Introduction: Embracing the Future of Materials Science
In an era defined by relentless technological advancements, the demand for materials capable of withstanding extreme conditions and delivering exceptional performance continues to soar. High Entropy Alloys (HEAs), a revolutionary class of materials, have emerged as a beacon of innovation, promising to reshape industries ranging from aerospace to energy production. Among the diverse range of HEA compositions, FeCoNiCrAl (Fe Bal., Co 22.3-24.3, Ni 22.2-24.2, Cr 19.6-21.6, Al 9.7-11.7) stands out as a particularly promising candidate, exhibiting an exceptional combination of strength, ductility, and corrosion resistance. This comprehensive exploration delves into the intricacies of this remarkable material, unraveling its properties, applications, and the competitive advantages it offers.
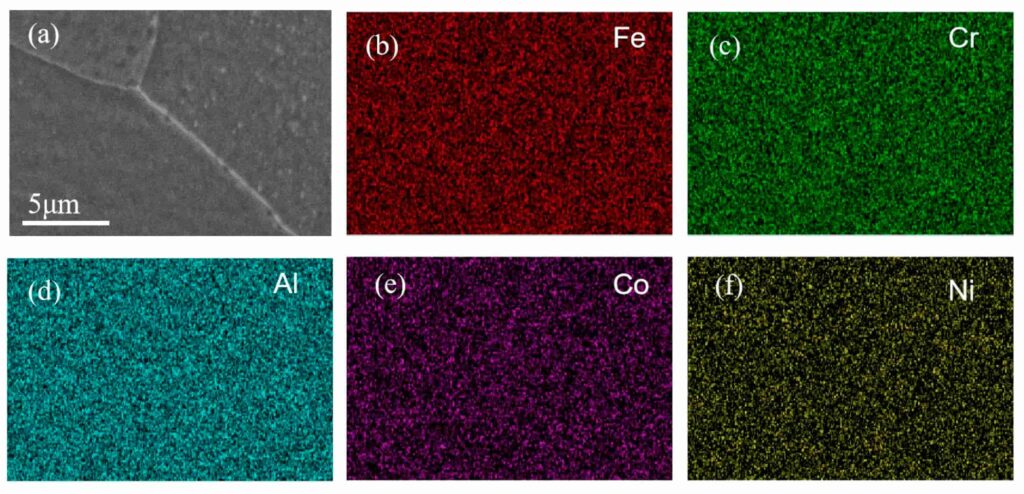
Delving into the World of FeCoNiCrAl HEA Powder
What is FeCoNiCrAl HEA Powder?
FeCoNiCrAl HEA powder represents a specific composition within the broader family of High Entropy Alloys. Unlike traditional alloys, which rely on one or two principal elements, HEAs are characterized by the presence of five or more elements in near-equal atomic proportions (typically 5-35%). This unique compositional strategy, venturing beyond the conventional corners of binary and ternary phase diagrams, unlocks a vast new realm of possibilities in materials design.
In the specific case of FeCoNiCrAl, the alloy consists of iron (Fe) as the base element, balanced with carefully controlled proportions of cobalt (Co), nickel (Ni), chromium (Cr), and aluminum (Al). The powder form of this alloy, produced through advanced gas atomization (GA) techniques, results in spherical particles with exceptional flowability and packing density, making it ideal for various manufacturing processes.
Unveiling the Mechanisms Behind Exceptional Properties
The remarkable properties exhibited by FeCoNiCrAl HEA powder stem from four fundamental effects that distinguish HEAs from their conventional counterparts:
- High Entropy Effect: This effect, the cornerstone of HEA design, centers around the concept of configurational entropy. The random mixing of multiple principal elements significantly increases the configurational entropy of the alloy system. This heightened entropy stabilizes the solid solution phase, suppressing the formation of brittle intermetallic compounds often found in traditional alloys. This stabilization leads to enhanced ductility and toughness, allowing the material to withstand deformation without fracturing.
- Lattice Distortion Effect: The incorporation of different-sized atoms within the crystal lattice creates severe lattice distortion. This distortion hinders the movement of dislocations, the primary mechanism of plastic deformation in metals. The impeded dislocation motion results in increased strength and hardness, allowing the material to resist deformation under applied stress.
- Sluggish Diffusion Effect: The diffusion of atoms within the HEA lattice is significantly slower compared to conventional alloys. This sluggish diffusion arises from the complex energy landscape created by the multi-element environment. The reduced diffusion rates lead to improved thermal stability, creep resistance (resistance to deformation under prolonged stress at high temperatures), and enhanced resistance to grain growth, preserving desirable mechanical properties at elevated temperatures.
- Cocktail Effect: This intriguing effect refers to the synergistic interaction between the multiple constituent elements. This complex interplay can lead to unexpected and beneficial properties, often exceeding the predictions based on the rule of mixtures (a simple weighted average of the properties of the individual elements). The cocktail effect makes predicting HEA properties challenging but also opens up exciting possibilities for tailoring materials with specific property combinations.
Processing and Manufacturing: Shaping the Future with FeCoNiCrAl HEA Powder
The versatility of FeCoNiCrAl HEA powder lends itself to a variety of processing and manufacturing techniques, enabling the fabrication of components with tailored properties and geometries:
- Toz Metalurjisi: This cost-effective route involves the compaction of HEA powders into desired shapes followed by sintering at high temperatures. The sintering process fuses the powder particles together, forming a solid, dense material. Powder metallurgy is particularly well-suited for producing near-net-shape components, minimizing material waste and machining costs.
- Katmanlı Üretim: FeCoNiCrAl HEA powder is highly compatible with additive manufacturing processes, also known as 3D printing, such as Selective Laser Melting (SLM) and Electron Beam Melting (EBM). These techniques involve selectively melting and solidifying layers of HEA powder based on a digital design, enabling the fabrication of complex geometries with high precision and minimal material waste. This capability opens up new possibilities for lightweighting, functional integration, and customized designs.
- Termal Püskürtme: This family of coating technologies involves depositing molten or semi-molten HEA particles onto a substrate material. High-Velocity Oxygen Fuel (HVOF) and plasma spraying are common thermal spray techniques used for HEA deposition. These coatings provide exceptional wear and corrosion resistance, making them suitable for protecting components operating in harsh environments.
Navigating the Landscape: Classification of HEA Powders
The vast compositional space of HEAs leads to a wide variety of powder characteristics, necessitating classification schemes to guide material selection:
- Kompozisyon: The specific combination of elements and their respective atomic percentages primarily dictate the properties of the resulting HEA powder. In the case of FeCoNiCrAl, the carefully balanced proportions of each element contribute to its unique combination of strength, ductility, and corrosion resistance.
- Phase Structure: HEAs can exhibit various crystal structures, including face-centered cubic (FCC), body-centered cubic (BCC), and hexagonal close-packed (HCP), depending on the constituent elements and their interactions. Each crystal structure influences the material’s mechanical behavior, such as ductility, toughness, and strength. FeCoNiCrAl typically exhibits an FCC structure, contributing to its good ductility.
- Parçacık Boyutu ve Morfolojisi: The size and shape of HEA powder particles significantly impact their flowability, packing density, and ultimately, the properties of the final product. Spherical powders, like those produced through gas atomization for FeCoNiCrAl, are generally preferred for powder metallurgy and additive manufacturing due to their superior flowability, enabling uniform packing and dense, defect-free parts.
Market Trends and Future Outlook: A Glimpse into the Future
The global market for HEA powders is experiencing rapid growth, driven by a confluence of factors:
- Increasing Demand for High-Performance Materials: Industries are constantly seeking materials that can withstand increasingly extreme environments, such as high temperatures, corrosive atmospheres, and intense wear conditions. HEAs, with their unique combination of properties, are well-positioned to meet these demands.
- Growing Adoption of Additive Manufacturing: The rise of additive manufacturing technologies, particularly in aerospace, medical, and tooling industries, is driving the demand for high-quality metal powders. HEA powders, with their compatibility with these advanced manufacturing techniques, are poised to benefit significantly from this trend.
- Ongoing Research and Development: The field of HEAs is relatively young, and research efforts are continuously expanding, leading to the discovery of new HEA compositions with improved properties and a deeper understanding of their behavior. This continuous innovation is expected to further fuel market growth.
Unveiling the Specifics: Technical Specifications of FeCoNiCrAl HEA Powder
Mülkiyet | Değer |
---|---|
Alaşım Adı | FeCoNiCrAl |
Tip | FCC High Entropy Alloy Powder |
Composition (at.%) | Fe Bal., Co 22.3-24.3, Ni 22.2-24.2, Cr 19.6-21.6, Al 9.7-11.7 |
Üretim Yöntemi | Gaz Atomizasyonu (GA) |
Parçacık Morfolojisi | Küresel |
Partikül Boyut Aralığı | Customizable (Typically 15-45 µm for AM) |
Görünür Yoğunluk | ~4.0 g/cm³ |
Flow Rate (Hall Flowmeter) | ~25 s/50 g |
Anahtar Özellikler | High Strength, Good Ductility, Excellent Corrosion Resistance, Good Wear Resistance |
Uygulamalar | Additive Manufacturing, Powder Metallurgy, Thermal Spray Coatings |
Table 1: Technical Specifications of FeCoNiCrAl HEA Powder
Applications: Where Performance Meets Versatility
The unique combination of properties exhibited by FeCoNiCrAl HEA powder makes it ideal for a wide range of applications across diverse industries:
1. Aerospace:
- High-Temperature Components: FeCoNiCrAl’s excellent high-temperature strength and creep resistance make it suitable for components in jet engines, rocket nozzles, and other aerospace applications exposed to extreme temperatures.
- Lightweight Structural Parts: The potential for lightweighting without sacrificing strength makes FeCoNiCrAl attractive for aerospace structures, potentially improving fuel efficiency.
2. Automotive:
- Motor Bileşenleri: FeCoNiCrAl can be used to create engine components, such as valves, pistons, and cylinder liners, that can withstand the high temperatures and corrosive environments found in internal combustion engines.
- Egzoz Sistemleri: FeCoNiCrAl-based exhaust systems can offer improved durability and resistance to corrosion, particularly in demanding applications such as heavy-duty trucks and off-road vehicles.
3. Energy:
- Coatings for Gas Turbines: FeCoNiCrAl coatings can protect gas turbine blades from high temperatures, oxidation, and wear, improving efficiency and extending their lifespan.
- Components for Nuclear Reactors: FeCoNiCrAl’s resistance to radiation damage and high-temperature strength make it a potential candidate for components in advanced nuclear reactor designs.
4. Tooling:
- Kesici Aletler: FeCoNiCrAl can be used to create cutting tools with exceptional hardness, wear resistance, and hot hardness, improving cutting performance and tool life.
- Dies and Molds: FeCoNiCrAl-based dies and molds can withstand the high temperatures, pressures, and wear encountered in various manufacturing processes, such as injection molding and die casting.
5. Other Applications:
- Kimyasal İşleme Ekipmanları: FeCoNiCrAl’s corrosion resistance makes it suitable for components in chemical processing equipment exposed to corrosive chemicals.
- Denizcilik Uygulamaları: FeCoNiCrAl’s resistance to saltwater corrosion makes it a potential material for marine components.
Comparing Xmetto with Other HEA Powder Suppliers
Tedarikçi | Konum | Fiyat Aralığı (USD/kg) | Uzmanlık Alanları |
---|---|---|---|
Xmetto | Çin | 600 – 1200 | Custom compositions, wide range of particle sizes, competitive pricing, focus on customer collaboration and technical support |
Marangoz Teknolojisi | ABD | 900 – 1800 | Established supplier, high-quality powders, focus on aerospace applications, stringent quality control processes |
Aubert & Duval | Fransa | 800 – 1600 | Wide range of HEA compositions, expertise in powder metallurgy, strong research and development capabilities |
TLS Technik | Almanya | 700 – 1400 | Focus on additive manufacturing powders, high purity and sphericity, specialized in gas-atomized powders |
Table 2: Comparison of Xmetto with Other HEA Powder Suppliers
Advantages and Disadvantages: A Balanced Perspective
Avantajlar | Dezavantajlar |
---|---|
Exceptional Strength and Ductility: FeCoNiCrAl HEA powder exhibits a remarkable combination of strength and ductility, surpassing many conventional alloys. | High Cost Compared to Conventional Alloys: The complex compositions and specialized processing techniques associated with HEA powders contribute to their higher cost. |
Excellent Wear and Corrosion Resistance: The presence of chromium and aluminum promotes the formation of protective oxide layers, providing exceptional resistance to wear, corrosion, and oxidation. | Limited Availability of Some Compositions: While the number of HEA compositions is rapidly expanding, some specific compositions may have limited commercial availability. |
High-Temperature Stability and Creep Resistance: The sluggish diffusion and high melting points of HEAs contribute to their excellent thermal stability and resistance to creep at elevated temperatures. | Relatively New Technology, Further Research and Development Needed: HEAs are a relatively new class of materials, and further research is ongoing to fully understand their behavior and optimize their properties. |
Tailorable Properties Through Compositional Design: The vast compositional space of HEAs allows for tailoring material properties to meet specific application requirements. | Challenges in Processing and Manufacturing Due to High Melting Points and Reactivity: The high melting points and potential reactivity of some HEA constituent elements can pose challenges for processing and manufacturing. |
Table 3: Advantages and Disadvantages of FeCoNiCrAl HEA Powder
Related Insights: Exploring the Frontiers of HEA Research
The field of HEAs is characterized by continuous innovation and exploration, with researchers constantly pushing the boundaries of materials science:
- Developing Novel Processing Techniques: Researchers are exploring advanced processing techniques, such as spark plasma sintering and field-assisted sintering, to further enhance the properties and performance of HEA components.
- Investigating the Effects of Severe Plastic Deformation: Applying severe plastic deformation techniques, such as high-pressure torsion and equal-channel angular pressing, to HEAs can lead to grain refinement and further enhance their mechanical properties.
- Exploring the Potential of HEA Composites: Combining HEA powders with other materials, such as ceramics or carbon nanotubes, to create HEA composites with tailored properties is an active area of research.
Why Choose Xmetto for FeCoNiCrAl HEA Powder?
Xmetto distinguishes itself as a premier supplier of high-quality FeCoNiCrAl HEA powder, offering a compelling combination of factors that cater to the needs of discerning customers:
- Özel Çözümler: Xmetto understands that each customer has unique requirements. They offer customizable FeCoNiCrAl HEA powder compositions, particle size distributions, and packaging options to meet specific application needs.
- Rekabetçi Fiyatlandırma: Xmetto is committed to providing high-quality FeCoNiCrAl HEA powder at competitive prices, making it accessible for a wider range of industries and applications.
- Teknik Uzmanlık: Xmetto’s team of experienced engineers and material scientists possesses extensive knowledge in HEA powder production, characterization, and processing. They provide valuable technical support to customers, assisting them in selecting the right powder for their application, optimizing processing parameters, and troubleshooting any challenges that may arise.
- Customer-Centric Approach: Xmetto prioritizes customer satisfaction, building long-term partnerships based on trust, reliability, and a deep understanding of their customers’ needs.
Sıkça Sorulan Sorular (SSS)
1. What is the typical lead time for FeCoNiCrAl HEA powder orders from Xmetto?
Lead times vary depending on the order size, specific composition, particle size requirements, and current stock levels. For standard FeCoNiCrAl powder grades, lead times are typically 2-4 weeks. Custom orders may require longer lead times.
2. Can Xmetto provide material characterization data for their FeCoNiCrAl HEA powder?
Yes, Xmetto provides comprehensive material characterization data upon request, including chemical composition analysis, particle size distribution analysis, morphology characterization using SEM, and other relevant data as needed.
3. Does Xmetto offer technical support for processing FeCoNiCrAl HEA powder?
Yes, Xmetto has a dedicated team of technical experts who can provide guidance on powder processing techniques, including powder metallurgy, additive manufacturing, and thermal spraying. They can assist with material selection, process optimization, and troubleshooting.
4. What quality control measures are in place to ensure the consistency and quality of Xmetto’s FeCoNiCrAl HEA powder?
Xmetto implements stringent quality control measures throughout the production process, including raw material inspection, in-process monitoring, and final product testing. They adhere to international quality standards and can provide relevant certifications upon request.
5. What are the recommended storage conditions for FeCoNiCrAl HEA powder?
To prevent oxidation and moisture absorption, it is recommended to store FeCoNiCrAl HEA powder in a cool, dry environment, preferably under an inert atmosphere (e.g., argon or nitrogen).