In the world of high-performance materials, where strength, durability, and precision reign supreme, M2 powder stands out as a true champion. This remarkable material, meticulously engineered through the magic of powder metallurgy, empowers manufacturers to push the boundaries of what’s possible, crafting components that can withstand the most demanding applications.
But what exactly is M2 powder, and why is it causing such a stir across industries? Buckle up as we embark on an exhilarating journey into the realm of M2 powder metallurgy, uncovering its secrets, exploring its remarkable properties, and discovering how this game-changing material can revolutionize your manufacturing processes and unlock a world of possibilities.
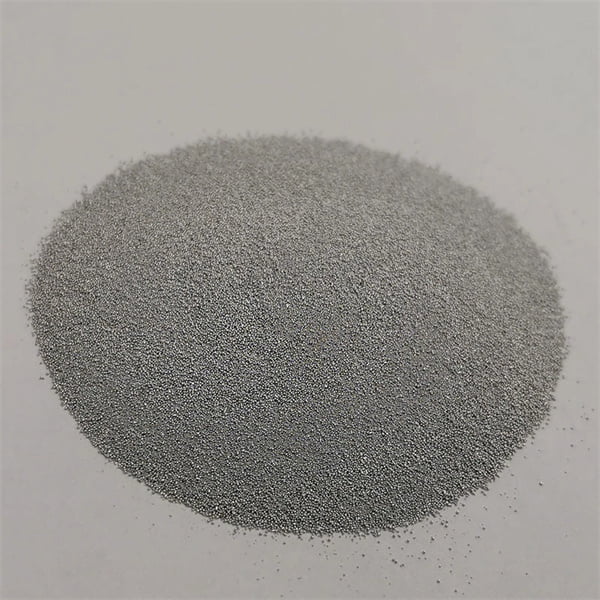
What is M2 Powder? A Glimpse into the Realm of High-Performance Metallurgy
M2 powder isn’t your average metal powder. It’s a high-speed steel powder, meticulously crafted to deliver exceptional hardness, wear resistance, and toughness – a potent combination that sets it apart from conventional steel grades. But what makes it so special? Let’s break it down:
- Composition is Key: M2 powder gets its superpowers from a carefully balanced blend of elements, each playing a crucial role in its remarkable performance. We’re talking about a potent mix of:
- Molybdeen (Mo): The backbone of M2’s strength and hardness, providing exceptional high-temperature strength and wear resistance.
- Wolfraam (W): Enhancing hardness and wear resistance, especially at elevated temperatures, making M2 ideal for high-speed cutting tools.
- Vanadium (V): Forming hard carbides that boost wear resistance and contribute to M2’s impressive toughness.
- Chroom (Cr): Boosting hardenability and providing a touch of corrosion resistance, ensuring M2 can handle a bit of heat.
- The Powder Metallurgy Magic: Unlike traditional steelmaking, which involves melting and casting, M2 powder is produced through a fascinating process called powder metallurgy. This involves:
- Atomizing: Molten M2 steel is transformed into a fine powder using high-pressure gas or water jets.
- Blending: The powder is carefully blended to ensure uniform particle size and composition.
- Verdichten: The powder is then pressed into a desired shape using immense pressure, creating a solid “green” part.
- Sinteren: The green part is heated in a controlled atmosphere, fusing the powder particles together without melting them completely, resulting in a near-net-shape component with exceptional properties.
Why Choose M2 Powder? Unveiling the Advantages that Set it Apart
M2 powder isn’t just another material option; it’s a strategic advantage, offering a compelling combination of properties that can transform your manufacturing processes and elevate your products to new heights of performance:
- Unmatched Hardness and Wear Resistance: M2 powder reigns supreme when it comes to hardness and wear resistance, laughing in the face of friction and abrasion. This makes it the ultimate choice for applications where components are subjected to extreme wear and tear, such as cutting tools, dies, and wear parts.
- Exceptional Toughness: While hardness is crucial, toughness is equally important, preventing brittle fractures under impact or shock loads. M2 powder strikes a remarkable balance between hardness and toughness, making it ideal for applications where components need to withstand both wear and impact, such as punches, chisels, and shear blades.
- High Hot Hardness: Many materials crumble under the pressure of high temperatures, losing their hardness and strength. Not M2 powder! It maintains its hardness and strength even at elevated temperatures, making it the go-to choice for high-speed cutting tools and other applications where heat is a factor.
- Enhanced Dimensional Accuracy: Powder metallurgy allows for the production of near-net-shape components with exceptional dimensional accuracy, minimizing the need for costly and time-consuming machining operations. This translates to faster production times, reduced material waste, and ultimately, lower manufacturing costs.
- Tailored Microstructures: The powder metallurgy process allows for precise control over the microstructure of M2 components, enabling manufacturers to fine-tune properties such as grain size and carbide distribution to meet specific application requirements.
M2 Powder in Action: Exploring its Diverse Applications Across Industries
The exceptional properties of M2 powder have made it a sought-after material across a wide range of industries, revolutionizing how we manufacture high-performance components:
1. Cutting Tools: Slicing Through Challenges with Precision and Speed
M2 powder is the undisputed champion of the cutting tool industry, forming the backbone of high-speed cutting tools used in a variety of machining operations:
- Drills: M2 powder’s hardness and wear resistance make it ideal for drilling tough materials like stainless steel, titanium, and hardened steel, ensuring long tool life and precise holes.
- End Mills: From roughing to finishing operations, M2 powder end mills excel at machining a wide range of materials, delivering high material removal rates, excellent surface finishes, and extended tool life.
- Milling Cutters: M2 powder milling cutters are the workhorses of the machining world, capable of tackling heavy-duty milling operations, slotting, profiling, and contouring with exceptional precision and durability.
2. Dies and Molds: Shaping the Future of Manufacturing
The durability, hardness, and dimensional accuracy of M2 powder make it a top contender for manufacturing dies and molds used in a variety of industries:
- Cold Forming Dies: M2 powder’s resistance to wear and deformation under high pressure makes it ideal for cold forming dies used to shape metals without heating, ensuring precise tolerances and long die life.
- Plastic Injection Molds: The high polish achievable with M2 powder, coupled with its resistance to wear from abrasive plastics, makes it suitable for injection molding applications, producing high-quality plastic parts with excellent surface finishes.
- Powder Compaction Dies: The durability and dimensional stability of M2 powder make it an excellent choice for manufacturing the very dies used to compact other powder metallurgy parts, ensuring consistency and precision in the powder metallurgy process itself.
3. Wear Parts: Standing Strong Against the Test of Time
In industries where components face constant friction, abrasion, and wear, M2 powder emerges as a hero, extending the lifespan of critical parts:
- Lagers en bussen: M2 powder’s exceptional wear resistance and ability to withstand high loads make it suitable for bearings and bushings used in high-stress applications, reducing friction, minimizing wear, and extending component life.
- Rollers and Guides: M2 powder’s hardness and ability to maintain its shape under pressure make it ideal for rollers and guides used in material handling systems, ensuring smooth operation, minimizing downtime, and reducing maintenance costs.
- Nozzles and Valves: In applications where abrasive fluids or powders are handled, M2 powder’s wear resistance and corrosion resistance make it a suitable choice for nozzles and valves, ensuring consistent flow rates, preventing premature wear, and extending component lifespan.
Comparing M2 Powder to the Competition: How Does it Stack Up?
Eigendom | M2 Poeder | High-Speed Steel (HSS) | Wolfraamcarbide (WC) |
---|---|---|---|
Hardheid | Heel hoog | Hoog | Extreem hoog |
Slijtvastheid | Heel hoog | Hoog | Extreem hoog |
Taaiheid | Hoog | Gematigd | Laag |
Kosten | Gematigd | Lager | Hoger |
M2 Powder vs. High-Speed Steel (HSS): M2 powder offers superior hardness, wear resistance, and hot hardness compared to conventional high-speed steel (HSS). While HSS might be more cost-effective for less demanding applications, M2 powder reigns supreme when performance is paramount.
M2 Powder vs. Tungsten Carbide (WC): Tungsten carbide boasts even higher hardness and wear resistance than M2 powder, making it suitable for extreme wear applications. However, M2 powder surpasses tungsten carbide in toughness, making it a more versatile choice for applications requiring a balance of wear resistance and impact resistance.
The Future of M2 Powder: Innovation and Advancements on the Horizon
The world of materials science is in a constant state of evolution, and M2 powder is no exception. Researchers and manufacturers are continuously exploring new ways to enhance its properties, expand its applications, and unlock its full potential. Here are some exciting advancements on the horizon:
- Metaaladditieve productie: The use of metal additive manufacturing techniques, such as selective laser melting (SLM) and electron beam melting (EBM), is revolutionizing the way M2 powder is processed, enabling the creation of complex geometries and intricate designs previously impossible with traditional manufacturing methods.
- Nanostructured M2 Powder: Researchers are exploring the use of nanotechnology to create M2 powder with even finer particle sizes, resulting in enhanced mechanical properties, improved wear resistance, and increased toughness.
- Surface Modification Techniques: Advanced surface treatments, such as coatings and nitriding, are being applied to M2 powder components to further enhance their wear resistance, corrosion resistance, and overall performance in demanding environments.
Frequently Asked Questions about M2 Powder Metallurgy
1. How does the hardness of M2 powder compare to other tool steels?
M2 powder boasts exceptional hardness, typically achieving 62-64 HRC on the Rockwell C scale. This surpasses the hardness of many other tool steels, including high-speed steel (HSS), making it ideal for applications requiring superior wear resistance and cutting performance.
2. Can M2 powder components be heat treated to further enhance their properties?
Absolutely! M2 powder responds exceptionally well to heat treatment processes like austenitizing, quenching, and tempering. These treatments allow for precise tailoring of hardness, toughness, and other mechanical properties to meet specific application requirements.
3. What are the limitations of using M2 powder in corrosive environments?
While M2 powder offers some corrosion resistance thanks to its chromium content, it’s not its strongest suit. For applications involving prolonged exposure to corrosive chemicals or harsh environments, stainless steels or other corrosion-resistant alloys might be more suitable.
4. Is M2 powder suitable for use in additive manufacturing processes?
Yes, M2 powder is compatible with certain metal additive manufacturing technologies, particularly powder bed fusion methods like selective laser melting (SLM). This opens up exciting possibilities for creating complex M2 components with intricate geometries and internal features.
5. What factors influence the cost of M2 powder?
Several factors can influence the cost of M2 powder, including raw material prices (especially molybdenum and tungsten), powder particle size and distribution requirements, and the complexity of the powder production process. Despite being more expensive than some alternatives, M2 powder’s exceptional performance often justifies the investment for demanding applications.
If you want to know everything, this guide will help:
Iron-Based Alloy Powders: Ultimate Complete Guide to Excellence