and processes:
- Fuerza y resistencia excepcionales: A100 steel alloy powder stands out for its impressive combination of high strength and toughness. This means it can withstand heavy loads, resist impact and shock, and endure harsh operating conditions without fracturing or failing. Its high tensile strength allows it to withstand pulling forces, while its impressive yield strength ensures it can resist deformation under stress, making it ideal for components subjected to heavy loads and demanding environments.
- Excelente soldabilidad: Unlike some high-strength steels that can become brittle or lose their toughness when welded, A100 retains its excellent weldability, even after heat treatment. This makes it ideal for fabricating complex structures and assemblies where welding is essential, without compromising its mechanical properties or risking weak points in the final product.
- Good Fatigue Resistance: Components in many applications are subjected to repeated cycles of stress and strain, which can lead to fatigue failure over time. A100 steel alloy powder exhibits good fatigue resistance, meaning it can withstand these repeated cycles without succumbing to fatigue cracks and premature failure, ensuring long-term reliability and performance in demanding applications.
- Rentabilidad: While the initial cost of A100 steel alloy powder might be slightly higher than some conventional steels, its superior properties often translate into long-term cost savings. The ability to create near-net-shape components reduces machining costs, while its enhanced durability and lifespan minimize replacement and maintenance expenses, making it a cost-effective choice in the long run.
A100 Steel Alloy Powder in Action: Real-World Applications
The exceptional combination of strength, toughness, weldability, and cost-effectiveness makes A100 steel alloy powder a highly sought-after material across a wide range of industries, enabling the creation of high-performance components for the most demanding applications:
1. Automotive Industry: Driving Performance and Safety
- Gears and Shafts: In the heart of every vehicle’s drivetrain, gears and shafts are subjected to immense torque and rotational forces. A100’s high strength and fatigue resistance make it an ideal material for these critical components, found in transmissions, axles, differentials, and other demanding applications, ensuring smooth power transmission, durability, and reliable performance under high stress and speed.
- Suspension Components: Suspension systems are crucial for a vehicle’s handling, stability, and overall safety. A100’s strength and toughness make it exceptionally well-suited for critical suspension components like control arms, knuckles, spindles, and even spring seats, ensuring these components can withstand the constant stresses of bumps, potholes, and cornering maneuvers, contributing to a safe and controlled ride.
- Safety-Critical Parts: When it comes to passenger safety, there’s no room for compromise. A100’s high strength, impact resistance, and weldability make it a suitable material for safety-critical components like seatbelt anchors, airbag deployment mechanisms, steering system parts, and even crumple zones, where material performance directly impacts the vehicle’s ability to protect occupants in the event of a collision.
2. Construction and Mining Equipment: Building for Strength and Durability
- Excavator Buckets and Teeth: In the unforgiving world of construction and mining, excavator buckets and teeth are subjected to constant wear and tear from digging, scooping, and moving heavy materials. A100’s exceptional wear resistance, impact strength, and ability to be heat-treated to very high hardness levels make it an ideal material for these components, extending their lifespan, reducing downtime, and lowering operating costs in these demanding industries.
- Crusher Components: Crushing and grinding operations in mining and quarrying require materials that can withstand extreme impact and abrasion. A100’s high strength, toughness, and wear resistance make it well-suited for crusher jaws, cones, mantles, and other wear-resistant components, ensuring these machines can handle the toughest materials and deliver reliable performance under extreme conditions.
- Componentes estructurales: From massive cranes to powerful bulldozers, construction and mining equipment rely on strong and durable structural components. A100 steel alloy powder can be used to create robust booms, arms, frames, chassis components, and other structural elements, ensuring the equipment can withstand heavy loads, resist fatigue, and endure harsh operating conditions, maximizing its lifespan and productivity.
3. Energy Industry: Powering a Reliable Future
- Wind Turbine Components: Harnessing the power of wind requires robust and reliable turbines capable of withstanding constant stress and harsh environmental conditions. A100’s high strength, fatigue resistance, and weldability make it a suitable material for critical wind turbine components like gearbox housings, yaw rings, main shafts, and even blade bearings, ensuring these massive structures can operate reliably for years, generating clean energy with minimal downtime.
- Oil and Gas Pipelines: Transporting oil and gas over long distances, often through challenging terrain and under extreme pressure, requires pipelines built to withstand the test of time. While not as corrosion-resistant as some specialized alloys, A100’s high strength and toughness make it suitable for certain pipeline applications, particularly for transporting high-pressure fluids or in environments where impact resistance is crucial, providing a balance of strength, durability, and cost-effectiveness.
- Valves and Fittings: Controlling the flow of oil and gas, often under extreme pressure and in corrosive environments, requires valves and fittings built to exacting standards. A100’s strength, toughness, weldability, and resistance to pressure make it a suitable material for these demanding applications, ensuring these critical components maintain their integrity and prevent leaks, ensuring the safe and efficient operation of oil and gas infrastructure.
Benchmarking A100: Comparing Properties
Propiedad | A100 Steel Alloy Powder | 4140 Steel | 300M Steel |
---|---|---|---|
Resistencia a la tracción | Alta | Moderado | Muy alta |
Límite elástico | Alta | Moderado | Muy alta |
Dureza | Excelente | Bien | Bien |
Soldabilidad | Excelente | Bien | Moderado |
Coste | Moderado | Baja | Más alto |
A100 vs. 4140 Steel: When compared to 4140 steel, a commonly used medium-carbon steel known for its versatility, A100 emerges as a higher-performance option. A100 offers superior strength, toughness, and weldability compared to 4140. While 4140 might be more cost-effective for less demanding applications, A100 excels when a combination of high strength, toughness, and weldability is required, justifying its use in components subjected to greater stress, impact, or fatigue.
A100 vs. 300M Steel: Both A100 and 300M are high-strength steels, often considered for demanding applications where strength is paramount. However, they have distinct characteristics that make them suitable for different use cases. 300M generally exhibits higher strength and hardness, making it suitable for applications requiring extreme wear resistance or the ability to withstand very high loads. However, A100 offers better weldability and is often more cost-effective, making it a more practical choice for many applications where extreme strength is not the primary requirement and where ease of fabrication and cost considerations are important factors.
The Future of A100 Steel Alloy Powder: Innovation and Beyond
The world of materials science is in a constant state of evolution, and A100 steel alloy powder is no exception. Researchers and manufacturers are continuously exploring new frontiers, seeking innovative ways to enhance its properties, expand its applications, and unlock its full potential, pushing the boundaries of what’s possible with this versatile material:
- Advanced Additive Manufacturing: Metal additive manufacturing techniques, such as laser powder bed fusion (LPBF) and binder jetting, are rapidly transforming the manufacturing landscape, and A100 steel alloy powder is at the forefront of this revolution. These advanced additive manufacturing technologies are opening up new possibilities for creating complex A100 components with intricate geometries, internal features, and optimized designs, allowing engineers to create parts with enhanced performance, reduced weight, and customized properties, further expanding its potential applications.
- Surface Engineering: The surface of a material is often the first line of defense against wear, corrosion, and fatigue. Researchers are exploring advanced surface treatments, such as coatings, nitriding, and laser peening, to further enhance the surface properties of A100 components. These treatments can create even more durable surfaces, improve wear and corrosion resistance, and enhance fatigue life, extending the lifespan of components, expanding their potential applications in harsh environments, and reducing maintenance requirements.
- Alloy Optimization: The quest for the perfect material is an ongoing endeavor, and A100 steel alloy powder is no exception. Ongoing research focuses on fine-tuning the chemical composition of A100, exploring the addition of new alloying elements, and optimizing processing parameters to achieve even better combinations of strength, toughness, weldability, and other desirable properties. These advancements could lead to the development of new A100 grades with enhanced performance characteristics, tailored to meet the ever-increasing demands of industries seeking high-performance materials for the most challenging applications.
If you want to know everything, this guide will help:
Iron-Based Alloy Powders: Ultimate Complete Guide to Excellence