Atomización de polvo metálico es una técnica de reducción del tamaño de partículas utilizada para producir polvos metálicos finos con características optimizadas para aplicaciones industriales. Este proceso implica forzar el metal fundido a través de una boquilla para desintegrarlo en gotas uniformes que se solidifican rápidamente en partículas de polvo.
La atomización permite controlar la distribución del tamaño de las partículas de polvo, la morfología, la pureza y otras propiedades críticas para un alto rendimiento en la impresión 3D de metales, la fabricación de piezas de pulvimetalurgia, los procesos de recubrimiento metálico y más. Este artículo proporciona una descripción general completa de varios tipos de equipos de atomización, principios de funcionamiento, consideraciones de diseño, aplicaciones, ventajas y limitaciones.
Descripción general del proceso de atomización de polvo metálico
La atomización de polvo metálico convierte el metal líquido a granel en polvos esféricos finos con características controladas. Esto se logra rompiendo una corriente de metal fundido en finas gotas mediante el impacto de un chorro de gas o líquido. Las gotas se solidifican rápidamente formando partículas de polvo a medida que se enfrían.
Los pasos clave involucrados en este proceso son:
- Fusión de metales – La carga de metal en bruto se funde mediante horno de inducción, fusión por arco u otras técnicas. Los metales comunes atomizados incluyen aluminio, titanio, níquel, hierro, cobalto, cobre, etc.
- Suministro de metal fundido – El metal líquido se mantiene a temperatura óptima y se canaliza hacia la zona de atomización mediante artesa, crisoles o bombas.
- Atomización – La corriente de metal fundido se desintegra en gotas mediante la interacción con un gas o líquido a alta velocidad. Se utilizan varios métodos de atomización.
- Colección de polvo – El polvo metálico atomizado se enfría y se recoge para operaciones posteriores. Se pueden utilizar procesos de tamizado, separación magnética y recocido.
- Caracterización del polvo – Se analiza la distribución granulométrica, morfología, densidad, fluidez y microestructura del polvo.
El control adecuado de los parámetros del proceso, como la composición del metal, la temperatura, la velocidad del fluido atomizador y el diseño del atomizador, es fundamental para lograr las características deseadas del polvo.
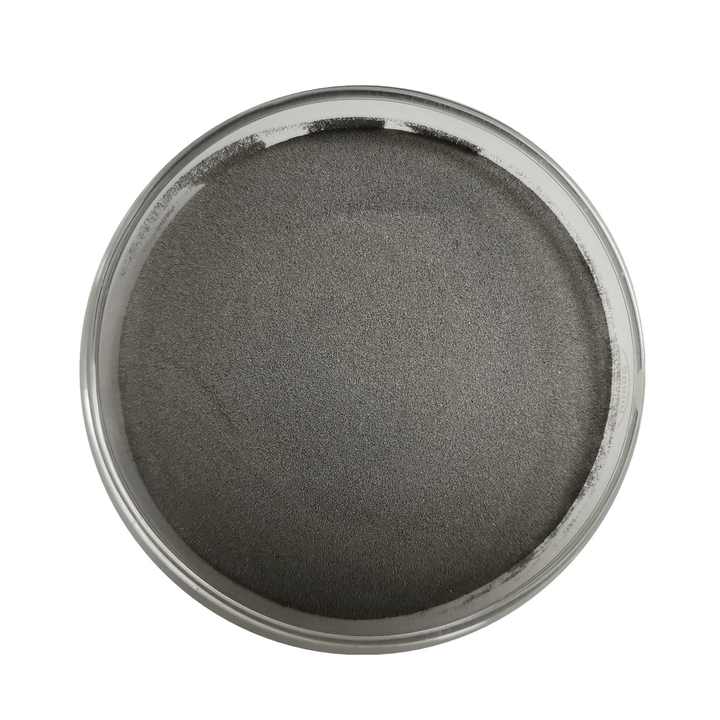
Tipos de equipos de atomización
Los sistemas de atomización se pueden clasificar según el medio utilizado para desintegrar el metal fundido en gotas:
Atomización de gases
En la atomización de gas, la energía cinética del gas a alta presión acelera y dispersa rápidamente la corriente de metal líquido en finas gotas. Según el diseño del suministro de gas, se puede clasificar en:
- Atomización de gas a presión – Utiliza boquillas estrechamente acopladas para suministrar aire comprimido o gas inerte lateralmente a la corriente de metal líquido.
- Atomización de gas con boquilla de dos fluidos – Las boquillas coaxiales introducen el gas de atomización de alta velocidad alrededor de un tubo de suministro metálico interno.
- Atomización de gas con múltiples boquillas – Utiliza una serie de boquillas convergentes-divergentes para enviar chorros de gas supersónicos a la corriente de fusión.
Los polvos atomizados con gas tienen un tamaño de partícula más bajo, una morfología más uniforme y una mayor pureza en comparación con los polvos atomizados con agua. Pero el proceso consume mucha energía y es caro.
Atomización del agua
En la atomización con agua, la corriente de metal fundido se desintegra mediante su impacto con chorros de agua a alta presión. Se forman gotas con una distribución de tamaño más amplia. La atomización con agua tiene menores costos de capital y operativos en comparación con la atomización con gas.
Según el diseño, la atomización del agua puede utilizar:
- Atomización de agua estrechamente acoplada – Los chorros de agua inciden directamente sobre el metal líquido que sale de la artesa.
- Atomización de agua en caída libre – La corriente de metal fundido que cae es interceptada por chorros de agua debajo de la artesa.
Los polvos atomizados con agua tienen formas de partículas más irregulares y una distribución más amplia, ideal para prensar y sinterizar. Pero el agua introduce contaminación.
Atomización centrífuga
En la atomización centrífuga, el metal fundido se vierte o bombea a un disco o copa que gira a alta velocidad. El metal forma una fina película en el perímetro que se desintegra en finas gotas debido a las fuerzas centrífugas.
Las ventajas incluyen diseño simple, bajo consumo de gas y fácil ampliación. Pero el rango de tamaño es relativamente mayor que el de la atomización con gas. Se utiliza para producir polvos esféricos a partir de metales de bajo punto de fusión como estaño, plomo, zinc, etc.
Atomización de gas ultrasónica
Combina la atomización del gas con un generador ultrasónico acoplado a la boquilla. Las vibraciones de alta frecuencia mejoran la desintegración y dispersión del metal en gotas más finas, logrando un polvo submicrónico.
Muy eficaz para generar morfologías de polvo nanocristalino y amorfo. Pero es caro y requiere mucho mantenimiento. Utilizado para aplicaciones especializadas.
Atomización por erosión por chispa
En esta técnica de atomización eléctrica, se aplica una descarga de chispa pulsada de alta corriente entre el metal fundido y la punta de un electrodo, creando plasma que desintegra el metal en un polvo esférico ultrafino.
Permite la producción de polvo metálico muy fino y altamente esférico. Pero baja tasa de producción y alto costo. Se utiliza principalmente para metales preciosos como oro, platino y paladio.
Componentes y diseño del atomizador
Los atomizadores constan de una variedad de componentes diseñados para derretir, verter, atomizar, enfriar y recolectar el polvo metálico de manera efectiva.
Sistema de fundición y vertido de metales
- Horno de inducción – Se utiliza más comúnmente para fundir metales como el acero. Permite un buen control de la temperatura y una baja contaminación del material fundido.
- Crisoles – Vasijas de cerámica refractaria utilizadas para contener carga metálica. Puede calentarse en un horno separado y verterse manualmente o incorporarse directamente al sistema de atomización.
- Tundish – Depósito intermedio de metal fundido que controla la velocidad de vertido en la sección de atomización.
- bajante – Dirige con precisión el flujo de metal fundido hacia la zona de atomización. Fabricado en metal refractario como el tungsteno para soportar altas temperaturas.
- Bombas – Se utiliza para controlar la entrega de metal fundido alimentado a presión en ciertas configuraciones de atomizador.
Sección de atomización
- Boquilla atomizadora – Boquillas especializadas resistentes a alta presión y temperatura que se utilizan para crear chorros de gas o agua para atomización.
- Conjuntos de boquillas – Múltiples boquillas especializadas ubicadas estratégicamente para optimizar la formación de gotas.
- Componentes giratorios – Los discos y copas utilizados en la atomización centrífuga giran a velocidades muy altas: de 10.000 a 50.000 RPM impulsados por un motor eléctrico.
- Generador ultrasónico – Convierte la señal eléctrica en vibraciones mecánicas de alta frecuencia en la región de la boquilla. Utilizado en atomización ultrasónica.
- Fuente de alimentación – Proporciona alta corriente para generar un arco eléctrico para la atomización por erosión por chispa.
Sistema de manipulación de polvo
- Separadores de ciclones – Separe el polvo fino del gas de proceso o de los flujos de agua mediante fuerzas centrífugas.
- Filtros de bolsa – Recoger polvo muy fino no separado en ciclones. Necesita reemplazo frecuente.
- Clasificadores de pantalla – Clasificación granulométrica del polvo en diferentes fracciones mediante tamices de malla.
- Separadores magnéticos – Elimine cualquier contaminante metálico atrapado en el polvo.
- Transportadores – Transporta polvo entre equipos. Se utilizan transportadores de tornillo, de correa y vibratorios.
- Tolvas – Almacena polvo para su posterior procesamiento o envasado.
- Limpieza por aspiración – Elimina el polvo derramado de equipos y superficies. Crítico para polvos metálicos reactivos.
Instrumentación y controles
- Sensores de temperatura – Es fundamental para monitorear y controlar la temperatura del horno/fundido y de la boquilla para una atomización óptima.
- Sensores de presión – Controle la presión del gas y del agua en las boquillas para mantener una atomización adecuada.
- Medidores de flujo – Medir y controlar los caudales de fluido de atomización y masa fundida.
- Tacómetros – Monitorea la velocidad de rotación de los discos de atomización centrífuga.
- Sensores de nivel – Mantener niveles óptimos de fusión en recipientes clave. Evita el desbordamiento.
- Parada de emergencia – Requerido para el apagado rápido y seguro de la maquinaria en caso de cualquier problema.
- Sistema de control – El control informático automatizado optimiza la coordinación de los parámetros y mejora la repetibilidad.
Parámetros del proceso de atomización de polvo metálico
La selección adecuada de los parámetros del proceso es clave para lograr polvos con las características deseadas. La siguiente tabla resume las variables clave y su influencia en las propiedades del polvo:
Parámetro | Efecto sobre las propiedades del polvo |
---|---|
Temperatura del metal fundido | Una temperatura más alta reduce la viscosidad y mejora la atomización. Pero puede aumentar la oxidación y la pérdida por evaporación. |
Presión del gas atomizador | Una presión de gas más alta mejora la distribución del tamaño de las partículas y reduce el tamaño promedio. Pero aumenta el consumo de gas. |
Tasa de flujo de gas atomizador | Un mayor caudal mejora la reducción del tamaño de las partículas. Pero aumenta el uso de gas. |
Velocidad del fluido atomizador | Una mayor velocidad mejora la reducción del tamaño de las partículas. Depende del diseño de la boquilla. |
Diseño de boquilla | Las boquillas especializadas crean gotas y polvo más finos. |
Tasa de vertido de fusión | Las tasas de vertido más altas aumentan el rendimiento para la operación continua pero pueden reducir el tamaño de las partículas. |
Derretir sobrecalentamiento | Aumenta a medida que la temperatura de vertido aumenta por encima del punto de fusión. Mejora la fluidez. |
Filtración por fusión | Elimina inclusiones y contaminantes. Mejora la pureza del polvo. |
Distancia de atomización | Una distancia de caída libre más larga permite más tiempo para la formación de gotas. Reduce la formación de satélites. |
Composición del derretimiento | Los elementos de aleación pueden cambiar la viscosidad y la tensión superficial, afectando el comportamiento de atomización y las características del polvo. |
Caracterización del polvo metálico atomizado.
Las propiedades y la calidad del polvo atomizado determinan el rendimiento en aplicaciones posteriores. Las características clave evaluadas son:
Distribución del tamaño de las partículas
La distribución de partículas de polvo en fracciones de diferentes tamaños, comúnmente representada como percentiles D10, D50 y D90. La atomización con gas puede alcanzar menos de 20 micrones, mientras que la atomización con agua produce un polvo más grueso.
Forma y morfología de las partículas
El polvo atomizado con gas tiene partículas muy esféricas, mientras que el polvo atomizado con agua es más irregular. Las partículas de satélite indican una falta de atomización óptima. El polvo redondeado tiene mejor flujo y densidad de empaquetamiento.
Composición química
La composición elemental y de fases de los ensayos. Determina el grado de aleación. La atomización del gas produce una alta pureza, mientras que el agua puede contaminar metales reactivos como el titanio y el aluminio.
Densidad aparente y de grifo
Indicador de eficiencia de envasado de polvo. Una mayor densidad mejora las propiedades del producto en prensado y sinterización. Pero puede afectar el flujo de polvo. Los valores suelen ser 40-65% de densidad del material.
Características de flujo
Importante para el manejo y procesamiento posterior. Influenciado por factores como la forma de las partículas, la distribución del tamaño y la estructura de la superficie. Mejorado mediante recocido, tratamiento superficial.
Microestructura
Estructura interna del polvo revelada por microscopía. El polvo atomizado con gas tiene granos finos y defectos debido a una solidificación rápida, mientras que el polvo atomizado con agua es más grueso. Determina el comportamiento de sinterización.
Aplicaciones de la atomización de polvo metálico
Los polvos metálicos atomizados encuentran una amplia gama de usos en la fabricación avanzada, mejorando la calidad y el rendimiento del producto en comparación con el procesamiento de metales convencional:
Fabricación aditiva
- Impresión 3D: los polvos esféricos atomizados con distribución de tamaño controlada son ideales para técnicas de fusión en lecho de polvo. Se utilizan comúnmente superaleaciones de aluminio, titanio y níquel.
- Moldeo por inyección de metal: los polvos más finos de acero inoxidable, titanio y aluminio mejoran el proceso de sinterización y la densidad de los componentes.
Pulvimetalurgia
- Prensa y sinterización: polvo ferroso atomizado con agua irregular y más grueso que se utiliza para una alta producción de piezas P/M con buenas propiedades mecánicas.
- Imanes blandos y duros: los polvos finos cristalinos de NdFeB y SmCo producen imanes unidos y prensados en caliente de alto rendimiento.
- Materiales de fricción: el polvo de cobre atomizado con agua mejora el rendimiento de las pastillas de freno y los forros del embrague.
Recubrimientos superficiales
- Pulverización térmica: polvo esférico de distribución de tamaño controlado, importante para recubrimientos uniformes y densos mediante plasma o pulverización HVOF. WC-Co, polvo de aleación de níquel utilizado.
- Deposición de vapor: materia prima en polvo de superaleación ultrafina utilizada en la deposición física de vapor por haz de electrones para recubrimientos de turbinas con protección mejorada.
Otros
- Moldeo por inyección de metal: las materias primas en polvo fino de acero inoxidable, titanio y aluminio pueden producir componentes pequeños y complejos.
- Pastas para soldadura fuerte: aleaciones de plata, oro y cobre atomizadas que se utilizan en la fabricación de uniones para soldadura fuerte a alta temperatura.
- Erosión por chispa: el polvo esférico ultrafino utilizado como medio dieléctrico mejora la precisión y la velocidad del mecanizado por electroerosión.
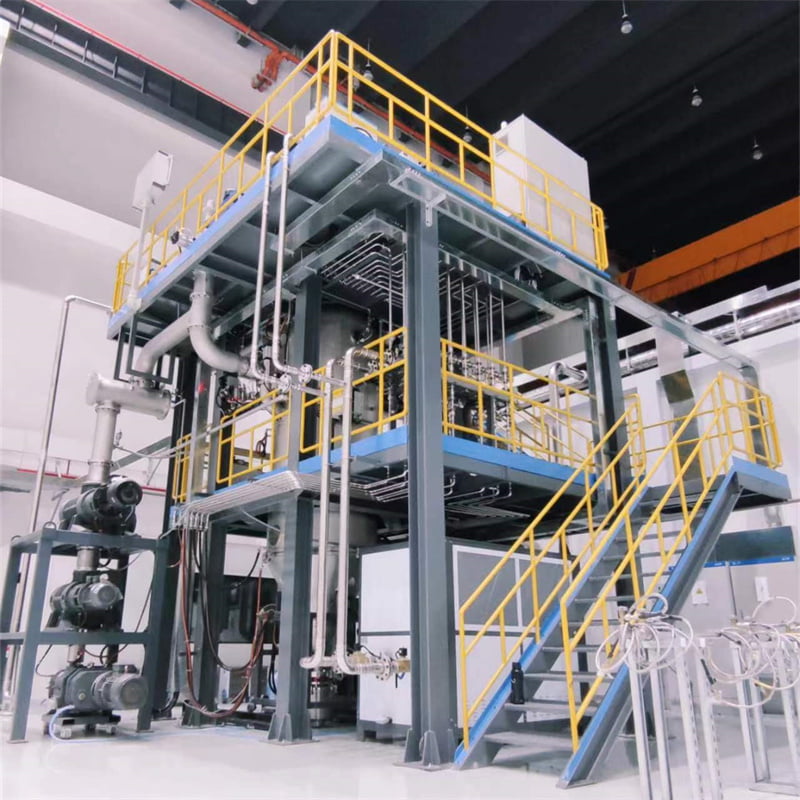
Ventajas de la atomización de polvo metálico
En comparación con las rutas convencionales de procesamiento de metales, los beneficios clave del uso de polvos atomizados incluyen:
- Propiedades mecánicas mejoradas – La microestructura fina y homogénea de la rápida solidificación aumenta el límite elástico, la vida a la fatiga y la ductilidad.
- Control dimensional preciso – El polvo esférico y consistente permite una fabricación de forma neta precisa y de alta densidad. Reduce el mecanizado.
- Mayor productividad – Los componentes se pueden producir en masa mediante el procesamiento de polvo metálico más rápido que los métodos sustractivos.
- Mayor libertad de diseño – Se pueden fabricar geometrías complejas que son imposibles mediante fundición o mecanizado.
- Minimiza el desperdicio – La capacidad de forma casi neta reduce la pérdida de chatarra en comparación con la metalurgia de lingotes. El polvo no utilizado se puede reciclar.
- Menor consumo de energía – El proceso en polvo requiere temperatura y energía más bajas que la producción a partir de metal a granel.
- Aleaciones personalizadas – Se pueden atomizar composiciones especializadas que son difíciles de producir mediante lingotes.
- Alta pureza – Los elementos reactivos como el titanio se pueden atomizar con menor contaminación que las prácticas convencionales.
Limitaciones de la atomización de polvo metálico
- Se requiere una alta inversión de capital para equipos de atomización y sistemas de manipulación de polvo en comparación con el procesamiento de metales a granel.
- Se necesitan procesos posteriores adicionales como compactación, sinterización, etc. para fabricar productos a partir de polvos. La ruta de producción general es compleja.
- Lograr polvo ultrafino a nanoescala puede ser un desafío y costoso con rendimientos más bajos.
- Potencial de contaminación al utilizar la atomización con agua, especialmente para metales reactivos.
- El polvo puede absorber oxígeno y humedad, lo que requiere almacenamiento y manipulación protectores.
- Existen problemas de seguridad relacionados con explosiones de polvo, riesgos de incendio y toxicidad de determinadas composiciones y morfologías de polvo.
- Variabilidad en las propiedades de los componentes finales en comparación con los productos forjados. Los defectos relacionados con el polvo pueden manifestarse después de la consolidación.
- El reciclaje y la reutilización del polvo metálico son limitados en comparación con las formas metálicas a granel. El material se desecha después de 1-2 ciclos de reutilización.
- La falta de estándares industriales para polvos metálicos novedosos en cuanto a características, metodología de prueba, control de calidad y certificación crea barreras para su adopción.
Selección de un sistema de atomización de polvo metálico
Elegir el equipo de atomización adecuado para una aplicación depende de factores como:
Volumen de producción
- Baja producción: atomizadores a escala piloto y de laboratorio. Sistemas de atomización centrífugos o de gas a presión.
- Producción media: atomizadores continuos con capacidad de producción de polvo de hasta 3 toneladas/hora.
- Alta producción: sistemas personalizados a gran escala con capacidad superior a 10 toneladas/hora.
Material en polvo
- Los metales no reactivos como el acero y las aleaciones de níquel pueden utilizar la atomización con agua.
- Las aleaciones sensibles al agua como el aluminio y el titanio necesitan atomización con gas inerte.
- Los metales refractarios como el tungsteno requieren protección y medios atomizadores especializados.
Propiedades del polvo
- Atomización con gas para polvo más fino por debajo de 30 micras con morfología esférica.
- Atomización con agua para obtener polvo más grueso e irregular para prensar.
- Atomización especializada para polvo metálico nanocristalino o amorfo.
Aplicación del producto
- La fabricación aditiva utiliza polvo muy fino y de distribución controlada de partículas procedente de la atomización de gas.
- El moldeo por inyección de polvo requiere un polvo fino y esférico con buen flujo.
- Los recubrimientos por pulverización térmica necesitan un polvo denso y esférico que se acumule bien.
Costes de capital y explotación
- La atomización de agua tiene un menor costo de equipo y de operación, pero puede comprometer la calidad del polvo.
- La atomización de gas tiene un costo de capital 10 veces mayor pero produce un polvo superior. Los costos operativos también son más altos.
- La atomización centrífuga es económica pero tiene limitaciones de tamaño y forma.
Integración de Planta
- Requiere infraestructura suficiente para la preparación de la masa fundida, manipulación, almacenamiento y transporte de polvo.
- Sistemas de protección para metales reactivos como atmósfera de gas inerte.
- Los controles automatizados y el monitoreo de datos mejoran la estabilidad del proceso.
Principales fabricantes de atomizadores de polvo metálico
Varias empresas ofrecen sistemas y componentes de atomización de polvo metálico estandarizados y diseñados a medida:
Sistemas de atomización de gases
- Praxair: líder del mercado en equipos de atomización de gas a alta presión. Ofrece sistemas de laboratorio, piloto y escala de producción.
- AP&C: se especializa en atomizadores de gas con boquillas de acoplamiento cerrado para metales reactivos y refractarios. Se utiliza ampliamente para polvos de titanio y aluminio.
- ALD Vacuum Technologies: diseña atomizadores de gas con múltiples boquillas para una producción media a alta. Propiedad de Oerlikon Metco.
Atomización del agua
- Gasbarre: ofrece atomización de agua en caída libre y monobloque para volúmenes medianos a altos.
- Sheffield Atomising Systems: especializados en tecnología de atomización de agua en caída libre desde hace más de 50 años.
Atomización centrífuga
- ABB: importante proveedor de equipos a nivel mundial. Ofrece sistemas de atomización centrífuga a escala de laboratorio a producción completa.
- Ferrum AG: proveedor líder de atomizadores centrífugos horizontales y verticales con sede en Suiza.
Atomización ultrasónica
- Tekna: ofrece sistemas atomizadores de gas ultrasónicos basados en su tecnología patentada de guía de inducción de doble hilo acoplado.
- Ultramet: proporciona equipos especializados de atomización ultrasónica con tecnología de licuado de alta temperatura
Atomización por erosión por chispa
- PyroGenesis: ofrece el sistema de atomización por plasma (PAS) para producir polvos metálicos esféricos ultrafinos.
- Plasma Innovations: suministra los sistemas de atomización de erosión por chispa del proceso de electrodo giratorio (REP).
Análisis de costos de atomizadores de polvo metálico
El costo del atomizador depende de la escala, la tasa de producción, el nivel de automatización y el material en polvo que se procesa. Estimaciones típicas de costos de capital:
Atomizador de gas de gran producción | Construcción personalizada | 1000 | 10 millones |
---|---|---|---|
Atomizador de agua de pequeña producción | Sistema de remolque/contenedor | 100 | 750,000 |
Atomizador de agua de producción media | Sistema de refugio | 500 | 2 millones |
Atomizador de agua de gran producción | Construcción personalizada | 2000 | 5 millones |
Atomizador centrífugo piloto | Montado sobre patines | 50 | 400,000 |
Atomizador centrífugo mediano | Sistema de refugio | 500 | 1.5 millones |
Atomizador ultrasónico de laboratorio | Mesa de trabajo | 5 | 250,000 |
Atomizador ultrasónico piloto | Montado sobre patines | 20 | 1 millón |
Atomizador de erosión por chispa | Sistema de contenedores | 10 | 2 millones |
Costos de operacion
- Los principales costos son energía, mano de obra, mantenimiento y uso de gas inerte.
- El consumo de energía de atomización de gas es de ~500-800 kWh por tonelada de polvo. Consumo de gas 5-10 m3 por kg de polvo.
- El uso de energía de atomización de agua se reduce a ~200-400 kWh por tonelada de polvo. Pero mayor mano de obra y mantenimiento.
- Consumo de energía de atomización centrífuga ~300-500 kWh por tonelada de polvo. Menor uso de gas inerte.
- Las piezas consumibles como boquillas y bolsas de filtro requieren un reemplazo frecuente.
Oportunidades de reducción de costos
- El aumento de la escala de producción y la producción de polvo reduce el costo de capital por kg de polvo.
- Un mayor grado de automatización y seguimiento mejora la productividad laboral.
- El reciclaje y la reutilización de gases de proceso, agua y calor residual reducen los gastos operativos.
- Los programas de mantenimiento preventivo minimizan el tiempo de inactividad y los costos de mantenimiento.
- El suministro local de energía, gases, agua y servicios auxiliares reduce los gastos logísticos.
- La compra de sistemas de atomización reconstruidos/usados reduce el desembolso de capital para los pequeños productores.
Equipos de atomización de polvo metálico: preguntas frecuentes
P: ¿Cuál es el rango de tamaño de partícula típico que se logra en la atomización de gas?
R: La atomización de gas puede producir polvos con un tamaño de partícula desde 1 micrón hasta más de 100 micras. Los valores típicos de D50 son de 10 a 45 micrones para la mayoría de las aleaciones. Es posible obtener polvos más finos de menos de 10 micrones con boquillas optimizadas y altas velocidades de gas.
P: ¿Cuánto puede producir anualmente un pequeño sistema atomizador de gas?
R: Un atomizador de gas a escala piloto con una producción de 10 kg/h y que funcione 5000 horas al año puede producir ~50 000 kg de polvo al año. Un sistema de producción pequeño con una capacidad de 50 kg/h puede producir ~250 000 kg al año en plena producción.
P: ¿Qué tipos de metales se pueden atomizar hasta convertirlos en polvo?
R: La mayoría de los sistemas de aleaciones comerciales han sido atomizados, incluidos acero inoxidable, acero para herramientas, aleaciones de níquel, aleaciones de titanio, aleaciones de aluminio, superaleaciones, aleaciones de cobalto, etc. Los metales refractarios como el tungsteno y el molibdeno son desafiantes y requieren sistemas de atomización especializados.
P: ¿Cuál es el mejor método de atomización para metales reactivos como el titanio?
R: Se prefiere la atomización de gas con un gas inerte como argón o nitrógeno para metales reactivos como titanio y aluminio. Esto evita la oxidación y la contaminación en comparación con la atomización del agua.
P: ¿Qué tamaño de partícula se puede lograr con la atomización ultrasónica?
R: Los atomizadores de gas ultrasónicos pueden generar polvo metálico submicrónico y nanométrico con un tamaño promedio inferior a 100 nanómetros cuando están optimizados. Pero la tasa de producción de polvo es baja.
P: ¿Se puede reciclar el polvo metálico después de su uso en la fabricación aditiva?
R: Sí, el polvo no utilizado se puede reutilizar en procesos de fabricación aditiva. Pero el polvo sólo se puede reciclar 1 o 2 veces antes de que sus propiedades se degraden. Luego es necesario volver a atomizar el polvo para continuar reutilizándolo.
P: ¿Cuál es la mejor manera de manipular el polvo reactivo fino?
R: Usar cajas de guantes inertes, sellar contenedores de polvo, evitar la exposición al aire/humedad. Algunos materiales reactivos pueden requerir tratamiento superficial. El polvo de aluminio atomizado con agua suele estar recubierto para evitar la oxidación.
P: ¿Por qué es importante el gas inerte de alta pureza para la atomización del gas?
R: La alta pureza minimiza la contaminación. La humedad y el oxígeno pueden oxidar las aleaciones reactivas durante la atomización. Los gases atrapados pueden quedar atrapados en el polvo, creando defectos en las propiedades de la pieza final.
P: ¿Qué tan fácil es dar servicio y reparar un atomizador de gas?
R: El mantenimiento de rutina es sencillo. Pero las reparaciones importantes, como el reemplazo de las boquillas, pueden llevar días y requieren personal con capacitación especializada. Se deben conservar conjuntos de boquillas adicionales como repuestos para un cambio rápido.
P: ¿Qué problemas de seguridad existen con la producción de polvo metálico?
R: La manipulación de polvo fino siempre presenta riesgo de explosión de polvo. Otras preocupaciones son los peligros del gas presurizado, la electricidad de alto voltaje, las temperaturas elevadas y la manipulación de metales fundidos que requieren equipo de protección y capacitación.