In the ever-evolving landscape of advanced materials, aluminum alloy powders have emerged as a transformative force, revolutionizing manufacturing and design across a multitude of industries. Their unparalleled versatility, seamlessly blending lightweight strength with exceptional properties, has propelled them to the forefront of innovation, empowering engineers and designers to push the boundaries of what’s possible. But with a vast and diverse array of aluminum alloy powder types available, navigating this intricate landscape can feel like embarking on an expedition through uncharted territory.
Fear not, fellow innovators! Consider this comprehensive guide your trusted compass to the exciting world of aluminum alloy powders. We’ll delve deep into the nuances of over 20 key grades, equipping you with the knowledge and insights to make informed decisions and unlock the full potential of these transformative materials, propelling your business to the forefront of its industry.
Deciphering the Code: Unlocking the Secrets of Aluminum Alloy Powder Designations
Before we embark on our exploration of specific grades, let’s demystify the language of aluminum alloy powder designations. These alphanumeric codes, far from being cryptic jargon exclusive to material scientists, hold the key to unlocking a treasure trove of information about an alloy’s composition, properties, and potential applications. By understanding these codes, you gain the power to navigate the world of aluminum alloy powders with confidence and precision.
- The Four-Digit System: A Universal Language for Aluminum Alloys: Most aluminum alloy powder designations adhere to a standardized four-digit system, a universal language that transcends geographical boundaries and industry jargon. Here’s how it works:
- First Digit: Unveiling the Core Identity: The first digit serves as the alloy’s passport, indicating the major alloying element and providing a glimpse into its general characteristics and personality.
- 1xxx: Pure Aluminum (99.00% or higher) – The purist of the aluminum family, known for its lightweight nature, exceptional corrosion resistance, and high electrical and thermal conductivity. Ideal for applications where purity is paramount.
- 2xxx: Copper (Cu) – The strongman of the group, copper additions imbue these alloys with high strength, good machinability, and excellent fatigue resistance. Often found in demanding aerospace applications where structural integrity is non-negotiable.
- 3xxx: Manganese (Mn) – The well-rounded member, manganese additions impart moderate strength, good formability, and solid corrosion resistance. A versatile choice for general-purpose applications where a balance of properties is desired.
- 4xxx: Silicon (Si) – The casting virtuoso, silicon’s claim to fame is its ability to enhance fluidity during casting, making it a key ingredient in welding and brazing alloys. When intricate designs and complex geometries are paramount, silicon takes center stage.
- 5xxx: Magnesium (Mg) – The seafarer’s ally, magnesium additions enhance weldability, corrosion resistance, and provide moderate strength. A natural fit for marine applications and environments where resisting the elements is crucial.
- 6xxx: Magnesium and Silicon (Mg + Si) – The dynamic duo, magnesium and silicon combine to create heat-treatable alloys with good formability and corrosion resistance. Their versatility makes them a popular choice across a wide range of industries and applications.
- 7xxx: Zinc (Zn) – The heavyweights of the aluminum world, zinc additions create the highest strength aluminum alloys, boasting exceptional strength-to-weight ratios and remarkable fatigue resistance. When performance under pressure is non-negotiable, these alloys rise to the challenge, finding homes in aerospace components, high-performance vehicles, and demanding tooling applications.
- 8xxx: Other elements – The niche specialists, this category encompasses alloys with unique compositions tailored to meet the demands of highly specialized applications. From lithium additions for enhanced aerospace performance to rare earth elements for elevated temperature capabilities, these alloys push the boundaries of what’s possible.
- Second Digit: Fine-Tuning the Formula: The second digit acts as a modifier, signifying subtle but important variations in the alloy’s composition or processing methods. These variations, while seemingly small, can have a significant impact on the alloy’s final properties and suitability for specific applications.
- Last Two Digits: Pinpointing the Exact Match: The final two digits act as a fingerprint, uniquely identifying the specific alloy within the series and pinpointing its exact characteristics. This level of granularity ensures that you’re selecting the ideal alloy with the precise properties required for your application, leaving no room for ambiguity.
- First Digit: Unveiling the Core Identity: The first digit serves as the alloy’s passport, indicating the major alloying element and providing a glimpse into its general characteristics and personality.
- Example: Deciphering AlSi10Mg Powder: Let’s break down the designation AlSi10Mg powder to illustrate the power of this system:
- Al: The foundation of it all, indicating an aluminum base.
- Si: Silicon takes the spotlight as the major alloying element, hinting at good casting properties.
- 10: The numerical value quantifies the silicon content, indicating approximately 10% silicon in the alloy.
- Mg: Magnesium joins the mix as a secondary alloying element, suggesting enhanced strength and potential heat-treatability.
Navigating the Landscape: Exploring 20+ Aluminum Alloy Powder Grades in Detail
Now that we’ve equipped ourselves with the knowledge to decipher alloy designations like seasoned material scientists, let’s embark on a journey through the diverse and fascinating world of aluminum alloy powder grades. Each grade possesses its own unique set of characteristics, strengths, and ideal applications. Understanding these nuances is key to selecting the perfect material for your specific needs.
1. Casting Alloys: Where Precision and Flow Converge to Create Intricate Designs
- AlSi10Mg Powder: The Casting Champion: This versatile alloy stands tall as a true champion in the casting realm, boasting an impressive combination of exceptional fluidity, excellent strength-to-weight ratio, and commendable corrosion resistance. Its ability to flow effortlessly into intricate molds while maintaining structural integrity makes it a top contender for a wide range of applications, from complex automotive parts and aerospace components to intricate molds for plastics and other materials.
- AlSi7Mg Powder: The Thermal Maestro: Offering a compelling balance of strength, ductility, and thermal conductivity, this grade excels in applications where efficient heat dissipation is paramount. Its ability to effectively transfer heat away from critical components makes it a natural fit for engine components, cylinder heads, heat sinks, and other applications where thermal management is crucial.
- AlSi12 Powder: The Intricate Detail Specialist: With its high silicon content, this alloy exhibits exceptional flow characteristics during casting, enabling the production of intricately shaped parts with fine details and complex geometries. It’s often favored for applications demanding high wear resistance, such as pistons, engine blocks, hydraulic components, and other parts subjected to friction and abrasion.
- AlSiCu Powder (AlSi10): The Strength-Enhanced Performer: The addition of copper to this alloy elevates its performance to new heights, enhancing its strength and machinability compared to its copper-free counterparts. This makes it suitable for applications requiring higher mechanical properties, such as gears, pump housings, structural components, and other parts subjected to significant stress and strain.
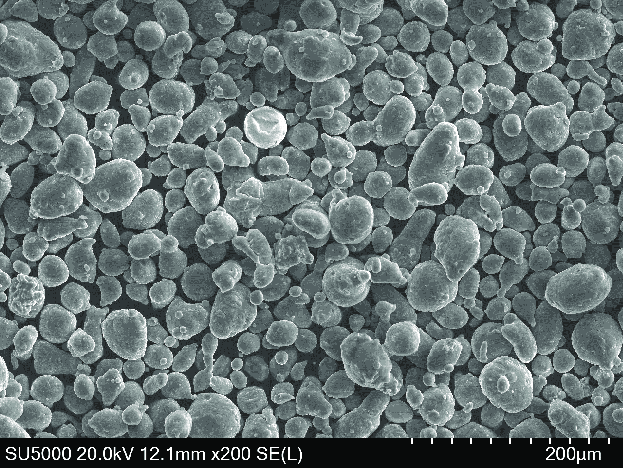

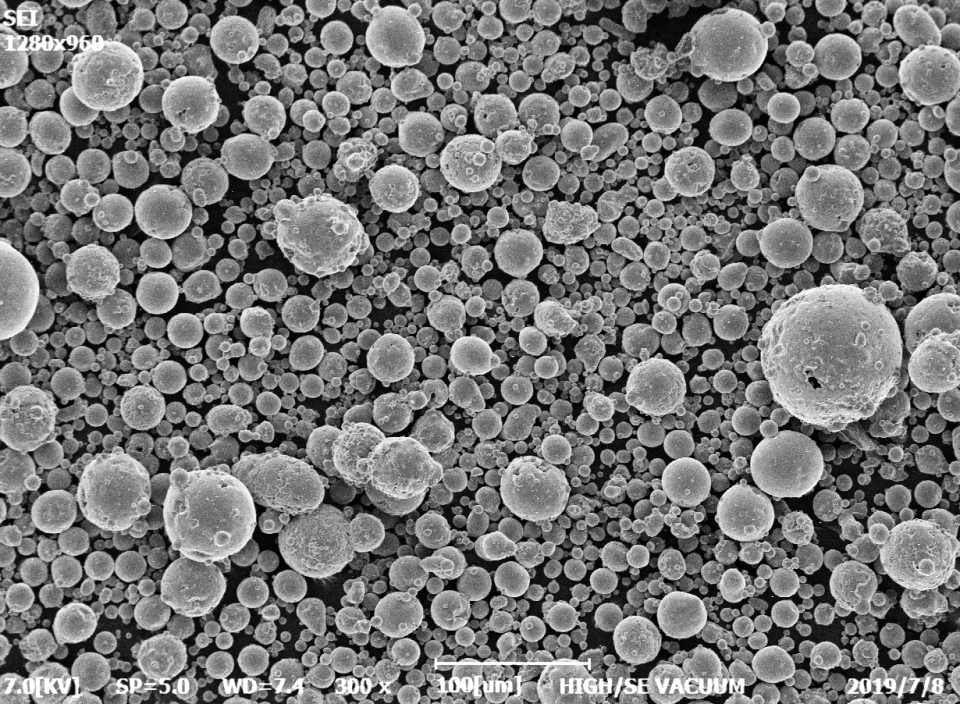
2. Wrought Alloys: Forging Strength and Durability for Demanding Applications
- Al 2024 Powder: The Aerospace Trailblazer: Renowned for its impressive strength-to-weight ratio and exceptional fatigue resistance, this high-performance alloy has earned its place as a cornerstone of the aerospace industry. Its ability to withstand the rigors of flight, enduring countless cycles of stress and strain, makes it a trusted choice for aircraft structures, fuselage panels, wing components, and other critical aerospace applications where lightweight strength and reliability are non-negotiable.
- Al 6061 Powder: The Versatile Workhorse: This adaptable alloy has earned its reputation as a true workhorse, offering a winning combination of good strength, commendable corrosion resistance, and excellent weldability. Its versatility shines through in a wide range of applications, from bicycle frames and automotive parts to architectural structures, marine components, and countless other products where a balance of properties is desired.
- Al 7075 Powder: The Strength Champion: Boasting exceptional strength that surpasses even some steels, this high-strength alloy stands as a testament to the power of aluminum alloying. Its remarkable strength-to-weight ratio and exceptional fatigue resistance make it the go-to choice for applications demanding the utmost in strength and durability, such as aircraft landing gear, high-performance sporting equipment, high-stress tooling, and other components subjected to extreme forces.
- Al 3003 Powder: The Balanced Performer: This versatile alloy strikes a harmonious balance between strength, formability, and corrosion resistance, making it suitable for a wide range of applications across various industries. Its adaptability shines through in cookware, chemical equipment, decorative trim, and other products where a combination of properties is desired.
- Al 3103 Powder: The Enhanced Strength Sibling: Similar to 3003 but with a slight edge in strength, this alloy is often favored in applications requiring good formability and corrosion resistance, such as heat exchangers, roofing, siding, and other products exposed to the elements.
- Al 3004 Powder: The Manganese-Strengthened Option: With the addition of manganese to enhance its strength, this alloy finds its niche in applications demanding good formability and corrosion resistance, such as cans, pressure vessels, and other products requiring structural integrity.
- Al 3104 Powder: The Stronger and More Durable Choice: Similar to 3004 but with enhanced strength and durability, this alloy is often chosen for applications requiring robust performance, such as awnings, siding, truck bodies, and other products subjected to wear and tear.
- Al 3203 Powder: The Magnesium-Fortified Alloy: This alloy, fortified with a higher magnesium content, offers improved strength and formability compared to its 3003 counterpart. This makes it well-suited for applications like beverage cans, pressure vessels, automotive components, and other products requiring a combination of strength and formability.
3. Other Notable Grades: Tailored Solutions for Niche Applications
- Pure Aluminum Powder: The Conductor of Choice: With its high electrical conductivity, excellent reflectivity, and commendable corrosion resistance, pure aluminum powder finds its niche in a variety of specialized applications. From powder metallurgy and conductive coatings to pigments and even pyrotechnics, pure aluminum powder delivers where other materials fall short.
- AlMgScZr Powder: The High-Temperature Performer: This specialized alloy, enhanced with the addition of scandium and zirconium, exhibits exceptional strength, creep resistance, and weldability, even at elevated temperatures. These characteristics make it ideal for high-temperature applications in aerospace, energy, and other demanding industries where materials must withstand extreme conditions.
- AlSi50 Pulver: The Brazing and Soldering Specialist: With its high silicon content, this grade is specifically engineered for brazing and soldering applications, providing excellent flow characteristics and joint strength. Its ability to effectively join dissimilar metals makes it a valuable asset in a variety of industries.
- AlSiMg Powder: The Versatile Family: This broad category encompasses a range of alloys with varying silicon and magnesium content, offering a spectrum of properties to meet diverse application requirements. These alloys typically strike a balance between strength, castability, and weldability, making them suitable for applications such as automotive parts, aerospace components, and structural elements.
Table 1: A Quick Glance at Key Properties of Select Aluminum Alloy Powder Grades
Legeringsklass | Densitet (g/cm³) | Draghållfasthet (MPa) | Förlängning (%) | Viktiga funktioner |
---|---|---|---|---|
AlSi10Mg | 2.65 | 200-300 | 8-12 | Excellent castability, good strength, corrosion resistance |
AlSi7Mg | 2.66 | 180-250 | 5-8 | Good thermal conductivity, balance of strength and ductility |
Al 2024 | 2.78 | 450-550 | 10-15 | High strength-to-weight ratio, excellent fatigue resistance |
Al 6061 | 2.70 | 290-350 | 10-18 | Good strength, corrosion resistance, weldability |
Ren Al | 2.70 | 90-120 | 20-30 | High electrical conductivity, reflectivity, corrosion resistance |
Choosing the Right Aluminum Alloy Powder: A Roadmap to Success in Material Selection
Selecting the optimal aluminum alloy powder for your specific needs is akin to choosing the right tool for the job. It requires careful consideration of several key factors to ensure that the chosen material aligns perfectly with your application requirements, processing capabilities, and budgetary constraints.
- Application Requirements: Defining the Performance Needs: Before delving into the world of alloy designations and material properties, it’s crucial to clearly define the specific mechanical, physical, and chemical properties demanded by your application. What level of strength is required? How important is ductility? Will the material be exposed to corrosive environments? What about thermal or electrical conductivity? Answering these questions will provide a roadmap for your material selection process.
- Processing Method: Aligning Material with Manufacturing: How do you plan to process the aluminum alloy powder? Different grades exhibit varying levels of suitability for specific processing techniques, such as additive manufacturing, powder metallurgy, or thermal spraying. Choosing a material that aligns with your intended processing method is crucial for ensuring manufacturing efficiency and achieving the desired product quality.
- Cost Considerations: Balancing Performance with Budget: Aluminum alloy powder prices can vary significantly depending on the alloy composition, production method, desired particle characteristics, and supplier capabilities. While high-performance alloys may offer exceptional properties, they often come at a premium cost. Balancing performance requirements with budgetary constraints is essential for finding a cost-effective solution that meets both your technical and financial needs.
Here’s a simplified breakdown to guide your selection:
- Intricate Castings with Strength and Corrosion Resistance: AlSi10Mg, AlSi7Mg, AlSi12
- High-Strength, Lightweight Components for Demanding Applications: Al 2024, Al 7075
- Versatile Applications Requiring a Balance of Properties: Al 6061, Al 3003, Al 3xxx series
- Specialized Applications with Unique Property Requirements: Pure Aluminum Powder, AlMgScZr Powder
- Brazing and Soldering Applications: AlSi50 Pulver
1. What are the key advantages of using aluminum alloy powders over traditional aluminum forms?
Aluminum alloy powders offer several advantages over traditional forms, such as ingots or billets:
- Enhanced Design Flexibility: Powder metallurgy and additive manufacturing techniques enable the creation of complex geometries and intricate designs not possible with traditional manufacturing methods.
- Förbättrade materialegenskaper: Powder processing allows for greater control over microstructure and alloy composition, leading to enhanced mechanical properties, such as higher strength, improved fatigue resistance, and tailored thermal conductivity.
- Tillverkning i nära-nätform: Powder metallurgy processes often result in near-net-shape components, reducing the need for extensive machining and minimizing material waste.
2. What are the primary applications of AlSi10Mg powder?
AlSi10Mg powder is a versatile alloy widely used in:
- Fordon: Engine components, transmission parts, structural components
- Aerospace: Lightweight brackets, housings, and structural elements
- Medicintekniska produkter: Implants, surgical instruments, prosthetics
- Konsumentvaror: Sporting equipment, electronics housings
3. What factors influence the cost of aluminum alloy powders?
Several factors impact the cost of aluminum alloy powders:
- Alloy Composition: The type and amount of alloying elements significantly influence the cost.
- Powder Particle Size and Distribution: Finer aluminum alloy powders with tighter size distributions generally command higher prices due to the increased processing required.
- Produktionsmetod: The production method, such as atomization or milling, affects the cost.
- Market Demand and Availability: Fluctuations in supply and demand can influence pricing.
4. What are the key considerations when choosing between Al 6061 and Al 7075 powder?
Both Al 6061 and Al 7075 are widely used aluminum alloys, but they differ in key properties:
- Styrka: Al 7075 exhibits significantly higher strength than Al 6061, making it suitable for high-stress applications.
- Svetsbarhet: Al 6061 offers better weldability than Al 7075, making it more suitable for applications requiring welding or joining.
- Kostnad: Al 6061 is generally more cost-effective than Al 7075.
5. What are the future trends shaping the aluminum alloy powder market?
The aluminum alloy powder market is poised for significant growth, driven by:
- Increased Adoption of Additive Manufacturing: The expanding use of additive manufacturing across industries is driving demand for high-performance aluminum alloy powders.
- Lightweighting in Automotive and Aerospace: The push for fuel efficiency and reduced emissions is driving the adoption of lightweight aluminum alloys in automotive and aerospace applications.
- Utveckling av nya legeringar: Ongoing research and development efforts are leading to the creation of new aluminum alloy powders with enhanced properties, expanding their application possibilities.
The Future is Forged with Aluminum Alloy Powders: Embracing Innovation and Sustainability
Aluminum alloy powders are more than just raw materials; they are the building blocks of a lighter, stronger, and more sustainable future. As researchers continue to push the boundaries of material science, developing new alloys with enhanced properties and exploring innovative processing techniques, aluminum alloy powders are poised to revolutionize industries far and wide. From lightweighting in aerospace and automotive to advancements in medical devices, energy technologies, and consumer products, the potential applications for these transformative materials are boundless.
Ready to unlock the limitless potential of aluminum alloy powders and embark on a journey of innovation and growth? Contact us today to discuss your specific application requirements and discover how our expertise can help you navigate the world of these transformative materials and achieve your goals. Together, let’s forge a brighter, lighter, and more sustainable future.
If you want to know more about aluminum alloy powders:
We recommend the following quality blogs for you:Aluminiumlegeringspulver: Din ultimata resurs för innovation