Introduction: A Material for Extreme Conditions
In the realm of high-performance materials, CuCrZr powder stands out as a versatile and robust solution for applications demanding exceptional strength, conductivity, and resistance to wear and tear, especially under extreme temperatures. This copper-based alloy powder, enriched with chromium and zirconium, has garnered significant attention across industries for its unique ability to maintain its mechanical and electrical properties even in challenging environments.
This comprehensive exploration delves into the intricacies of CuCrZr powder, covering its properties, processing techniques, diverse applications, and competitive landscape, ultimately highlighting why it has become a material of choice for engineers and manufacturers seeking to push the boundaries of performance.
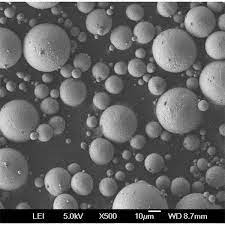
Understanding CuCrZr Powder
What is CuCrZr Powder?
CuCrZr powder is a specialized alloy powder primarily composed of copper (Cu), with carefully controlled additions of chromium (Cr) and zirconium (Zr). This unique composition gives rise to a material that inherits the excellent electrical and thermal conductivity of copper while exhibiting significantly enhanced strength, hardness, and resistance to wear, softening, and oxidation, particularly at elevated temperatures. This combination of properties makes CuCrZr powder particularly well-suited for applications where high electrical and thermal conductivity must be maintained under demanding mechanical and thermal conditions.
Working Principle: Synergy of Elements
The remarkable properties of CuCrZr powder stem from the synergistic interplay of its constituent elements:
- Bakır (Cu): As the base metal, copper provides the foundation for excellent electrical and thermal conductivity. Its inherent ductility also contributes to the alloy’s overall toughness.
- Krom (Cr): Chromium is the key to enhancing the material’s strength, hardness, and resistance to wear, oxidation, and softening at high temperatures. It forms protective oxide layers that prevent further oxidation and contribute to the material’s durability.
- Zirkonyum (Zr): Zirconium further improves the alloy’s strength and high-temperature properties, particularly its resistance to creep. It also acts as a grain refiner, promoting a finer and more uniform microstructure, which leads to improved mechanical properties and increased resistance to wear and tear.
Processing of CuCrZr Powder
CuCrZr powder is typically processed using powder metallurgy techniques, which offer advantages in terms of control over composition and microstructure:
- Toz Üretimi: Atomization is the most common method for producing CuCrZr powder. This involves melting the alloy and then atomizing it into fine droplets using a high-pressure gas stream. The droplets solidify rapidly into powder particles, resulting in a powder with a controlled particle size distribution.
- Compaction: The CuCrZr powder is then compacted into the desired shape using a die and high pressure. This process, known as pressing, densifies the powder and forms a “green compact” that has sufficient strength for handling but is still porous.
- Sinterleme: The green compact is then heated in a controlled atmosphere, typically a reducing atmosphere to prevent oxidation, to a temperature below the melting point of the alloy. This process, known as sintering, allows for the bonding of the powder particles through diffusion, resulting in a dense and solid component with the desired mechanical and electrical properties.
Classifications and Grades
CuCrZr powder is available in various grades and classifications to meet the specific requirements of different applications. These classifications are typically based on factors like:
- Kompozisyon: The precise percentages of Cu, Cr, and Zr can be adjusted to fine-tune the material’s properties. For example, higher chromium content generally leads to increased strength and wear resistance.
- Parçacık Boyutu Dağılımı: The size distribution of the powder particles influences the powder’s flowability, packing density, and the final product’s properties. Finer powders generally result in higher densities and finer microstructures.
- Oksijen İçeriği: The oxygen content of the powder is carefully controlled as it can significantly affect the material’s conductivity and mechanical properties. Lower oxygen content is generally desirable for achieving higher conductivity.
Pazar Eğilimleri
The demand for CuCrNb powder is driven by the increasing need for high-performance materials in various industries, including:
- Elektrik ve Elektronik: The growing demand for smaller, more powerful, and more reliable electronic devices has led to an increased need for materials like CuCrZr powder that can withstand high temperatures and currents. This is particularly true in applications like resistance welding electrodes, electrical contacts, and lead frames.
- Otomotiv: The automotive industry is constantly striving for lighter and more fuel-efficient vehicles. This has led to an increased use of lightweight materials like aluminum in car bodies, which in turn has driven the demand for resistance welding electrodes made from materials like CuCrZr powder that can handle the challenges of welding these materials.
- Havacılık ve uzay: The aerospace industry demands materials that can withstand extreme temperatures, pressures, and corrosive environments. CuCrZr powder’s excellent high-temperature properties and resistance to oxidation make it well-suited for components used in aircraft engines, exhaust systems, and other critical applications.
CuCrZr Powder: A Closer Look
Table 1: Properties and Specifications of CuCrZr Powder
Mülkiyet | Typical Value(s) | Birim |
---|---|---|
Kompozisyon | Cu: 98-99%, Cr: 0.8-1.2%, Zr: 0.15-0.3% | wt.% |
Yoğunluk | 8,9 g/cm³ | g/cm³ |
Elektriksel İletkenlik | 80-90% IACS (International Annealed Copper Standard) | % IACS |
Çekme Dayanımı | 450-600 MPa | MPa |
Sertlik | 120-180 HB (Brinell Hardness) | HB |
Softening Temperature | > 450 °C | °C |
Parçacık Boyutu | 10-100 µm (typical range) | µm |
Table 2: Comparing CuCrZr Powder with Similar Materials
Malzeme | Electrical Conductivity (% IACS) | Çekme Dayanımı (MPa) | Softening Temperature (°C) | Aşınma Direnci |
---|---|---|---|---|
CuCrZr | 80-90 | 450-600 | > 450 | Mükemmel |
Saf Bakır | 100 | 200-250 | < 200 | Zayıf |
CuCr | 70-80 | 350-450 | 400 | İyi |
CuW (Copper Tungsten) | 30-40 | 500-700 | > 500 | Çok iyi |
Applications of CuCrZr Powder
The unique properties of CuCrZr powder make it suitable for a wide range of applications across various industries:
1. Resistance Welding Electrodes: This is one of the most common applications for CuCrZr powder. The material’s excellent conductivity, high strength, and wear resistance at elevated temperatures make it ideal for spot welding electrodes, particularly for demanding applications like automotive manufacturing where high-volume production and consistent weld quality are critical. CuCrZr electrodes offer longer electrode life, reduced downtime for electrode dressing or replacement, and improved weld consistency.
2. Electrical Contacts: CuCrZr powder is also widely used in the production of electrical contacts for applications like switches, relays, and connectors. The material’s high conductivity, wear resistance, and resistance to arcing erosion ensure reliable electrical contact and extended component life. This is particularly important in applications where high currents or voltages are present.
3. High-Temperature Components: CuCrZr powder’s resistance to softening and oxidation at elevated temperatures makes it suitable for components used in furnaces, heat exchangers, and other high-temperature environments. These components can include heating elements, burner nozzles, and structural components that need to maintain their strength and integrity under extreme thermal cycling.
4. Lead Frames for Electronic Packaging: In the electronics industry, CuCrZr powder is used in the production of lead frames, which are used to provide electrical connections between the semiconductor chip and the external circuitry. The material’s good conductivity, strength, and thermal expansion properties make it well-suited for this application, ensuring reliable electrical and thermal performance.
5. Other Applications: CuCrZr powder also finds applications in a variety of other areas, including:
- Rulmanlar ve Burçlar: Its good wear resistance and high-temperature strength make it suitable for bearings and bushings operating under demanding conditions.
- Valve Guides: Its resistance to wear and erosion make it suitable for valve guides in internal combustion engines.
- Mold Components: Its high thermal conductivity and resistance to wear make it suitable for mold components used in plastic injection molding.
Target Industries and Users:
- Otomotiv: Automotive manufacturers and their component suppliers are major users of CuCrZr powder, primarily for resistance welding electrodes used in body-in-white production.
- Elektronik: Electronics manufacturers utilize CuCrZr powder for electrical contacts, lead frames, and other components requiring high conductivity and reliability.
- Industrial Equipment: Manufacturers of industrial furnaces, heat treatment equipment, and other high-temperature applications utilize CuCrZr powder for its strength and resistance to softening.
Comparing Suppliers of CuCrZr Powder
Table 3: Supplier Comparison for CuCrZr Powder
Tedarikçi | Konum | Fiyat Aralığı (USD/kg) | Uzmanlık Alanları |
---|---|---|---|
Xmetto | Çin | $45 – $65 | Customized compositions, consistent quality, competitive pricing |
Kymera Uluslararası | ABD | $60 – $80 | High-purity powders, wide range of alloys, technical support |
Ametek Specialty Metal Powders | ABD | $55 – $75 | Fine particle sizes, specialized grades, research and development capabilities |
Metal Tozları Makinaları | BIRLEŞIK KRALLIK | $50 – $70 | Gas atomized powders, technical support, global distribution network |
Not: Prices are approximate and can vary based on order volume, specifications, and market conditions.
Advantages and Limitations of CuCrZr Powder
Table 4: Advantages and Disadvantages of CuCrZr Powder
Avantajlar | Sınırlamalar |
---|---|
Yüksek mukavemet ve sertlik | Relatively higher cost compared to pure copper |
Mükemmel aşınma direnci | Processing can be more challenging than some alloys |
İyi elektrik ve ısı iletkenliği | Limited ductility compared to pure copper |
Resistance to softening at high temperatures | – |
Good resistance to oxidation and corrosion | – |
Related Insights: The Importance of Powder Metallurgy
The remarkable properties of CuCrZr powder are realized through powder metallurgy, a specialized manufacturing process offering unique advantages:
- Control over Composition: Powder metallurgy allows for precise control over the alloy composition, enabling the creation of materials with tailored properties to meet specific application requirements. This is particularly important for achieving the desired balance of conductivity, strength, and high-temperature performance in CuCrZr alloys.
- Near-Net Shape Manufacturing: Powder metallurgy enables the production of parts that are close to their final shape, reducing the need for extensive machining and minimizing material waste. This can result in significant cost savings, especially for complex shapes.
- Uniform Microstructure: Powder metallurgy processes typically result in a more homogeneous and finer microstructure compared to traditional casting methods. This finer and more uniform microstructure contributes to improved mechanical properties, such as higher strength and increased ductility.
- Suitability for Complex Shapes: Powder metallurgy is well-suited for producing complex shapes that may be difficult or impossible to manufacture using traditional casting or machining methods. This allows for greater design freedom and the ability to create components with intricate geometries.
Conclusion: CuCrZr Powder – A Material for the Future
CuCrZr powder has emerged as a critical material for a wide range of demanding applications across various industries. Its unique combination of high conductivity, strength, wear resistance, and high-temperature performance makes it an ideal choice for components that operate under extreme conditions. As industries continue to push the boundaries of performance and efficiency, the demand for advanced materials like CuCrZr powder is only expected to grow.
Why Choose Xmetto for CuCrZr Powder?
Xmetto stands out as a reliable and innovative supplier of CuCrZr powder, offering:
- Yüksek Kaliteli Tozlar: Stringent quality control measures ensure consistent powder properties, meeting the demanding requirements of high-performance applications. Our commitment to quality ensures that our CuCrZr powder consistently meets or exceeds industry standards.
- Rekabetçi Fiyatlandırma: Xmetto provides competitive pricing without compromising on quality, making it a cost-effective choice for your material needs. We strive to offer our customers the best value for their investment.
- Özelleştirme Seçenekleri: Xmetto offers customized CuCrZr powder compositions tailored to meet specific application requirements. Our technical team works closely with customers to understand their needs and develop tailored solutions.
- Teknik Uzmanlık: Our team of experts provides technical support and guidance throughout the material selection and implementation process. We are committed to helping our customers achieve optimal results with our CuCrZr powder.
- Reliable Supply Chain: Xmetto ensures a stable and reliable supply chain, meeting your material demands consistently. We understand the importance of timely delivery and work closely with our customers to ensure their production schedules are met.
FAQs: Addressing Your Key Questions
1. What are the key advantages of using CuCrZr powder for resistance welding electrodes?
CuCrZr powder offers a unique combination of high electrical conductivity, excellent wear resistance at elevated temperatures, and superior resistance to softening. This makes it ideal for resistance welding electrodes, ensuring consistent performance and extended electrode life, especially in demanding applications like automotive manufacturing.
2. How does the addition of zirconium influence the properties of CuCrZr powder compared to CuCr powder?
Zirconium further enhances the high-temperature strength and softening resistance of the alloy. It also acts as a grain refiner, promoting a finer and more uniform microstructure, leading to improved mechanical properties and increased resistance to wear and tear.
3. What are the typical sintering temperatures used for CuCrZr powder?
Sintering temperatures for CuCrZr powder typically range from 900°C to 1050°C, depending on the desired final density, microstructure, and properties. The sintering process is usually carried out in a reducing atmosphere to prevent oxidation.
4. Can CuCrZr powder be used in additive manufacturing processes?
Yes, CuCrZr powder is suitable for additive manufacturing processes like selective laser melting (SLM). Its good flowability, suitable melting point, and ability to achieve high densities after sintering make it a viable material for producing complex components with intricate geometries.
5. What technical support does Xmetto offer to ensure successful implementation of CuCrZr powder?
Xmetto provides comprehensive technical support, including detailed material specifications, processing guidelines, and expert advice on powder selection, optimization of sintering parameters, and troubleshooting any potential challenges encountered during implementation. We strive to ensure our customers achieve optimal results with our CuCrZr powder.