Gas atomization is a specialized manufacturing process to produce fine metallic powders with precise composition and consistent particle sizes. The powders find application across automotive, aerospace, medical, and industrial sectors.
Overview of gas atomized powder
Table 1: Summary of the Gas Atomization Process
Parameter | Details |
---|---|
Raw Materials | Metals like titanium, aluminum, steels, nickel alloys in form of ingots, electrodes or wire |
Process Principle | Melting feedstock and breaking up molten metal stream into fine droplets using high pressure gas jets |
Atomizing Gases | Air, Nitrogen, Argon |
Solidification Rate | 10^3 – 10^5 °C/s |
Final Products | Spherical metal powders with controlled size ranging from 10 microns to 500 microns |
Controlled gas flow rates, precise atomization nozzles and specialized cooling designs enable the production of fine, spherical powders.
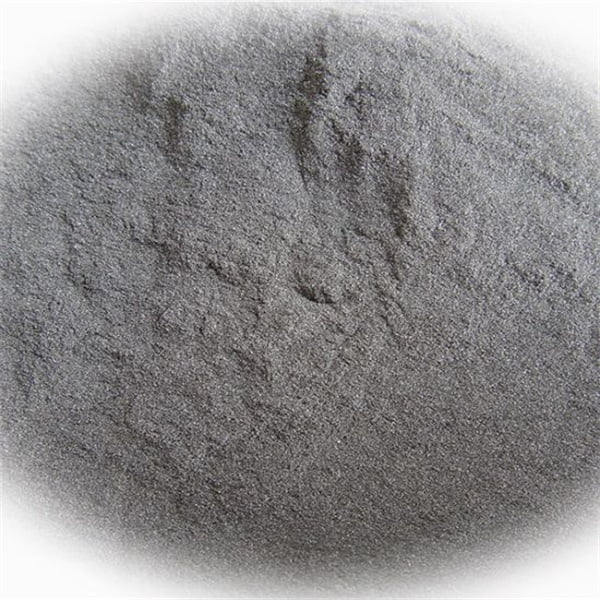
Applications of Gas Atomized Powders
Table 2: Major Application Areas of Gas Atomized Powder
Industry | Application Examples |
---|---|
Additive Manufacturing | 3D printing of aerospace and medical components |
Powder Injection Molding | Manufacture of small, complex metal parts with better mechanical properties |
Thermal Spray Coatings | Feedstock powder for wear and corrosion resistant coatings |
Metal Injection Molding | Small precision components like gears and cutting tool tips |
Brazing Pastes | Nickel and aluminum based brazing filler metal powders |
The consistent powder characteristics like particle size distribution, purity and morphology make gas atomized powders a preferred feedstock across powder metallurgy processes.
Advantages Over Alternatives
Table 3: Benefits of Gas Atomized Powder Over Other Types
Parameter | Benefit |
---|---|
Particle Shape | Highly spherical morphology gives excellent flowability |
Particle Size Control | Consistent microstructure which minimizes defects in finished components |
Composition Consistency | Precise control over alloying elements ensures reliable mechanical properties |
Cost Effectiveness | Higher yields compared to water atomization with easier powder recovery |
Product Customization | Flexibility to tailor powder composition and particle sizes as per application |
The combination of precision, consistency and flexibility makes gas atomization a versatile powder production technique at commercial scales.
Typical Specifications
Table 4: Typical Specification Range for Gas Atomized Powders
Parameter | Range |
---|---|
Materials | Titanium, Aluminum, Steels, Nickel, Copper alloys |
Particle Size | 10 to 500 μm |
Particle Size Distribution | Tight distribution with SG > 0.9 |
Oxygen Content | 100 – 1000 ppm range |
Nitrogen Content | < 100 ppm |
Shape | Highly spherical > 80% |
Apparent Density | Up to 65% of pure metal |
The properties can be tailored over a wide range as per intended usage across industries.
Pros vs Cons
Table 5: Advantages and Limitations of Gas Atomization
Pros | Cons |
---|---|
Consistent particle characteristics | Limitations on alloying additions like reactive elements |
Cost effective for higher volumes | Initial equipment capital cost relatively high |
Wide range of alloy families | Handling of fine pyrophoric powders requires care |
Scale-up to tonnage quantities feasible | Post-processing often required to remove satellites and fines |
Despite growing expertise globally, gas atomized powder still requires significant process development and qualification efforts by end-users to apply successfully for niche applications.
FAQs
Q: Does gas atomization allow single crystal powder production?
A: Very challenging – the rapid solidification rates create fine grained microstructures. Specialized variants like Electrode Induction-melting Gas Atomization (EIGA) can yield some fraction of single crystal particles.
Q: What is the typical nitrogen content range for gas atomized titanium powder?
A: With best practices, N2 levels of 100-500 ppm can be achieved for gas atomized titanium powder. This expands AM capability versus other variants with higher oxygen/nitrogen which negatively impacts mechanical performance.
Q: What is the key difference between gas and water atomized metal powders?
A: Gas atomization allows better particle shape and size control. Water atomization yields faster cooling rates but experiences more oxidation and satellite particle issues during powder production and recovery.