Properties and Characteristics of CoCrW Powder
CoCrW powder is a versatile material known for its exceptional properties, making it a popular choice in various industries. The unique combination of cobalt, chromium, and tungsten provides CoCrW powder with a distinct set of characteristics that make it suitable for demanding applications.
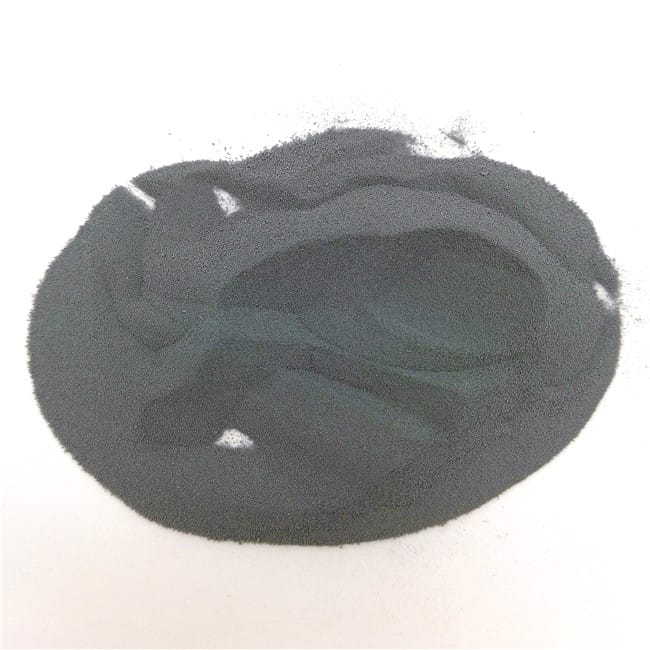
Kimyasal Bileşim
The primary components of CoCrW powder are cobalt, chromium, and tungsten. The exact composition can vary depending on specific requirements, but typical ranges include:
- 40-65%
- 19-30%
- 5-15%
Other elements, such as nickel, iron, manganese, and silicon, may be added in smaller quantities to tailor the properties further.
Fiziksel Özellikler
CoCrW powder exhibits several physical properties that contribute to its performance:
- Approximately 8.3 g/cm³
- High, typically around 1400-1500°C
- Varies depending on manufacturing process, ranging from fine to coarse powders
- Typically gray or silver in color
Mekanik Özellikler
CoCrW powder possesses excellent mechanical properties, including:
- It exhibits both high tensile and yield strengths, making it suitable for applications requiring structural integrity.
- CoCrW powder can be deformed without fracturing, allowing for complex shapes and processes.
- Its hard and abrasive nature provides excellent wear resistance, making it ideal for components subjected to friction and abrasion.
- CoCrW powder can withstand repeated stress cycles without failing, ensuring long-term durability.
Korozyon Direnci
CoCrW powder is highly resistant to corrosion, especially in oxidizing environments. The chromium content forms a protective oxide layer on the surface, preventing corrosion and maintaining the integrity of the material. This property is particularly valuable in applications exposed to harsh conditions, such as marine environments or corrosive chemicals.
Yüksek Sıcaklık Performansı
CoCrW powder can maintain its mechanical properties and resist oxidation at elevated temperatures. This makes it suitable for applications in high-temperature environments, such as jet engine components, gas turbines, and heat exchangers.
Properties of CoCrW Powder
CoCrW powder can be produced through various manufacturing processes, each with its own advantages and disadvantages. The choice of process depends on factors such as desired particle size, purity, and cost. Atomization is a common method for producing CoCrW powder. It involves melting the alloy and then breaking it into tiny droplets, which solidify into powder particles. There are several types of atomization processes: Plasma spraying is a process in which a plasma torch is used to heat a powder feedstock to a high temperature, melting the particles and depositing them onto a substrate. CoCrW powder can be used as a feedstock for plasma spraying to create coatings or components. Electrodeposition is a process in which a metal or alloy is deposited onto a substrate from a solution containing ions of the metal. CoCrW powder can be produced by electrodepositing a CoCrW alloy onto a sacrificial substrate and then removing the substrate to obtain the powder. Mechanical alloying is a process in which powders of different elements are mixed and subjected to intense mechanical energy, causing them to bond and form a new alloy. CoCrW powder can be produced by mechanically alloying cobalt, chromium, and tungsten powders. Other methods for producing CoCrW powder include: CoCrW powder is a versatile material with a wide range of applications across various industries. Its unique combination of properties, including high strength, wear resistance, corrosion resistance, and high-temperature performance, makes it suitable for demanding environments. CoCrW powder offers several advantages that make it a desirable material for many applications. However, it also has some limitations that should be considered. CoCrW powder is a promising material with a bright future, driven by ongoing research and development efforts. Several trends and developments are shaping the future of CoCrW powder, including: Q1: What are the key benefits of using CoCrW powder for wear-resistant coatings and components? A1: CoCrW powder stands out for its exceptional hardness, excellent wear resistance, and strong resistance to corrosion, even at high temperatures. This makes it ideal for applications facing severe wear, impact, and harsh environments. Q2: Which industries and applications commonly utilize CoCrW powder? A2: CoCrW powder finds extensive use in industries like oil and gas, aerospace, tooling, and power generation. Common applications include valve components, seals, cutting tools, and other parts subjected to high wear and tear. Q3: What thermal spray processes are recommended for applying CoCrW powder coatings? A3: High-Velocity Oxygen Fuel (HVOF) and Plasma Transferred Arc (PTA) welding are highly effective for applying CoCrW powder coatings. These processes create dense, well-bonded coatings with superior wear and corrosion resistance. Q4: How does the Tungsten (W) content in CoCrW powder contribute to its overall performance? A4: Tungsten plays a vital role in enhancing the hardness, wear resistance, and high-temperature strength of CoCrW powder. The higher the tungsten content, the harder and more wear-resistant the resulting coating or component will be. Q5: Are there any special considerations for handling and storing CoCrW powder safely? A5: As with any fine metal powder, handle CoCrW powder with care. Store it in a cool, dry place, away from sources of ignition and incompatible materials. Using appropriate personal protective equipment, such as gloves and a mask, during handling is always recommended.
Mülkiyet
Değer
Kimyasal bileşim
Cobalt, chromium, tungsten (with potential additions)
Yoğunluk
Approximately 8.3 g/cm³
Erime noktası
1400-1500°C
Parçacık boyutu
Değişir
Görünüş
Gray or silver
Güç
High tensile and yield strengths
Süneklik
İyi
Aşınma direnci
Mükemmel
Yorulma direnci
İyi
Korozyon direnci
Mükemmel
High-temperature performance
İyi
Manufacturing Processes of CoCrW Powder
Atomizasyon
Plazma Püskürtme
Elektrodepozisyon
Mekanik Alaşımlama
Diğer Yöntemler
Manufacturing Processes of CoCrW Powder
Süreç
Açıklama
Avantajlar
Dezavantajlar
Atomizasyon
Melting and spraying the alloy into droplets
Versatile, produces a wide range of particle sizes
Can be energy-intensive
Plazma püskürtme
Heating and depositing powder onto a substrate
Can create complex coatings and components
Özel ekipman gerektirir
Elektrodepozisyon
Depositing metal from a solution onto a substrate
Precise control over composition and microstructure
Can be slow and expensive
Mekanik alaşımlama
Mixing and bonding powders
Produces homogeneous alloys
Can be time-consuming and energy-intensive
Diğer yöntemler
CVD, sintering
Specific applications
May have limitations in terms of scalability or cost
Applications of CoCrW Powder
Havacılık ve Uzay Endüstrisi
Biyomedikal Uygulamalar
Otomotiv Endüstrisi
Enerji Sektörü
Other Industries
Applications of CoCrW Powder
Endüstri
Uygulamalar
Havacılık ve Uzay
Turbine blades, vanes, engine components
Biyomedikal
Diş implantları, cerrahi aletler
Otomotiv
Engine components, exhaust systems
Enerji
Gaz türbinleri, nükleer reaktörler
Diğer
Kimyasal işleme, elektronik
Advantages and Disadvantages of CoCrW Powder
Avantajlar
Dezavantajlar
Advantages and Disadvantages of CoCrW Powder
Avantaj
Dezavantaj
Yüksek mukavemet ve dayanıklılık
Maliyet
Korozyon direnci
Brittle nature
High-temperature performance
İşleme zorlukları
Biyouyumluluk
Sınırlı kullanılabilirlik
Çok Yönlülük
Future Trends and Developments in CoCrW Powder
Gelişen Uygulamalar
Technological Advancements
Araştırma ve Geliştirme Çalışmaları
Future Trends and Developments in CoCrW Powder
Trend
Development
Gelişmekte olan uygulamalar
Additive manufacturing, energy storage, wearable technology
Technological advancements
Nanotechnology, surface modification, advanced manufacturing processes
Research and development efforts
New compositions, recycling and sustainability, cost reduction
CoCrW Powder: Your Top 5 Questions Answered
Geniş Kobalt Bazlı Toz yelpazesi hakkında daha fazla bilgi edinmek isterseniz, lütfen tablodaki isimlere tıklayın :