Properties and Characteristics of FeCoNiCrMo-1 Powder
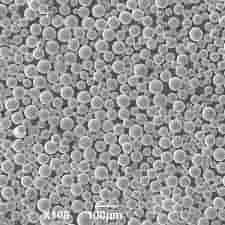
FeCoNiCrMo-1 powder, a high-entropy alloy (HEA), exhibits a unique combination of properties that make it a promising material for various applications. Its composition, consisting of iron, cobalt, nickel, chromium, and molybdenum, contributes to its exceptional characteristics.
Chemical Composition and Significance
Élément | Poids Pourcentage |
---|---|
Fer (Fe) | 20-25 |
Cobalt (Co) | 20-25 |
Nickel (Ni) | 15-20 |
Chrome (Cr) | 15-20 |
Molybdène (Mo) | 5-10 |
Propriétés physiques
- FeCoNiCrMo-1 powder typically has a density in the range of 7.8-8.2 g/cm³.
- The particle size distribution can vary depending on the manufacturing process, but it is generally in the range of a few micrometers to several tens of micrometers.
- Sintered FeCoNiCrMo-1 parts may have a porosity of 1-5%, depending on the sintering conditions.
Propriétés mécaniques
- FeCoNiCrMo-1 powder exhibits high hardness, often exceeding 400 Vickers Hardness Units (HV). This high hardness is attributed to the solid solution strengthening effect of the alloying elements.
- The tensile strength of FeCoNiCrMo-1 powder is typically in the range of 1000-1200 MPa. It offers excellent mechanical strength and resistance to deformation.
- While FeCoNiCrMo-1 powder is relatively hard, it can still exhibit some ductility, especially at elevated temperatures.
- The alloy’s high hardness and strength contribute to its excellent fatigue resistance, making it suitable for applications subjected to cyclic loading.
Propriétés magnétiques
- FeCoNiCrMo-1 powder exhibits a moderate saturation magnetization, typically in the range of 80-100 emu/g.
- The coercivity of the alloy is relatively low, which makes it suitable for applications requiring soft magnetic materials.
Corrosion and Oxidation Resistance
- The alloy’s composition, particularly the presence of chromium, provides good corrosion resistance in various environments, including acidic and alkaline conditions.
- FeCoNiCrMo-1 powder demonstrates excellent oxidation resistance at elevated temperatures, making it suitable for high-temperature applications.
Autres propriétés
- The alloy maintains its mechanical properties at elevated temperatures, making it suitable for applications in harsh environments.
- FeCoNiCrMo-1 powder has shown promising radiation resistance, making it a potential candidate for nuclear applications.
The unique combination of properties exhibited by FeCoNiCrMo-1 powder makes it a versatile material with potential applications in various industries, including aerospace, energy, automotive, and medical.
Manufacturing Processes for FeCoNiCrMo-1 Powder
The production of FeCoNiCrMo-1 powder involves various manufacturing processes, each with its own advantages and limitations. The choice of process depends on factors such as desired particle size, purity, and cost.
Powder Metallurgy Techniques
- This is a common method for producing FeCoNiCrMo-1 powder. The alloy is melted and then atomized into small droplets by a high-velocity gas or liquid. The droplets solidify quickly to form powder particles.
- In this process, elemental powders of iron, cobalt, nickel, chromium, and molybdenum are mixed and then subjected to intense mechanical deformation. This process can result in the formation of a homogeneous alloy powder with a fine particle size.
Frittage
- The powder is compacted into a shape and then heated in a furnace to bond the particles together. This process is often used to produce bulk parts from FeCoNiCrMo-1 powder.
- The powder is compacted in a sealed container and then subjected to high pressure and temperature. This process can result in a denser and more uniform microstructure.
Other Manufacturing Approaches
- A laser beam is used to melt a powder layer onto a substrate, creating a coating of FeCoNiCrMo-1 alloy.
- This process involves building up a part layer by layer using a powder bed and a laser or electron beam. Additive manufacturing can be used to produce complex shapes and geometries.
Manufacturing Process Comparison
FeCoNiCrMo-1 powder, with its unique combination of properties, has found applications in various industries. Its high hardness, strength, corrosion resistance, and magnetic properties make it a valuable material for a wide range of components. Despite its promising properties, the development and commercialization of FeCoNiCrMo-1 powder face several challenges. Addressing these challenges will be crucial for realizing the full potential of this material. Addressing the challenges associated with FeCoNiCrMo-1 powder will be essential for unlocking its full potential and realizing its benefits in various industries. Continued research and development efforts are expected to drive advancements in this promising material.
Processus
Avantages
Inconvénients
Atomisation
High purity powder, wide range of particle sizes
Expensive, energy-intensive
Alliage mécanique
Homogeneous alloy, fine particle size
Time-consuming, high energy consumption
Pressureless Sintering
Simple process, low cost
Potential for porosity, limited part complexity
Pressage isostatique à chaud
High density, uniform microstructure
High pressure and temperature requirements
Revêtement par laser
Precise control of coating thickness, rapid deposition
Limited part size, potential for defects
Fabrication additive
Complex part geometries, customization
High cost, slower production rate
Applications and Uses of FeCoNiCrMo-1 Powder
Aérospatiale et défense
Secteur de l'énergie
Dispositifs médicaux
Autres applications
Tableau des applications
L'industrie
Applications
Aérospatiale et défense
Turbine blades, armor plating, missile components
Secteur de l'énergie
Fuel cells, batteries, nuclear applications
Dispositifs médicaux
Implants, outils chirurgicaux
Autres applications
Electronics, automotive components, industrial tools
Challenges and Future Developments in FeCoNiCrMo-1 Powder
Current Challenges
Future Developments
Potential Benefits and Contributions
If you would like to know more about the wide range of High Entropy Alloy Powder, please click on the names in the table: