Stellite 3 Powder
はじめに
ステライト 3 powder is a high-performance material produced through specialized manufacturing techniques. The unique properties of this alloy, such as its exceptional hardness, wear resistance, and corrosion resistance, make it ideal for applications requiring exceptional durability and performance. This chapter will delve into the primary manufacturing processes used to produce Stellite 3 powder, highlighting their advantages and challenges.
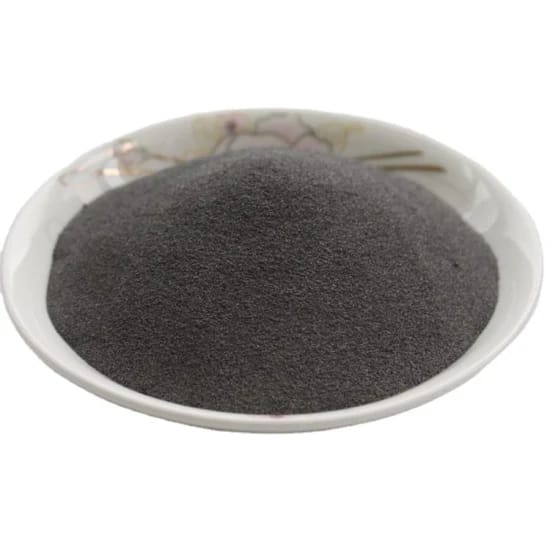
Powder Metallurgy Techniques
Powder metallurgy is the predominant method for producing Stellite 3 powder. This process involves creating a fine powder of the alloy and then compacting and sintering it to form the desired shape. The following are the most common powder metallurgy techniques used for Stellite 3:
- This is the most widely used method for producing Stellite 3 powder. In atomization, molten Stellite 3 is rapidly cooled by a high-velocity gas or liquid, breaking it down into tiny particles. The cooling rate can be controlled to influence the particle size and morphology.
- This technique involves spraying a plasma jet onto a substrate, melting the Stellite 3 powder particles and depositing them onto the surface. Plasma spraying is often used to create coatings or overlays of Stellite 3 on other materials.
粉末冶金の利点
- Powder metallurgy allows for precise control over the composition, microstructure, and properties of Stellite 3 powder.
- Complex shapes and intricate components can be produced through powder metallurgy techniques.
- This reduces the need for extensive machining, saving time and material.
- Powder metallurgy can produce materials with consistent properties throughout the entire component.
Quality Control and Testing
To ensure the quality and reliability of Stellite 3 powder, rigorous quality control measures are implemented throughout the manufacturing process. This includes:
- Testing to verify the chemical composition of the powder to meet specifications.
- Measuring the distribution of particle sizes to ensure optimal compaction and sintering.
- Analyzing the microstructure of the powder to assess its internal structure and properties.
- Evaluating the hardness, tensile strength, and other mechanical properties of the sintered components.
Comparison of Powder Metallurgy Techniques for Stellite 3
Powder metallurgy techniques are essential for the production of Stellite 3 powder, offering precise control, complex shape capabilities, and near-net-shape production. By understanding the manufacturing processes involved, engineers and manufacturers can optimize the production of Stellite 3 components for various applications. はじめに Stellite 3 powder is renowned for its exceptional properties, which make it a highly sought-after material in various industries. This chapter will delve into the key properties of Stellite 3 powder, including its mechanical characteristics, wear resistance, and corrosion resistance. 機械的特性 Stellite 3 powder exhibits impressive mechanical properties, making it suitable for demanding applications. Some of the key mechanical properties include: 耐摩耗性 One of the most significant advantages of Stellite 3 powder is its exceptional wear resistance. This is due to its hard, carbide-rich microstructure. Stellite 3 components can withstand abrasive and erosive wear, making them ideal for applications involving high-speed contact or the handling of abrasive materials. 耐食性 Stellite 3 powder is also highly resistant to corrosion, particularly in oxidizing environments. The chromium content in the alloy forms a protective oxide layer that acts as a barrier against corrosion. This makes Stellite 3 suitable for applications in corrosive environments, such as chemical processing and marine environments. Mechanical Properties of Stellite 3 Powder Stellite 3 powder is one of several Stellite alloys, each with unique properties. For example, Stellite 6 is known for its higher cobalt content and improved hot hardness, while Stellite 21 offers enhanced resistance to pitting corrosion. The choice of Stellite alloy depends on the specific requirements of the application. 結論 Stellite 3 powder is a high-performance material with exceptional properties. Its hardness, wear resistance, and corrosion resistance make it suitable for a wide range of demanding applications. By understanding the properties and performance characteristics of Stellite 3 powder, engineers and manufacturers can select the optimal material for their specific needs. はじめに Stellite 3 powder’s exceptional properties make it a versatile material with a wide range of applications across various industries. This chapter will explore some of the primary applications and industries that benefit from the use of Stellite 3 powder. 切削工具 Stellite 3 powder is widely used in the production of cutting tools, such as drills, milling cutters, and reamers. Its exceptional hardness and wear resistance ensure long tool life and high machining efficiency. Stellite 3 cutting tools are particularly suitable for machining hard and abrasive materials. 耐摩耗コンポーネント Stellite 3 powder is used to fabricate wear-resistant components, including valves, pumps, and bearings. Its resistance to abrasion and erosion makes it ideal for applications where components are subjected to constant wear and tear. Stellite 3-based components are commonly found in industries such as mining, oil and gas, and power generation. 航空宇宙・防衛 The aerospace and defense industries rely on Stellite 3 powder for critical components due to its high-temperature strength, corrosion resistance, and wear resistance. Applications include turbine blades, rocket nozzles, and other components that operate in harsh environments. Other Industries Stellite 3 powder has applications in various other industries, including: Applications of Stellite 3 Powder Stellite 3 powder’s unique properties make it a valuable material in a wide range of industries. Its applications span from cutting tools and wear-resistant components to aerospace and defense. As technology continues to advance, new and innovative applications for Stellite 3 powder are likely to emerge. はじめに Stellite 3 powder is one of several Stellite alloys, each with unique properties and applications. This chapter will compare Stellite 3 to other common Stellite alloys, highlighting their differences in composition, properties, and suitability for various applications. ステライト 6 Stellite 6 is another popular Stellite alloy known for its higher cobalt content and improved hot hardness. This makes it suitable for applications that require resistance to high-temperature wear and corrosion. However, Stellite 6 may be less resistant to certain types of corrosion compared to Stellite 3. ステライト21 Stellite 21 is a Stellite alloy with a higher chromium content, which provides enhanced resistance to pitting corrosion. It is often used in applications where exposure to aggressive environments is a concern. However, Stellite 21 may have slightly lower hardness and wear resistance compared to Stellite 3. Comparison of Stellite Alloys The choice of Stellite alloy depends on the specific requirements of the application. Factors to consider include: 結論 Stellite 3 powder is a versatile material with unique properties that make it suitable for a wide range of applications. However, other Stellite alloys, such as Stellite 6 and Stellite 21, may be more appropriate for specific requirements. By carefully considering the properties and applications of each alloy, engineers and manufacturers can select the optimal Stellite material for their needs. はじめに The field of materials science is constantly evolving, and Stellite 3 powder is no exception. This chapter will explore some of the potential future trends and developments in the production, properties, and applications of Stellite 3 powder. Advances in Powder Metallurgy Techniques Continued advancements in powder metallurgy techniques will likely lead to improvements in the production of Stellite 3 powder. New methods may enable the creation of finer particles with more uniform properties, resulting in enhanced performance and reduced manufacturing costs. New Applications and Industries As technology progresses, new applications and industries may emerge that can benefit from the unique properties of Stellite 3 powder. For example, advancements in additive manufacturing (3D printing) may enable the production of complex Stellite 3 components with intricate geometries. Research and Development Efforts Ongoing research and development efforts will continue to explore ways to improve the properties and performance of Stellite 3 powder. This may involve investigating new alloy compositions, developing novel manufacturing techniques, or exploring new applications. Potential Future Trends and Developments The future of Stellite 3 powder is promising, with potential advancements in manufacturing techniques, new applications, and ongoing research and development efforts. As technology continues to evolve, Stellite 3 powder will likely play an increasingly important role in various industries, providing exceptional performance and durability. Q1: What makes Stellite 3 powder a good choice for wear-facing applications, especially in harsh environments? A1: Stellite 3 powder is a cobalt-based alloy specifically designed to handle demanding wear applications. It excels due to its remarkable combination of wear resistance, high-temperature strength, and corrosion resistance, making it a top choice for industries like oil and gas, chemical processing, and power generation, where components are exposed to extreme conditions. Q2: What are the key differences between Stellite 3 powder and other cobalt-based alloys? A2: While many cobalt-based alloys offer good wear resistance, Stellite 3 distinguishes itself through its specific composition. The blend of chromium, tungsten, and carbon creates a unique balance of hardness, toughness, and resistance to wear, galling, and abrasion, even at elevated temperatures. This makes it superior to other cobalt alloys in demanding wear applications. Q3: What are the recommended thermal spray processes for applying Stellite 3 powder coatings? A3: Achieving optimal coating performance requires using appropriate thermal spray processes. For Stellite 3 powder, High-Velocity Oxygen Fuel (HVOF) and Plasma Transferred Arc (PTA) welding are recommended. These techniques ensure proper particle melting and bonding, resulting in dense, durable coatings with superior properties. Q4: Can you provide examples of specific components that often benefit from Stellite 3 powder coatings? A4: Many industrial components exposed to harsh conditions benefit from the protective qualities of Stellite 3 coatings. Some prime examples include valves, seats, seals, pumps, and other parts subjected to high wear, erosion, or corrosive environments. Applying Stellite 3 coatings to these components significantly extends their lifespan and reduces maintenance requirements. Q5: What post-coating treatments are typically performed on Stellite 3 coatings to enhance their performance? A5: While Stellite 3 coatings offer excellent properties as-sprayed, post-coating heat treatments can further enhance their performance. These treatments, involving controlled heating and cooling cycles, are tailored to the specific application and aim to relieve residual stresses within the coating while optimizing its hardness and wear resistance for maximum durability.
テクニック
メリット
デメリット
霧化
Versatile, produces fine particles
Requires specialized equipment, energy-intensive
プラズマ・スプレー
Suitable for coatings, rapid deposition
Limited control over particle size, potential for porosity
Stellite 3 Powder
プロパティ
代表値
Hardness (BHN)
500-600
引張強さ (MPa)
1000-1200
延性
中程度
Stellite 3 Powder
産業
アプリケーション
切削工具
Drills, milling cutters, reamers
耐摩耗コンポーネント
Valves, pumps, bearings
航空宇宙・防衛
タービンブレード、ロケットノズル
化学処理
Valves, pumps
海洋産業
Propellers, shafts, seals
自動車産業
Valve seats, exhaust valves
Stellite 3 Powder
合金
構成
主要物件
アプリケーション
Stellite 3
Cobalt-based, high chromium
High hardness, wear resistance, corrosion resistance
Cutting tools, wear-resistant components, aerospace
ステライト 6
Cobalt-based, higher cobalt
Improved hot hardness, wear resistance
High-temperature applications, turbine blades
ステライト21
Cobalt-based, higher chromium
Enhanced pitting corrosion resistance
Aggressive environments, chemical processing
Stellite 3 Powder
トレンド
潜在的なメリット
Advances in powder metallurgy
Improved particle size distribution, reduced manufacturing costs
New applications and industries
Expanded market for Stellite 3 powder
Research and development efforts
Enhanced properties, improved performance
Stellite 3 Powder: Your Top 5 Questions Answered
If you would like to know more about the wide range of Cobalt Based Powder, please click on the names in the table: