In the demanding world of industrial manufacturing, where performance and reliability are paramount, few materials can match the exceptional resilience of 316L 스테인리스 스틸 파우더. This austenitic stainless steel, celebrated for its superior corrosion resistance, impressive strength, and biocompatibility, has become the gold standard for applications demanding unwavering performance in the face of challenging environments and stringent requirements.
This comprehensive guide delves deep into the world of 316L stainless steel powder, uncovering the secrets behind its remarkable properties, exploring its diverse applications across industries, and revealing how this exceptional material can empower you to create cutting-edge products that redefine durability and longevity.
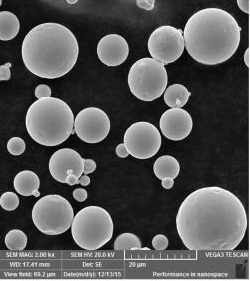
Deconstructing Durability: Understanding 316L Stainless Steel Powder
316L stainless steel powder is not merely finely ground metal; it’s a meticulously engineered material, meticulously crafted to deliver exceptional performance in the most demanding applications. As a low-carbon variant of the renowned 316 stainless steel, 316L boasts even greater resistance to corrosion, particularly after welding, making it an indispensable asset in industries ranging from aerospace and chemical processing to medical devices and marine engineering.
The Alchemy of Strength: Composition Breakdown
The secret to 316L stainless steel powder’s impressive resilience lies in its carefully balanced chemical composition, a symphony of elements working in concert to achieve unparalleled performance:
- 철(Fe): Forming the backbone of 316L’s structure, iron provides the inherent strength and stability upon which its remarkable properties are built.
- 크롬 (Cr): The guardian against corrosion, chromium forms a microscopically thin, yet incredibly robust, oxide layer on the material’s surface, effectively shielding it from the ravages of moisture, oxygen, and a wide array of corrosive agents.
- 니켈(Ni): Enhancing both corrosion resistance and ductility, nickel improves 316L’s ability to withstand deformation without fracturing, making it ideal for applications requiring both strength and flexibility.
- 몰리브덴(Mo): The secret weapon of 316L, molybdenum elevates its resistance to pitting and crevice corrosion, particularly in chloride-rich environments, making it the go-to choice for marine applications and chemical processing equipment.
- Low Carbon (L): The “L” in 316L signifies its low carbon content, which minimizes the risk of carbide precipitation during welding, preserving its exceptional corrosion resistance even in welded components.
This meticulously calibrated blend of elements, combined with the precision and control offered by powder metallurgy, transforms 316L stainless steel powder into a material capable of exceeding expectations in the most demanding environments.
Why Choose 316L Stainless Steel Powder? Unveiling the Advantages
In the competitive arena of high-performance materials, 316L stainless steel powder stands tall as a beacon of reliability and versatility, offering a compelling array of advantages that can revolutionize your manufacturing capabilities:
- Unmatched Corrosion Resistance: 316L’s high chromium, nickel, and molybdenum content makes it exceptionally resistant to a wide spectrum of corrosive agents, including acids, alkalis, chlorides, and seawater. This inherent resistance to corrosion makes it the material of choice for applications in harsh environments, such as chemical processing plants, offshore oil rigs, and marine vessels.
- Exceptional Strength and Durability: 316L stainless steel powder exhibits impressive tensile strength, yield strength, and fatigue resistance, allowing it to withstand high stresses, pressures, and cyclic loading without compromising its structural integrity. This makes it ideal for demanding applications such as pressure vessels, pipelines, and structural components in challenging environments.
- 뛰어난 생체 적합성: 316L’s biocompatibility and resistance to corrosion make it a preferred material for medical implants, surgical instruments, and other medical devices that come into contact with the human body. Its inert nature minimizes the risk of allergic reactions or adverse tissue responses, ensuring patient safety and implant longevity.
- 고온 성능: 316L stainless steel powder retains its strength and corrosion resistance at elevated temperatures, making it suitable for applications involving exposure to heat, such as heat exchangers, furnace components, and exhaust systems.
- Formability and Weldability: Despite its impressive strength, 316L exhibits good formability, allowing it to be shaped into complex geometries using various manufacturing processes. It also demonstrates excellent weldability, enabling the creation of strong, reliable joints for intricate assemblies.
Powder Metallurgy: Unlocking the True Potential of 316L
While 316L stainless steel can be processed through traditional casting and forging methods, powder metallurgy has emerged as the superior manufacturing technique, unlocking the material’s true potential and enabling the creation of components with unparalleled properties and performance characteristics.
The Powder Metallurgy Advantage: A Closer Look
기능 | Traditional Methods | 분말 야금 |
---|---|---|
재료 활용 | Lower | 더 높음 |
설계 유연성 | 제한적 | 광범위 |
Microstructure Control | 제한적 | Precise |
기계적 특성 | 양호 | 향상된 |
Porosity Control | 어려운 | Precise |
Here’s a closer look at how powder metallurgy elevates 316L stainless steel:
- Enhanced Purity and Homogeneity: Powder metallurgy minimizes the risk of impurities and ensures a uniform distribution of alloying elements throughout the material, resulting in consistent and predictable performance.
- Near-Net-Shape Components: The ability to form complex shapes directly from powder reduces the need for costly and time-consuming secondary machining operations, saving time and resources while enabling the creation of intricate geometries.
- Tailored Microstructures: Powder metallurgy empowers manufacturers to fine-tune the microstructure of 316L components with unparalleled precision. By carefully controlling parameters like powder particle size, compaction pressure, and sintering temperature, manufacturers can optimize grain size, porosity, and mechanical properties to meet specific application requirements.
316L Stainless Steel Powder in Action: Real-World Applications
The exceptional combination of corrosion resistance, strength, biocompatibility, and high-temperature performance makes 316L stainless steel powder a sought-after material across a diverse range of industries, enabling the creation of high-performance components for critical applications:
- Medical Devices and Implants: 316L’s biocompatibility, corrosion resistance, and sterilizability make it an ideal material for medical implants, such as orthopedic implants, cardiovascular stents, and dental implants. Its inert nature ensures long-term compatibility with the human body, while its strength and durability provide reliable performance for the lifetime of the implant.
- 화학 처리 장비: In the demanding world of chemical processing, 316L stainless steel powder reigns supreme. Its exceptional resistance to corrosive chemicals, high temperatures, and pressures makes it the material of choice for tanks, vessels, pipes, valves, pumps, and other critical components that handle corrosive substances and operate under extreme conditions.
- 항공우주 부품: The aerospace industry demands materials that can withstand extreme temperatures, pressures, and corrosive environments. 316L stainless steel powder rises to the challenge, finding applications in engine components, exhaust systems, structural parts, and fasteners, ensuring the safety and reliability of aircraft and spacecraft.
- Marine Engineering and Offshore Oil & Gas: The harsh marine environment, with its high salinity, moisture, and corrosive elements, poses a constant challenge to materials. 316L stainless steel powder’s exceptional resistance to seawater corrosion makes it an indispensable material for shipbuilding, offshore oil & gas platforms, desalination plants, and other marine applications, ensuring long-term durability and reliability in demanding marine environments.
- Food and Beverage Processing: Hygiene and corrosion resistance are paramount in food and beverage processing. 316L stainless steel powder meets these stringent requirements, finding applications in tanks, vats, pipes, valves, and other equipment that come into contact with food products, ensuring safety, hygiene, and preventing contamination.
This is just a glimpse into the vast potential of 316L stainless steel powder. As industries continue to innovate and demand materials that can withstand increasingly challenging environments and meet stringent performance requirements, this exceptional material is poised to play an even more significant role in shaping the future of manufacturing.
The Future of 316L Stainless Steel Powder: Innovation and Beyond
The world of materials science is in a constant state of evolution, and 316L stainless steel powder is no exception. Researchers and manufacturers are continuously pushing the boundaries, exploring innovative ways to enhance its properties, expand its applications, and unlock its full potential:
- Advanced Additive Manufacturing: Metal additive manufacturing techniques, such as laser powder bed fusion (LPBF) and binder jetting, are rapidly transforming the manufacturing landscape, and 316L stainless steel powder is at the forefront of this revolution. These advanced additive manufacturing technologies are opening up new possibilities for creating complex 316L components with intricate geometries, internal features, and optimized designs, allowing engineers to create parts with enhanced performance, reduced weight, and customized properties.
- Surface Engineering: The surface of a material is often the first line of defense against wear, corrosion, and fatigue. Researchers are exploring advanced surface treatments, such as coatings, nitriding, and laser peening, to further enhance the surface properties of 316L components. These treatments can create even more durable surfaces, improve wear and corrosion resistance, and enhance fatigue life, extending the lifespan of components and expanding their potential applications in demanding environments.
- Alloy Optimization: The quest for the perfect material is an ongoing endeavor, and 316L stainless steel powder is no exception. Ongoing research focuses on fine-tuning the chemical composition of 316L, exploring the addition of new alloying elements, and optimizing processing parameters to achieve even better combinations of strength, toughness, corrosion resistance, and other desirable properties. These advancements could lead to the development of new 316L grades with enhanced performance characteristics, tailored to meet the ever-increasing demands of industries seeking high-performance materials for the most challenging applications.
FAQs: Addressing Your 316L Stainless Steel Powder Queries
1. How does 316L stainless steel powder differ from 316 stainless steel powder?
The key difference lies in the carbon content. 316L has a lower carbon content (indicated by the “L” for low carbon) than 316. This lower carbon content reduces the risk of carbide precipitation during welding, making 316L more resistant to sensitization and intergranular corrosion, especially in as-welded conditions.
2. Can 316L stainless steel powder be used for applications requiring high magnetic permeability?
316L stainless steel is generally considered non-magnetic in its annealed state. However, it can exhibit slight magnetic properties after cold working or welding. If strong magnetic properties are required, other materials like ferritic or martensitic stainless steels might be more suitable.
3. What are the typical applications of 316L stainless steel powder in additive manufacturing?
316L is widely used in additive manufacturing for producing complex components like:
- 의료용 임플란트: Custom-designed implants, bone plates, and surgical instruments.
- Aerospace parts: Fuel nozzles, turbine blades, and complex internal channels in engine components.
- Tooling and molds: Conformal cooling channels in injection molding tools for improved cooling efficiency.
4. How does the cost of 316L stainless steel powder compare to other stainless steel grades?
316L stainless steel powder is generally more expensive than standard grades like 304 due to the addition of molybdenum and the controlled processing required to maintain its low carbon content. However, its superior properties, especially its enhanced corrosion resistance, often outweigh the initial cost difference in demanding applications where long-term performance and reliability are crucial.
5. What are the key factors to consider when selecting a supplier for 316L stainless steel powder?
When choosing a supplier, it’s essential to consider factors like:
- 파우더 품질: Ensure the powder meets industry standards for chemical composition, particle size distribution, and purity.
- Production capabilities: Assess the supplier’s capacity to meet your volume requirements and delivery timelines.
- 품질 인증: Look for certifications like ISO 9001 and AS9100 to ensure adherence to quality management systems.
- 기술 전문성: Choose a supplier with experience in powder metallurgy and a deep understanding of 316L’s properties and applications.
FAQs: Addressing Your 316L Stainless Steel Powder Queries
1. How does 316L stainless steel powder differ from 316 stainless steel powder?
The key difference lies in the carbon content. 316L has a lower carbon content (indicated by the “L” for low carbon) than 316. This lower carbon content reduces the risk of carbide precipitation during welding, making 316L more resistant to sensitization and intergranular corrosion, especially in as-welded conditions.
2. Can 316L stainless steel powder be used for applications requiring high magnetic permeability?
316L stainless steel is generally considered non-magnetic in its annealed state. However, it can exhibit slight magnetic properties after cold working or welding. If strong magnetic properties are required, other materials like ferritic or martensitic stainless steels might be more suitable.
3. What are the typical applications of 316L stainless steel powder in additive manufacturing?
316L is widely used in additive manufacturing for producing complex components like:
- 의료용 임플란트: Custom-designed implants, bone plates, and surgical instruments.
- Aerospace parts: Fuel nozzles, turbine blades, and complex internal channels in engine components.
- Tooling and molds: Conformal cooling channels in injection molding tools for improved cooling efficiency.
4. How does the cost of 316L stainless steel powder compare to other stainless steel grades?
316L stainless steel powder is generally more expensive than standard grades like 304 due to the addition of molybdenum and the controlled processing required to maintain its low carbon content. However, its superior properties, especially its enhanced corrosion resistance, often outweigh the initial cost difference in demanding applications where long-term performance and reliability are crucial.
5. What are the key factors to consider when selecting a supplier for 316L stainless steel powder?
When choosing a supplier, it’s essential to consider factors like:
- 파우더 품질: Ensure the powder meets industry standards for chemical composition, particle size distribution, and purity.
- Production capabilities: Assess the supplier’s capacity to meet your volume requirements and delivery timelines.
- 품질 인증: Look for certifications like ISO 9001 and AS9100 to ensure adherence to quality management systems.
- 기술 전문성: Choose a supplier with experience in powder metallurgy and a deep understanding of 316L’s properties and applications.
모든 것을 알고 싶다면 이 가이드가 도움이 될 것입니다.
철 기반 합금 분말: 우수성을 위한 궁극의 완벽한 가이드