Properties and Characteristics of CoNiCr Powder
CoNiCr powder, a ternary alloy composed of cobalt, nickel, and chromium, exhibits a unique combination of properties that make it highly desirable for a wide range of applications. These properties are primarily influenced by the alloy composition and manufacturing process.
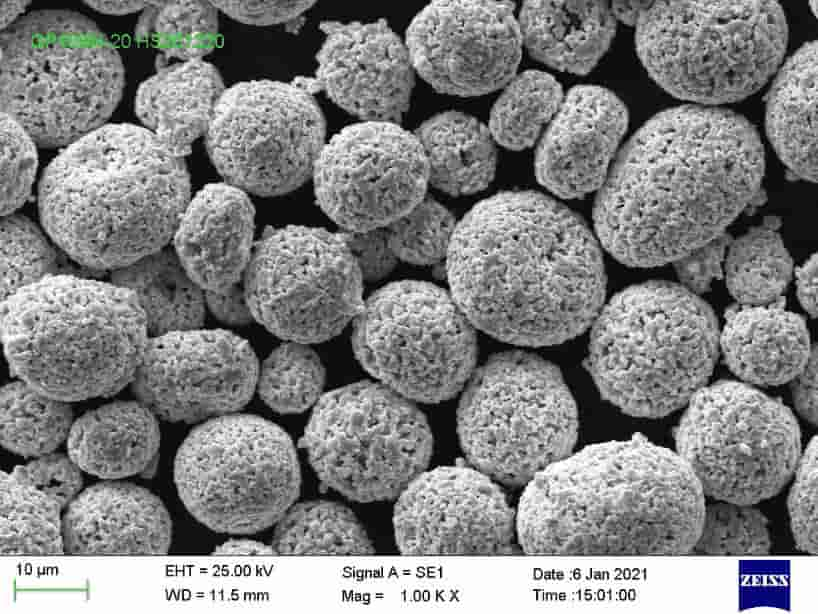
Chemical Composition and Role of Each Element
Element | Typical Percentage | Role in CoNiCr Powder |
---|---|---|
Kobalt (Co) | 35-60% | Provides corrosion resistance, high strength, and thermal stability. |
Nikel (Ni) | 20-40% | Enhances toughness, elasticity, and resistance to oxidation, particularly at high temperatures. |
Krom (Cr) | 10-30% | Adds significant corrosion resistance, especially in oxidizing environments. |
Fiziksel Özellikler
- The particle size of CoNiCr powder can vary widely depending on the manufacturing process. Smaller particle sizes generally lead to improved sinterability and finer-grained microstructure.
- CoNiCr powder particles can exhibit various shapes, including spherical, angular, or irregular. The particle shape can influence the packing density and flowability of the powder.
- The density of CoNiCr powder is typically higher than that of many other metal powders, due to the presence of heavier elements like cobalt and nickel.
Mekanik Özellikler
- CoNiCr powder exhibits high hardness, which contributes to its excellent wear resistance and resistance to abrasion.
- The tensile strength of CoNiCr powder is generally high, making it suitable for applications requiring high mechanical strength.
- CoNiCr powder has good fatigue resistance, which is important for components subjected to cyclic loading.
- CoNiCr powder exhibits excellent creep resistance, allowing it to maintain its shape and mechanical properties at elevated temperatures.
Termal Özellikler
- The melting point of CoNiCr powder is relatively high, making it suitable for applications involving high-temperature environments.
- CoNiCr powder has moderate thermal conductivity, which can be beneficial for applications where heat dissipation is a concern.
- The thermal expansion coefficient of CoNiCr powder is relatively low, which helps to minimize distortion and cracking during thermal cycling.
Korozyon Direnci
- CoNiCr powder is highly resistant to oxidation, even at elevated temperatures.
- The chromium content in CoNiCr powder provides excellent resistance to pitting corrosion in chloride-containing environments.
- CoNiCr powder is generally resistant to sulfidation, which is important for applications in high-sulfur environments.
The combination of these properties makes CoNiCr powder a versatile material with a wide range of applications, including aerospace, automotive, biomedical, and electronics industries.
Manufacturing Processes of CoNiCr Powder
CoNiCr powder can be produced using various manufacturing techniques, each with its own advantages and disadvantages. The choice of manufacturing process often depends on factors such as desired particle size, shape, purity, and cost.
Powder Metallurgy Techniques
- This process involves spraying molten metal into a cooling gas or liquid, resulting in the formation of fine powder particles. The cooling medium can be air, water, or a mixture of both. Atomization is a common method for producing CoNiCr powder due to its ability to produce a wide range of particle sizes and shapes.
- In this process, elemental powders of cobalt, nickel, and chromium are blended together and subjected to intensive mechanical processing, such as ball milling. The mechanical energy causes the powders to deform, fracture, and re-bond, resulting in a homogeneous CoNiCr alloy powder. Mechanical alloying is particularly suitable for producing powders with a fine, uniform microstructure.
- This technique involves depositing CoNiCr alloy onto a sacrificial substrate from an electrolytic solution. The deposited alloy is then removed from the substrate and crushed to form powder. Electrodeposition can produce CoNiCr powder with a controlled composition and morphology.
Chemical Synthesis Methods
- CoNiCr powder can be produced by precipitating the alloy from a solution containing cobalt, nickel, and chromium salts. A suitable reducing agent is added to the solution to cause the metal ions to precipitate as a solid. Precipitation can be carried out in a variety of conditions, such as pH, temperature, and stirring rate.
- In this process, a sol (a colloidal suspension of solid particles in a liquid) is formed by mixing metal salts with a suitable precursor. The sol is then converted into a gel through a process called gelation. The gel is dried and calcined to produce CoNiCr powder. The sol-gel process can produce powders with a high degree of purity and control over particle size and morphology.
Diğer Yöntemler
- This technique involves reacting a mixture of metal oxides (e.g., cobalt oxide, nickel oxide, chromium oxide) with a reducing agent (e.g., aluminum, magnesium) under highly exothermic conditions. The rapid reaction generates heat, which melts the reactants and forms CoNiCr powder. Combustion synthesis is a relatively inexpensive and scalable method for producing CoNiCr powder.
- This process involves spraying a molten metal or alloy onto a substrate using a high-velocity plasma jet. The molten material solidifies upon contact with the substrate, forming a coating or layer. CoNiCr powder can be produced by collecting the sprayed material. Plasma spraying is often used to produce coatings for wear and corrosion resistance.
The choice of manufacturing process for CoNiCr powder depends on various factors, including desired properties, cost, and production scale. Table 1 summarizes the key characteristics and applications of different manufacturing methods.
CoNiCr powder, while offering numerous benefits, also presents potential environmental and safety risks if not handled and disposed of properly. This chapter discusses the environmental impacts and safety considerations associated with CoNiCr powder. Table 1 summarizes the key environmental and safety considerations associated with CoNiCr powder.
Üretim Yöntemi
Avantajlar
Dezavantajlar
Uygulamalar
Atomizasyon
Produces a wide range of particle sizes and shapes, high purity
Requires specialized equipment and can be energy-intensive
Havacılık, otomotiv, elektronik
Mekanik Alaşımlama
Produces fine, uniform microstructure, scalable
Can be time-consuming and energy-intensive
Havacılık, otomotiv, elektronik
Elektrodepozisyon
Precise control over composition and morphology, relatively low cost
Limited control over particle size and shape, requires a sacrificial substrate
Electronics, biomedical
Yağış
Simple and scalable, high purity
Can be difficult to control particle size and morphology
Chemical synthesis, catalysis
Sol-Gel Süreci
High purity, control over particle size and morphology
Complex process, can be time-consuming
Electronics, catalysis
Combustion Synthesis
Simple and scalable, low cost
Difficult to control particle size and morphology, can produce off-gases
Havacılık ve uzay, otomotiv
Plazma Püskürtme
Produces coatings with high wear and corrosion resistance
Limited control over particle size and shape, can be energy-intensive
Aerospace, automotive, biomedical
Environmental and Safety Considerations
Environmental Impacts
Güvenlikle İlgili Hususlar
Güvenlik Önlemleri
Sustainable Practices
Çevresel Etki
Safety Consideration
Etki Azaltıcı Önlemler
Air pollution
Respiratory hazards
PPE, ventilation
Water pollution
Skin irritation, eye irritation
Proper disposal, waste management
Soil contamination
Fire and explosion hazards
Storage, handling procedures
Recycling, pollution prevention
Geniş Yüksek Entropi Alaşımlı Toz yelpazesi hakkında daha fazla bilgi edinmek isterseniz, lütfen tablodaki isimlere tıklayın :