Properties of CuAlMn Powder
CuAlMn powder is a ternary alloy composed of copper, aluminum, and manganese. Its unique composition and microstructure contribute to a range of desirable properties, making it a versatile material for various applications.
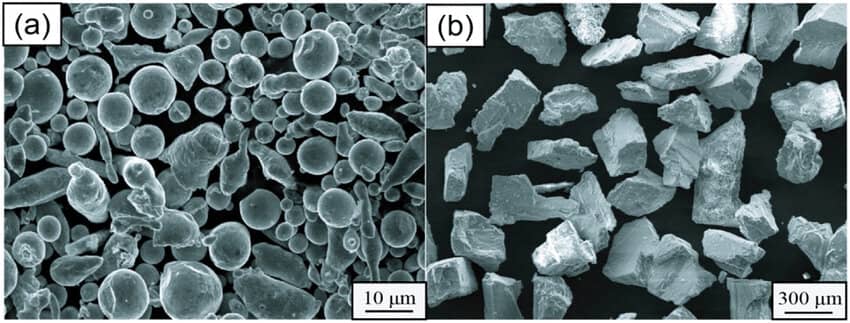
Fiziksel Özellikler
- CuAlMn powder typically exhibits a density in the range of 7.8-8.2 g/cm³.
- The particle size distribution can vary depending on the manufacturing method, but it commonly ranges from a few micrometers to several tens of micrometers.
- The particles can have different morphologies, such as spherical, irregular, or dendritic, which can influence their properties and behavior.
Kimyasal Bileşim
Element | Tipik Bileşim (%) |
---|---|
Bakır (Cu) | 60-70 |
Alüminyum (Al) | 20-30 |
Manganez (Mn) | 5-10 |
Other elements (e.g., Fe, Si) | Trace amounts |
Mekanik Özellikler
- CuAlMn powder is generally harder than pure copper, exhibiting a hardness in the range of 100-150 Brinell hardness units.
- The tensile strength of CuAlMn powder can vary depending on the processing conditions and composition, but it typically falls within the range of 300-500 MPa.
- CuAlMn powder is generally ductile, allowing for good formability and machinability.
Termal Özellikler
- The melting point of CuAlMn powder is typically higher than that of pure copper, ranging from 900-1000°C.
- CuAlMn powder exhibits moderate thermal conductivity compared to pure copper, making it suitable for applications where good heat dissipation is required.
Manyetik Özellikler
- CuAlMn powder is typically paramagnetic, meaning it is weakly attracted to a magnetic field. However, the magnetic properties can be influenced by the composition and microstructure.
The properties of CuAlMn powder can vary depending on factors such as manufacturing method, composition, and processing conditions. It’s essential to consult specific material data sheets or conduct testing to determine the exact properties for a particular application.
[Insert relevant table data here, if available]
For instance, a table could provide data on the hardness, tensile strength, and ductility of CuAlMn powder under different processing conditions or compositions.
Manufacturing Processes for CuAlMn Powder
CuAlMn powder can be produced through various manufacturing processes, each with its own advantages and limitations. The choice of manufacturing method often depends on factors such as desired particle size, purity, and cost.
Powder Metallurgy Techniques
- This process involves melting the alloy and then spraying it into a cooling chamber, where it solidifies into small droplets that cool and solidify into powder particles. Atomization can produce powders with a wide range of particle sizes and morphologies.
- In this process, elemental powders of copper, aluminum, and manganese are mixed together and subjected to intense mechanical deformation, which results in the formation of a fine, homogeneous powder. Mechanical alloying can produce powders with a controlled microstructure and composition.
Elektrodepozisyon
- In this process, a CuAlMn alloy is deposited onto a sacrificial substrate from an electrolytic solution containing copper, aluminum, and manganese ions. The deposited alloy is then removed from the substrate and ground or milled into powder. Electrodeposition can produce powders with a high purity and controlled composition.
Other Manufacturing Methods
- CVD involves the deposition of a CuAlMn alloy from a gaseous phase onto a heated substrate. This method can produce powders with a high purity and controlled morphology.
- In this method, a sol (a colloidal suspension) containing copper, aluminum, and manganese precursors is formed and then converted into a gel. The gel is then dried and calcined to produce CuAlMn powder. Sol-gel synthesis can produce powders with a controlled particle size and microstructure.
[Insert relevant table data here, if available]
For instance, a table could compare the particle size distribution, purity, and cost of CuAlMn powder produced by different manufacturing methods.
The choice of manufacturing method for CuAlMn powder often depends on the specific requirements of the application. For example, if high purity and controlled particle size are essential, electrodeposition or CVD may be preferred. If a wider range of particle sizes and morphologies are acceptable, atomization or mechanical alloying may be more suitable.
Applications of CuAlMn Powder
CuAlMn powder is a versatile material with a wide range of applications due to its unique combination of properties. Its high strength, good conductivity, and corrosion resistance make it suitable for various industries.
Structural Materials
- CuAlMn powder is used to produce components such as aircraft landing gear, engine parts, and structural panels due to its high strength-to-weight ratio and fatigue resistance.
- CuAlMn powder is used to manufacture components such as brake systems, engine parts, and transmission gears, offering improved wear resistance and durability.
- CuAlMn powder is also used in other structural applications, including construction materials, machinery components, and tooling.
Electronic Materials
- CuAlMn powder is used as a conductor material in electrical components such as wires, cables, and connectors due to its good electrical conductivity.
- CuAlMn powder is used to produce electrical contacts for switches, relays, and other devices, offering excellent wear resistance and low contact resistance.
- CuAlMn powder is used as a material for electrodes in batteries and fuel cells due to its good electrical conductivity and corrosion resistance.
Manyetik Malzemeler
- CuAlMn powder is used to produce soft magnetic cores for transformers, inductors, and other magnetic devices due to its low magnetic loss and high permeability.
Catalytic Materials
- CuAlMn powder is used as a catalyst in various chemical reactions, including hydrogenation, dehydrogenation, and oxidation.
Diğer Uygulamalar
- CuAlMn powder is used to produce protective coatings for surfaces, offering improved wear resistance, corrosion resistance, and thermal conductivity.
- CuAlMn powder is used as a reinforcement material in composite materials, improving their mechanical properties and electrical conductivity.
[Insert relevant table data here, if available]
For instance, a table could compare the properties of CuAlMn powder to other materials commonly used in specific applications.
The specific application of CuAlMn powder depends on its composition, processing method, and desired properties. By carefully selecting the appropriate manufacturing process and composition, CuAlMn powder can be tailored to meet the requirements of various industries and applications.
Challenges and Future Directions
Despite its numerous advantages, the development and application of CuAlMn powder face several challenges. Addressing these challenges and exploring future research directions will be crucial for further advancing the use of this material.
Zorluklar
- The manufacturing of CuAlMn powder can be relatively expensive, especially for high-purity and specialized grades. Reducing manufacturing costs is essential to make CuAlMn powder more competitive in the market.
- Ensuring consistent properties and reproducibility of CuAlMn powder can be challenging due to variations in manufacturing processes and raw materials. Developing standardized manufacturing methods and quality control measures is crucial.
- The recycling and sustainable production of CuAlMn powder are important considerations. Developing efficient recycling processes and exploring environmentally friendly manufacturing methods will be essential for promoting its long-term use.
Future Directions
- Exploring new manufacturing techniques such as additive manufacturing (3D printing) and advanced powder metallurgy processes can improve the properties, cost-effectiveness, and sustainability of CuAlMn powder.
- Investigating new alloy compositions incorporating additional elements can further enhance the properties of CuAlMn powder for specific applications.
- Developing methods to functionalize CuAlMn powder with specific properties, such as improved corrosion resistance, conductivity, or catalytic activity, will expand its potential applications.
- Advancing characterization techniques and developing accurate models to predict the properties and behavior of CuAlMn powder will aid in its design and optimization.
- Exploring the integration of CuAlMn powder into advanced materials such as composites, coatings, and functional materials will open up new opportunities for its application.
For instance, a table could compare the manufacturing costs, recycling rates, and sustainability metrics of different CuAlMn powder production methods.
Addressing these challenges and pursuing future research directions will be essential for realizing the full potential of CuAlMn powder and ensuring its continued development and application in various industries.
CuAlMn Powder FAQs: Addressing Key Concerns for Potential Users
Here are five FAQs tailored for potential users of CuAlMn powder, focusing on their likely concerns and information needs:
1. What are the key characteristics of CuAlMn powder that make it suitable for electrical resistance applications?
CuAlMn powder offers a unique combination of high electrical resistivity, good mechanical strength, and excellent resistance to oxidation at elevated temperatures. This makes it highly suitable for applications like resistance welding electrodes, electrical resistance heating elements, and precision resistors where controlled electrical resistance and thermal stability are crucial.
2. How does the addition of manganese and aluminum influence the properties of CuAlMn powder?
Manganese significantly increases the electrical resistivity of the copper alloy while maintaining good ductility. Aluminum enhances the material’s strength, corrosion resistance, and high-temperature stability, further expanding its suitability for demanding electrical resistance applications.
3. What are the typical processing methods used for CuAlMn powder?
CuAlMn powder can be processed using conventional powder metallurgy techniques, including pressing and sintering. The powder is compacted into the desired shape and then sintered at elevated temperatures in a controlled atmosphere to achieve the desired density and electrical properties.
4. What factors influence the final electrical resistivity of sintered CuAlMn components?
The final electrical resistivity of sintered CuAlMn components is influenced by factors such as the alloy composition, powder particle size and distribution, sintering temperature, and sintering time. Precise control over these parameters is essential for achieving the desired electrical properties.
5. What technical support does Xmetto provide to ensure the successful implementation of CuAlMn powder?
Xmetto offers comprehensive technical support, including detailed material specifications, processing guidelines, and expert advice on powder selection, sintering parameters, and achieving desired electrical properties. We are committed to assisting our customers in optimizing the use of CuAlMn powder in their specific applications.