Applications of TZM Powder
Titanium‑zirconium‑molybdenum (TZM) is a molybdeen alloy that is optimized for high-temperature applications and is produced mainly by powder metallurgy. Addition of 0.5 wt% titanium, 0.08 wt% zirconium and typically 0.01–0.04 wt% carbonTZM powder, with its exceptional combination of high-temperature strength, corrosion resistance, and low thermal expansion, finds diverse applications across various industries. Its unique properties make it an ideal material for components operating in demanding environments.
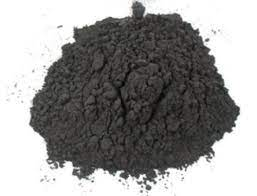
Luchtvaartindustrie
- TZM’s high-temperature strength and resistance to oxidation make it a preferred choice for rocket nozzle components, ensuring efficient and reliable performance.
- The alloy’s excellent creep resistance and fatigue properties allow it to withstand the extreme temperatures and stresses encountered in turbine blades, enhancing engine efficiency and durability.
- TZM’s ability to withstand thermal shock and maintain structural integrity makes it suitable for heat shields, protecting spacecraft from the intense heat of reentry.
Kernenergie
- TZM’s corrosion resistance and compatibility with nuclear fuels make it a suitable material for fuel cladding, ensuring the safe containment of radioactive materials.
- The alloy’s neutron absorption properties and high-temperature performance make it ideal for control rods, which regulate the nuclear reaction in reactors.
- TZM’s ability to withstand harsh environments and radiation exposure makes it a valuable material for various reactor components, such as structural supports and piping.
Chemische verwerking
- TZM’s high thermal conductivity and corrosion resistance make it an excellent choice for heat exchangers, facilitating efficient heat transfer in chemical processes.
- The alloy’s ability to withstand corrosive environments and maintain mechanical properties makes it suitable for piping and valves in chemical plants.
- TZM’s strength and resistance to high pressures make it a viable material for reactor vessels in chemical processing applications.
Other Industries
- TZM’s low thermal expansion and high electrical conductivity make it useful in electronic components, such as heat sinks and connectors.
- The alloy’s biocompatibility and corrosion resistance make it suitable for medical devices, such as implants and surgical instruments.
- TZM’s high-temperature strength and lightweight properties make it a potential material for high-performance automotive components, such as turbocharger components and exhaust manifolds.
Applications of TZM Powder
TZM powder is produced through a combination of powder metallurgy techniques and consolidation methods. These processes ensure the desired properties and characteristics of the final product. Manufacturing Processes of TZM Powder The future of TZM powder is promising, with ongoing advancements in manufacturing processes, materials science, and applications. These developments are driven by the increasing demand for high-performance materials in various industries. Future Trends and Developments in TZM Powder
Industrie
Toepassingen
Lucht- en ruimtevaart
Rocket nozzles, turbine blades, heat shields
Kernenergie
Fuel cladding, control rods, reactor components
Chemische verwerking
Heat exchangers, piping, valves, reactor vessels
Elektronica
Koellichamen, connectoren
Medische apparaten
Implantaten, chirurgische instrumenten
Automobiel
Turbocharger components, exhaust manifolds
Manufacturing Processes of TZM Powder
Poederproductie
Powder Consolidation
Oppervlaktebehandelingen
Proces
Beschrijving
Verneveling
Spraying molten alloy into a cooling gas
Mechanisch legeren
Mixing powders through mechanical deformation
Plasmaspuiten
Melting powders in a high-temperature plasma
Hot Pressing
Compacting powder under pressure at high temperature
Sinteren
Bonding powder particles through atomic diffusion
Smeden
Shaping powder into components through hammering or pressing
Coating
Applying a protective layer to the powder surface
Hittebehandeling
Modifying the microstructure through heating and cooling
Future Trends and Developments in TZM Powder
Advances in Manufacturing Processes
New Applications
Uitdagingen en kansen
Trend
Beschrijving
Advanced Powder Production
New techniques for producing TZM powder with improved properties
Additieve productie
Using TZM powder in 3D printing processes
Nanostructured TZM
Developing TZM powder with nanoscale features
Energie opslag
Applying TZM powder in batteries and fuel cells
Elektronica
Using TZM powder in electronic packaging and heat sinks
Biomedical Engineering
Using TZM powder in medical implants and devices
Kosten en beschikbaarheid
Addressing the challenges of high cost and limited availability
Recycling and Sustainability
Developing sustainable recycling processes
International Collaboration
Fostering cooperation among researchers, industry, and governments
If you would like to know more about the wide range of other Powder, please click on the names in the table: