In the meticulously controlled realm of chemical production, where precision reigns supreme and consistency is paramount, the relentless pursuit of creating high-quality products – from specialized coatings with exacting specifications to pharmaceutical ingredients demanding impeccable purity – hinges on the ability to master reactions, particle sizes, and material properties with unwavering accuracy. This is where atomización equipment takes center stage, often operating diligently behind the scenes yet playing an absolutely essential role in a vast and diverse array of chemical processes.
Far from being a one-size-fits-all solution, atomization encompasses a sophisticated and ever-evolving landscape of techniques and specialized equipment, each meticulously optimized for specific applications within the intricate tapestry of the chemical industry. Join us on a journey as we delve deep into the fascinating world of atomization, exploring the intricacies of this transformative technology and how it’s shaping the present and future of chemical production.
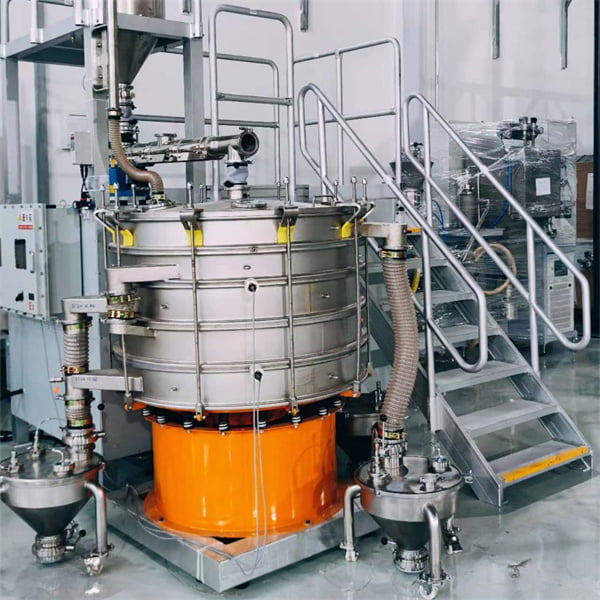
Why Atomization Matters in Chemical Production: A Foundation of Precision and Control
Imagine, for a moment, the remarkable ability to transform a thick, viscous polymer solution into a fine, ethereal mist, a delicate dance of particles that coats a surface with impeccable evenness, creating a durable, protective layer that stands as a bulwark against the relentless forces of wear and tear. Or picture the power to conjure perfectly spherical catalyst particles, each one a miniature marvel of engineering with precisely controlled size and porosity, meticulously designed to optimize a chemical reaction with unparalleled efficiency and yield. These captivating scenarios offer but a glimpse into the transformative power of atomization in the realm of chemical production.
Let’s delve deeper into the compelling reasons why this technology has become an indispensable tool in the chemist’s arsenal:
- Exquisite Control Over Particle Size & Distribution: The Cornerstone of Consistency: In the intricate and often unpredictable world of chemical processes, the size and uniformity of particles often hold the key to unlocking the desired properties of the final product. Atomization empowers manufacturers with the ability to achieve incredibly tight control over particle size distribution, ensuring batch-to-batch consistency, guaranteeing process reproducibility, and ultimately delivering products that consistently meet the most stringent performance standards.
- Enhanced Reaction Kinetics & Unparalleled Efficiency: Accelerating Reactions with Finesse: By ingeniously generating smaller droplets or particles, each boasting a significantly larger surface area for interaction, atomization acts as a catalyst, accelerating reaction rates, promoting more efficient mixing, and enhancing mass transfer – all of which culminate in faster, more efficient, and cost-effective chemical processes, maximizing output while minimizing waste.
- Uncompromising Product Quality & Performance: Engineering Excellence at the Microscopic Level: Whether the goal is to create flawlessly uniform coatings that protect and enhance, synthesize nanoparticles with meticulously tailored properties for cutting-edge applications, or produce pharmaceuticals with precisely controlled release profiles for optimal therapeutic effect, atomization emerges as the enabling technology, empowering manufacturers to achieve superior product quality and performance that consistently exceeds expectations.
- Minimized Waste & a Reduced Environmental Footprint: A Pathway to Sustainable Production: In an era of heightened environmental consciousness, where sustainability is no longer a choice but an imperative, atomization processes often shine as beacons of responsible manufacturing, minimizing waste generation compared to traditional methods and contributing to a cleaner, greener, and more environmentally responsible chemical industry, paving the way for a more sustainable future.
5 Key Applications of Atomization Equipment in Chemical Production: A Versatile Toolkit for Innovation
Atomization, far from being a one-size-fits-all approach, stands as a testament to versatility – a technology tailored to address specific challenges and achieve desired outcomes across a diverse and ever-expanding spectrum of chemical processes.
1. Spray Drying: The Art of Transforming Solutions into Free-Flowing Powders
In the realm of chemical production, where the transformation of matter from one form to another is an everyday endeavor, spray drying reigns supreme, widely recognized for its remarkable ability to transform liquid solutions, slurries, or suspensions into dry, free-flowing powders with meticulously controlled particle characteristics. This elegant and highly efficient process involves atomizing the liquid feed into a carefully controlled drying chamber, where a precisely regulated stream of hot gas, typically air, facilitates the rapid evaporation of the solvent, leaving behind the desired solid product in a convenient, easily handled, and readily transportable powder form.
Característica | Descripción | Beneficios |
---|---|---|
Proceso | Atomization of liquid feed into a temperature-controlled drying chamber, where rapid solvent evaporation occurs | Highly efficient, easily scalable from laboratory to industrial production levels, and well-suited for processing heat-sensitive materials that require gentle handling |
Tamaño de las partículas | Typically ranging from micrometers to millimeters, offering a wide range of possibilities | Offers exceptional control over particle size distribution, enabling manufacturers to fine-tune flowability, solubility, and reactivity for specific applications, ensuring optimal performance |
Aplicaciones | Extensively used in the production of pigments, catalysts, ceramics, pharmaceuticals, detergents, and a wide range of food additives, showcasing its versatility | A highly versatile and widely adopted technique suitable for a diverse array of chemical products, making it an indispensable tool in many industries |
2. Spray Coating: The Science of Creating Durable & Functional Surfaces
From the protective coatings that shield our cars from the ravages of weather and time to the non-stick surfaces that make our culinary endeavors a delight, spray coating plays an indispensable role in enhancing the functionality and durability of countless products we rely on daily. In the realm of chemical production, atomization emerges as the cornerstone of this transformative process, enabling the application of uniform coatings with precise thickness control, ensuring optimal performance, longevity, and a flawless finish.
Key Applications:
- Protective Coatings: Shielding Surfaces from the Elements: Creating robust, corrosion-resistant coatings on metal surfaces, extending their lifespan and protecting them from the elements; applying impenetrable barrier coatings on packaging materials to preserve freshness and prevent contamination; and formulating weather-resistant coatings on building materials to withstand the test of time and maintain structural integrity.
- Functional Coatings: Adding Value and Functionality: Applying conductive coatings in the intricate world of electronics, enabling the flow of electrons and facilitating communication; depositing anti-reflective coatings on lenses for crystal-clear optics, minimizing glare and maximizing light transmission; and integrating catalytic coatings within chemical reactors to accelerate and optimize reactions, increasing efficiency and yield.
3. Chemical Reactor Engineering: The Quest for Optimizing Reaction Conditions
Within the controlled environment of a chemical reactor, where reactions unfold with calculated precision and every parameter is carefully monitored, atomization plays a pivotal role in orchestrating the perfect environment for optimal outcomes, ensuring that reactions proceed efficiently and yield the desired products. By ensuring efficient mixing, maximizing contact between reactants, and meticulously controlling reaction temperature, atomization empowers chemical engineers to fine-tune reactions with remarkable accuracy, achieving the desired results with minimal waste and maximum yield.
Key Applications:
- Gas-Liquid Reactions: Enhancing Mass Transfer for Faster Reactions: In processes like oxidation, hydrogenation, and combustion, where the interaction between gases and liquids is crucial, atomization takes center stage, transforming liquids into a fine mist of droplets within gas streams, dramatically enhancing mass transfer and accelerating reaction rates for increased efficiency and productivity.
- Liquid-Liquid Reactions: Creating Intimate Mixtures for Optimal Reactivity: Creating exquisitely fine dispersions of immiscible liquids, atomization acts as a bridge, improving mixing and reaction efficiency in critical processes like polymerization, emulsification, and extraction, ensuring that reactants have ample opportunity to interact and form the desired products.
4. Nanoparticle Synthesis: The Art of Engineering Materials at the Nanoscale
Nanomaterials, with their extraordinary properties that defy conventional limitations and seemingly limitless potential applications, are rapidly transforming industries, from medicine to electronics, holding the promise of a future where materials are engineered at the atomic level. At the heart of this nanotechnology revolution lies atomization, a critical enabling technology for synthesizing nanoparticles with meticulously controlled size, shape, and composition, unlocking their full potential and paving the way for a new era of material science.
Key Applications:
- Production of Metal Nanoparticles: Unlocking the Potential of Noble Metals: Atomization techniques are instrumental in creating nanoparticles of silver, gold, platinum, and other metals, unlocking their unique properties for applications in catalysis, electronics, and even targeted drug delivery in medicine, where their small size and high surface area offer unprecedented advantages.
- Synthesis of Ceramic Nanoparticles: Engineering Ceramics with Atomic Precision: Producing ceramic nanoparticles with tailored characteristics is essential for developing high-performance ceramics, more efficient catalysts, and highly sensitive sensors, pushing the boundaries of material science and enabling the creation of materials with unprecedented properties.
5. Pharmaceutical Manufacturing: The Precision of Delivering Targeted Therapies
In the world of pharmaceutical manufacturing, where precision and efficacy are paramount and even the slightest deviation from specifications can have significant consequences, atomization emerges as a critical technology for creating advanced drug delivery systems that enhance drug effectiveness, improve patient compliance, and minimize unwanted side effects, leading to better patient outcomes.
Key Applications:
- Production of Dry Powder Inhalers (DPIs): Targeting the Respiratory System with Precision: Atomization is the driving force behind the creation of micronized drug particles specifically engineered for pulmonary delivery, allowing for direct targeting of the respiratory system with minimal systemic exposure, improving efficacy and reducing side effects.
- Microencapsulation of Drugs: Protecting and Delivering Active Ingredients with Precision: By encapsulating drug molecules within protective shells, atomization enables controlled drug release profiles, improves drug stability, masks unpleasant tastes, and enhances the overall patient experience, making medications easier to take and improving adherence to treatment regimens.
Essential Atomization Equipment for Chemical Production: The Tools of Precision Engineering
Achieving the remarkable level of precision and control required in these intricate chemical processes demands a sophisticated arsenal of specialized equipment, each piece meticulously designed to meet the stringent demands of the industry and ensure consistent, high-quality results, meeting the exacting specifications of modern chemical manufacturing.
Here are some key players in the atomization equipment lineup, the workhorses of precision engineering:
- Spray Dryers: The Cornerstone of Powder Production: Available in a wide range of configurations, from compact lab-scale models used for research and development to massive industrial-scale systems capable of handling tons of material per hour, spray dryers are the workhorses of powder production, transforming liquid feeds into dry powders with precisely controlled particle properties, meeting the demands of various industries.
- Spray Nozzles: The Precision Delivery System: Often considered the heart of any spray-based atomization process, spray nozzles are available in a dizzying array of designs, each optimized for specific applications, flow rates, and droplet size requirements, ensuring the precise delivery of liquids for optimal results, ensuring consistent and repeatable performance.
- Atomizers: Harnessing the Power of Physics: These ingenious devices employ a variety of methods, from ultrasonic vibration and compressed air to electrostatic forces, to generate fine droplets or particles from liquids, expanding the possibilities for atomization across various applications, providing flexibility and precision in particle size control.
- Fluid Bed Processors: Masters of Drying, Granulation, and Coating: While primarily known for their roles in drying, granulation, and coating processes, fluid bed processors also find applications in certain chemical reactions where precise control over temperature and gas-solid contact is paramount, ensuring uniform processing and optimal reaction conditions.
- Electrospinning & Electrospraying Equipment: Pioneers in Nanomaterial Fabrication: These specialized systems harness the power of electrostatic forces to generate incredibly fine nanofibers and nanoparticles from polymer solutions and other materials, opening up exciting possibilities in nanotechnology and materials science, enabling the creation of materials with unprecedented properties and applications.
The Future of Chemical Production: Atomization at the Forefront of Innovation
As the chemical industry continues its relentless evolution, driven by the insatiable demands for greater efficiency, sustainability, and the development of novel materials and products that push the boundaries of innovation, atomization technology will undoubtedly play an increasingly vital role, shaping the future of the industry and enabling the creation of a more sustainable and technologically advanced future.
Here are some key trends on the horizon that are poised to further elevate the importance of atomization in chemical production, driving progress and shaping the industry of tomorrow:
- Miniaturization & Microfluidics: The Quest for Smaller, More Efficient Devices: The relentless march towards smaller, more efficient devices is fueling the development of microfluidic atomizers, capable of generating highly uniform droplets and particles at incredibly low flow rates, opening up new possibilities for precision and control, miniaturizing devices, and reducing waste.
- Process Intensification: Maximizing Efficiency and Minimizing Environmental Impact: Atomization is playing a pivotal role in the development of more compact, efficient, and sustainable chemical processes by intensifying reaction rates, minimizing waste generation, and reducing energy consumption, aligning with the industry’s commitment to environmental responsibility and paving the way for a greener future.
- Smart & Adaptive Atomization: The Rise of Intelligent Manufacturing: The integration of sophisticated sensors, advanced control systems, and powerful machine learning algorithms is paving the way for the development of “smart” atomization systems that can adapt to changing process conditions in real-time, optimizing performance, and ensuring consistent, high-quality results, ushering in an era of intelligent manufacturing where precision and adaptability reign supreme.
FAQs: Delving Deeper into Atomization in Chemical Production
1. What are the primary advantages of using atomization techniques in chemical production compared to traditional methods?
Atomization offers several key advantages over traditional methods, including:
- Control mejorado: Achieve precise control over particle size, distribution, and morphology, leading to consistent product quality and performance.
- Mayor eficiencia: Accelerate reaction rates, improve mixing, and enhance mass transfer, resulting in faster, more efficient processes.
- Improved Product Quality: Create products with superior properties, including uniformity, purity, and controlled release profiles.
- Reduced Waste & Environmental Impact: Minimize waste generation and energy consumption, contributing to a more sustainable chemical industry.
2. Can you provide some specific examples of how atomization is used in the pharmaceutical industry?
Atomization plays a crucial role in pharmaceutical manufacturing, enabling the production of:
- Dry Powder Inhalers (DPIs): Creating micronized drug particles for targeted pulmonary delivery, enhancing efficacy and reducing systemic side effects.
- Microencapsulated Drugs: Encapsulating drug molecules within protective shells for controlled release, improved stability, and enhanced patient compliance.
- Injectable Suspensions: Formulating suspensions with uniform particle size distribution for optimal drug delivery and bioavailability.
3. What types of atomization equipment are commonly used in the chemical industry?
The chemical industry relies on a diverse range of atomization equipment, including:
- Spray Dryers: Transforming liquid feeds into dry powders with controlled particle characteristics.
- Spray Nozzles: Delivering liquids with precise flow rates and droplet sizes for various coating and reaction applications.
- Atomizers: Generating fine droplets or particles using methods like ultrasonic vibration, compressed air, or electrostatic forces.
- Fluid Bed Processors: Facilitating drying, granulation, and coating processes, as well as certain chemical reactions.
- Electrospinning & Electrospraying Equipment: Producing nanofibers and nanoparticles for advanced material applications.
4. How is atomization technology evolving to meet the future demands of chemical production?
Atomization technology is continuously evolving, driven by trends such as:
- Miniaturization & Microfluidics: Developing smaller, more efficient atomizers for precise control at low flow rates.
- Process Intensification: Integrating atomization into compact, efficient, and sustainable chemical processes.
- Smart & Adaptive Atomization: Incorporating sensors, control systems, and machine learning for real-time process optimization.
5. What are the key considerations when selecting atomization equipment for a specific chemical process?
Choosing the right atomization equipment requires careful consideration of factors such as:
- Desired Particle Size & Distribution: Matching equipment capabilities to the specific particle characteristics required.
- Propiedades del material: Considering factors like viscosity, surface tension, and thermal sensitivity of the material being atomized.
- Production Scale & Throughput: Selecting equipment with appropriate capacity and scalability for the desired production volume.
- Process Requirements: Evaluating factors like temperature control, residence time, and environmental considerations.
- Cost & Maintenance: Balancing equipment cost with operational expenses, maintenance requirements, and overall lifecycle costs.