Manufacturing Processes for FeCoNiCrMn Powder
FeCoNiCrMn powder, a high-entropy alloy (HEA), offers unique properties that make it desirable for various applications. The manufacturing process significantly influences the powder’s microstructure, particle size distribution, and overall properties.
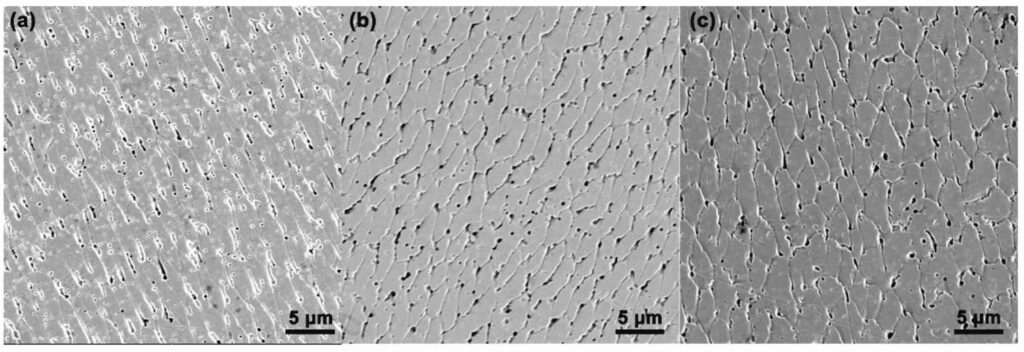
Mekanisk legering (MA)
Mechanical alloying is a widely used method for producing FeCoNiCrMn powder. It involves subjecting a mixture of elemental powders to repeated impact and deformation under controlled conditions. This process results in a fine-grained, homogeneous powder with a uniform distribution of elements. MA is particularly suitable for producing HEAs due to its ability to overcome the sluggish diffusion kinetics of multi-component alloys.
Gas-Phase Condensation (GPC)
GPC is another effective method for producing FeCoNiCrMn powder. In this process, a vaporized mixture of the constituent elements is rapidly cooled, leading to the formation of tiny particles. GPC offers precise control over particle size and morphology, making it suitable for producing powders with specific properties.
Elektroplätering
Electroplating is a versatile technique that can be used to produce FeCoNiCrMn powder. By depositing the alloy onto a suitable substrate, followed by detachment and grinding, it is possible to obtain powders with controlled particle size and composition. Electroplating is particularly useful for producing powders with complex shapes or coatings.
Andra metoder
- This method involves spraying a molten metal or alloy onto a substrate, resulting in the formation of a powder layer.
- In this process, a molten metal or alloy is atomized by water, producing fine powder particles.
- A laser beam is used to vaporize a target material, creating a plume of particles that can be collected as powder.
Comparison of Manufacturing Processes for FeCoNiCrMn Powder
Characterization of FeCoNiCrMn powder is essential for understanding its microstructure, properties, and suitability for various applications. A comprehensive characterization involves analyzing its particle size distribution, morphology, chemical composition, and physical properties. Particle size distribution is a critical parameter that influences the powder’s behavior during processing and its performance in applications. It can be determined using techniques such as: The morphology of FeCoNiCrMn powder particles, including their shape and surface characteristics, can significantly affect their properties. It can be examined using: Accurate determination of the chemical composition of FeCoNiCrMn powder is crucial for ensuring that it meets the desired specifications. This can be achieved using: A variety of physical properties, including density, magnetic properties, and electrical conductivity, can be measured to assess the suitability of FeCoNiCrMn powder for different applications. Common techniques include: FeCoNiCrMn powder, a high-entropy alloy (HEA), exhibits unique mechanical properties that make it a promising material for various applications. These properties are influenced by factors such as particle size, microstructure, and processing conditions. FeCoNiCrMn powder typically exhibits high hardness and strength due to its fine-grained microstructure and the formation of a solid-solution phase. This combination results in a dense, robust material with excellent resistance to wear and abrasion. While FeCoNiCrMn powder generally exhibits good ductility, its toughness can vary depending on the specific composition and processing conditions. The addition of elements like carbon or nitrogen can enhance the toughness by promoting the formation of fine-grained carbides or nitrides. FeCoNiCrMn powder has shown promising fatigue resistance, making it a potential candidate for applications subjected to cyclic loading. The fine-grained microstructure and the presence of multiple alloying elements contribute to its fatigue strength. The high hardness and strength of FeCoNiCrMn powder make it highly resistant to wear. This property is particularly beneficial for applications such as cutting tools, bearings, and protective coatings. FeCoNiCrMn powder, a high-entropy alloy (HEA), offers excellent corrosion resistance due to the presence of multiple alloying elements. The synergistic effect of these elements creates a protective oxide layer on the surface of the powder, which acts as a barrier against corrosive environments. The corrosion behavior of FeCoNiCrMn powder is influenced by various factors, including the environment, pH, temperature, and the presence of specific ions. Common corrosion mechanisms include: FeCoNiCrMn powder exhibits excellent corrosion resistance in a wide range of environments, including: To further enhance the corrosion resistance of FeCoNiCrMn powder, various protective coatings and treatments can be applied, such as: FeCoNiCrMn powder, a high-entropy alloy (HEA), offers unique properties that make it suitable for a wide range of applications. Its excellent mechanical properties, corrosion resistance, and high-temperature performance make it a promising material for various industries. FeCoNiCrMn powder is increasingly used in additive manufacturing (AM) processes, such as 3D printing. Its excellent printability and mechanical properties make it a suitable material for producing complex components with intricate geometries. AM of FeCoNiCrMn powder enables the fabrication of custom parts with tailored properties, reducing lead times and minimizing material waste. The magnetic properties of FeCoNiCrMn powder can be tailored by adjusting its composition and microstructure. It has potential applications in magnetic recording devices, sensors, and actuators. The alloy’s high saturation magnetization and low coercivity make it suitable for high-density data storage and magnetic field sensing. FeCoNiCrMn powder can be used to produce electrical components such as contacts, connectors, and conductors. Its excellent electrical conductivity and corrosion resistance make it a reliable material for these applications. Additionally, the alloy’s high-temperature performance makes it suitable for use in harsh environments. FeCoNiCrMn powder has shown promise in biomedical applications, including implants, stents, and surgical tools. Its biocompatibility and corrosion resistance make it a suitable material for these applications. The alloy’s mechanical properties, such as its strength and fatigue resistance, are also important for ensuring the long-term performance of implants. FeCoNiCrMn powder has potential applications in various other industries, including:
Process
Fördelar
Nackdelar
Mekanisk legering
Produces fine-grained, homogeneous powder.
Can be time-consuming and energy-intensive.
Gas-Phase Condensation
Precise control over particle size and morphology.
Requires specialized equipment and complex process control.
Elektroplätering
Can produce powders with complex shapes or coatings.
Limited to producing powders on a substrate.
Plasmasprutning
High production rates.
Can produce powders with a wide particle size distribution.
Atomisering av vatten
Simple process.
Limited control over particle size and morphology.
Laser Ablation
Precise control over particle composition.
Low production rates and high cost.
Characterization of FeCoNiCrMn Powder
Fördelning av partikelstorlek
Morfologi
Kemisk sammansättning
Fysikaliska egenskaper
Characterization Techniques for FeCoNiCrMn Powder
Fastighet
Teknik
Fördelning av partikelstorlek
Sieving, laser diffraction, dynamic light scattering
Morfologi
SEM, TEM, AFM
Kemisk sammansättning
ICP-OES, XRF, EDX
Täthet
Pyknometri
Magnetic properties
Magnetometry
Elektrisk ledningsförmåga
Conductivity measurement
Mechanical Properties of FeCoNiCrMn Powder
Hardness and Strength
Ductility and Toughness
Utmattningshållfasthet
Slitstyrka
Mechanical Properties of FeCoNiCrMn Powder
Fastighet
Typiska värden
Hårdhet
300-400 HV
Draghållfasthet
1000-1200 MPa
Sträckgräns
800-1000 MPa
Duktilitet
10-20% elongation
Tålighet
50-70 J/m²
Utmattningshållfasthet
300-400 MPa
Slitstyrka
Utmärkt
Corrosion Resistance of FeCoNiCrMn Powder
Corrosion Mechanisms
Corrosion Behavior in Different Environments
Protective Coatings and Treatments
Corrosion Resistance of FeCoNiCrMn Powder in Different Environments
Miljö
Motståndskraft mot korrosion
Seawater
Utmärkt
Acidic media
Bra
Alkaline solutions
Bra
Oxidizing environments
Utmärkt
Reducing environments
Bra
Applications of FeCoNiCrMn Powder
Additiv tillverkning
Magnetic Materials
Electrical Components
Biomedicinska tillämpningar
Other Potential Uses
Applications of FeCoNiCrMn Powder
Tillämpning
Fördelar
Additiv tillverkning
Complex component fabrication, reduced lead times, minimized material waste
Magnetiska material
High-density data storage, magnetic field sensing
Elektriska komponenter
Excellent conductivity, corrosion resistance, high-temperature performance
Biomedical applications
Biocompatibility, corrosion resistance, mechanical properties
Flyg- och rymdindustrin
Lightweight, high-strength components
Fordon
Durability, corrosion resistance
Energi
High-temperature performance, electrical conductivity
Kemisk bearbetning
Korrosionsbeständighet
If you would like to know more about the wide range of High Entropy Alloy Powder, please click on the names in the table: