In the fiercely competitive and unforgiving realm of industrial tooling, where precision and durability are non-negotiable, and where tools are pushed to their absolute limits day in and day out, one material stands tall, revered for its exceptional wear resistance and its uncanny ability to maintain a razor-sharp edge even under the most demanding conditions: D2 powder. This high-carbon, high-chromium tool steel, renowned for its ability to withstand the relentless onslaught of abrasive wear and retain its cutting edge even when faced with extreme pressures and abrasive materials, is the secret weapon behind countless industries that rely on tools that stay sharper, longer, and consistently deliver exceptional results. This blog post delves deep into the fascinating world of D2 powder, exploring its unique properties, its diverse range of applications across various industries, and why it’s the go-to choice for tooling that demands uncompromising performance, unwavering reliability, and an exceptionally long service life.
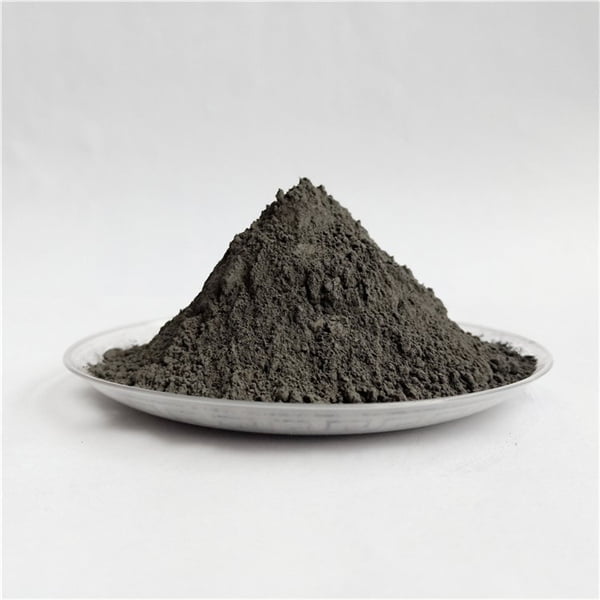
What Makes D2 Powder the Undisputed King of Wear Resistance?
D2 powder doesn’t just stumble upon its well-deserved reputation for exceptional wear resistance; it earns it through a potent and carefully engineered combination of strategically selected alloying elements and advanced processing techniques that work in perfect harmony to create a material capable of withstanding the harshest conditions. It’s not just about being hard; it’s about resisting the relentless forces of abrasion, erosion, and deformation, ensuring the tool maintains its critical cutting edge, its dimensional accuracy, and its overall structural integrity over extended periods of use, even when subjected to extreme pressures, high temperatures, and abrasive materials that would render lesser tool steels useless in no time. Here’s a closer look at the key properties that make D2 powder the undisputed king of wear resistance:
- High Carbon Content: The Foundation of Hardness and Wear Resistance: At the very core of D2 powder’s exceptional wear resistance lies its impressive carbon content, typically around 1.5%, a defining characteristic that sets it apart from other tool steels. This high carbon content, combined with a significant amount of chromium, forms hard, wear-resistant chromium carbides within the steel matrix. These carbides, strategically dispersed throughout the material, act like microscopic pieces of armor, creating a formidable barrier against abrasion and effectively maintaining the tool’s cutting edge even when working with highly abrasive materials or under extreme pressure conditions that would quickly dull or damage other tool steels.
- Yüksek Krom Content: The Shield Against Corrosion and Wear: D2 powder typically contains around 12% chromium, a strategic addition that elevates it to the status of a semi-stainless steel, providing it with an extra layer of protection against the elements. This high chromium content provides excellent corrosion resistance, effectively shielding the tool from the damaging effects of rust and oxidation, which can quickly degrade cutting edges, compromise structural integrity, and ultimately shorten tool life. This corrosion resistance also plays a crucial role in enhancing wear resistance by preventing the formation of pits, cracks, and other surface imperfections that can accelerate wear and tear, ensuring the tool maintains its smooth, wear-resistant surface for as long as possible.
- High Wear Resistance: The Ability to Endure the Grind: The synergistic combination of high carbon and chromium content, along with carefully calculated additions of other alloying elements like molybdenum and vanadium, each playing a specific role in enhancing its properties, gives D2 powder its exceptional wear resistance, a characteristic that sets it apart from the competition. This means it can withstand prolonged contact with abrasive materials, high pressures that would deform lesser steels, and the constant friction of sliding or cutting actions without experiencing significant material loss, dulling of its cutting edge, or compromising its structural integrity, making it the ideal choice for applications where tool life, consistent performance, and unwavering reliability are paramount.
- High Hardness: Holding an Edge Against All Odds: D2 powder can be heat-treated to achieve a remarkably high hardness level, typically in the range of 60-64 HRC (Rockwell Hardness Scale), a testament to its ability to withstand extreme forces without succumbing to deformation. This high hardness allows the tool to resist deformation under pressure, maintaining its precise shape and critical cutting edge even when subjected to high stress, impact loads, and the constant friction of cutting or shaping operations. It’s like encasing the tool in a microscopic suit of armor, protecting it from the relentless forces it encounters during its service life, ensuring it remains sharp, precise, and ready to perform at its best.
D2 Powder in Action: Tooling Applications Where Wear Resistance Reigns Supreme
The exceptional wear resistance and seemingly unyielding edge retention of D2 powder, coupled with its impressive hardness and ability to withstand extreme conditions, make it the material of choice for a wide and diverse range of tooling applications across numerous industries where tools are pushed to their absolute limits, precision is non-negotiable, and longevity is paramount:
- Cutting Tools: Where Sharpness is Non-Negotiable: D2 powder reigns supreme in the realm of cutting tools, where maintaining a sharp, long-lasting edge is not just desired, it’s essential. Its applications in this domain are vast and varied, including:
- Industrial Knives and Blades: From cutting through stacks of paper and sheets of plastic to slicing through textiles and even processing food products, D2 powder blades are the workhorses of countless industries. Their ability to maintain their sharpness and resist wear from abrasive materials ensures clean, precise cuts, reduces downtime for blade changes, and improves overall productivity over extended production runs.
- Ölür ve Yumruklar: In the world of metal forming, where precision and repeatability are critical, D2 powder dies and punches are essential components for stamping, blanking, and forming operations. Their exceptional wear resistance allows them to withstand the high pressures and abrasive wear inherent in these processes, maintaining their dimensional accuracy and producing consistent, high-quality parts over millions of cycles without succumbing to premature wear or deformation.
- Shear Blades: Tasked with the demanding job of cutting through sheet metal and other materials, often with varying thicknesses and compositions, D2 powder shear blades are built to endure. Their resistance to dulling, chipping, and deformation ensures clean, straight cuts, reduces material waste, and extends blade life, even when working with tough, abrasive, or difficult-to-cut materials.
- Precision Tooling: Where Accuracy is Everything: Beyond the realm of cutting tools, D2 powder finds its niche in a variety of precision tooling applications where maintaining dimensional accuracy and resisting wear over time are critical factors in ensuring consistent, high-quality results:
- Gauges and Measuring Instruments: In industries where precision is paramount, such as manufacturing, aerospace, and automotive, gauges and measuring instruments must be incredibly accurate and maintain their dimensions over time. D2 powder’s exceptional wear resistance and ability to hold tight tolerances make it the ideal material for these applications, ensuring that measurements remain accurate and reliable, even after repeated use.
- Injection Molding Components: The world of plastic injection molding relies heavily on precision-engineered components to create consistent, high-quality plastic parts. D2 powder is a key player in this field, used for mold inserts, ejector pins, and other critical components that experience high wear from the constant heating, cooling, and injection of molten plastic. Its wear resistance and dimensional stability ensure that molds produce accurate parts over millions of cycles, maintaining the integrity of the manufacturing process.
- Custom Tooling: Tailored Solutions for Demanding Applications: The versatility of D2 powder, coupled with its ability to be machined to incredibly tight tolerances, makes it the go-to choice for custom tooling applications where wear resistance, edge retention, and dimensional stability are non-negotiable. This allows engineers and designers to develop innovative tooling solutions for specific, often challenging applications, knowing that D2 powder can handle the demands and deliver the desired results.
D2 Powder vs. the Competition: Choosing the Right Tool Steel for the Job – A Balancing Act of Properties
Selecting the optimal tool steel for a specific application is a critical decision that can make or break a project, and it involves carefully weighing the pros and cons of various options, considering factors like the material being worked with, the forces involved, the desired balance of properties, and of course, budget constraints. While D2 powder undoubtedly excels in wear resistance, other tool steels might be more suitable depending on the specific requirements of the application. It’s a balancing act, and understanding the strengths and weaknesses of each option is crucial to making an informed decision. Here’s a comparison of D2 powder with other commonly used tool steels to help you navigate the world of tool steel selection:
Mülkiyet | D2 Powder | S7 Tool Steel | A2 Tool Steel | M2 Tool Steel |
---|---|---|---|---|
Aşınma Direnci | Mükemmel | İyi | Çok iyi | İyi |
Sertlik | Orta düzeyde | Mükemmel | İyi | Orta düzeyde |
Sertlik | Çok Yüksek | Orta düzeyde | Yüksek | Çok Yüksek |
Korozyon Direnci | İyi | Düşük | İyi | Düşük |
Key Considerations When Choosing a Tool Steel: Finding the Perfect Match for Your Application:
- Wear Resistance: Battling Abrasion and Prolonging Tool Life: If the application involves working with abrasive materials, high pressures that can wear down cutting edges, or prolonged sliding or cutting actions that generate friction and heat, D2 powder’s exceptional wear resistance makes it a top contender, ensuring your tools can withstand the demands and deliver consistent results over an extended lifespan.
- Toughness: When Impact Resistance is Paramount: For applications where tools are subjected to high impact loads, sudden shocks, or repeated hammering, tougher tool steels like S7, with their higher impact resistance and ability to absorb and dissipate energy, might be a more suitable choice. While D2 powder possesses good toughness, it might be more prone to chipping or cracking under such extreme conditions, making toughness a critical factor to consider.
- Hardness vs. Toughness: Finding the Sweet Spot for Optimal Performance: The eternal dilemma in material science: achieving the perfect balance between hardness, which dictates wear resistance, and toughness, which determines a material’s ability to withstand impact without fracturing. D2 powder’s high hardness delivers exceptional wear resistance but might make it more susceptible to chipping under impact compared to tougher steels. It’s a trade-off, and finding the right balance for your specific application is key to maximizing performance and tool life.
- Corrosion Resistance: Protecting Your Investment from the Elements: If the application involves exposure to moisture, humid environments, or corrosive substances, D2 powder’s good corrosion resistance, thanks to its chromium content, offers a significant advantage over tool steels like M2, which are more susceptible to rust and degradation. Choosing a corrosion-resistant tool steel can significantly extend tool life and reduce maintenance costs, especially in demanding environments.
- Cost vs. Performance: Weighing the Value Proposition: D2 powder typically falls within a moderate cost range compared to other tool steels. While it might not be the cheapest option available, its exceptional wear resistance, balanced properties, and ability to extend tool life often translate to long-term cost savings. It’s an investment that pays dividends in the form of reduced downtime for tool changes, increased productivity, and improved overall efficiency.
Unlocking the Full Potential of D2 Powder: Processing and Heat Treatment – A Symphony of Precision and Control
Like a sculptor meticulously shaping a masterpiece from a block of raw stone, transforming D2 powder from its raw, granular form into high-performance tooling requires a carefully orchestrated series of processing and heat treatment steps, each designed to refine its structure, enhance its properties, and unlock its full potential. These processes are meticulously controlled, involving precise temperatures, carefully timed durations, and specialized equipment to optimize the microstructure of the material, ensuring it delivers the required hardness, wear resistance, toughness, and dimensional stability for the most demanding applications. Here’s a closer look at the key stages involved in this transformative journey:
1. Powder Production: From Molten Metal to Fine Particles: The journey begins with the creation of D2 powder, typically through a process known as gas atomization. This method involves melting the steel, bringing it to a liquid state, and then atomizing it into a fine mist of droplets using a high-pressure stream of inert gas. These droplets, suspended in the gas stream, solidify rapidly into fine powder particles, ensuring a high degree of chemical homogeneity and a fine, uniform microstructure, which are crucial for its exceptional properties.
2. Powder Compaction: Shaping the Future Under Pressure: The fine D2 powder, now in a controllable form, is then compacted into a desired shape using a precisely machined die and a powerful high-pressure press. This process, known as cold isostatic pressing (CIP), applies pressure uniformly in all directions, ensuring a homogenous density distribution within the compacted part. This results in a “green” compact, a pre-sintered form that, while still relatively fragile, holds its shape and is ready for the next stage of its transformation.
3. Sintering: Fusing Particles into a Solid Form: The green compact, now resembling its final form but lacking the structural integrity of a solid object, is then subjected to a controlled heating process called sintering. During sintering, the powder particles, brought into close contact during compaction, bond together at elevated temperatures, typically in a vacuum or carefully controlled atmosphere, to prevent oxidation and ensure the desired properties are achieved. This process transforms the loose powder into a solid, dense component, ready for the final stages of its transformation.
4. Heat Treatment: The Alchemy of Transformation: To achieve the desired hardness, wear resistance, toughness, and other mechanical properties that make D2 powder so sought after, the sintered component undergoes a carefully orchestrated multi-step heat treatment process, a delicate dance of heating and cooling that determines its final properties:
* Austenitizing: The first step involves heating the steel to a high temperature, typically above its critical point, to dissolve the carbides into the austenite matrix, creating a uniform, high-temperature structure that’s primed for transformation. This step ensures that the carbides are evenly distributed throughout the material, which is crucial for its final properties.
* Söndürme: Once the austenitizing temperature is reached and held for a specific duration, the steel is rapidly cooled, typically in a quenching medium like oil or water, to transform the austenite into martensite, a hard, strong structure that forms the basis for D2 powder’s impressive hardness and wear resistance. The speed of cooling during quenching is critical, as it determines the size and distribution of the martensite crystals, which directly influence the material’s final properties.
* Temperleme: After quenching, the steel, now incredibly hard but also brittle, undergoes a tempering process, which involves heating it to a lower temperature, carefully selected based on the desired properties, to reduce brittleness and increase toughness while maintaining a good level of hardness. The tempering temperature and time are carefully controlled to achieve the desired balance of properties for the specific application, as different temperatures and durations will result in different microstructures and, therefore, different mechanical properties.
5. Finishing Operations: Polishing the Masterpiece: With the heat treatment complete and the desired properties achieved, the component, now a high-performance tool steel, might undergo additional finishing operations, depending on the specific requirements of the application. These operations can include grinding, lapping, polishing, or coating to achieve the desired surface finish, tolerances, and functional characteristics. These finishing touches are crucial for ensuring the tool performs optimally in its intended application, adding the final layers of precision and refinement to a masterpiece of engineering.
D2 Powder: Your Frequently Asked Questions Answered
1. What are the key advantages of choosing D2 powder over conventional D2 tool steel?
D2 powder offers several advantages over conventional D2 steel, primarily due to its production process. The powder metallurgy process results in a finer, more uniform carbide structure, leading to improved wear resistance, toughness, and dimensional stability compared to its conventionally produced counterpart. This translates to longer tool life, increased productivity, and a better overall value proposition, especially for demanding applications.
2. Can D2 powder be used for applications involving high impact or shock loads?
While D2 powder possesses good toughness, it’s not the ideal choice for applications involving extremely high impact or shock loads. Its high hardness, while excellent for wear resistance, can make it slightly more susceptible to chipping or cracking under such extreme conditions. For these situations, tougher tool steels like S7, specifically designed to withstand impact and shock, would be a more suitable choice.
3. How does the cost of D2 powder compare to other high-performance tool steels?
D2 powder typically falls within a moderate cost range compared to other high-performance tool steels. While it might not be the cheapest option available, its exceptional wear resistance, balanced properties, and ability to extend tool life often translate to long-term cost savings. It’s an investment in performance and longevity that often outweighs the initial cost difference.
4. What are the typical heat treatment temperatures for D2 powder to achieve optimal properties?
Heat treatment temperatures for D2 powder can vary depending on the desired properties and specific application requirements. However, a typical austenitizing temperature range is 1850-1950°F (1010-1065°C), followed by quenching and tempering. The tempering temperature can range from 300-1000°F (150-540°C) depending on the desired balance of hardness and toughness. Consulting a heat treatment specialist is recommended to determine the optimal parameters for your specific application.
5. Is D2 powder readily machinable, or does it require specialized machining techniques?
D2 powder, in its annealed state, can be machined using conventional machining techniques. However, its high hardness after heat treatment requires specialized tooling and machining practices. Carbide tooling, slower cutting speeds, and adequate lubrication are essential for successful machining of hardened D2 powder.
Her şeyi bilmek istiyorsanız, bu kılavuz size yardımcı olacaktır:
Demir Bazlı Alaşım Tozları: Mükemmellik için Nihai Eksiksiz Kılavuz