Manufacturing Processes of CuSn40 Powder
CuSn40 powder, a versatile alloy with a wide range of applications, can be produced through various manufacturing processes. The choice of method often depends on the desired particle size, shape, and properties of the final product. Here are some of the most common techniques used to manufacture CuSn40 powder:
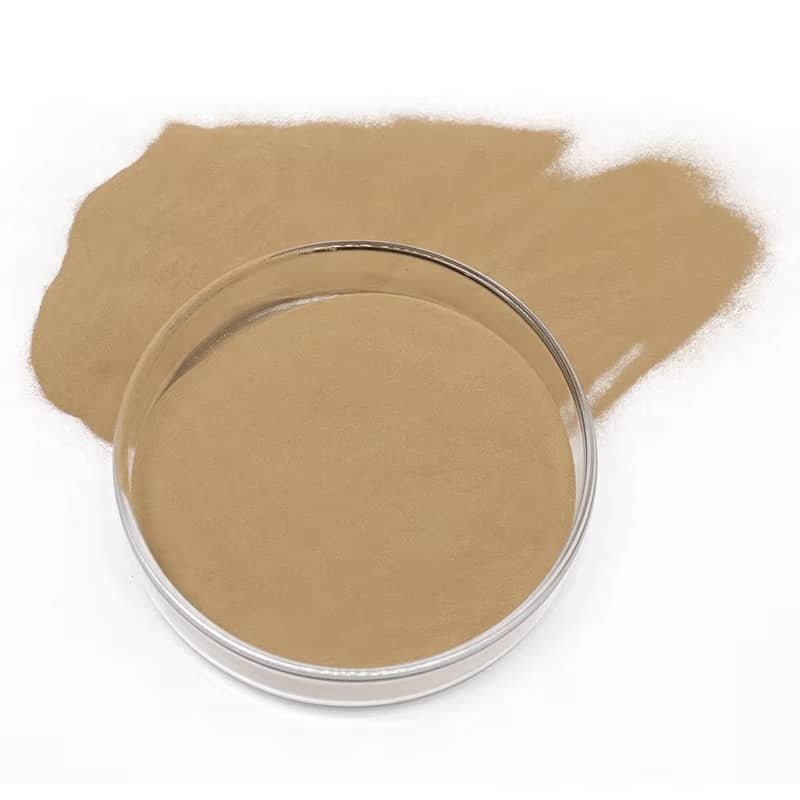
Atomización de gases
Gas atomization is a widely used method for producing metal powders, including CuSn40. In this process, molten metal is poured into a chamber filled with a high-velocity gas, such as nitrogen or argon. The gas breaks the molten metal into tiny droplets, which solidify rapidly to form spherical or near-spherical particles.
- Produces spherical particles with a narrow size distribution
- Alta pureza y baja contaminación
- Adecuado para una amplia gama de aleaciones
- Relatively high energy consumption
- Potential for gas entrapment in the powder
Atomización del agua
Water atomization is similar to gas atomization, but uses water instead of gas to break up the molten metal. The water is typically injected into the molten metal stream at high pressure, creating a fine mist that cools and solidifies the metal droplets.
- Lower energy consumption than gas atomization
- Can produce finer particles
- Suitable for alloys with lower melting points
- Potential for water contamination in the powder
- Limited control over particle shape
Aleación mecánica
Mechanical alloying is a solid-state process that involves the repeated deformation and re-formation of a mixture of metal powders. The powders are typically confined in a ball mill and subjected to intense mechanical energy, which causes them to cold-weld and fracture. This process can be used to produce CuSn40 powder with a homogeneous composition and a fine microstructure.
- Can produce powders with unique microstructures
- Suitable for alloys with high melting points
- Bajo consumo de energía
- Slow process
- Potential for contamination from the ball mill
Pulverización de plasma
Plasma spraying is a thermal spraying process that can be used to produce CuSn40 powder. In this process, a plasma torch is used to create a high-temperature plasma gas, which is then used to melt and atomize the metal powder. The molten particles are then sprayed onto a substrate, where they solidify to form a coating.
- Can produce powders with a wide range of particle sizes and shapes
- Suitable for alloys with high melting points
- Can be used to produce coatings with specific properties
- Alto consumo de energía
- Potential for contamination from the plasma gas
Comparison of Manufacturing Processes
CuSn40 powder possesses a unique combination of properties that make it a valuable material in various industries. These characteristics include: Properties of CuSn40 Powder CuSn40 powder finds widespread applications in various industries due to its unique combination of properties. Here are some of the key areas where CuSn40 powder is utilized: Applications of CuSn40 Powder Despite its numerous advantages, the use of CuSn40 powder faces certain challenges, and ongoing research and development efforts are focused on addressing these issues and exploring new possibilities. Challenges and Future Developments CuSn40 powder, like any other metal powder, presents potential safety hazards if not handled properly. It is essential to follow appropriate safety measures to protect workers and the environment. Safety Considerations and Handling Here are five FAQs tailored for potential users of CuSn40 powder, focusing on their likely concerns and information needs: 1. What makes CuSn40 powder particularly suitable for high-performance bearing and wear applications? CuSn40 powder, with its high tin content (40%), offers exceptional wear resistance, excellent load-bearing capacity, and good fatigue strength. This makes it ideal for demanding bearing applications, bushings, wear plates, and other components subjected to high friction and heavy loads. 2. How does the high tin content in CuSn40 powder influence its properties compared to lower tin bronze powders? The high tin content in CuSn40 powder contributes to the formation of hard, wear-resistant intermetallic phases within the microstructure. This results in significantly improved wear resistance, higher load-bearing capacity, and better anti-seizing properties compared to bronze alloys with lower tin content. 3. What are the typical processing methods used for CuSn40 powder? CuSn40 powder is commonly processed using powder metallurgy techniques, including pressing and sintering. The powder is first compacted into the desired shape using a die and high pressure, followed by sintering at elevated temperatures in a controlled atmosphere to bond the particles and achieve the desired density and mechanical properties. 4. What are the key considerations for optimizing the sintering process of CuSn40 powder? Optimizing the sintering process is crucial for achieving the desired properties in CuSn40 components. Key considerations include sintering temperature, time, heating rate, and atmosphere control. Precise control over these parameters ensures proper densification, formation of desired microstructures, and optimal mechanical properties. 5. What kind of technical support does Xmetto offer to ensure successful implementation of CuSn40 powder? Xmetto provides comprehensive technical support, including detailed material specifications, processing guidelines, and expert advice on powder selection, sintering parameters, and troubleshooting. We are dedicated to assisting our customers in achieving optimal results with our CuSn40 powder in their specific applications.
Proceso
Tamaño de las partículas
Forma
Pureza
Consumo de energía
Atomización de gases
Fine to coarse
Esférica
Alta
Alta
Atomización del agua
Fino
Esférica
Medio
Medio
Aleación mecánica
Fino
Irregular
Medio
Bajo
Pulverización de plasma
Fine to coarse
Irregular
Medio
Alta
Characteristics and Advantages of CuSn40 Powder
High Strength and Hardness
Excelente resistencia a la corrosión
Buena conductividad eléctrica y térmica
Porosity and Surface Area
Other Unique Properties
Propiedad
Valor
Resistencia a la tracción
Alta
Dureza
Alta
Resistencia a la corrosión
Excelente
Conductividad eléctrica
Bien
Conductividad térmica
Bien
Porosidad
Variable
Área de superficie
Alta
Resistencia a la fatiga
Bien
Soldabilidad
Bien
Biocompatibilidad
May be suitable
Applications of CuSn40 Powder
Fabricación aditiva (impresión 3D)
Pulvimetalurgia
Friction Materials (Brakes and Clutches)
Contactos eléctricos
Catalytic Materials
Other Potential Applications
Aplicación
Beneficios
Fabricación aditiva
Complex geometries, customization
Pulvimetalurgia
Sintered parts with desired properties
Materiales de fricción
Alta resistencia, dureza y resistencia al desgaste
Contactos eléctricos
Conductive properties, reliability
Catalytic Materials
High surface area, catalytic activity
Gestión térmica
Heat dissipation
Corrosion Protection
Resistance to corrosion
Dispositivos biomédicos
Biocompatibility, mechanical properties
Challenges and Future Developments
Desafíos
Future Developments
Desafío
Future Development
Coste y disponibilidad
Improved manufacturing techniques, increased production
Consistency and Quality Control
Advanced quality control methods, standardized manufacturing processes
Recycling and Sustainability
Development of recycling technologies, sustainable sourcing
New Applications
Research into emerging fields
Propiedades mejoradas
Material modification, alloy optimization
Nano-sized CuSn40 Powder
Research and development of nanomaterials
Hybrid Materials
Exploration of composite materials
Safety Considerations and Handling
Toxicity and Health Hazards
Storage and Transportation
Safe Handling Practices
Peligro
Precauciones
Inhalación
Respiratory protection, ventilation
Skin Contact
Gloves, protective clothing
Eye Contact
Eye protection, immediate rinsing
Ingestión
Avoid ingestion, wash hands thoroughly
Almacenamiento
Dry, well-ventilated area, sealed containers
Transportation
Proper containers, labeled with hazard information
Manejo de
PPE, ventilation, hygiene, emergency procedures
CuSn40 Powder FAQs: Addressing Key Concerns for Potential Users
If you would like to know more about the wide range of Copper Based Powder, please click on the names in the table: