Introduction: Engineering Solutions for Extreme Demands
In the relentless pursuit of materials that can withstand extreme temperatures, resist wear and tear, and deliver exceptional performance, cobalt-based powders have emerged as champions of innovation. These remarkable materials, prized for their hardness, strength, and corrosion resistance, are driving advancements in industries ranging from aerospace to energy production. This comprehensive exploration delves into the world of cobalt-based powders, unraveling their properties, processing techniques, diverse applications, and competitive landscape. Join us as we uncover why these powders are essential ingredients in shaping the future of high-performance materials.
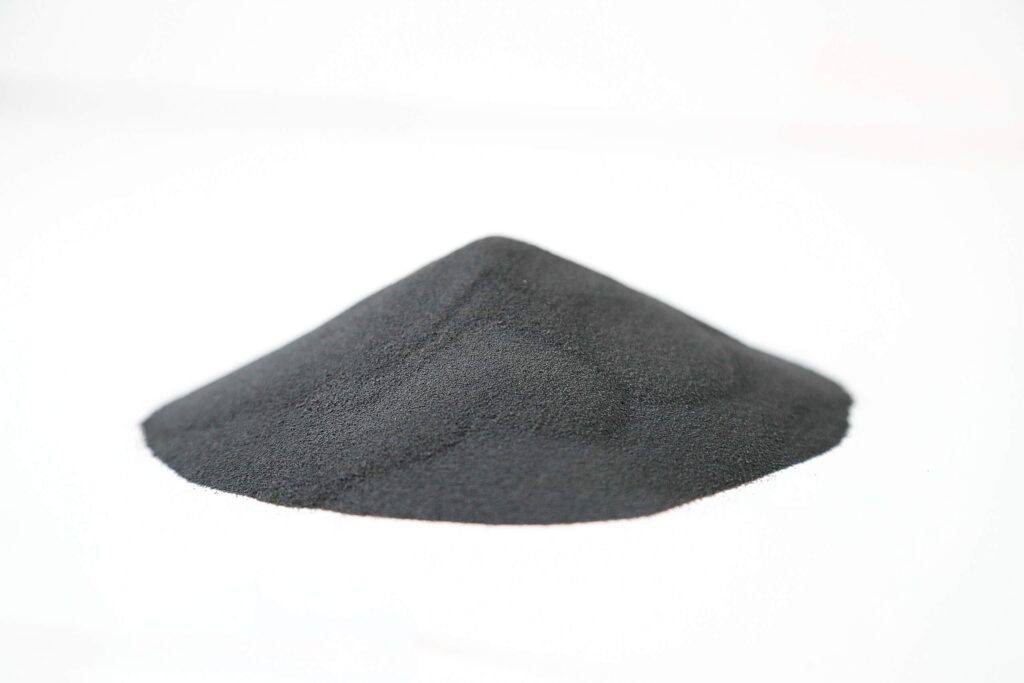
Understanding Cobalt Based Powders: A Closer Look
What are Cobalt Based Powders?
Cobalt-based powders are finely divided metallic materials where cobalt (Co) forms the primary constituent, often alloyed with elements like chromium (Cr), tungsten (W), nickel (Ni), molybdenum (Mo), and iron (Fe). These meticulously engineered alloys inherit cobalt’s inherent strength and corrosion resistance, further amplified by the synergistic effects of the additional elements. This unique combination of properties makes cobalt-based powders ideal for applications demanding exceptional wear resistance, high-temperature strength, and resistance to harsh environments like oxidation, abrasion, and erosion.
The powder form of these alloys offers significant advantages over traditional casting methods, allowing for greater control over composition and microstructure, ultimately leading to enhanced performance and extended component lifespan.
Working Principle: The Science Behind the Strength
The remarkable properties of cobalt-based powders arise from a combination of factors:
- Katı Çözelti Güçlendirme: The addition of alloying elements like chromium, tungsten, and molybdenum into the cobalt matrix creates solid solutions. The atoms of these alloying elements occupy positions within the cobalt crystal lattice, disrupting its regular arrangement. This makes it more difficult for dislocations (defects in the crystal structure) to move, thus increasing the alloy’s strength and hardness.
- Carbide Formation: Some alloying elements, like chromium and tungsten, can form hard and wear-resistant carbides within the cobalt matrix. These carbides act as reinforcing particles, hindering the movement of dislocations and significantly enhancing wear resistance, particularly at elevated temperatures.
- Grain Refinement: The powder metallurgy process used to manufacture cobalt-based components often results in a finer and more uniform grain structure compared to traditional casting methods. This finer grain size contributes to improved mechanical properties, including higher strength and toughness.
Processing of Cobalt Based Powders: From Powder to Performance
Cobalt-based powders are typically processed using powder metallurgy techniques, offering precise control over composition and microstructure:
- Toz Üretimi: Atomization is a common method for producing cobalt-based powders. The alloy is melted and then atomized into fine droplets using a high-pressure gas stream (often argon or nitrogen). The droplets rapidly solidify into powder particles, resulting in a powder with a controlled particle size distribution. Other methods like water atomization and centrifugal atomization are also employed.
- Powder Conditioning: The powder may undergo additional processing steps like sieving, screening, and blending to achieve the desired particle size distribution and ensure homogeneity. This ensures consistent flowability and packing density during subsequent processing steps.
- Compaction: The powder is then compacted into the desired shape using a die and high pressure. This densifies the powder and forms a “green compact” that possesses sufficient strength for handling but remains porous. The compaction pressure is carefully controlled to achieve the required green density and minimize the formation of defects.
- Sinterleme: The green compact is heated in a controlled atmosphere, often under vacuum or inert gas, to a temperature below the alloy’s melting point. This process, known as sintering, allows the powder particles to bond through diffusion, resulting in a dense and solid component with the desired mechanical and physical properties. The sintering temperature and time are critical parameters that influence the final microstructure and properties.
- Bitiriyorum: Depending on the application, the sintered component may undergo additional finishing operations like machining, grinding, polishing, or heat treatment to achieve the required dimensional tolerances, surface finish, or enhance specific properties like hardness and wear resistance.
Classifications and Grades: Tailoring Properties for Specific Needs
Cobalt-based powders are available in a wide range of grades and classifications, each tailored to meet the specific requirements of different applications. These classifications are typically based on factors like:
- Alaşım Bileşimi: The specific percentages of cobalt and other alloying elements significantly influence the material’s properties. For example, higher chromium content generally enhances corrosion and oxidation resistance, while higher tungsten content improves wear resistance and high-temperature strength. Nickel additions can improve ductility and toughness.
- Parçacık Boyutu Dağılımı: The size distribution of the powder particles affects the powder’s flowability, packing density, and the final product’s properties. Finer powders generally result in higher densities and finer microstructures, leading to enhanced mechanical properties.
- Oksijen İçeriği: The oxygen content of the powder is carefully controlled, as it can impact the material’s mechanical properties and corrosion resistance. Lower oxygen content is generally desirable for achieving higher ductility and toughness.
- Üretim Yöntemi: The powder production method, such as gas atomization or water atomization, can influence the powder’s particle shape, size distribution, and overall quality.
Market Trends: A Growing Demand for Extreme Performance
The global market for cobalt-based powders is experiencing substantial growth, driven by the increasing demand for high-performance materials in various industries, including:
- Havacılık ve uzay: The aerospace industry relies heavily on cobalt-based alloys for critical components like turbine blades, vanes, and other engine components that must withstand extreme temperatures, high stresses, and corrosive environments. The demand for fuel-efficient aircraft is driving the development of new cobalt-based alloys with improved high-temperature capabilities.
- Tıbbi İmplantlar: Cobalt-based alloys are biocompatible and exhibit excellent wear resistance, making them suitable for medical implants like hip and knee replacements, dental implants, and bone plates. The aging population and increasing demand for orthopedic procedures are driving the growth of this market segment.
- Tooling and Wear Parts: The exceptional wear resistance and hardness of cobalt-based alloys make them ideal for cutting tools, dies, and wear parts used in demanding applications like mining, construction, and metal forming. The growing manufacturing sector and the need for increased productivity are driving the demand for high-performance tooling materials.
- Petrol ve Gaz: The oil and gas industry utilizes cobalt-based alloys for downhole drilling tools, valves, and other components exposed to harsh environments, including high temperatures, high pressures, and corrosive fluids. The exploration of unconventional oil and gas reserves is driving the demand for materials that can withstand increasingly challenging operating conditions.
- 3D Baskı: Cobalt-based alloys are gaining popularity in additive manufacturing (3D printing) due to their excellent properties and the ability to create complex geometries with high precision. This technology is opening up new possibilities for the design and manufacture of high-performance components in various industries.
Cobalt Based Powders: Properties and Specifications
Table 1: Key Properties of Common Cobalt-Based Powder Alloys
Alaşım Tanımlaması | Typical Composition (wt.%) | Yoğunluk (g/cm³) | Melting Range (°C) | Sertlik (HRC) | Çekme Dayanımı (MPa) | Uygulamalar |
---|---|---|---|---|---|---|
Stellite 6 | Co: 65, Cr: 28, W: 4, C: 1.2 | 8.3 | 1250-1350 | 58-62 | 850-1100 | Valves, seats, wear plates, bushings, bearings |
Stellite 12 | Co: 59, Cr: 29, W: 9, C: 1.8 | 8.7 | 1260-1380 | 60-64 | 900-1200 | Cutting tools, dies, nozzles, wear rings, hot work applications |
Tribaloy T-800 | Co: 40, Ni: 32, Mo: 17, Cr: 7 | 9.2 | 1350-1420 | 55-60 | 750-950 | Bearings, seals, wear rings, valve components, high-temperature applications |
MP35N | Co: 35, Ni: 35, Cr: 20, Mo: 10 | 9.2 | 1370-1425 | 45-50 | 1400-1700 | Medical implants, aerospace fasteners, marine components, high-strength applications |
Haynes 25 | Co: 50, Cr: 20, W: 15, Ni: 10, Fe: 3 | 9.1 | 1300-1400 | 48-53 | 800-1000 | Gas turbine components, chemical processing equipment, heat-resistant applications |
Not: Properties can vary depending on processing conditions and specific alloy variations.
Applications of Cobalt Based Powders: Where Performance Matters
The unique properties of cobalt-based powders make them indispensable in a wide range of applications:
- Havacılık ve uzay:
- Target Users: Aircraft engine manufacturers, aerospace component suppliers, maintenance, repair, and overhaul (MRO) companies
- Main Applications: Turbine blades and vanes for jet engines, combustion chamber components, rocket nozzles, wear-resistant coatings for bearings and gears, seals, fasteners
- Advantages in Aerospace: High-temperature strength, wear resistance, corrosion resistance, fatigue resistance
- Tıbbi:
- Target Users: Medical device manufacturers, orthopedic surgeons, dentists
- Main Applications: Hip and knee implants, dental implants, bone plates and screws, surgical instruments, stents, heart valves
- Advantages in Medical: Biocompatibility, wear resistance, corrosion resistance, strength, fatigue resistance
- Tooling and Wear Parts:
- Target Users: Tool manufacturers, machining and manufacturing industries, mining and construction companies
- Main Applications: Cutting tools for high-speed machining, dies for metal forming, wear plates and liners for mining and construction equipment, nozzles for abrasive blasting, saw tips, milling cutters, drills
- Advantages in Tooling: High hardness, wear resistance, hot hardness (retains hardness at elevated temperatures), toughness, impact resistance
- Petrol ve Gaz:
- Target Users: Oil and gas exploration and production companies, drilling contractors, equipment manufacturers
- Main Applications: Downhole drilling tools (drill bits, drill collars), valves and seats for high-pressure and corrosive environments, pumps and compressors, wellhead components, pipelines
- Advantages in Oil & Gas: Corrosion resistance, wear resistance, erosion resistance, high-temperature strength, pressure resistance
- Other Industries:
- Kimyasal İşleme: Pumps, valves, reactors, heat exchangers (corrosion resistance, wear resistance)
- Gıda İşleme: Blades, knives, wear parts (corrosion resistance, wear resistance, non-toxicity)
- Nuclear Power Generation: Control rod components, wear parts (high-temperature strength, radiation resistance)
Comparing Suppliers of Cobalt Based Powders: Finding the Right Fit
Table 2: Supplier Comparison for Cobalt Based Powders
Tedarikçi | Konum | Fiyat Aralığı (USD/kg) | Uzmanlık Alanları |
---|---|---|---|
Xmetto | Çin | $80 – $150 | Competitive pricing, wide range of alloys, customizable compositions, focus on quality and consistency |
Marangoz Teknolojisi | ABD | $120 – $200 | Premium quality, specialized grades, technical support, long history of innovation in high-performance alloys |
ATI Özel Malzemeler | ABD | $110 – $180 | High-performance alloys, research and development capabilities, focus on aerospace and demanding applications |
Erasteel | Fransa | $90 – $160 | Gas atomized powders, global distribution network, wide range of powder sizes and grades, technical expertise |
Sandvik Malzeme Teknolojisi | İsveç | $100 – $170 | High-quality powders, focus on wear-resistant and corrosion-resistant alloys, technical support and application expertise |
Not: Prices are approximate and can vary based on order volume, specific alloy, particle size distribution, and market conditions.
Advantages and Limitations of Cobalt Based Powders: A Balanced Perspective
Table 3: Advantages and Disadvantages of Cobalt Based Powders
Avantajlar | Sınırlamalar |
---|---|
Olağanüstü aşınma direnci | Relatively high cost compared to some other materials (e.g., some steel alloys) |
Yüksek sertlik ve mukavemet | Potential for cobalt leaching in certain environments (medical applications), although this is mitigated by using biocompatible grades |
Excellent corrosion resistance, including resistance to oxidation, sulfidation, and chloride attack | Processing can be challenging, requiring specialized equipment and expertise in powder metallurgy |
High-temperature strength and stability, maintaining properties at elevated temperatures | |
Biocompatibility (for select alloys), suitable for medical implants and devices | |
Can be processed using additive manufacturing (3D printing) to create complex shapes |
Related Insights: Cobalt – A Critical Material
Cobalt is classified as a critical material due to its economic importance and supply chain vulnerabilities. The Democratic Republic of Congo (DRC) currently accounts for a significant portion of global cobalt production. However, ethical concerns surrounding mining practices in the DRC have prompted efforts to diversify supply chains and explore alternative materials. Recycling of cobalt from end-of-life products is also gaining traction as a sustainable solution to meet the growing demand for this critical element.
Why Choose Xmetto for Cobalt Based Powders?
- Maliyet-Etkinlik: Xmetto offers competitively priced cobalt-based powders without compromising on quality, making us a cost-effective choice for your material needs.
- Wide Selection: We provide a comprehensive range of cobalt-based alloys, catering to diverse applications and specific performance requirements.
- Özelleştirme: Our technical team can work with you to develop customized powder compositions tailored to your unique specifications.
- Teknik Uzmanlık: Our team possesses extensive knowledge and experience in powder metallurgy and can provide guidance on material selection, processing optimization, and troubleshooting.
- Commitment to Quality: We are dedicated to providing high-quality cobalt-based powders that meet or exceed industry standards. Our rigorous quality control processes ensure consistency and reliability.
FAQs: Addressing Your Key Questions
1. What are the key factors to consider when selecting a cobalt-based powder for a specific application?
The most important factors include the required wear resistance, operating temperature, corrosion resistance, mechanical strength, and budget constraints. Our technical team can assist you in selecting the most suitable alloy based on your specific needs.
2. What are the typical particle size ranges available for cobalt-based powders?
Particle size ranges can vary depending on the alloy and manufacturing process. Common ranges include fine powders (1-10 µm), medium powders (10-45 µm), and coarse powders (45-150 µm). The choice of particle size distribution depends on factors like the desired final density, flowability requirements, and the specific powder metallurgy process being used.
3. What are the health and safety considerations when handling cobalt-based powders?
Cobalt-based powders can pose inhalation hazards. It’s crucial to implement proper dust control measures, including wearing appropriate respiratory protection (e.g., NIOSH-approved respirators), using local exhaust ventilation, and following safe handling practices. Material Safety Data Sheets (MSDS) should be consulted for specific handling and storage guidelines.
4. What is the difference between Stellite and Tribaloy alloys?
Stellite alloys are primarily cobalt-chromium-tungsten alloys known for their exceptional wear resistance, particularly at elevated temperatures. They are widely used in applications like valves, seats, and wear parts. Tribaloy alloys are cobalt-based alloys containing significant amounts of molybdenum, offering excellent wear resistance and corrosion resistance in harsh environments. They are often used in bearings, seals, and other wear applications.
5. Can cobalt-based powders be recycled?
Yes, cobalt is a highly recyclable material. Recycling processes can recover cobalt from end-of-life products like cutting tools, wear parts, and medical implants. Recycling plays a vital role in ensuring a sustainable supply of this critical material and reducing the environmental impact associated with cobalt mining.
Conclusion: Embracing the Future of High-Performance Materials
Cobalt-based powders represent a triumph of materials science, offering a unique combination of properties that meet the demands of extreme applications. As industries continue to push the boundaries of performance, these powders will play an increasingly vital role in shaping the future of aerospace, medical devices, tooling, and countless other sectors. By understanding the nuances of cobalt-based powders, their processing, applications, and the competitive landscape, we can harness their full potential to create innovative solutions that drive progress and enhance our world.