In the relentless pursuit of pushing material boundaries, industries are constantly seeking innovative technologies that deliver unparalleled precision and performance. This demand has fueled a surge in advanced manufacturing techniques, with a particular emphasis on crafting materials at the micro-scale for enhanced properties. Enter confined распыление, a cutting-edge process revolutionizing metal powder production and unlocking a new era of possibilities for advanced manufacturing. This comprehensive guide delves deep into the intricacies of confined atomization, exploring its principles, advantages, applications, and future potential.
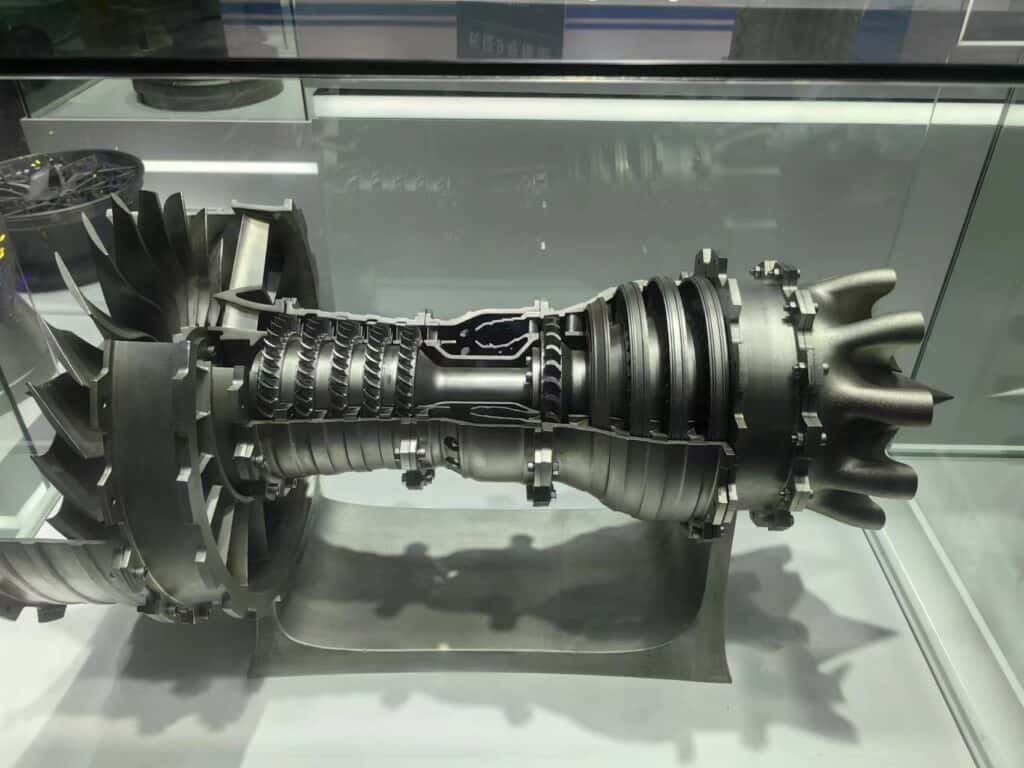
Deconstructing Confined Atomization: A Symphony of Controlled Energy
Imagine a molten metal stream, heated to its liquid state, flowing with controlled precision through a carefully designed nozzle. As it emerges, it encounters a formidable force – a high-pressure, inert gas jet strategically directed to intercept and disintegrate the molten stream into a myriad of minuscule droplets. This meticulously orchestrated collision, occurring within a confined chamber, lies at the heart of confined atomization. This chamber isn’t merely a passive container; it’s a precisely engineered environment, often incorporating specific geometries and internal features that play a crucial role in shaping the atomization process.
This is where confined atomization distinguishes itself from other atomization techniques like free-fall or even close-coupled methods. In those processes, atomization happens in a relatively open environment, leaving less control over the process dynamics. Confined atomization, however, leverages the chamber’s design to manipulate the gas flow and droplet behavior. This precise control allows manufacturers to influence droplet formation, cooling rates, and ultimately, the characteristics of the resulting powder, leading to a level of customization not achievable with other methods.
Why Confined Atomization? Unveiling the Advantages
The allure of confined atomization stems from its ability to produce metal powders with exceptional characteristics, unmatched by other atomization methods. Let’s delve into the key advantages that set this technology apart:
- Unparalleled Particle Size Control: Confined atomization reigns supreme when it comes to achieving extremely fine and uniform powder particle sizes. The confined environment, coupled with the precisely controlled gas dynamics, allows for fine-tuning the atomization process to produce powders with exceptionally narrow particle size distributions, often in the nanometer and sub-micron range. This level of control is crucial for applications demanding the utmost precision and consistency, such as additive manufacturing, where even slight variations in particle size can impact the quality of the final 3D-printed part. Similarly, in metal injection molding, precise particle size control ensures uniform flow and packing of the powder within the mold, leading to components with superior dimensional accuracy and mechanical properties.
- Exceptional Powder Purity: Maintaining high purity levels in metal powders is paramount for many applications, especially when dealing with reactive metals or alloys sensitive to contamination. The controlled atmosphere within the confined atomization chamber, typically purged with inert gases like argon or helium, minimizes the risk of oxidation or contamination during the process. This results in powders with exceptional purity levels, crucial for preserving the desired properties of the final product and ensuring optimal performance in demanding applications. For instance, in the production of high-performance alloys for aerospace applications, even trace amounts of oxygen or other impurities can significantly degrade the alloy’s mechanical properties and compromise its performance under extreme conditions.
- Tailored Particle Morphology: Beyond particle size, confined atomization offers a remarkable degree of control over particle morphology, or shape. By carefully manipulating process parameters like gas pressure, flow rate, and chamber geometry, manufacturers can influence the solidification behavior of the atomized droplets, resulting in powders with tailored shapes. This capability is particularly valuable for applications requiring specific powder flow characteristics, packing densities, or surface area properties. For instance, spherical powders are highly desirable for their excellent flowability in additive manufacturing, ensuring consistent powder delivery and layer formation during the 3D printing process. On the other hand, irregularly shaped powders might be preferred for their enhanced packing density in powder metallurgy applications, leading to higher density components with improved mechanical properties.
- Enhanced Production Efficiency: While often associated with higher initial investment costs compared to other atomization methods, confined atomization can offer significant long-term cost advantages through enhanced production efficiency. The tightly controlled process typically results in higher yields, minimizing material waste and maximizing the utilization of valuable raw materials. Additionally, the ability to produce highly consistent powders with minimal variations reduces the need for extensive post-processing steps like sieving or milling, further contributing to cost savings and streamlined production workflows. This efficiency is particularly valuable when working with expensive metals or alloys, where minimizing material waste is crucial for maintaining cost-effectiveness.
Applications Across Industries: Where Confined Atomization Shines
The unique capabilities of confined atomization have positioned it as a key enabler for a wide range of industries seeking high-performance materials and advanced manufacturing solutions. Let’s explore some of the key application areas where this technology is making a significant impact:
- Aerospace: Reaching New Heights with Advanced Materials: The aerospace industry demands materials capable of withstanding extreme temperatures, high stresses, and corrosive environments, all while maintaining strict weight limitations. Confined atomization plays a pivotal role in producing high-purity, fine-grained powders of superalloys, titanium alloys, and other advanced materials used in critical aerospace components like turbine blades, engine components, and structural parts. These powders, with their controlled particle size and morphology, enable the fabrication of components with exceptional strength-to-weight ratios, improved fatigue resistance, and enhanced resistance to creep and oxidation. These factors are crucial for ensuring the safety and reliability of aircraft and spacecraft, allowing for lighter designs, improved fuel efficiency, and extended service life.
- Medical Implants: Advancing Healthcare with Biocompatible Materials: Confined atomization is instrumental in producing biocompatible metal powders used in the manufacturing of medical implants, such as hip replacements, knee implants, dental implants, and even specialized stents and surgical instruments. The high purity levels achievable with this method minimize the risk of allergic reactions or implant rejection, a critical factor in ensuring patient well-being and successful implant integration. Moreover, the fine particle size and controlled morphology of the powders contribute to enhanced biocompatibility and osseointegration, promoting bone growth around the implant and ensuring long-term stability. The ability to produce powders from a wide range of biocompatible metals, including titanium alloys, cobalt-chrome alloys, and tantalum, expands the possibilities for developing innovative and patient-specific implant solutions tailored to individual needs and anatomical requirements.
- Electronics: Powering Innovation with High-Conductivity Materials: The electronics industry thrives on miniaturization and performance, requiring high-purity, fine-grained metal powders for various applications, including conductive pastes used in printed circuit boards, capacitor materials for energy storage, and electrical contacts for reliable signal transmission. Confined atomization excels in producing powders of metals like copper, silver, and gold with exceptional purity and fine particle sizes, crucial for achieving high conductivity, low electrical resistance, and excellent solderability. These properties are essential for creating reliable and high-performance electronic components used in smartphones, computers, automotive electronics, and countless other devices that define our modern world.
- Powder Metallurgy: Elevating Traditional Manufacturing with Advanced Powders: Powder metallurgy (PM), a well-established manufacturing process, is experiencing a resurgence thanks to the availability of high-quality powders produced through confined atomization. These powders enable the production of PM components with enhanced mechanical properties, higher densities, and improved surface finishes, expanding the application possibilities of this versatile manufacturing process. The use of fine powders reduces porosity in the final sintered parts, leading to improved strength, ductility, and fatigue resistance, making PM a viable option for a wider range of demanding applications. Additionally, the enhanced surface finish achievable with fine powders reduces the need for secondary finishing operations, contributing to cost savings and shorter lead times, making PM a more competitive manufacturing process.
Confined Atomization vs. Other Atomization Techniques: A Comparative Analysis
While confined atomization offers distinct advantages, understanding its position within the broader landscape of atomization techniques is crucial for making informed decisions about the most suitable powder production method for specific applications.
Тип распыления | Основные характеристики | Идеальные приложения | Преимущества | Недостатки |
---|---|---|---|---|
Free-Fall | Cost-effective, versatile, suitable for a wide range of powder sizes, from coarse particles for thermal spray coatings to finer powders for some powder metallurgy applications. | Powder metallurgy, thermal spray coatings, hardfacing alloys | Lower cost, simple setup, high production rates | Limited control over particle size and morphology, potential for oxidation or contamination, may require additional processing steps for specific applications. |
Close-Coupled | Produces fine, uniform powders with high efficiency, offering excellent control over particle size distribution and morphology compared to free-fall methods. Suitable for applications requiring finer powders and improved control over particle characteristics. | Additive manufacturing, metal injection molding, high-performance alloys, advanced coatings | High efficiency, good particle size control, relatively low contamination risk, suitable for a wide range of metals and alloys. | Less precise control over particle size compared to confined atomization, limited ability to produce extremely fine powders, may not be suitable for applications requiring the highest levels of purity. |
Confined | Offers exceptional control over particle characteristics, capable of producing extremely fine powders with very narrow size distributions and high purity levels. Ideal for demanding applications requiring the utmost precision and control over powder properties. | Aerospace superalloys, medical implants, specialty powders, high-value applications requiring exceptional powder quality, advanced electronics, and emerging technologies with stringent material requirements. | Unparalleled particle size control, exceptional powder purity, tailored particle morphology, enhanced production efficiency, enables the production of powders with unique properties and functionalities. | Higher initial investment cost, more complex setup, lower production rates compared to free-fall or close-coupled atomization, may not be cost-effective for all applications. |
Looking Ahead: The Future of Confined Atomization
As industries continue to demand increasingly sophisticated materials and manufacturing processes, confined atomization stands poised for continued innovation and expansion into new frontiers. Here are some key trends shaping the future of this transformative technology:
- Advanced Process Modeling and Simulation: Computational fluid dynamics (CFD) and other advanced simulation techniques are playing an increasingly important role in optimizing confined atomization processes. By modeling the complex interactions between the molten metal, atomization gas, and chamber geometry, researchers and engineers can fine-tune process parameters to achieve desired powder characteristics with greater precision and efficiency. This data-driven approach reduces the reliance on trial-and-error experimentation, accelerates the development of new powder materials, and enables the production of powders with tailored properties for specific applications, ultimately leading to faster development cycles and more efficient use of resources.
- Интеграция с аддитивным производством: The synergy between confined atomization and additive manufacturing is poised for significant growth. As additive manufacturing technologies mature and find broader adoption across industries, the demand for high-quality, specialized metal powders will continue to rise. Confined atomization, with its ability to produce powders with exceptional purity, fine particle sizes, and controlled morphology, is ideally suited to meet the stringent requirements of additive manufacturing processes, enabling the fabrication of complex, high-performance components with enhanced properties and functionalities. This integration has the potential to revolutionize manufacturing, enabling the creation of customized parts with intricate geometries and tailored properties, on-demand and with minimal waste.
- Exploration of New Material Systems: The development of novel alloys, metal matrix composites, and other advanced materials is driving innovation in confined atomization technology. These materials often present unique challenges in terms of their melting behavior, reactivity, and solidification kinetics, requiring specialized process parameters and chamber designs to achieve the desired powder characteristics. Researchers and manufacturers are continually exploring new approaches, optimizing process parameters, and developing innovative chamber designs to successfully atomize these challenging materials while maintaining the desired powder properties, unlocking their full potential for advanced applications. This continuous exploration of new material systems will drive the development of next-generation materials with unprecedented properties and performance characteristics, pushing the boundaries of what’s possible in various fields.
In the relentless pursuit of pushing material boundaries, industries are constantly seeking innovative technologies that deliver unparalleled precision and performance. This demand has fueled a surge in advanced manufacturing techniques, with a particular emphasis on crafting materials at the micro-scale for enhanced properties. Enter confined atomization, a cutting-edge process revolutionizing metal powder production and unlocking a new era of possibilities for advanced manufacturing. This comprehensive guide delves deep into the intricacies of confined atomization, exploring its principles, advantages, applications, and future potential.
Deconstructing Confined Atomization: A Symphony of Controlled Energy
Imagine a molten metal stream, heated to its liquid state, flowing with controlled precision through a carefully designed nozzle. As it emerges, it encounters a formidable force – a high-pressure, inert gas jet strategically directed to intercept and disintegrate the molten stream into a myriad of minuscule droplets. This meticulously orchestrated collision, occurring within a confined chamber, lies at the heart of confined atomization. This chamber isn’t merely a passive container; it’s a precisely engineered environment, often incorporating specific geometries and internal features that play a crucial role in shaping the atomization process.
This is where confined atomization distinguishes itself from other atomization techniques like free-fall or even close-coupled methods. In those processes, atomization happens in a relatively open environment, leaving less control over the process dynamics. Confined atomization, however, leverages the chamber’s design to manipulate the gas flow and droplet behavior. This precise control allows manufacturers to influence droplet formation, cooling rates, and ultimately, the characteristics of the resulting powder, leading to a level of customization not achievable with other methods.
Why Confined Atomization? Unveiling the Advantages
The allure of confined atomization stems from its ability to produce metal powders with exceptional characteristics, unmatched by other atomization methods. Let’s delve into the key advantages that set this technology apart:
- Unparalleled Particle Size Control: Confined atomization reigns supreme when it comes to achieving extremely fine and uniform powder particle sizes. The confined environment, coupled with the precisely controlled gas dynamics, allows for fine-tuning the atomization process to produce powders with exceptionally narrow particle size distributions, often in the nanometer and sub-micron range. This level of control is crucial for applications demanding the utmost precision and consistency, such as additive manufacturing, where even slight variations in particle size can impact the quality of the final 3D-printed part. Similarly, in metal injection molding, precise particle size control ensures uniform flow and packing of the powder within the mold, leading to components with superior dimensional accuracy and mechanical properties.
- Exceptional Powder Purity: Maintaining high purity levels in metal powders is paramount for many applications, especially when dealing with reactive metals or alloys sensitive to contamination. The controlled atmosphere within the confined atomization chamber, typically purged with inert gases like argon or helium, minimizes the risk of oxidation or contamination during the process. This results in powders with exceptional purity levels, crucial for preserving the desired properties of the final product and ensuring optimal performance in demanding applications. For instance, in the production of high-performance alloys for aerospace applications, even trace amounts of oxygen or other impurities can significantly degrade the alloy’s mechanical properties and compromise its performance under extreme conditions.
- Tailored Particle Morphology: Beyond particle size, confined atomization offers a remarkable degree of control over particle morphology, or shape. By carefully manipulating process parameters like gas pressure, flow rate, and chamber geometry, manufacturers can influence the solidification behavior of the atomized droplets, resulting in powders with tailored shapes. This capability is particularly valuable for applications requiring specific powder flow characteristics, packing densities, or surface area properties. For instance, spherical powders are highly desirable for their excellent flowability in additive manufacturing, ensuring consistent powder delivery and layer formation during the 3D printing process. On the other hand, irregularly shaped powders might be preferred for their enhanced packing density in powder metallurgy applications, leading to higher density components with improved mechanical properties.
- Enhanced Production Efficiency: While often associated with higher initial investment costs compared to other atomization methods, confined atomization can offer significant long-term cost advantages through enhanced production efficiency. The tightly controlled process typically results in higher yields, minimizing material waste and maximizing the utilization of valuable raw materials. Additionally, the ability to produce highly consistent powders with minimal variations reduces the need for extensive post-processing steps like sieving or milling, further contributing to cost savings and streamlined production workflows. This efficiency is particularly valuable when working with expensive metals or alloys, where minimizing material waste is crucial for maintaining cost-effectiveness.
Applications Across Industries: Where Confined Atomization Shines
The unique capabilities of confined atomization have positioned it as a key enabler for a wide range of industries seeking high-performance materials and advanced manufacturing solutions. Let’s explore some of the key application areas where this technology is making a significant impact:
- Aerospace: Reaching New Heights with Advanced Materials: The aerospace industry demands materials capable of withstanding extreme temperatures, high stresses, and corrosive environments, all while maintaining strict weight limitations. Confined atomization plays a pivotal role in producing high-purity, fine-grained powders of superalloys, titanium alloys, and other advanced materials used in critical aerospace components like turbine blades, engine components, and structural parts. These powders, with their controlled particle size and morphology, enable the fabrication of components with exceptional strength-to-weight ratios, improved fatigue resistance, and enhanced resistance to creep and oxidation. These factors are crucial for ensuring the safety and reliability of aircraft and spacecraft, allowing for lighter designs, improved fuel efficiency, and extended service life.
- Medical Implants: Advancing Healthcare with Biocompatible Materials: Confined atomization is instrumental in producing biocompatible metal powders used in the manufacturing of medical implants, such as hip replacements, knee implants, dental implants, and even specialized stents and surgical instruments. The high purity levels achievable with this method minimize the risk of allergic reactions or implant rejection, a critical factor in ensuring patient well-being and successful implant integration. Moreover, the fine particle size and controlled morphology of the powders contribute to enhanced biocompatibility and osseointegration, promoting bone growth around the implant and ensuring long-term stability. The ability to produce powders from a wide range of biocompatible metals, including titanium alloys, cobalt-chrome alloys, and tantalum, expands the possibilities for developing innovative and patient-specific implant solutions tailored to individual needs and anatomical requirements.
- Electronics: Powering Innovation with High-Conductivity Materials: The electronics industry thrives on miniaturization and performance, requiring high-purity, fine-grained metal powders for various applications, including conductive pastes used in printed circuit boards, capacitor materials for energy storage, and electrical contacts for reliable signal transmission. Confined atomization excels in producing powders of metals like copper, silver, and gold with exceptional purity and fine particle sizes, crucial for achieving high conductivity, low electrical resistance, and excellent solderability. These properties are essential for creating reliable and high-performance electronic components used in smartphones, computers, automotive electronics, and countless other devices that define our modern world.
- Powder Metallurgy: Elevating Traditional Manufacturing with Advanced Powders: Powder metallurgy (PM), a well-established manufacturing process, is experiencing a resurgence thanks to the availability of high-quality powders produced through confined atomization. These powders enable the production of PM components with enhanced mechanical properties, higher densities, and improved surface finishes, expanding the application possibilities of this versatile manufacturing process. The use of fine powders reduces porosity in the final sintered parts, leading to improved strength, ductility, and fatigue resistance, making PM a viable option for a wider range of demanding applications. Additionally, the enhanced surface finish achievable with fine powders reduces the need for secondary finishing operations, contributing to cost savings and shorter lead times, making PM a more competitive manufacturing process.
Confined Atomization vs. Other Atomization Techniques: A Comparative Analysis
While confined atomization offers distinct advantages, understanding its position within the broader landscape of atomization techniques is crucial for making informed decisions about the most suitable powder production method for specific applications.
Тип распыления | Основные характеристики | Идеальные приложения | Преимущества | Недостатки |
---|---|---|---|---|
Free-Fall | Cost-effective, versatile, suitable for a wide range of powder sizes, from coarse particles for thermal spray coatings to finer powders for some powder metallurgy applications. | Powder metallurgy, thermal spray coatings, hardfacing alloys | Lower cost, simple setup, high production rates | Limited control over particle size and morphology, potential for oxidation or contamination, may require additional processing steps for specific applications. |
Close-Coupled | Produces fine, uniform powders with high efficiency, offering excellent control over particle size distribution and morphology compared to free-fall methods. Suitable for applications requiring finer powders and improved control over particle characteristics. | Additive manufacturing, metal injection molding, high-performance alloys, advanced coatings | High efficiency, good particle size control, relatively low contamination risk, suitable for a wide range of metals and alloys. | Less precise control over particle size compared to confined atomization, limited ability to produce extremely fine powders, may not be suitable for applications requiring the highest levels of purity. |
Confined | Offers exceptional control over particle characteristics, capable of producing extremely fine powders with very narrow size distributions and high purity levels. Ideal for demanding applications requiring the utmost precision and control over powder properties. | Aerospace superalloys, medical implants, specialty powders, high-value applications requiring exceptional powder quality, advanced electronics, and emerging technologies with stringent material requirements. | Unparalleled particle size control, exceptional powder purity, tailored particle morphology, enhanced production efficiency, enables the production of powders with unique properties and functionalities. | Higher initial investment cost, more complex setup, lower production rates compared to free-fall or close-coupled atomization, may not be cost-effective for all applications. |
Looking Ahead: The Future of Confined Atomization
As industries continue to demand increasingly sophisticated materials and manufacturing processes, confined atomization stands poised for continued innovation and expansion into new frontiers. Here are some key trends shaping the future of this transformative technology:
- Advanced Process Modeling and Simulation: Computational fluid dynamics (CFD) and other advanced simulation techniques are playing an increasingly important role in optimizing confined atomization processes. By modeling the complex interactions between the molten metal, atomization gas, and chamber geometry, researchers and engineers can fine-tune process parameters to achieve desired powder characteristics with greater precision and efficiency. This data-driven approach reduces the reliance on trial-and-error experimentation, accelerates the development of new powder materials, and enables the production of powders with tailored properties for specific applications, ultimately leading to faster development cycles and more efficient use of resources.
- Интеграция с аддитивным производством: The synergy between confined atomization and additive manufacturing is poised for significant growth. As additive manufacturing technologies mature and find broader adoption across industries, the demand for high-quality, specialized metal powders will continue to rise. Confined atomization, with its ability to produce powders with exceptional purity, fine particle sizes, and controlled morphology, is ideally suited to meet the stringent requirements of additive manufacturing processes, enabling the fabrication of complex, high-performance components with enhanced properties and functionalities. This integration has the potential to revolutionize manufacturing, enabling the creation of customized parts with intricate geometries and tailored properties, on-demand and with minimal waste.
- Exploration of New Material Systems: The development of novel alloys, metal matrix composites, and other advanced materials is driving innovation in confined atomization technology. These materials often present unique challenges in terms of their melting behavior, reactivity, and solidification kinetics, requiring specialized process parameters and chamber designs to achieve the desired powder characteristics. Researchers and manufacturers are continually exploring new approaches, optimizing process parameters, and developing innovative chamber designs to successfully atomize these challenging materials while maintaining the desired powder properties, unlocking their full potential for advanced applications. This continuous exploration of new material systems will drive the development of next-generation materials with unprecedented properties and performance characteristics, pushing the boundaries of what’s possible in various fields.
Conclusion: Embracing the Precision of Confined Atomization
Confined atomization has emerged as a game-changer in the field of metal powder production, offering unparalleled control over particle characteristics and unlocking new possibilities for advanced manufacturing. As industries continue their relentless pursuit of lighter, stronger, more durable, and more sustainable materials and manufacturing processes, confined atomization stands as a key enabling technology, poised to shape the future of material science and drive innovation across a wide range of industries. From aerospace and medical to electronics and beyond, the precision and control offered by confined atomization will continue to drive the development of cutting-edge materials and manufacturing solutions, shaping the world around us in profound ways.
FAQs: Addressing Common Queries About Confined Atomization
1. What are the primary cost considerations when choosing between confined atomization and other methods like free-fall or close-coupled atomization?
While confined atomization typically involves a higher initial investment due to the specialized equipment and process controls, it often leads to long-term cost savings. This is attributed to its higher powder yields, reduced material waste, and the potential to eliminate or minimize post-processing steps like sieving or milling. The cost-effectiveness becomes particularly significant when working with expensive metals or alloys and in applications demanding exceptional powder quality, where the benefits outweigh the initial investment.
2. Can confined atomization be used to produce powders from a wide range of metals and alloys?
Yes, confined atomization is a versatile technique capable of processing a wide range of metals and alloys, including but not limited to aluminum, copper, nickel, titanium, and their respective alloys. The process parameters and chamber design can be tailored to accommodate the specific melting points, viscosities, and reactivity of different materials.
3. How does confined atomization contribute to the advancement of additive manufacturing technologies?
Confined atomization is a key enabler for additive manufacturing by providing the high-quality, specialized metal powders essential for these processes. The ability to produce powders with exceptional purity, fine particle sizes, and controlled morphology directly impacts the quality, mechanical properties, and surface finish of 3D-printed components.
4. What role does process modeling and simulation play in optimizing confined atomization?
Advanced simulation techniques, such as computational fluid dynamics (CFD), are instrumental in optimizing confined atomization processes. By modeling the complex interactions between the molten metal, atomization gas, and chamber geometry, engineers can predict powder characteristics, optimize process parameters, and reduce the need for costly and time-consuming trial-and-error experimentation.
5. What are the key areas of future development and innovation in confined atomization?
The future of confined atomization is driven by the exploration of new material systems, the development of even more precise process control mechanisms, and its seamless integration with advanced manufacturing technologies like additive manufacturing. Research into new chamber designs, atomization gas compositions, and real-time process monitoring will further enhance the capabilities of this technology, enabling the production of even more sophisticated and high-performance materials.
If you’d like to learn more about this, check out this comprehensive guide:
Оборудование для распыления газа: Ключ к точному проектированию