In the relentless pursuit of lighter, stronger, and more intricate components, the manufacturing world is undergoing a remarkable transformation. At the forefront of this revolution lies powder metallurgy, a technology that’s redefining how we perceive and utilize metals. Driving this innovation is gas atomizasyon, a process that’s not merely about creating metal dust but about unlocking the hidden potential of metals in ways previously unimaginable. Join us as we delve into the seven key benefits of gas atomization for producing metal powders, uncovering why it’s become the gold standard for industries demanding unparalleled material performance.
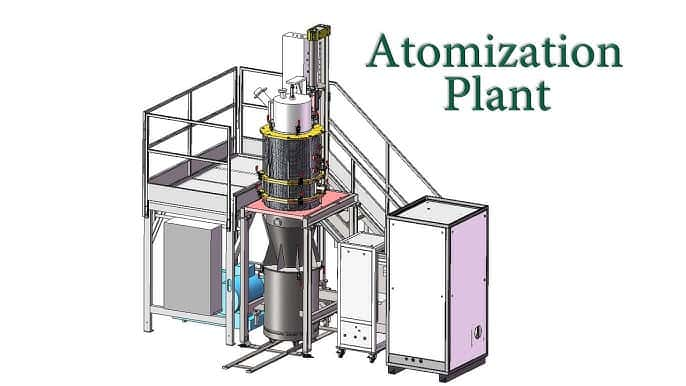
What is Gas Atomization? Transforming Molten Metal into a World of Possibilities
Imagine a crucible glowing with molten metal, heated to temperatures exceeding 1,500°C (2,732°F), flowing like liquid fire. Now, envision this fiery stream being met by a barrage of high-velocity inert gas jets, shattering it into a mesmerizing spray of tiny, incandescent droplets. This captivating process is the essence of gas atomization. Let’s break down this intricate dance of heat and pressure:
- Melting the Metal: The Crucible of Transformation: The journey begins by carefully selecting the desired metal or alloy and placing it within a crucible, a specialized container designed to withstand extreme temperatures. Intense heat, generated by induction heating or other high-temperature furnaces, melts the metal, transforming it into a molten state, ready for the next stage of its transformation.
- Creating a Controlled Stream: Guiding the Molten Flow: The molten metal, now a shimmering pool of liquid potential, is meticulously guided through a precisely engineered nozzle positioned at the top of the atomization chamber. This controlled flow ensures a consistent and predictable stream of molten metal, crucial for achieving uniform particle size and distribution in the final powder.
- The Power of High-Velocity Gas: Atomization Unleashed: This is where the true magic of gas atomization unfolds. Jets of inert gas, typically argon or nitrogen, are strategically injected into the chamber at supersonic speeds, creating a powerful force that collides with the descending molten metal stream. This high-velocity impact overcomes the metal’s surface tension, shattering it into a myriad of tiny droplets, each a miniature replica of the original molten metal.
- Rapid Solidification: From Droplets to Powder Particles: As these droplets, propelled by the force of the gas jets, travel through the controlled environment of the chamber, they encounter a rapid decrease in temperature. This rapid cooling, combined with the inherent properties of the inert gas atmosphere, causes the droplets to solidify quickly, transforming from liquid metal to solid powder particles, each a tiny building block for future innovation.
- Powder Collection: Harvesting the Fruits of Atomization: The solidified metal powder, now cooled to a manageable temperature, settles at the bottom of the atomization chamber, ready to be collected and further processed. This collected powder, the culmination of the gas atomization process, is ready to be sieved, classified, and packaged, ready to empower industries with its unique properties and unlock a world of manufacturing possibilities.
Why Choose Gas Atomization? 7 Advantages That Set it Apart
Gas atomization isn’t just another method in the metal powder production playbook; it’s often the preferred method, thanks to a symphony of benefits that other techniques struggle to replicate. Let’s explore the seven pillars of its superiority:
1. Exceptional Powder Quality: The Foundation of Superior Performance
Gas atomization stands out for its ability to produce metal powders of exceptional quality, characterized by:
- Spherical Particle Shape: The Geometry of Flow: The rapid solidification that occurs within the controlled gas atmosphere of the atomization chamber promotes the formation of spherical powder particles. This spherical shape is highly desirable for powder flowability, ensuring smooth and consistent delivery during processing. It also enhances packing density, allowing for more particles to occupy a given volume, crucial for achieving dense and uniform microstructures during consolidation.
- Controlled Particle Size Distribution: Tailoring Properties with Precision: Gas atomization empowers manufacturers with precise control over the gas pressure and flow rate, critical parameters that directly influence the particle size distribution of the resulting powder. This control allows for fine-tuning the powder’s characteristics to meet specific application requirements, whether it’s creating fine powders for additive manufacturing or coarser powders for metal injection molding.
- High Purity: Preserving the Integrity of the Metal: The use of inert gases, such as argon or nitrogen, during the atomization process minimizes the risk of oxidation and contamination. This pristine environment ensures that the resulting metal powders retain their desired chemical composition and exhibit superior properties, crucial for applications demanding high performance and reliability.
2. Versatility in Metal Selection: From Everyday Metals to Exotic Alloys
Gas atomization isn’t confined to a limited repertoire of metals; it’s a versatile virtuoso capable of transforming a wide range of metals and alloys into valuable powders, including:
- Alüminyum: Lightweight and corrosion-resistant, aluminum powders find applications in aerospace, automotive, and packaging industries.
- Bakır: Known for its excellent electrical and thermal conductivity, copper powders are essential for electronics, electrical contacts, and heat exchangers.
- Tin: Used in solders, alloys, and coatings, tin powders are valued for their low melting point and corrosion resistance.
- Çelik: The workhorse of construction and manufacturing, steel powders find applications in automotive parts, construction materials, and tooling.
- Titanyum: Lightweight, strong, and biocompatible, titanium powders are used in aerospace components, medical implants, and sporting goods.
- Nickel-based Superalloys: Resistant to high temperatures and corrosion, these alloys are used in jet engines, gas turbines, and other demanding applications.
- Refractory Metals like Tungsten and Molybdenum: With extremely high melting points, these metals are used in high-temperature applications, such as lighting, electronics, and aerospace.
This remarkable versatility makes gas atomization an indispensable tool for producing powders tailored to specific applications, from the lightweight structures of aerospace to the demanding environments of power generation.
3. Scalability for Industrial Demands: From Grams to Tons of Innovation
Whether your needs call for a small batch of specialized powder for research and development or tons of material to fuel large-scale industrial production, gas atomization rises to the challenge with remarkable scalability.
Production Scale | Uygulama |
---|---|
Laboratory Scale | Research and development, prototyping, small-scale production of specialized alloys for niche applications where precise control and customization are paramount. |
Pilot Scale | Process optimization, material testing, production of limited quantities for market testing or specialized applications where larger volumes than lab scale are required. |
Industrial Scale | High-volume production for industries like automotive, aerospace, medical, and energy, where consistent quality and large quantities of metal powders are essential to meet demanding production schedules. |
4. Control Over Microstructure: Engineering Materials at the Atomic Level
Gas atomization’s ability to achieve rapid solidification rates unlocks a world of possibilities for engineering materials with unique microstructures that are challenging or even impossible to achieve through traditional casting methods. This level of control allows for tailoring material properties with exceptional precision, including:
- Geliştirilmiş Güç ve Sertlik: By controlling the cooling rate and solidification process, gas atomization can create finer grain structures within the metal powder particles, resulting in increased strength and hardness compared to conventionally processed materials.
- Geliştirilmiş Aşınma Direnci: The fine and uniform microstructures achievable with gas atomization contribute to enhanced wear resistance, making these powders ideal for applications subjected to friction and abrasion, such as cutting tools, engine components, and bearings.
- Increased Corrosion Resistance: The rapid solidification process can promote the formation of protective oxide layers or the homogeneous distribution of alloying elements, enhancing the material’s resistance to corrosion in harsh environments.
- Özel Manyetik Özellikler: By carefully controlling the composition and solidification parameters, gas atomization enables the production of metal powders with specific magnetic properties, crucial for applications in motors, sensors, and data storage devices.
5. Cost-Effectiveness for Demanding Applications: Balancing Performance and Value
While the initial investment for gas atomization equipment might be higher compared to some other powder production methods, its ability to produce high-quality powders with exceptional properties often translates into significant long-term cost savings. This value proposition is particularly compelling for demanding applications where material performance is paramount, such as:
- Havacılık ve Uzay Bileşenleri: Lightweight yet strong components are crucial for aircraft and spacecraft, and gas atomized powders enable the production of high-performance parts that meet stringent aerospace industry standards.
- Tıbbi İmplantlar: Biocompatible materials with excellent corrosion resistance and mechanical properties are essential for medical implants, and gas atomized powders offer the purity, biocompatibility, and performance required for these critical applications.
- Yüksek Performanslı Kesici Takımlar: Cutting tools made from gas atomized powders exhibit enhanced hardness, wear resistance, and toughness, leading to longer tool life, improved cutting performance, and reduced machining costs.
- Turbine Blades for Power Generation: Gas turbines operate at extreme temperatures and pressures, demanding materials with exceptional creep resistance and high-temperature strength. Gas atomized superalloy powders enable the production of turbine blades that can withstand these demanding conditions, ensuring efficient and reliable power generation.
6. Environmental Responsibility: Minimizing Waste and Emissions
In an era where environmental consciousness is paramount, gas atomization stands out as a relatively environmentally friendly process, especially when compared to other metal powder production methods. The use of inert gases minimizes the potential for oxidation, reducing the need for additional chemical processing and minimizing the generation of harmful byproducts. Additionally, the high material yield and minimal waste generation inherent to gas atomization contribute to a more sustainable manufacturing process, aligning with the growing demand for eco-conscious practices.
7. Enabling Advanced Manufacturing Technologies: The Future of Metal Fabrication
Gas atomized metal powders are the unsung heroes behind many advanced manufacturing technologies that are revolutionizing the way we design, prototype, and manufacture components. These technologies, which leverage the unique properties of these powders, include:
- Katmanlı Üretim (3D Baskı): This transformative technology builds three-dimensional objects layer by layer from a digital design, using metal powders as the building material. Gas atomized powders, with their spherical shape, controlled particle size distribution, and high purity, are ideal for additive manufacturing processes, enabling the creation of complex geometries and intricate designs with exceptional precision.
- Metal Enjeksiyon Kalıplama (MIM): MIM creates complex-shaped metal parts by injecting a mixture of fine metal powder and a binder into a mold. Gas atomized powders are well-suited for MIM due to their excellent flowability and ability to pack densely, resulting in high-quality, near-net-shape components with good dimensional accuracy.
- Sıcak İzostatik Presleme (HIP): This process consolidates metal powders into near-net-shape components with superior mechanical properties by applying high pressure and temperature in a controlled atmosphere. Gas atomized powders, with their high purity and fine microstructure, respond well to HIP, resulting in components with excellent density, strength, and fatigue resistance.
Frequently Asked Questions About Gas Atomization
1. What are the limitations of gas atomization in terms of powder production?
While gas atomization offers numerous advantages, it’s important to acknowledge its limitations:
- Minimum Particle Size: There’s a limit to how small the powder particles can be, typically around 1-10 micrometers. For applications requiring nano-sized particles, other methods might be more suitable.
- Ekipman Maliyeti: Gas atomization equipment can be capital-intensive, especially for large-scale production.
- Süreç Karmaşıklığı: Achieving and maintaining optimal powder characteristics require precise control over various process parameters.
2. How does gas atomization contribute to the advancement of additive manufacturing?
Gas atomization plays a crucial role in additive manufacturing by providing:
- Yüksek Kaliteli Tozlar: The spherical shape, controlled particle size distribution, and high purity of gas atomized powders are ideal for consistent and reliable additive manufacturing processes.
- Malzeme Çeşitliliği: The ability to atomize a wide range of metals and alloys expands the material choices available for additive manufacturing, enabling the creation of components with tailored properties.
- Improved Part Performance: The unique microstructures achievable with gas atomized powders can enhance the mechanical properties and performance of additively manufactured parts.
3. Can gas atomized powders be used for applications other than powder metallurgy?
Yes, gas atomized powders find applications beyond traditional powder metallurgy, including:
- Termal Sprey Kaplamalar: Creating protective coatings on surfaces to enhance wear resistance, corrosion resistance, or thermal properties.
- Sert Lehimleme ve Lehimleme: Used as filler metals in brazing and soldering applications due to their controlled particle size and flow characteristics.
- Powder Metallurgy Composites: Combined with other materials to create composite materials with enhanced properties.
4. How does the choice of inert gas affect the gas atomization process?
The choice of inert gas, typically argon or nitrogen, can influence:
- Toz Saflığı: Argon generally results in higher purity powders due to its lower reactivity.
- Cooling Rate: Helium, with its higher thermal conductivity, can lead to faster cooling rates and finer microstructures.
- Maliyet: Nitrogen is generally more cost-effective than argon or helium.
5. What are the future trends and developments in gas atomization technology?
The field of gas atomization continues to evolve, driven by:
- Improved Process Control: Advanced sensors and control systems enable finer control over process parameters, leading to more consistent powder quality.
- New Alloy Development: Research into atomizing new and advanced alloys expands the range of materials available for demanding applications.
- Increased Sustainability: Efforts to improve energy efficiency and reduce the environmental impact of gas atomization processes are ongoing.
Embracing the Future of Metal Powders: Gas Atomization Leads the Way
As industries continue to push the boundaries of material science, demanding lighter, stronger, and more complex metal components, gas atomization will undoubtedly play an increasingly vital role in shaping the future of manufacturing. Its ability to produce high-quality metal powders with tailored properties, exceptional purity, and controlled microstructures makes it an indispensable technology for industries ranging from the demanding environments of aerospace and the precision of medical devices to the efficiency of power generation and beyond.
By embracing the potential of gas atomization, businesses can unlock new levels of performance, efficiency, and sustainability, positioning themselves at the forefront of innovation in a world hungry for advanced materials and groundbreaking manufacturing solutions.