Introduction: Taming the Heat with Advanced Materials
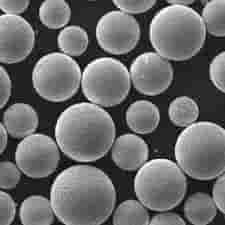
In the relentless pursuit of technological advancement, we often encounter environments of extreme heat and pressure. Whether it’s the depths of a rocket engine or the heart of a nuclear reactor, these demanding applications require materials that can withstand incredible challenges. C103 Powder(Nb Bal., Hf 9.0-11.0, Ti 0.7-1.3) niob alloy powder emerges as a champion in this arena, offering a remarkable combination of high-temperature strength, corrosion resistance, and desirable nuclear properties. This deep dive explores the properties, applications, and competitive advantages of this exceptional material.
C103 Niobium Alloy Powder: A Closer Look
What is C103 Niobium Alloy Powder?
C103 is a specific grade of niobium-based alloy specifically engineered for high-temperature applications. Its designation, C103, refers to its chemical composition, primarily consisting of niobium (Nb) as the base element, with carefully controlled additions of hafnium (Hf) and titanium (Ti). The powder form, typically produced through advanced processing techniques like plasma spheroidization (PS) and subsequent refinement (PREP), results in spherical particles with excellent flowability and packing density, making it ideal for various manufacturing processes.
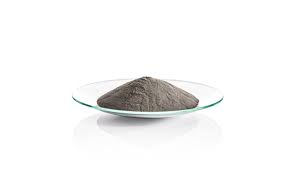
Deciphering the Properties of C103
The remarkable properties of C103 stem from the synergistic interaction of its constituent elements and the specific processing techniques used:
- Hög smältpunkt: Niobium itself boasts one of the highest melting points among all metals. The addition of hafnium and titanium further elevates this temperature threshold, making C103 suitable for applications exceeding 1000°C.
- Exceptional High-Temperature Strength: C103 maintains its strength at elevated temperatures where most metals would soften or deform. This property is crucial for components operating under extreme thermal stress.
- Utmärkt korrosionsbeständighet: Niobium forms a highly stable and protective oxide layer on its surface. This passive layer, enhanced by the presence of hafnium and titanium, provides C103 with exceptional resistance to oxidation, even in harsh environments.
- Desirable Nuclear Properties: C103 exhibits a low thermal neutron cross-section, making it relatively transparent to neutrons. This property, coupled with its high-temperature strength and corrosion resistance, makes it valuable for nuclear applications.
Processing and Manufacturing: Shaping C103 for Demanding Applications
C103’s versatility allows for its processing through various methods:
- Powder Metallurgy: Compacting and sintering C103 powder allows for the production of near-net-shape components with high density and minimal material waste.
- Additiv tillverkning: C103 powder is compatible with advanced additive manufacturing techniques like Electron Beam Melting (EBM), enabling the fabrication of complex geometries with high precision.
- Other Processes: C103 can also be processed through techniques like arc melting, electron beam welding, and hot isostatic pressing, depending on the desired final form and application.
Navigating the Landscape: Classification of Niobium Alloy Powders
Niobium alloy powders are classified based on:
- Sammansättning: The specific combination of elements and their atomic percentages dictate the properties of the resulting alloy powder.
- Produktionsmetod: Different production methods, such as plasma spheroidization or hydride-dehydride processes, influence particle size, morphology, and powder characteristics.
- Partikelstorlek och morfologi: Spherical C103 powders are often preferred for their superior flowability and packing density, particularly in additive manufacturing.
Market Trends and Future Outlook: A Glimpse into the Future
The global market for specialized niobium alloy powders like C103 is experiencing steady growth, driven by:
- Increasing Demand from High-Tech Industries: Industries such as aerospace, defense, and energy are increasingly demanding materials capable of withstanding extreme temperatures and corrosive environments.
- Advancements in Additive Manufacturing: The rise of additive manufacturing is driving the demand for high-quality metal powders like C103, which can be processed into complex components with intricate designs.
- Focus on Material Efficiency and Sustainability: The use of powder metallurgy and additive manufacturing with C103 aligns with the growing emphasis on material efficiency and reducing waste in manufacturing processes.
Unveiling the Specifics: Technical Specifications of C103 Niobium Alloy Powder
Fastighet | Värde |
---|---|
Alloy Name | C103 |
Typ | Niobium-Hafnium-Titanium Alloy Powder |
Composition (wt.%) | Nb Bal., Hf 9.0-11.0, Ti 0.7-1.3 |
Produktionsmetod | Plasma Spheroidization (PS), Processed (PREP) |
Partikelmorfologi | Sfärisk |
Partikelstorleksintervall | Customizable (Typically 45-150 µm for AM) |
Skenbar densitet | ~6.6 g/cm³ |
Viktiga egenskaper | High Melting Point, Exceptional High-Temperature Strength, Excellent Corrosion Resistance, Desirable Nuclear Properties |
Tillämpningar | Aerospace, Nuclear, Chemical Processing, High-Temperature Furnaces |
Table 1: Technical Specifications of C103 Niobium Alloy Powder
Applications: Where C103 Excels
C103’s unique combination of properties makes it suitable for a wide range of demanding applications:
1. Aerospace:
- Rocket Engine Components: C103’s high-temperature strength and resistance to oxidation make it suitable for components in rocket engines, such as combustion chambers, nozzles, and thrust vectoring systems.
- Hypersonic Vehicles: As hypersonic vehicles experience extreme temperatures during atmospheric re-entry, C103’s ability to maintain its strength and resist oxidation makes it a candidate material for leading edges, nose cones, and other critical components.
2. Nuclear:
- Nuclear Reactor Components: C103’s low thermal neutron cross-section, high-temperature strength, and corrosion resistance make it suitable for components in nuclear reactors, such as cladding for fuel rods, control rods, and structural components.
- Ion Thrusters: C103 is used in the construction of ion thrusters, a type of electric propulsion system used for spacecraft propulsion, due to its ability to withstand the high temperatures and corrosive environments encountered in these systems.
3. Chemical Processing:
- High-Temperature Furnaces: C103’s high melting point and resistance to oxidation make it suitable for components in high-temperature furnaces used in various industrial processes, such as metal refining and ceramic production.
- Chemical Reactors: C103’s corrosion resistance makes it valuable for components in chemical reactors handling corrosive chemicals at elevated temperatures.
4. Other Applications:
- Medicinska implantat: In specific cases, C103’s biocompatibility and corrosion resistance make it a potential material for certain medical implants, particularly those requiring high strength and resistance to wear.
- High-Intensity Lighting: C103 is used in high-intensity discharge lamps, such as those used in stadium lighting and film projectors, due to its ability to withstand the high temperatures generated by these lamps.
Comparing Xmetto with Other Niobium Alloy Powder Suppliers
Leverantör | Plats | Prisintervall (USD/kg) | Specialiteter |
---|---|---|---|
Xmetto | Kina | 1200 – 2400 | Competitive pricing, focus on customer collaboration, expertise in powder metallurgy |
ATI Specialmaterial | USA | 1800 – 3600 | Wide range of refractory metal powders, high purity, stringent quality control |
Plansee | Österrike | 1500 – 3000 | Focus on high-performance applications, expertise in powder processing and component manufacturing |
Materion | USA | 1600 – 3200 | Wide range of advanced materials, including sputtering targets and specialty powders |
Table 2: Comparison of Xmetto with Other Niobium Alloy Powder Suppliers
Advantages and Disadvantages: A Balanced Perspective
Fördelar | Nackdelar |
---|---|
Exceptional High-Temperature Strength and Creep Resistance: C103 maintains its strength at temperatures where most metals would soften or deform, making it suitable for extreme environments. | High Cost Compared to Conventional Alloys: The specialized processing and relatively low demand for C103 contribute to its higher cost compared to more common alloys. |
Utmärkt korrosionsbeständighet: The formation of a stable and protective oxide layer provides C103 with exceptional resistance to oxidation and corrosion in various environments. | Begränsad tillgänglighet: C103 is a specialized material with limited production and availability compared to more common alloys. |
Desirable Nuclear Properties: Its low thermal neutron cross-section makes C103 suitable for nuclear applications where neutron transparency is crucial. | Challenges in Processing and Machining: C103’s high melting point and hardness can pose challenges for processing and machining, often requiring specialized equipment and techniques. |
Biocompatibility (in Specific Applications): C103’s biocompatibility makes it a potential candidate for certain medical implants, particularly those requiring high strength and wear resistance. | Susceptibility to Embrittlement: C103 can be susceptible to embrittlement at very low temperatures, limiting its use in cryogenic applications. |
Table 3: Advantages and Disadvantages of C103 Niobium Alloy Powder
Related Insights: Exploring the Frontiers of Niobium Alloy Research
- Developing Advanced Processing Techniques: Researchers are exploring advanced processing techniques, such as additive manufacturing and field-assisted sintering, to further enhance the properties and performance of C103 components.
- Investigating the Effects of Alloying Additions: Research is ongoing to investigate the effects of adding other elements, such as tungsten or molybdenum, to further improve the high-temperature strength, creep resistance, or oxidation resistance of C103.
- Exploring Applications in Emerging Technologies: C103 is being explored for potential applications in emerging technologies, such as fusion energy, advanced aerospace propulsion systems, and high-temperature sensors.
Why Choose Xmetto for C103 Niobium Alloy Powder?
Xmetto distinguishes itself as a leading supplier of high-quality C103 niobium alloy powder due to:
- Commitment to Quality: Xmetto maintains rigorous quality control measures throughout the production process, ensuring the consistency and reliability of its C103 powder.
- Teknisk expertis: Xmetto’s team possesses in-depth knowledge of powder metallurgy and material science, providing valuable technical support to customers.
- Konkurrenskraftig prissättning: Xmetto offers C103 powder at competitive prices, making this advanced material more accessible for various applications.
- Customer-Centric Approach: Xmetto prioritizes customer satisfaction, building strong relationships based on trust, responsiveness, and a deep understanding of customer needs.
Vanliga frågor och svar (FAQ)
1. What is the minimum order quantity for C103 niobium alloy powder from Xmetto?
Xmetto strives to accommodate various order sizes. The minimum order quantity for C103 powder can vary depending on the specific product specifications and stock availability.
2. Can Xmetto provide material certification for their C103 powder?
Yes, Xmetto provides material certification documentation upon request, ensuring the traceability and quality of its C103 powder.
3. Does Xmetto offer guidance on processing C103 powder?
Yes, Xmetto’s technical team can provide guidance on processing C103 powder, including recommendations for powder metallurgy parameters, additive manufacturing settings, and other relevant processing techniques.
4. What is the shelf life of C103 powder, and what are the recommended storage conditions?
C103 powder has a long shelf life if stored properly. It is recommended to store the powder in a cool, dry environment, preferably under an inert atmosphere (e.g., argon or nitrogen) to prevent oxidation and moisture absorption.
5. Does Xmetto offer other niobium-based alloy powders?
Yes, in addition to C103, Xmetto offers a range of other niobium-based alloy powders with varying compositions and properties to meet diverse application requirements.