In the competitive landscape of material science and advanced manufacturing, achieving superior product quality while optimizing costs is paramount. 물 분무 powders, with their unique combination of desirable properties, have emerged as a leading material choice across a range of industries. But what exactly makes them stand out? Let’s delve into the five key properties that set water atomized powders apart and explore how these properties translate into real-world advantages.
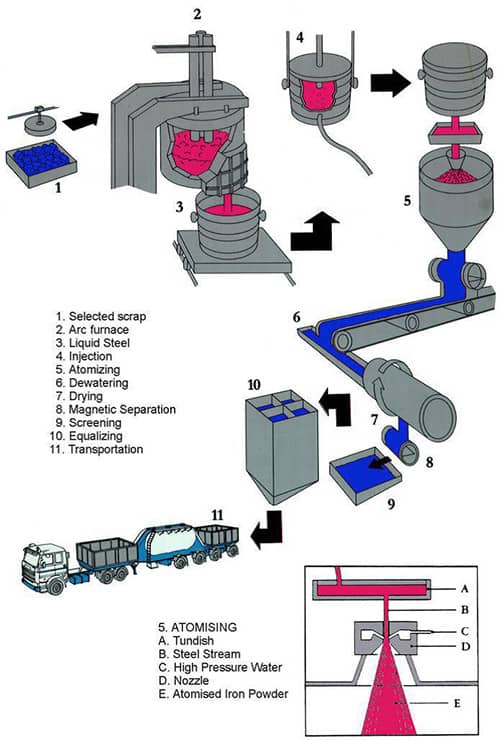
1. Exceptional Purity: The Foundation of Quality
Imagine constructing a high-performance engine with contaminated metal alloys. The results could be catastrophic. In industries demanding high performance, reliability, and longevity, material purity is non-negotiable. Water atomized powders excel in this aspect, offering a level of purity unmatched by many other powder production methods.
The water atomization process utilizes high-pressure water jets to break down molten metal into fine droplets. Water, being chemically inert, minimizes the risk of oxidation and contamination during this critical transformation. This results in powders with exceptionally high purity levels, often exceeding those achieved through gas atomization or other methods.
Benefits of High Purity:
- 향상된 내식성: Impurities within a metal matrix can act as starting points for corrosion initiation and propagation. High-purity powders translate to components with superior corrosion resistance, extending their lifespan in demanding environments such as chemical processing, marine applications, and outdoor exposure.
- 향상된 기계적 특성: Even minute impurities can compromise a material’s strength, ductility, fatigue resistance, and overall structural integrity. High-purity water atomized powders contribute to more robust and reliable final products, capable of withstanding demanding operating conditions.
- Greater Predictability & Control: When you begin with a pure base material, you have greater control over the final product’s properties. This leads to more predictable and consistent performance, reducing the risk of unexpected failures and ensuring consistent product quality.
2. Spherical Morphology: The Shape of Performance
Think about filling a container with irregularly shaped rocks versus smooth, round marbles. The marbles will pack more efficiently, leaving less empty space. This simple analogy highlights a key advantage of water atomized powders – their predominantly spherical shape, a characteristic that significantly impacts their performance in various applications.
During the rapid cooling phase of water atomization, the molten metal droplets solidify quickly within the water bath. This rapid solidification promotes the formation of spherical particles, a highly desirable attribute in powder metallurgy, additive manufacturing, and other powder processing techniques.
Benefits of Spherical Morphology:
- 향상된 흐름성: Spherical powders flow more easily and consistently compared to irregularly shaped powders. This is crucial for processes like powder metallurgy and additive manufacturing, where uniform powder delivery and spreading are essential for achieving consistent density and part geometry.
- 포장 밀도 개선: The spherical shape allows for tighter packing of powder particles, leading to denser and more homogenous final products after compaction and sintering. This higher density translates to superior mechanical properties and reduced porosity in the final component.
- Reduced Wear and Tear: In applications involving powder flow and handling, spherical particles minimize friction and wear on equipment, contributing to longer equipment lifespan and reduced maintenance costs. This is particularly important in industrial settings where downtime can be costly.
3. Controlled Particle Size Distribution: Precision Engineering at its Finest
Imagine trying to create a smooth, flawless surface coating using a mixture of coarse sand and fine dust. Achieving a uniform coating would be nearly impossible. Similarly, in many applications, controlled particle size distribution is vital for achieving the desired material properties and processability.
Water atomization offers a high degree of control over particle size, allowing manufacturers to fine-tune the powder characteristics to meet specific application needs. By adjusting process parameters like water jet pressure, nozzle design, and melt flow rate, manufacturers can precisely control the particle size distribution of the resulting powder.
Benefits of Controlled Particle Size Distribution:
- Tailored Material Properties: Particle size influences a material’s surface area, reactivity, porosity, and other crucial properties. Controlled size distribution allows manufacturers to tailor materials for specific applications, optimizing characteristics like surface finish, reaction rates, or sintering behavior.
- Enhanced Processability: In powder metallurgy and additive manufacturing, consistent particle size ensures uniform powder flow, packing, and sintering, leading to higher quality parts with improved dimensional accuracy and mechanical properties. This control is critical for achieving repeatable and reliable manufacturing processes.
- 표면 마감 개선: Finer particle sizes contribute to smoother surface finishes in coatings and additive manufacturing, reducing the need for extensive post-processing steps like grinding or polishing. This not only saves time and costs but also enhances the aesthetic appeal and functionality of the final product.
4. Alloy Versatility: Expanding the Material Palette
The field of materials science is constantly evolving, with new alloys being developed to meet increasingly demanding performance requirements across various industries. Water atomization shines in its ability to handle a wide range of metals and alloys, including those with high melting points that might pose challenges for other atomization techniques.
Benefits of Alloy Versatility:
- Access to Advanced Materials: Water atomization allows manufacturers to utilize a wider range of alloys, including specialty metals like titanium and nickel-based superalloys, opening doors to new possibilities in product design and performance. This access to advanced materials enables the creation of components with exceptional strength-to-weight ratios, high-temperature resistance, and other desirable properties.
- Customization & Innovation: The ability to process diverse alloys enables the creation of tailored materials with specific properties to meet unique application requirements. This flexibility fosters innovation in various industries, allowing engineers to develop novel solutions for challenging problems.
- Responsiveness to Market Demands: As new alloys emerge and material requirements evolve, water atomization provides a reliable and adaptable method for producing powders, ensuring manufacturers can keep pace with evolving market demands and stay ahead of the competition.
5. Cost-Effectiveness: Optimizing Value
In today’s competitive landscape, achieving high quality at a reasonable cost is paramount for business success. Water atomization offers a compelling combination of performance and affordability, making it an attractive option for manufacturers seeking to optimize their production processes.
Factors Contributing to Cost-Effectiveness:
- 높은 생산 속도: Water atomization is a relatively high-throughput process, allowing for the production of large quantities of powder in a shorter timeframe. This high production capacity contributes to lower per-unit costs, making it a scalable solution for meeting large-scale demand.
- 에너지 소비 감소: Compared to gas atomization, which requires heating and controlling a stream of inert gas, water atomization generally consumes less energy. This lower energy requirement further reduces operational expenses, contributing to overall cost savings.
- 재료 낭비 감소: The controlled nature of the water atomization process, combined with the ability to recycle unused powder, minimizes material waste. This efficient use of raw materials contributes to cost savings and aligns with sustainability goals.
Water Atomization vs. Other Methods: A Comparative Glance
기능 | 물 분무 | 가스 분무 |
---|---|---|
파티클 모양 | Predominantly Spherical | Irregular, Often Tear-Drop Shaped |
입자 크기 분포 | Narrow, Highly Controllable | Wider, Less Controllable |
분말 순도 | High Due to Inert Atmosphere | Moderate, Potential for Oxidation |
생산 비용 | Lower Operating Costs | Higher Operating Costs (Gas Heating) |
합금 유연성 | High, Suitable for High Melting Point Metals | Moderate, Limited by Melting Point Constraints |
FAQs: Water Atomized Powders – Delving Deeper into the Details
Water atomized powders offer a unique combination of properties that make them highly desirable across various industries. Here we address some common questions, providing a deeper understanding of their capabilities and applications.
1. What types of applications are best suited for water atomized powders?
Water atomized powders excel in applications demanding high purity, consistent particle size, and excellent flowability. This makes them ideal for:
- 분말 야금: Manufacturing high-performance gears, bearings, and structural components with superior mechanical properties.
- 적층 제조(3D 프린팅): Creating complex geometries with high accuracy and excellent surface finish in aerospace, medical, and automotive industries.
- 금속 사출 성형(MIM): Producing small, intricate parts with tight tolerances for electronics, medical devices, and firearm components.
- 열 스프레이 코팅: Applying wear-resistant, corrosion-resistant, or thermally insulating coatings to surfaces in aerospace, energy, and automotive industries.
- Welding Consumables: Manufacturing welding wires and fluxes that ensure smooth arc stability, low spatter, and high-quality welds.
2. How does the cost of water atomized powders compare to gas atomized powders?
Generally, water atomization is more cost-effective than gas atomization due to several factors:
- Lower Energy Requirements: Water atomization doesn’t require heating and controlling a stream of expensive inert gases, leading to lower energy consumption.
- Faster Production Rates: Water atomization boasts higher production rates compared to gas atomization, contributing to lower per-unit costs.
- Economical Atomizing Medium: Water, being readily available and inexpensive compared to argon or nitrogen used in gas atomization, significantly reduces operational costs.
3. Can water atomization be used to produce powders from all types of metals and alloys?
Water atomization is highly versatile and compatible with a wide range of metals and alloys, including:
- Steels: Carbon steels, stainless steels, tool steels, and other alloy steels for various structural and tooling applications.
- 알루미늄 합금: Widely used in automotive, aerospace, and packaging industries for their lightweight and corrosion-resistant properties.
- 구리 합금: Utilized in electrical applications, plumbing, and heat exchangers for their excellent electrical and thermal conductivity.
- 니켈 합금: Known for their high-temperature resistance and corrosion resistance, used in aerospace, chemical processing, and energy industries.
- 티타늄 합금: Highly sought after in aerospace and medical industries for their exceptional strength-to-weight ratio and biocompatibility.
However, some reactive metals might require specialized processing conditions or modifications to the standard water atomization process.
4. How does the spherical shape of water atomized powders benefit additive manufacturing processes?
The spherical morphology of water atomized powders offers several advantages in additive manufacturing:
- Smooth Powder Flow: Spherical particles flow consistently and evenly, ensuring uniform powder distribution in the 3D printing bed, leading to consistent part density.
- Optimal Packing Density: The spherical shape allows for tighter packing, minimizing voids and porosity in the final printed part, resulting in superior mechanical properties.
- Uniform Laser Interaction: Spherical particles interact more consistently with the laser beam, promoting uniform melting and solidification, contributing to a smoother surface finish.
5. Is water atomization an environmentally friendly process?
Water atomization is considered relatively environmentally friendly compared to some other powder production methods due to:
- Non-Toxic Atomizing Medium: Water, the primary atomizing medium, is non-toxic and environmentally benign.
- Reduced Gas Emissions: Unlike gas atomization, water atomization doesn’t involve the use of inert gases, minimizing the potential for greenhouse gas emissions.
- Water Recycling: Advancements in closed-loop systems allow for water recycling within the atomization plant, reducing water consumption and minimizing wastewater discharge.
However, it’s crucial to implement proper waste management practices and ensure responsible sourcing of raw materials to minimize the overall environmental impact.