In the ever-evolving landscape of modern manufacturing, gaining a competitive edge often hinges on strategic material selection. Распыление воды metal powders have emerged as a leading contender, offering a compelling synergy of properties that translate into tangible benefits across a diverse range of industries. But what exactly are these advantages, and how do they impact your bottom line? Let’s delve into the seven key benefits of choosing water atomized metal powders for your next project, with a particular focus on how these advantages manifest in real-world applications.
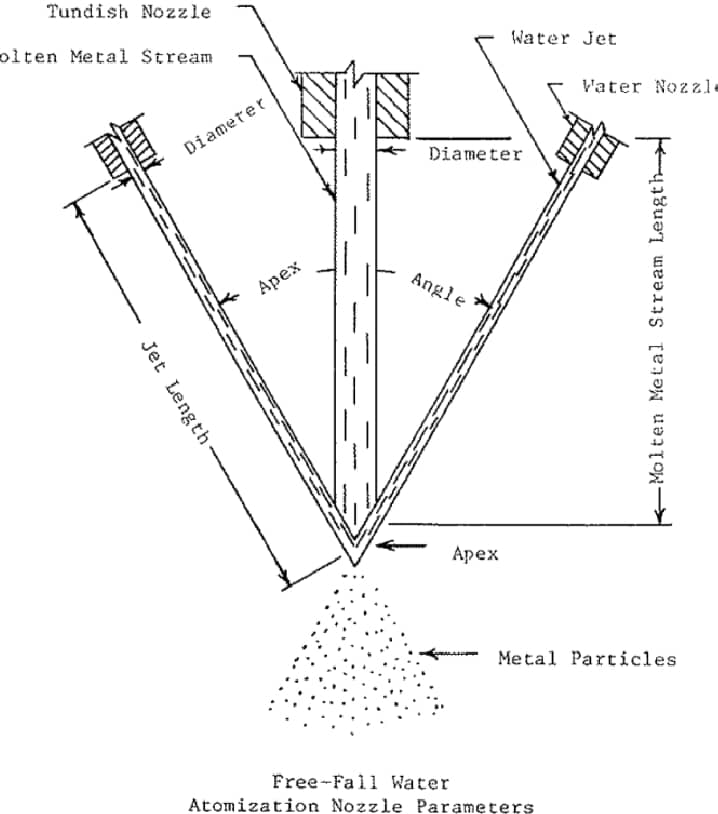
1. Superior Powder Purity: The Foundation of Quality
Imagine constructing a high-performance aircraft engine with contaminated materials. The consequences could be catastrophic. In industries where performance, reliability, and safety are paramount, material purity is non-negotiable. Water atomized powders excel in this domain, offering exceptionally high purity levels that surpass many other powder production methods.
During the water atomization process, high-pressure water jets impact a stream of molten metal, transforming it into a fine spray of droplets. These droplets rapidly solidify into powder particles as they quench within the water bath. The use of water, a chemically inert medium, minimizes the risk of oxidation and contamination during this critical transformation. This results in powders with exceptional purity levels, often exceeding those achieved through gas atomization or other methods.
Benefits of High Purity in Action:
- Аэрокосмическая промышленность: High-purity titanium alloy powders are essential for manufacturing critical aircraft components like turbine blades and engine parts. The enhanced corrosion resistance and superior mechanical properties ensure long-term performance and safety in demanding operating conditions.
- Медицинские имплантаты: Impurities in medical implants can lead to adverse reactions and implant failure. Water atomized powders, with their exceptional purity, are ideal for manufacturing biocompatible implants that minimize the risk of rejection and ensure long-term stability within the body.
- Электроника: High-purity copper powders are crucial for producing conductive pastes and inks used in printed electronics and microelectronic packaging. The absence of impurities ensures optimal electrical conductivity and reliability in these sensitive applications.
2. Spherical Morphology: The Shape of Performance
Think about filling a mold with irregularly shaped rocks versus smooth, round marbles. The marbles will pack more efficiently, leaving less empty space and creating a more uniform structure. This simple analogy highlights a key advantage of water atomized powders – their predominantly spherical shape.
The rapid cooling process inherent to water atomization plays a crucial role in shaping these desirable particles. As the molten metal droplets quench within the water bath, they solidify quickly and uniformly, promoting the formation of spherical particles. This morphology is highly desirable in various applications, especially those involving powder flow, packing, and sintering, which are essential steps in powder metallurgy and additive manufacturing.
Benefits of Spherical Morphology in Action:
- Аддитивное производство: Spherical powders flow consistently and evenly, ensuring uniform powder distribution in the 3D printing bed. This translates to higher density 3D printed parts with improved mechanical properties and a smoother surface finish, crucial for aerospace, medical, and automotive applications.
- Порошковая металлургия: The spherical shape of water atomized powders allows for tighter packing during compaction, resulting in denser and more homogenous parts after sintering. This is critical for manufacturing high-strength gears, bearings, and structural components used in demanding applications.
- Литье металлов под давлением: Spherical powders enhance the flowability of feedstock materials used in metal injection molding, allowing for the production of complex and intricate parts with tight tolerances. This is particularly valuable for manufacturing small components used in electronics, medical devices, and other precision industries.
3. Controlled Particle Size Distribution: Precision Engineering at its Finest
Imagine trying to create a flawless, high-performance coating using a mixture of coarse sand and fine dust. Achieving a uniform and durable coating would be nearly impossible. Similarly, in many applications, controlled particle size distribution is vital for achieving the desired material properties and processability.
Water atomization offers a high degree of control over particle size distribution, allowing manufacturers to fine-tune the powder characteristics to meet specific application needs. By adjusting process parameters like water jet pressure, nozzle design, melt flow rate, and the distance between the atomization nozzle and the water bath, manufacturers can precisely control the particle size distribution of the resulting powder.
Benefits of Controlled Particle Size Distribution in Action:
- Термические напыляемые покрытия: Different particle sizes are blended to create coatings with specific properties. For instance, finer particles enhance coating density and surface finish, while coarser particles improve deposition efficiency and coating thickness.
- Порошковая металлургия: Precisely controlled particle sizes ensure uniform powder flow and packing during compaction, leading to consistent density and improved mechanical properties in sintered parts. This is crucial for applications demanding high strength and reliability, such as gears and bearings.
- Аддитивное производство: Finer particle sizes in metal powders used for additive manufacturing contribute to smoother surface finishes and enhanced resolution in 3D printed parts. This is particularly important for medical implants, aerospace components, and intricate designs where surface quality is paramount.
4. Alloy Versatility: Expanding the Material Palette
The field of materials science is in a constant state of evolution, with new alloys being developed to meet the ever-increasing performance demands of various industries. Water atomization shines in its ability to handle a wide range of metals and alloys, including those with high melting points that might pose challenges for other atomization techniques.
This versatility stems from the inherent flexibility of the water atomization process. The use of water as the atomizing medium allows for the processing of a wide range of metals, from common steels and aluminum alloys to more exotic materials like titanium, nickel-based superalloys, and refractory metals.
Benefits of Alloy Versatility in Action:
- Аэрокосмическая промышленность: The ability to process high-temperature superalloys makes water atomization ideal for manufacturing turbine blades and other critical engine components that must withstand extreme temperatures and stresses.
- Медицинские имплантаты: Water atomization enables the production of powders from biocompatible titanium and cobalt-chrome alloys, essential for manufacturing implants that are well-tolerated by the human body and exhibit excellent corrosion resistance.
- Tooling & Molding: Water atomized tool steels are used to manufacture high-performance cutting tools, dies, and molds that offer superior wear resistance, hardness, and toughness, essential for demanding machining and molding applications.
5. Cost-Effectiveness: Optimizing Value
In today’s globally competitive market, achieving a balance between high quality and cost-effectiveness is paramount for business success. Water atomization offers a compelling combination of performance and affordability, making it an attractive option for manufacturers seeking to optimize their production processes without compromising on product quality.
Several factors contribute to the cost-effectiveness of water atomization:
- Высокие производственные показатели: Water atomization is a relatively high-throughput process, allowing for the production of large quantities of powder in a shorter timeframe. This high production capacity contributes to lower per-unit costs, making it a scalable solution for meeting large-scale demand.
- Низкое энергопотребление: Compared to gas atomization, which requires heating and controlling a stream of inert gas, water atomization generally consumes less energy. This lower energy requirement further reduces operational expenses, contributing to overall cost savings.
- Сокращение отходов материалов: The controlled nature of the water atomization process, combined with the ability to recycle unused powder, minimizes material waste. This efficient use of raw materials contributes to cost savings and aligns with sustainability goals.
Benefits of Cost-Effectiveness in Action:
- Автомобильная промышленность: The high production rates and cost-effectiveness of water atomized steel powders make them ideal for manufacturing gears, bearings, and other components for the automotive industry, where large production volumes and competitive pricing are essential.
- Строительная промышленность: Water atomized steel powders are used in the production of welding consumables, such as welding wires and fluxes. The cost-effectiveness of these powders contributes to more affordable welding processes, essential for large-scale construction projects.
- Powder Coating Industry: Water atomized metal powders are increasingly used in powder coating applications, offering a durable and cost-effective alternative to traditional liquid coatings. This is particularly beneficial for coating large surface areas, such as those found in architectural and industrial applications.
6. Environmental Responsibility: A Sustainable Choice
As environmental awareness continues to grow, manufacturers are increasingly seeking sustainable manufacturing solutions that minimize their ecological footprint. Water atomization aligns with this trend, offering a relatively clean and efficient powder production method compared to some alternatives.
Several factors contribute to the environmental benefits of water atomization:
- Water as Atomizing Medium: Water, the primary atomizing medium, is non-toxic and environmentally benign. Unlike some gases used in other atomization methods, water does not contribute to greenhouse gas emissions or pose significant risks to human health or the environment.
- Reduced Gas Emissions: Water atomization does not involve the use of large volumes of inert gases, which are often used in gas atomization processes. This significantly reduces the potential for greenhouse gas emissions and minimizes the overall carbon footprint of the powder production process.
- Water Recycling: Advancements in closed-loop systems allow for water recycling within the atomization plant, reducing water consumption and minimizing wastewater discharge. By treating and reusing water within the production process, water atomization minimizes its impact on local water resources.
Benefits of Environmental Responsibility in Action:
- Reduced Carbon Footprint: The use of water as the atomizing medium and the minimal use of inert gases contribute to a lower carbon footprint for water atomized powders compared to gas atomized powders. This aligns with the growing demand for sustainable manufacturing practices and helps companies meet their environmental responsibility goals.
- Minimized Water Consumption: Closed-loop water recycling systems in modern water atomization plants significantly reduce water consumption, making it a more sustainable option in water-stressed regions. This responsible use of water resources is essential for ensuring the long-term viability of manufacturing processes.
- Reduced Waste Generation: The efficient nature of water atomization, combined with the ability to recycle unused powder, minimizes waste generation. This reduces the environmental impact associated with waste disposal and promotes a more circular economy approach to material usage.
7. Enhanced Properties for Demanding Applications
The unique combination of properties offered by water atomized powders translates into enhanced performance in demanding applications across a wide range of industries. These properties include high purity, spherical morphology, controlled particle size distribution, alloy versatility, and cost-effectiveness, all of which contribute to improved material performance and expanded application possibilities.
Industry Examples:
Промышленность | Примеры применения | Основные преимущества |
---|---|---|
Аэрокосмическая промышленность | Лопатки турбин, компоненты двигателей, конструктивные элементы | High strength-to-weight ratio, high-temperature resistance, excellent fatigue resistance, corrosion resistance |
Автомобильная промышленность | Gears, bearings, fuel injectors, pistons, connecting rods | Wear resistance, corrosion resistance, high fatigue strength, good machinability, cost-effectiveness |
Медицина | Implants (orthopedic, dental, cardiovascular), surgical instruments, medical devices | Biocompatibility, corrosion resistance, high strength, wear resistance, sterilizability |
Tooling & Molding | Режущие инструменты, штампы, формы, изнашиваемые детали | Wear resistance, high hardness, high-temperature resistance, toughness, impact resistance |
Энергия | Solar cells, batteries, fuel cells, filters | High surface area, controlled porosity, catalytic properties, corrosion resistance, thermal stability |
Электроника | Capacitors, resistors, sensors, conductive inks and pastes | High purity, controlled particle size, electrical conductivity, solderability, printability |
Conclusion: Embracing the Advantages of Water Atomized Metal Powders
From superior purity and controlled particle size to cost-effectiveness and environmental responsibility, water atomized metal powders offer a compelling array of advantages for modern manufacturing. As industries continue to demand higher performance, greater customization, and more sustainable manufacturing practices, water atomized powders are poised to play an even more significant role in shaping the future of advanced materials and manufacturing technologies.