Metal powder is revolutionizing the tooling industry, offering a new dimension in tool design and manufacturing. But what exactly is metal powder, and how is it used to create tooling? This comprehensive guide delves deep into the world of metallpulver för verktyg, exploring its applications, benefits, limitations, and various types available. Buckle up and get ready to explore the fascinating world of metal additive manufacturing!
An Overview of Metal Powder for Tooling
Imagine creating complex tooling with intricate designs and exceptional properties – that’s the power of metal powder for tooling. This innovative approach utilizes fine metal particles to build three-dimensional tools through additive manufacturing techniques like 3D printing. Think of it like using a high-tech inkjet printer, but instead of ink, it deposits layers of metal powder to create a functional tool.
Metal powder for tooling offers a multitude of advantages over traditional subtractive manufacturing methods like machining. Here’s a quick glimpse of what makes it so exciting:
- Designfrihet: Unleash your creativity! Complex geometries and internal channels, once deemed impossible with traditional methods, become achievable with metal powder.
- Lättvikt: Metal powder tools can be lighter than their solid counterparts, reducing weight on machinery and improving overall efficiency.
- Materialeffektivitet: Since metal powder is used additively, there’s minimal waste compared to subtractive machining, making it a more sustainable option.
- Performance Optimization: Tailor properties by combining different metal powders. Need a super wear-resistant tool? Use a tungsten-based powder!
- Lead Time Reduction: Complex tools can be created much faster with additive manufacturing, accelerating your production cycle.
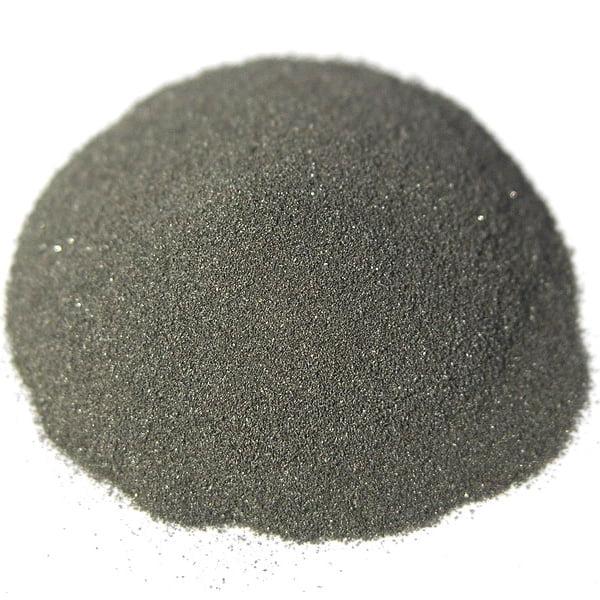
Metal Powders for Tooling: A Diverse Palette
Världen av metallpulver för verktyg boasts a diverse range of materials, each with its unique properties and applications. Here’s a closer look at ten of the most popular options:
1. Stainless Steel Powders (316L, 17-4PH):
- Sammansättning: Iron, chromium, nickel (316L), copper (17-4PH)
- Egenskaper: Excellent corrosion resistance, good strength and hardness (especially 17-4PH)
- Applikationer: Molds, punches, dies, jigs and fixtures for various applications
2. Tool Steel Powders (H13, M2):
- Sammansättning: Iron, carbon, chromium, molybdenum, vanadium (varying amounts)
- Egenskaper: Exceptional wear resistance, high hardness, good heat resistance (especially H13)
- Applikationer: Cutting tools, punches, dies, forming tools for metalworking applications
3. Aluminum Powders:
- Sammansättning: Predominantly aluminum, with trace amounts of other elements
- Egenskaper: Lightweight, good thermal conductivity, machinable
- Applikationer: Prototype tools, lightweight tooling components, heat sinks
4. Nickel Alloys (Inconel 625, Inconel 718):
- Sammansättning: Nickel, chromium, molybdenum (varying amounts)
- Egenskaper: Excellent high-temperature strength, corrosion resistance, good wear resistance
- Applikationer: Molds for hot working applications, tooling for harsh environments
5. Kopparpulver:
- Sammansättning: Predominantly copper, with trace amounts of other elements
- Egenskaper: Excellent thermal conductivity, good electrical conductivity, soft and ductile
- Applikationer: Heat sinks, electrodes for welding and brazing, conductive tooling components
6. Tungsten Carbide Powders:
- Sammansättning: Tungsten carbide (WC) particles with a metal binder (cobalt or nickel)
- Egenskaper: Exceptional wear resistance, unmatched hardness
- Applikationer: Cutting tools, wear pads, dies for high-abrasive applications
7. Cobalt Chrome Powders:
- Sammansättning: Cobalt and chromium alloy
- Egenskaper: Excellent wear resistance, high strength, good biocompatibility
- Applikationer: Medical and dental tooling, wear parts, cutting tools
8. Titanium Powders:
- Sammansättning: Predominantly titanium, with trace amounts of other elements
- Egenskaper: High strength-to-weight ratio, good corrosion resistance, biocompatible
- Applikationer: Aerospace tooling, medical implants (depending on the grade), lightweight tooling components
9. Maraging Steel Powders:
- Sammansättning: Iron, nickel, molybdenum, with low carbon content
- Egenskaper: High strength, good toughness, excellent dimensional stability after heat treatment
- Applikationer: Complex tooling requiring high strength and dimensional accuracy
10. Refractory Metal Powders (Molybdenum, Tantalum):
- Sammansättning: Molybdenum or tantalum
- Egenskaper: Extremely high melting points, good strength at high temperatures
- Applikationer: Molds for casting high-temperature materials, tooling for furnace applications
Välja rätt metallpulver
Selecting the ideal metal powder hinges on your specific tooling needs. Here are some key factors to consider:
- Ansökan: What is the primary function of the tool? Cutting, forming, molding, or something else entirely?
- Nödvändiga egenskaper: Do you prioritize wear resistance, strength, thermal conductivity, or a combination?
- Efterbearbetning: Will the tool require heat treatment or other finishing techniques? Different powders respond differently to these processes.
- Budget: Metal powders vary in cost, with exotic materials like titanium and nickel alloys commanding a premium.
Ytterligare överväganden:
Beyond the core properties, some additional factors can influence your choice of metal powder.
- Partikelstorlek och fördelning: The size and distribution of the metal powder particles significantly impact the final tool’s surface finish, mechanical properties, and printability. Finer powders generally produce smoother finishes but can be more challenging to print.
- Flytbarhet: The powder’s ability to flow freely is crucial for even deposition during the additive manufacturing process.
- Sintringsbeteende: Sintering is a heat treatment process that bonds the metal particles together. The powder’s sintering behavior determines the final strength and density of the tool.
För- och nackdelar med Metal Powder for Tooling
Every technology has its advantages and limitations, and metal powder for tooling is no exception. Let’s delve into both sides of the coin:
Fördelar:
- Designfrihet: Unleash your imagination! Complex geometries and internal channels become achievable, pushing the boundaries of tool design.
- Lättvikt: Metal powder tools can be lighter than their solid counterparts, reducing weight on machinery and improving overall efficiency.
- Materialeffektivitet: Since metal powder is used additively, there’s minimal waste compared to subtractive machining, making it a more sustainable option.
- Performance Optimization: Tailor properties by combining different metal powders. Need a super wear-resistant tool? Use a tungsten-based powder!
- Lead Time Reduction: Complex tools can be created much faster with additive manufacturing, accelerating your production cycle.
- Consolidation of Parts: Design complex tools with multiple functionalities, reducing the need for separate components.
Nackdelar:
- Kostnad: Metal powder additive manufacturing can be more expensive than traditional machining for certain applications, especially for high-volume production runs.
- Ytfinish: While improving, the surface finish of metal powder tools can be rougher compared to machined tools, requiring additional post-processing in some cases.
- Begränsat materialval: While the range of metal powders is expanding, it’s still not as vast as the options available for traditional machining.
- Part Size Limitations: Current additive manufacturing machines have limitations on the size of tools they can produce.
- Process Qualification: For critical applications, metal powder tooling may require additional qualification procedures to ensure performance and safety.

Tillämpningar av Metal Powder for Tooling
Metal powder for tooling is rapidly transforming various industries. Here are some captivating examples:
- Aerospace: Complex, lightweight engine components and heat sinks are being created using titanium and aluminum powders.
- Fordon: Prototypes for car parts, molds for casting complex components, and lightweight tooling for assembly lines are benefiting from metal additive manufacturing.
- Medicinsk: Customizable implants, surgical tools, and even dental prosthetics are being produced with biocompatible metal powders like cobalt chrome and titanium.
- Konsumentvaror: Complex molds for creating intricate jewelry designs, lightweight components for electronics, and even customized sporting goods are finding applications in metal powder tooling.
The Future of Metal Powder for Tooling
The future of metal powder for tooling is bright. As technology advances, we can expect:
- Minskade kostnader: Advancements in additive manufacturing technology and wider adoption are likely to bring down the cost of metal powder tooling.
- Expanded Material Selection: New metal powders with unique properties will emerge, offering even greater design flexibility.
- Förbättrad ytfinish: Advancements in printing techniques and post-processing methods will lead to smoother surface finishes for metal powder tools.
- Larger Build Volumes: Additive manufacturing machines with larger build volumes will enable the creation of even bigger and more complex tools.
- Hybrid Manufacturing: A combination of traditional and additive manufacturing techniques will become more prevalent, leveraging the strengths of both approaches.

Vanliga frågor
Metal powder for tooling is an exciting technology with vast potential. But navigating this new frontier can raise questions. This FAQ section tackles some of the most common queries to empower you on your metal powder tooling journey.
Q: Is metal powder tooling strong enough for real-world applications?
A: Absolutely! Metal powder tools can achieve exceptional strength depending on the chosen material. Tool steel powders, for instance, can deliver outstanding strength and wear resistance, making them suitable for demanding applications. The key lies in selecting the right metal powder for the specific job.
Q: How does the cost of metal powder tooling compare to traditional methods?
A: The cost equation can be complex. For simple tools and high-volume production runs, traditional machining might still be more economical. However, metal powder tooling shines in several scenarios:
- Complex geometries: The additive nature of 3D printing eliminates the need for complex machining processes, potentially offsetting the higher material cost of metal powders.
- Low-volume production: With minimal setup costs and faster turnaround times, metal powder tooling can be more cost-effective for producing small batches of tools.
- Lättvikt: The ability to create lightweight tools with metal powders can lead to significant cost savings in applications where weight reduction is crucial.
Q: What kind of 3D printer is needed for metal powder tooling?
A: Metal powder additive manufacturing utilizes specialized machines unlike those used for hobbyist-grade plastic printing. These machines employ techniques like laser melting or electron beam melting to fuse the metal powder particles layer by layer. While the technology is evolving rapidly, these machines typically require a significant investment and expertise to operate effectively.
Q: Can I use metal powder to repair existing tools?
A: Metal powder has the potential for tool repair applications. Techniques like laser cladding can be used to deposit metal powder onto a worn area of a tool, restoring its functionality. However, the feasibility and cost-effectiveness depend on the extent of damage and the type of tool.
Q: Where can I source metal powder for tooling?
A: Several reputable suppliers specialize in metal powders for additive manufacturing. These suppliers offer various materials, particle sizes, and grades to cater to diverse tooling needs. Always ensure you procure metal powders from reliable sources that meet industry standards for quality and safety.