1. Introduction: A Deep Dive into the Dynamic World of Aluminum Alloy Powder
アルミニウム合金 powders, meticulously engineered from finely ground aluminum alloy particles, represent a cornerstone of modern material science. These powders, far from being mere metallic dust, are the building blocks of innovation across a multitude of industries, driving progress in aerospace, automotive, medical, and beyond. Their versatility stems from their unique combination of properties – lightweight yet strong, corrosion-resistant yet readily alloyed – making them ideal for a wide range of applications.
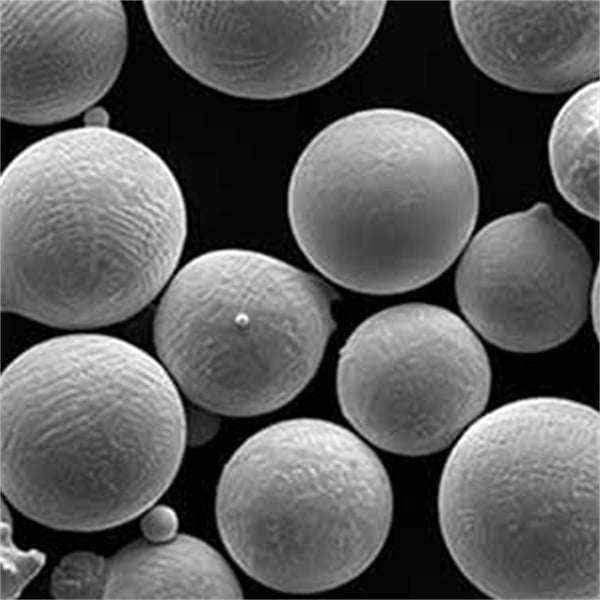
1.1 Defining and Classifying Aluminum Alloy Powder: A Spectrum of Possibilities
Aluminum alloy powders are not a monolithic entity; they exist in a spectrum of compositions, sizes, and shapes, each tailored to specific needs. Understanding these classifications is crucial for harnessing their full potential:
- 構成: This is the heart of what defines an aluminum alloy powder’s character. The specific blend of aluminum with other elements like copper, magnesium, silicon, or zinc dictates its strength, ductility, corrosion resistance, and even how it responds to heat treatments. For example, adding magnesium enhances strength-to-weight ratio, crucial for aerospace applications, while silicon improves castability, vital for intricate parts.
- 粒子径と分布: Imagine this as the powder’s “texture.” Ranging from nanometers to hundreds of micrometers, particle size influences how well the powder flows, how densely it can be packed, and ultimately, how the final product’s microstructure and properties will turn out. Finer powders are often favored for additive manufacturing, enabling intricate designs, while coarser ones might be suitable for powder metallurgy processes.
- 形態学: This refers to the shape of individual powder particles, whether spherical, irregular, dendritic, or flake-like. Morphology impacts how the particles pack together, their surface area, and how they interact with other materials during processing. Spherical powders, for instance, often exhibit better flowability, while irregular shapes can enhance green strength in compacted parts.
1.2 The Pivotal Role of Aluminum Alloy Powder in Material Science: Enabling Innovation
Aluminum alloy powders are not merely replacing existing materials; they are enabling entirely new possibilities, pushing the boundaries of what’s achievable in material science and engineering:
- Lightweight, High-Strength Components: In a world striving for energy efficiency, reducing weight without compromising strength is paramount. Aluminum alloy powders are key to this endeavor, enabling the creation of lightweight vehicles, aircraft, and structures that consume less fuel and reduce emissions.
- Complex Geometries with Enhanced Functionality: The advent of 3D printing has been a paradigm shift in manufacturing, and aluminum alloy powders are at the heart of this revolution. They enable the creation of intricately designed parts with complex internal channels, lattices, and geometries previously impossible to manufacture using traditional methods.
- Advanced Surface Coatings: Aluminum alloy powders aren’t limited to being the core material; they excel as protective and functional coatings as well. Through thermal spraying or cold spraying techniques, these powders can impart wear resistance to cutting tools, enhance corrosion resistance in marine environments, or even provide thermal barrier coatings in high-temperature applications.
1.3 Navigating This Comprehensive Guide: Your Roadmap to Aluminum Alloy Powder Expertise
This blog serves as your comprehensive guide to the world of aluminum alloy powders. We’ll delve into the intricacies of their production methods, explore their unique properties, uncover their diverse applications, and ultimately, provide you with the knowledge to navigate the exciting future that lies ahead for this versatile material.
2. From Raw Material to Engineered Powder: The Art and Science of Aluminum Alloy Powder Production
The journey from raw aluminum alloy to finely tuned powder is a fascinating blend of art and science, with each step carefully orchestrated to achieve the desired particle characteristics. This transformation involves breaking down the bulk material into fine particles while controlling their size, shape, and composition, ultimately influencing the final product’s properties.
2.1 Traditional Production Methods: The Foundation of Powder Metallurgy
- ガス霧化: This widely used method involves melting the aluminum alloy and then subjecting it to high-pressure gas jets, typically nitrogen or argon. These jets break the molten metal into fine droplets, which then solidify into powder particles as they cool. The process is versatile, cost-effective, and allows for good control over particle size distribution.
- Mechanical Alloying: Unlike atomization, which starts with molten metal, mechanical alloying is a solid-state process. It involves milling aluminum powder with other alloying elements in a high-energy ball mill. The repeated fracturing and welding of particles during milling lead to a highly uniform distribution of elements within the powder particles, a characteristic crucial for achieving specific mechanical properties.
2.2 Emerging Production Technologies: Pushing the Boundaries of Powder Characteristics
- 電解析出: This method leverages electrochemistry to produce aluminum alloy powder. An electrolytic cell is used, where aluminum ions are deposited onto a cathode, forming a powder with controlled particle size and morphology. This technique offers high purity and the potential for producing nanostructured powders with unique properties.
- Laser Melting and Rapid Solidification: This advanced technique utilizes a high-powered laser beam to melt a small area of the alloy. The molten pool then rapidly solidifies as the laser moves, creating ultrafine powders with unique microstructures and enhanced properties. This method allows for precise control over powder characteristics and is particularly suitable for producing high-performance alloys.
2.3 The Delicate Dance of Process Parameters and Powder Properties: A Symphony of Variables
The final properties of aluminum alloy powder are not solely determined by the chosen production method; they are intricately linked to a multitude of process parameters. These parameters act as levers, allowing engineers to fine-tune the powder characteristics to meet specific application requirements.
- ガス霧化: Parameters like gas pressure, flow rate, nozzle design, and the temperature of the molten metal all influence the cooling rate and solidification behavior of the droplets, ultimately impacting particle size distribution and morphology.
- Mechanical Alloying: Milling time, intensity, the type of milling media, and the atmosphere within the mill can significantly impact the degree of alloying, particle size reduction, and the potential for contamination.
- 電解析出: Factors such as current density, electrolyte composition, temperature, and the geometry of the electrodes influence the deposition rate, particle size, morphology, and purity of the produced powder.
- レーザー溶融: Laser power, scanning speed, spot size, and powder feed rate all play a crucial role in determining the melt pool dynamics, cooling rate, and ultimately, the microstructure and properties of the resulting powder.
Mastering the interplay of these parameters is crucial for producing aluminum alloy powders with consistent and predictable performance, paving the way for their successful implementation in demanding applications.
3. Unveiling the Unique Characteristics of Aluminum Alloy Powder: A Symphony of Strength, Lightness, and Versatility
Understanding the properties of aluminum alloy powder is akin to unlocking a treasure chest of possibilities. It’s not just about knowing the numbers; it’s about understanding how those numbers translate into real-world advantages, enabling engineers and designers to select the perfect material for their specific needs.
3.1 Physical Properties: Laying the Foundation for Lightweight Design and Beyond
プロパティ | 説明 |
---|---|
密度 | One of the most significant advantages of aluminum alloy powders is their low density. Significantly lighter than traditional ferrous alloys, they offer immense potential for weight reduction in vehicles, aircraft, and other structures, leading to improved fuel efficiency and reduced emissions. This property is particularly crucial in aerospace and automotive applications where every gram counts. |
融点 | The melting point of aluminum alloy powder is generally lower than that of the corresponding bulk alloy, making it suitable for processing techniques like sintering and additive manufacturing, which rely on controlled heating and melting. The specific melting point is influenced by the alloying elements present, allowing for tailoring to specific processing requirements. |
熱膨張 | Aluminum alloys, in general, have a relatively high coefficient of thermal expansion compared to some other metals. This property, while beneficial in certain applications, needs to be carefully considered during design, especially when the material will be exposed to significant temperature variations or joined with other materials with different expansion rates. |
電気伝導率 | While aluminum is an excellent conductor of electricity, the addition of alloying elements generally reduces its conductivity compared to pure aluminum. However, this property can be strategically controlled by selecting specific alloying elements and their concentrations. For instance, some aluminum alloys are designed to have good electrical conductivity while maintaining adequate strength for electrical applications. |
3.2 Mechanical Properties: The Backbone of Strength, Durability, and Reliability
- Strength and Ductility: The mechanical strength of aluminum alloy powder is not a fixed value; it’s a spectrum that can be finely tuned through alloy composition and processing methods. Adding elements like copper, magnesium, or zinc can significantly enhance the strength of the base aluminum, while heat treatments like age hardening can further boost both strength and ductility, allowing the material to withstand higher loads before deformation or fracture.
- Hardness and Wear Resistance: In applications where surfaces are subjected to constant friction or abrasion, hardness and wear resistance are paramount. Aluminum alloy powders, particularly those containing hard ceramic particles like silicon carbide or aluminum oxide, exhibit excellent wear resistance, making them suitable for applications such as cutting tools, engine components, and hydraulic systems.
- 疲労強度: Components subjected to cyclic loading, like those found in aircraft wings, engine parts, or turbine blades, need to withstand repeated stress cycles without failing. Aluminum alloy powders can be processed to achieve high fatigue strength, ensuring long-term reliability and safety in critical applications.
3.3 Chemical Properties: Resisting Corrosion, Oxidation, and the Test of Time
- 耐食性: Aluminum’s inherent corrosion resistance stems from the thin but tenacious oxide layer that forms on its surface when exposed to air. This oxide layer acts as a barrier, protecting the underlying metal from further oxidation. Alloying elements like magnesium and chromium can further enhance this resistance, making aluminum alloy powders suitable for use in harsh environments, from marine applications to chemical processing.
- Oxidation Behavior: At elevated temperatures, aluminum tends to oxidize, forming an oxide layer that can impact its properties. While this oxide layer can be protective in some instances, excessive oxidation can lead to degradation and loss of mechanical properties. Alloying elements and surface treatments can be employed to control oxidation behavior, extending the service life of components operating at high temperatures.
3.4 Characterization Techniques: Peering into the Microscopic World of Powder Metallurgy
- X-ray Diffraction (XRD): This technique utilizes the interaction of X-rays with the crystal lattice of the powder particles to provide valuable information about their internal structure. XRD can identify the phases present in the alloy, determine crystallite size, and even detect the presence of residual stresses within the powder particles.
- Scanning Electron Microscopy (SEM): SEM allows us to visualize the powder particles at high magnifications, revealing their morphology, size distribution, and surface features in intricate detail. This technique is invaluable for understanding how the powder’s physical characteristics relate to its processing behavior and final properties.
- Transmission Electron Microscopy (TEM): TEM takes us even deeper into the world of powder metallurgy, offering higher magnification and resolution than SEM. It allows for detailed analysis of the powder’s microstructure, revealing grain boundaries, defects, and even the arrangement of atoms within the particles. This level of analysis is crucial for understanding the relationship between processing, microstructure, and properties in advanced powder metallurgy applications.
4. Aluminum Alloy Powder in Action: Revolutionizing Industries from Aerospace to Energy
The unique properties of aluminum alloy powder, meticulously engineered through advanced production methods and characterized using sophisticated techniques, have unlocked a world of possibilities across a multitude of industries. Let’s explore how this versatile material is shaping the future of manufacturing and beyond.
4.1 Additive Manufacturing (3D Printing): Shaping the Future, Layer by Layer with Unprecedented Precision
- 選択的レーザー溶融(SLM): Imagine a laser beam tracing intricate patterns on a bed of aluminum alloy powder, selectively melting and fusing particles together, layer by layer. That’s the essence of SLM, a high-precision 3D printing technique that has revolutionized the way we design and manufacture complex components. SLM allows for the creation of parts with internal channels, lattices, and geometries previously impossible to achieve using traditional subtractive manufacturing methods.
- Direct Metal Laser Sintering (DMLS): Similar to SLM, DMLS also utilizes a laser beam as the heat source. However, instead of fully melting the powder, DMLS sinters the particles together at a temperature below their melting point. This process creates a solid part with slightly lower density and mechanical properties compared to SLM but offers advantages in terms of cost and processing speed.
- 電子ビーム溶解(EBM): EBM takes a different approach, utilizing a high-energy electron beam to melt the aluminum alloy powder. The electron beam, generated in a vacuum, offers advantages in terms of energy efficiency and the ability to process a wider range of materials, including those with high melting points. EBM is particularly well-suited for producing large-sized components with high density and good mechanical properties.
Advantages of Aluminum Alloy Powder in 3D Printing:
- デザインの自由と複雑さ: 3D printing with aluminum alloy powder breaks free from the constraints of traditional manufacturing, enabling the creation of complex geometries, intricate internal features, and customized designs tailored to specific applications.
- Lightweighting Opportunities: The inherent low density of aluminum alloys, combined with the ability to create lightweight designs with optimized geometries, makes 3D printing with aluminum alloy powder a game-changer for industries striving to reduce weight without compromising strength.
- Reduced Material Waste and Lead Times: Unlike subtractive manufacturing, where material is removed from a solid block, 3D printing is an additive process, building parts layer by layer. This significantly reduces material waste and allows for on-demand manufacturing, shortening lead times and enabling rapid prototyping.
- カスタマイズとオンデマンド製造: 3D printing empowers manufacturers with the ability to produce customized parts tailored to specific customer requirements. This on-demand manufacturing capability eliminates the need for large inventories, reduces storage costs, and allows for rapid design iterations and product development cycles.
Challenges in Additive Manufacturing with Aluminum Alloy Powder:
- Powder Quality Control and Consistency: The quality of the 3D printed part is directly linked to the quality and consistency of the aluminum alloy powder used. Ensuring uniform particle size distribution, morphology, and chemical composition is crucial for achieving reliable and repeatable results.
- 後処理の要件: 3D printed parts often require post-processing steps such as support removal, surface finishing, and heat treatments to achieve the desired dimensional accuracy, surface quality, and mechanical properties.
- コストを考慮する: While the cost of 3D printing has decreased significantly in recent years, it remains a major consideration, especially for large-scale production runs. The cost of aluminum alloy powder, equipment, and post-processing can be significant, and a thorough cost-benefit analysis is essential before adopting 3D printing for a specific application.
Applications of Aluminum Alloy Powder in 3D Printing:
- 航空宇宙 Lightweight components, fuel-efficient designs, complex geometries for aircraft interiors, engine parts, and structural components.
- 自動車: Prototyping, customized parts, lightweighting opportunities for engine components, chassis parts, and interior components.
- メディカルだ: Implants, prosthetics, customized surgical tools, dental restorations, and medical devices tailored to individual patient anatomy.
4.2 Powder Metallurgy: A Classic Approach with Renewed Relevance in a World of Advanced Materials
- Pressing and Sintering: This traditional powder metallurgy technique involves two main steps. First, the aluminum alloy powder is compacted into a desired shape using a die and a press, applying high pressure to form a “green” compact. This compact, while holding its shape, is still relatively fragile. It’s then subjected to a controlled heating process called sintering, where the temperature is raised below the melting point of the alloy. This causes the powder particles to bond together at their points of contact, increasing the compact’s strength and density.
- 熱間静水圧プレス(HIP): HIP takes sintering a step further by applying both high pressure and high temperature simultaneously. The green compact is placed in a sealed container and subjected to a high-pressure inert gas atmosphere while being heated to a temperature below its melting point. This process eliminates internal porosity, improves bonding between particles, and enhances the mechanical properties of the final product, making it suitable for demanding applications.
Advantages of Powder Metallurgy with Aluminum Alloy Powder:
- ニア・ネットシェイプ・マニュファクチャリング: Powder metallurgy allows for the production of parts that are close to their final shape, reducing the need for extensive machining and minimizing material waste. This is particularly advantageous for complex geometries and intricate designs.
- Uniform Microstructure and Properties: The controlled powder processing methods used in powder metallurgy result in a more uniform microstructure compared to traditional casting or forging techniques. This uniformity translates to more consistent and predictable mechanical properties throughout the part.
- Ability to Produce Complex Shapes: Powder metallurgy offers greater design freedom compared to some traditional manufacturing methods, enabling the production of complex shapes with intricate internal features that would be difficult or impossible to achieve otherwise.
Applications of Powder Metallurgy with Aluminum Alloy Powder:
- 自動車: Gears, bearings, connecting rods, sprockets, and other components requiring high strength, wear resistance, and precise dimensional tolerances.
- 航空宇宙 Structural components, turbine parts, landing gear components, and other parts requiring a balance of strength, lightweight, and reliability.
- Industrial Machinery: Cutting tools, wear-resistant parts, gears, bearings, and other components subjected to high loads, impact, or abrasion.
4.3 Surface Coatings: Shielding Against Wear, Corrosion, and the Ravages of Time
- 溶射: Imagine a stream of molten aluminum alloy particles propelled at high speed onto a surface, creating a protective coating that enhances its properties. That’s the essence of thermal spraying, a versatile coating technique that utilizes a high-temperature flame or plasma jet to melt the aluminum alloy powder and propel it towards the substrate. As the molten particles impact the surface, they flatten, solidify, and bond together, forming a dense and adherent coating.
- Cold Spraying: In contrast to thermal spraying, cold spraying doesn’t rely on melting the powder particles. Instead, solid aluminum alloy particles are accelerated to supersonic speeds using a high-pressure gas stream and directed towards the substrate. Upon impact, the kinetic energy of the particles causes them to deform plastically and bond with the substrate, forming a dense and adherent coating without significant heating.
Applications of Aluminum Alloy Powder Coatings:
- 腐食保護: Aluminum alloy coatings provide excellent corrosion resistance for a wide range of applications, from marine structures and offshore platforms to pipelines, storage tanks,and chemical processing equipment. The inherent corrosion resistance of aluminum, combined with the barrier properties of the coating, effectively protects the underlying substrate from harsh environments.
- 耐摩耗性: Aluminum alloy coatings, particularly those containing hard ceramic particles like silicon carbide or aluminum oxide, exhibit exceptional wear resistance, making them suitable for applications subjected to abrasion, erosion, or sliding wear. These coatings are commonly used in industries such as mining, power generation, and manufacturing to protect components like pumps, valves, and cutting tools.
- Thermal Barrier Coatings: In high-temperature applications, aluminum alloy coatings can act as thermal barriers, protecting the underlying substrate from excessive heat. These coatings reflect heat away from the surface, reducing thermal fatigue and extending the service life of components operating in extreme environments, such as gas turbine engines, furnaces, and exhaust systems.
4.4 Energy Applications: Powering a Sustainable Future with Lightweight and Efficient Solutions
- Fuel Cells: Aluminum alloy powders are playing an increasingly important role in the development of fuel cells, which offer a clean and efficient way to generate electricity. Aluminum can be used as a fuel source in certain types of fuel cells, and aluminum alloy powders are being explored as catalysts and components in fuel cell systems.
- バッテリー: The demand for high-performance batteries is skyrocketing, driven by the growth of electric vehicles, portable electronics, and renewable energy storage. Aluminum alloy powders are being investigated as anode materials in next-generation batteries, offering the potential for higher energy density and improved safety compared to conventional lithium-ion batteries.
- Solar Energy: Aluminum alloy powders are used in the production of solar cells, which convert sunlight into electricity. Aluminum pastes, made from finely ground aluminum powder, are used to create the electrical contacts on solar cells, enabling them to efficiently collect and conduct electricity.
5. Challenges and Opportunities: Navigating the Future Landscape of Aluminum Alloy Powder Technology
The future of aluminum alloy powder is brimming with possibilities, but it’s not without its challenges. Overcoming these hurdles will require continued innovation, collaboration between researchers, manufacturers, and end-users, and a commitment to pushing the boundaries of material science and engineering.
5.1 Addressing Key Challenges: Refining the Process, Enhancing Performance, and Ensuring Sustainability
- Powder Quality and Consistency: Achieving consistent and predictable performance from aluminum alloy powders hinges on maintaining stringent quality control throughout the production process. Variations in particle size distribution, morphology, and chemical composition can significantly impact the final product’s properties. Advanced characterization techniques, coupled with rigorous process monitoring and control, are essential for ensuring powder quality and consistency.
- コスト削減: While aluminum alloy powders offer numerous advantages, cost remains a barrier to wider adoption in some applications. Optimizing production processes, exploring alternative production methods, and developing cost-effective alloy compositions are crucial for making aluminum alloy powder technology more accessible across various industries.
- Environmental Sustainability: The production of aluminum, even in powder form, is an energy-intensive process. Minimizing the environmental impact of aluminum alloy powder production requires a multi-pronged approach, including increasing the use of recycled aluminum, optimizing production processes to reduce energy consumption and emissions, and developing closed-loop recycling systems for end-of-life products.
5.2 Seizing Emerging Opportunities: Pioneering New Frontiers in Material Science and Engineering
- Nanostructured Aluminum Alloys: Imagine aluminum alloy powders with grain sizes on the nanometer scale, exhibiting exceptional strength, enhanced ductility, and improved corrosion resistance. Nanostructured aluminum alloys, produced through advanced processing techniques, hold immense potential for applications requiring extreme performance, from aerospace components to high-performance cutting tools.
- 金属マトリックス複合材料: Aluminum alloy powders can serve as the matrix material in metal matrix composites (MMCs), where they are reinforced with ceramic particles, fibers, or other materials to enhance their properties. MMCs offer a unique combination of strength, stiffness, lightweight, and wear resistance, making them suitable for demanding applications in aerospace, automotive, and other industries.
- Biodegradable Aluminum Alloys: Researchers are exploring the development of biodegradable aluminum alloys for use in medical implants and devices. These alloys would gradually degrade and be absorbed by the body over time, eliminating the need for a second surgery for implant removal. Aluminum alloy powders, with their controlled composition and microstructure, offer a promising avenue for developing such biocompatible and biodegradable materials.
5.3 The Road Ahead: Collaboration, Innovation, and a Commitment to Sustainable Development
The journey towards unlocking the full potential of aluminum alloy powder technology is an ongoing endeavor, fueled by collaboration, innovation, and a shared commitment to sustainable development. As researchers continue to push the boundaries of material science and engineers develop innovative applications, aluminum alloy powders are poised to play an increasingly vital role in shaping a lighter, stronger, and more sustainable future.
