In the ever-evolving world of manufacturing, where efficiency and product quality reign supreme, staying ahead of the curve is paramount. Enter free-fall gas atomization, a transformative technology that has reshaped the landscape of metal powder production. This process, a carefully orchestrated interplay between molten metal and precisely controlled gas jets, unlocks a realm of possibilities for industries demanding the utmost control, versatility, and cost-effectiveness in their material sourcing.
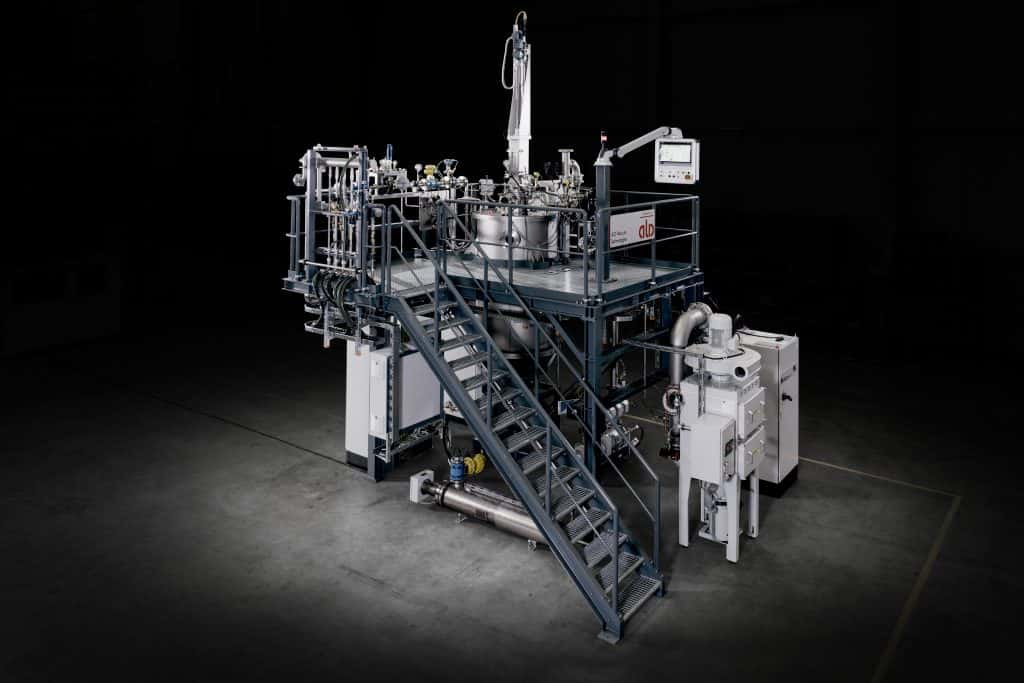
Free-Fall Atomization: Unraveling the Science Behind the Magic
Imagine a mesmerizing cascade of molten metal, glowing with intense heat, flowing gracefully downwards from a precisely controlled crucible. As this molten stream embarks on its descent, it encounters a strategically positioned barrage of high-velocity gas jets, their sole purpose to intercept and fragment the liquid metal into a myriad of minuscule droplets. This controlled collision, a testament to the power of engineering precision, lies at the heart of free-fall atomization – a process that transforms molten metal into a fine mist of rapidly solidifying particles.
Let’s break down the key players in this captivating transformation:
- The Molten Metal: The Heart of the Operation: The selection of the molten metal is paramount, dictated by the desired properties of the final powder and the specific requirements of the intended application. From ubiquitous aluminum and zinc to robust steel and exotic superalloys, free-fall atomization showcases its versatility by accommodating a vast spectrum of metallic materials.
- The Atomization Nozzle: The Precision Engineer: Acting as the gatekeeper of the process, the atomization nozzle is a marvel of engineering design. Its intricate geometry dictates the shape, velocity, and direction of the high-velocity gas jets, ultimately determining the size, distribution, and morphology of the resulting powder particles.
- The Atomization Chamber: Where Transformation Unfolds: This controlled environment serves as the stage for the intricate dance between molten metal and atomizing gas. Within the confines of the atomization chamber, the molten stream undergoes its dramatic transformation, fragmenting into a shower of droplets that rapidly cool and solidify as they descend, guided by carefully calibrated gas flows.
- The Collection System: Capturing the Essence: The final act in this orchestrated process involves capturing the solidified powder particles with utmost efficiency. Sophisticated collection systems, often employing a combination of cyclones and bag filters, work in unison to separate the precious metal powder from the atomization gas and any residual metal fines, ensuring minimal material loss and optimal product purity.
Why Free-Fall Atomization? Unveiling the Compelling Advantages
In the competitive arena of metal powder production, where efficiency and cost-effectiveness are paramount, free-fall atomization has secured its position as a leading technology, celebrated for its unique blend of advantages:
- Cost-Effectiveness: A Boon for Large-Scale Production: Free-fall atomizers, characterized by their relatively simple design and robust construction, offer an enticing cost advantage, particularly for high-volume powder production. This economic viability has propelled its widespread adoption in industries where optimizing production costs is paramount.
- Versatility in Powder Size Control: Tailoring Properties with Precision: One of the most compelling advantages of free-fall atomization lies in its remarkable ability to produce a wide spectrum of powder sizes, ranging from coarse particles ideal for thermal spray coatings to finer powders tailored for demanding powder metallurgy applications. This flexibility empowers manufacturers to fine-tune powder characteristics to meet the specific demands of their products and processes.
- Adaptability to Diverse Metals and Alloys: A Versatile Performer: Unlike some powder production methods confined to a limited selection of materials, free-fall atomization exhibits exceptional adaptability, readily processing a wide array of metals and alloys. From common ferrous and non-ferrous metals to specialized alloys with unique properties, this method rises to the challenge, making it a versatile choice for diverse industries.
- High Production Rates: Meeting the Demands of Industry: For industries where high-volume powder production is essential, free-fall atomization delivers, consistently achieving impressive production rates, often measured in tons per hour. This capability makes it a natural fit for large-scale manufacturing operations where meeting demanding production quotas is crucial.
Delving Deeper: Exploring the Diverse Applications of Free-Fall Atomized Powders
The versatility of free-fall atomization extends far beyond the production process itself, reflected in the wide array of applications that leverage the unique characteristics of the powders it produces:
- Powder Metallurgy (PM): Shaping the Future of Manufacturing: Powder metallurgy, a cornerstone of modern manufacturing, relies on the consolidation of metal powders into near-net-shape components, reducing material waste and enabling complex geometries. Free-fall atomized powders, with their controlled particle size distribution and excellent flowability, have become indispensable in PM, used to produce a wide range of components, including:
- Gears: From automotive transmissions to industrial machinery, gears produced from free-fall atomized powders offer high strength, wear resistance, and dimensional accuracy.
- Bearings: The controlled porosity and excellent surface finish achievable with free-fall atomized powders make them ideal for producing bearings with enhanced load-carrying capacity and wear properties.
- Filters: The controlled pore size distribution of filters produced from free-fall atomized powders allows for efficient filtration in various applications, ranging from automotive fuel systems to chemical processing.
- Structural Components: From aerospace brackets to medical implants, free-fall atomized powders enable the production of strong, lightweight, and complex-shaped structural components with tailored properties.
- Thermal Spray Coatings: Shielding Surfaces from the Extremes: Enhancing the surface properties of components is crucial in countless industries, and thermal spray coatings provide a versatile solution for improving wear resistance, corrosion resistance, and thermal barrier properties. Free-fall atomized powders, particularly those with coarser particle sizes, excel in thermal spray applications, finding use in:
- Aerospace: Protecting turbine blades from extreme temperatures and wear, ensuring the reliability of aircraft engines.
- Automotive: Enhancing the durability and performance of engine components, exhaust systems, and other critical parts.
- Oil and Gas: Shielding pipelines, valves, and other equipment from corrosion and wear in harsh environments.
- Power Generation: Protecting boiler tubes, turbine components, and other critical infrastructure from high temperatures and corrosive gases.
- Hardfacing Alloys: Armoring Surfaces Against Wear and Tear: When surfaces face the relentless onslaught of wear, abrasion, and impact, hardfacing alloys provide a formidable defense. Free-fall atomized powders serve as the building blocks of these alloys, which are applied to surfaces like:
- Cutting Tools: Extending the lifespan of drills, milling cutters, and other cutting tools by providing a hard, wear-resistant cutting edge.
- Mining Equipment: Protecting the teeth of excavator buckets, the surfaces of crusher jaws, and other mining equipment from abrasive wear, reducing downtime and maintenance costs.
- Agricultural Machinery: Enhancing the durability and wear resistance of plowshares, cultivator points, and other agricultural implements, ensuring optimal performance in demanding conditions.
- Welding and Brazing: Joining Metals with Precision: Joining metals is a fundamental aspect of countless manufacturing processes, and free-fall atomized powders play a crucial role in welding and brazing applications. These powders, often in the form of pre-alloyed mixtures, act as filler metals, providing the necessary properties to create strong, reliable joints in:
- Automotive Manufacturing: Joining body panels, chassis components, and exhaust systems with precision and strength.
- Aerospace Assembly: Creating critical joints in aircraft structures, engine components, and other aerospace applications.
- Pipeline Construction: Joining pipeline segments with strong, durable welds, ensuring the integrity of critical infrastructure.
Free-Fall Atomization: A Glimpse into a Future of Innovation
As industries continue their relentless pursuit of lighter, stronger, and more advanced materials, free-fall atomization remains at the forefront of innovation, constantly evolving to meet these ever-increasing demands. Here are some key trends shaping the future of this dynamic technology:
- Enhanced Process Control: Precision Through Technology: Advancements in sensor technologies, computational fluid dynamics modeling, and closed-loop control systems are empowering manufacturers to achieve unprecedented levels of precision and control over the free-fall atomization process. These innovations translate into powders with tighter particle size distributions, improved consistency, and enhanced material properties.
- New Material Development: Pushing the Boundaries of Possibility: The relentless exploration of new alloys and advanced materials, driven by the demand for components that can withstand extreme temperatures, resist wear and corrosion, and exhibit superior mechanical properties, is pushing the boundaries of free-fall atomization. This ongoing quest for innovation necessitates continuous advancements in nozzle design, process optimization, and a deep understanding of material science to accommodate the unique characteristics of these cutting-edge materials.
- Sustainability Focus: Minimizing the Environmental Footprint: As sustainability takes center stage in industrial practices, efforts to enhance the environmental friendliness of free-fall atomization are gaining momentum. This includes optimizing process parameters to reduce energy consumption, exploring the use of alternative atomization gases with lower environmental impact, and implementing strategies to minimize waste generation throughout the production cycle.
Choosing the Right Tool for the Job: A Comparative Perspective on Gas Atomization
While free-fall atomization stands as a versatile and widely adopted method for metal powder production, it’s crucial to recognize that it’s not a one-size-fits-all solution. Other gas atomization techniques, such as close-coupled atomization and confined atomization, offer distinct advantages for specific applications.
Here’s a table highlighting the key differences between these methods to guide your decision-making:
Atomization Type | Key Features | Ideal Applications |
---|---|---|
Free-Fall | Cost-effective, versatile, suitable for a wide range of powder sizes | Powder metallurgy, thermal spray coatings, hardfacing alloys |
Close-Coupled | Produces fine, uniform powders with high efficiency | Additive manufacturing, metal injection molding, high-performance alloys |
Confined | Offers exceptional control over particle characteristics, produces high-purity powders | Aerospace superalloys, medical implants, specialty powders |
FAQs: Addressing Your Free-Fall Atomization Queries
1. What are the limitations of free-fall atomization compared to other gas atomization methods?
While highly versatile, free-fall atomization might not be the ideal choice for applications demanding extremely fine powders with exceptionally narrow particle size distributions. In such cases, close-coupled or confined atomization, with their ability to exert finer control over particle formation, might be more suitable.
2. How does the choice of atomization gas influence the properties of the resulting powder?
The selection of the atomization gas is far from trivial, as it significantly influences the final properties of the powder. Inert gases, such as argon or helium, are often preferred to minimize oxidation during the atomization process, ensuring high-purity powders. In contrast, reactive gases can be intentionally introduced to achieve specific alloying effects or modify powder characteristics.
3. Can free-fall atomization be used to produce powders from high-melting-point metals?
While technically feasible, producing powders from high-melting-point metals using free-fall atomization presents unique challenges. The elevated temperatures involved necessitate higher energy inputs for melting and atomization, potentially leading to increased energy costs and nozzle wear. To address these challenges, advancements like plasma atomization, which utilizes a high-temperature plasma jet for melting and atomization, are being actively explored and refined.
4. How does free-fall atomization contribute to the overall cost-effectiveness of powder metallurgy?
Free-fall atomization plays a pivotal role in enhancing the cost-effectiveness of powder metallurgy processes through several key mechanisms. Its high material utilization rates minimize waste, reducing raw material costs. The ability to produce near-net-shape components reduces the need for extensive machining, leading to further cost savings. Additionally, its suitability for large-scale production allows for economies of scale, further contributing to its cost-effectiveness.
5. What are the key factors to consider when selecting a free-fall atomization system?
Selecting the optimal free-fall atomization system requires careful consideration of several key factors:
- Desired Production Capacity: Accurately estimating your required powder production volume, typically measured in kilograms per hour or tons per year, is crucial for selecting a system with the appropriate capacity.
- Required Powder Specifications: Clearly defining the desired powder characteristics, including particle size range, distribution, morphology, and purity, is essential for choosing a system capable of consistently meeting these specifications.
- Type of Metal Being Processed: The melting point, reactivity, and other characteristics of the metal or alloy being processed will influence the choice of atomization system components, such as the crucible material, heating method, and atomization gas.
- Budget Constraints: Establishing a realistic budget for the atomization system, considering both initial investment costs and ongoing operational expenses, is crucial for making an informed decision.
- Expertise of Potential Equipment Suppliers: Seeking out reputable equipment suppliers with a proven track record in free-fall atomization technology is essential for ensuring reliable equipment performance, access to technical support, and a smooth integration process.
If you’d like to learn more about this, check out this comprehensive guide:
Gas Atomization Equipment: The Key to Precise Engineering