Haynes 188 Powder'ın Kısa Tarihçesi
Kökenleri ve Gelişimi
Haynes 188 toz, yüksek sıcaklıkta kobalt bazlı alaşım, 20. yüzyılın başlarına dayanan zengin bir geçmişe sahiptir. Gelişimi, özellikle havacılık ve enerji endüstrilerinde aşırı sıcaklıklara ve zorlu ortamlara dayanabilen malzemelere yönelik artan talepten kaynaklanmıştır.
Alaşımın kökenleri, kobalt bazlı alaşımların geliştirilmesinde öncü olan Union Carbide'ın Stellite Bölümü'ne kadar uzanmaktadır. 1950'lerin başında, Stellite'deki araştırmacılar üstün yüksek sıcaklık özelliklerine sahip alaşımlar oluşturmak için yeni bileşimler denemeye başladılar. Bu araştırma sonunda Haynes 188'in geliştirilmesine yol açtı.
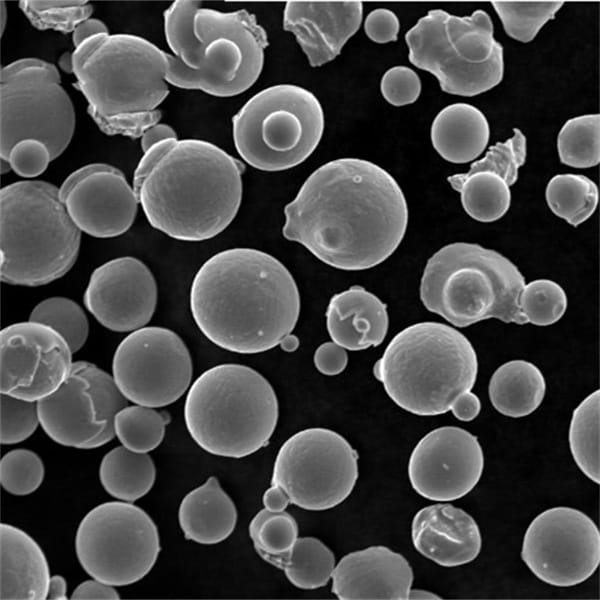
Önemli Yenilikler ve Kilometre Taşları
- Haynes 188 alaşımının kobalt bazlı bir süper alaşım olarak ilk geliştirilmesi.
- Karmaşık bileşenlerin üretimi için Haynes 188 toz metalurjisi tekniklerinin tanıtılması.
- Uygulamaların havacılık ve enerji sektörlerine doğru genişletilmesi.
- Performansı artırmak için alaşımın bileşiminde ve üretim süreçlerinde yapılan iyileştirmeler.
- Katmanlı üretim süreçlerinde Haynes 188 tozunun kullanımının artması.
- Yeni uygulamalar keşfetmek ve özellikleri geliştirmek için devam eden araştırma ve geliştirme.
Haynes'in Tarihindeki Kilometre Taşları 188 Toz
Haynes 188 tozu, başta havacılık ve enerji olmak üzere çeşitli endüstriler üzerinde önemli bir etkiye sahiptir. Olağanüstü yüksek sıcaklık özellikleri ve korozyon direnci, onu jet motorları, gaz türbinleri ve nükleer reaktörler gibi uygulamalardaki kritik bileşenler için vazgeçilmez bir malzeme haline getirmiştir. Yıllar içinde alaşım sürekli olarak geliştirilmiş ve iyileştirilmiş, böylece günümüzün zorlu teknolojik ortamına uygunluğu sağlanmıştır. Araştırma ve geliştirme çalışmaları ilerlemeye devam ettikçe, Haynes 188 tozunun malzeme bilimi ve mühendisliğinin geleceğini şekillendirmede daha da hayati bir rol oynaması beklenmektedir. Bileşim ve Kimyasal Yapı Haynes 188 tozu, olağanüstü yüksek sıcaklık özellikleriyle bilinen kobalt bazlı bir süper alaşımdır. Bileşimi tipik olarak şunları içerir: Haynes 188 Tozunun Tipik Bileşimi Haynes 188 tozu, zorlu uygulamalar için uygun olmasını sağlayan fiziksel özelliklerin bir kombinasyonunu sergiler: Yüksek Sıcaklıklara Karşı Olağanüstü Direnç Haynes 188 tozunun en ayırt edici özelliklerinden biri, yüksek sıcaklıklara karşı olağanüstü direncidir. Bunun nedeni, alaşımın yüzeyinde daha fazla oksidasyon ve korozyona karşı bir bariyer görevi gören koruyucu bir oksit tabakasının oluşmasıdır. Bu oksit tabakası yüksek sıcaklıklarda bile kararlı ve yapışkandır. Haynes 188 Tozunun Fiziksel Özellikleri Haynes 188 tozunun olağanüstü yüksek sıcaklık özellikleri, korozyon direnci ve mekanik mukavemeti, onu çok çeşitli endüstriyel uygulamalarda değerli bir malzeme haline getirmektedir. Çok yönlülüğü, aşağıdaki gibi bileşenlerde kullanılmasına yol açmıştır: Haynes 188 Powder Uygulamaları Haynes 188 tozu tipik olarak, döküm veya dövme gibi geleneksel metal işleme süreçlerine ihtiyaç duymadan bileşenler oluşturmak için metal tozlarının işlenmesini içeren toz metalurjisi teknikleri kullanılarak üretilir. Aşağıdakiler Haynes 188 tozu için yaygın üretim süreçleridir: Haynes 188 Tozu için Üretim Süreçleri Haynes 188 tozu, geniş bir uygulama yelpazesine sahip değerli bir malzeme olmaya devam etmektedir. Teknoloji ilerledikçe ve yeni zorluklar ortaya çıktıkça, devam eden araştırma ve geliştirme çabaları yeni uygulamaları keşfetmeye, özellikleri geliştirmeye ve üretim süreçlerini iyileştirmeye odaklanmaktadır. Haynes 188 Toz Teknolojisinde Potansiyel Gelişmeler Gelişen Uygulamalar ve Pazar Fırsatları Araştırma ve Geliştirme Çalışmaları Araştırma ve geliştirme çalışmaları ilerlemeye devam ettikçe, Haynes 188 tozunun malzeme bilimi ve mühendisliğinin geleceğini şekillendirmede giderek daha önemli bir rol oynaması beklenmektedir. Ortaya çıkan zorlukları ele alarak ve yeni fırsatları keşfederek, bu çok yönlü alaşım teknolojik ilerlemelere ve sürdürülebilir kalkınmaya katkıda bulunmaya devam edecektir. S1: Haynes 188 tozunu zorlu uygulamalar için yüksek performanslı bir malzeme olarak öne çıkaran nedir? A1: Haynes 188 tozu, aşırı koşullara dayanmak üzere özel olarak tasarlanmış kobalt bazlı bir süper alaşımdır. Olağanüstü mukavemeti ve 1800°F'yi (982°C) bile aşan yüksek sıcaklıklarda oksidasyona karşı olağanüstü direnci ile öne çıkar. Bu özellikler, bileşenlerin düzenli olarak aşırı ısı ve aşındırıcı ortamlarla karşı karşıya kaldığı havacılık, gaz türbinleri ve endüstriyel fırınlar gibi endüstrilerdeki zorlu uygulamalar için en iyi seçim olmasını sağlar. S2: Haynes 188 tozunun benzersiz özelliklerine katkıda bulunan temel bileşim unsurları nelerdir? A2: Haynes 188'in olağanüstü performansı, dikkatle dengelenmiş bileşimine atfedilebilir. Alaşım temel olarak kobalt, nikel, krom ve tungstenden oluşur. Bu elementler sinerjik bir şekilde çalışarak alaşıma etkileyici mukavemet, oksidasyon direnci ve önemli bir bozulma veya çarpılma olmaksızın yüksek sıcaklıklara uzun süre maruz kalmaya dayanma kabiliyeti sağlar. S3: Haynes 188 toz boyalarını etkili bir şekilde uygulamak için önerilen termal sprey işlemleri nelerdir? A3: Optimum kaplama performansı elde etmek için uygun termal püskürtme işleminin seçilmesi çok önemlidir. Haynes 188 tozu için Yüksek Hızlı Oksijen Yakıtı (HVOF) ve Plazma Transferli Ark (PTA) kaynağı tercih edilen yöntemlerdir. Bu teknikler, toz partiküllerinin tamamen erimesini sağlamak için yeterli ısı girdisi sağlayarak üstün yapışma ve istenen özelliklere sahip yoğun, iyi bağlanmış kaplamalarla sonuçlanır. S4: Haynes 188 tozu hangi endüstrilerde ve uygulamalarda yaygın olarak kullanılır? A4: Haynes 188 tozunun olağanüstü yüksek sıcaklık özellikleri, onu aşırı koşullarla uğraşan endüstrilerde oldukça aranan bir ürün haline getirmektedir. Havacılıkta, yanma kutuları, geçiş kanalları ve art yakıcı parçalar gibi kritik bileşenler için yaygın olarak kullanılır. Malzeme ayrıca endüstriyel gaz türbinlerinde, özellikle yanma gömlekleri, geçiş parçaları ve aşırı sıcaklıklara ve aşındırıcı gazlara maruz kalan diğer sıcak bölüm bileşenlerinin üretiminde yaygın olarak kullanılmaktadır. S5: Haynes 188 kaplamalarının performansını daha da artırmak için tipik olarak hangi kaplama sonrası işlemler uygulanmaktadır? A5: Haynes 188 kaplamaları püskürtüldüklerinde mükemmel özellikler sergilerken, kaplama sonrası işlemler performanslarını ve uzun ömürlülüklerini daha da artırabilir. Isıl işlemler genellikle kaplama içindeki artık gerilmeleri gidermek ve gelişmiş performans için mikro yapısını optimize etmek için kullanılır. Bu işlemler, özel uygulamaya ve istenen özelliklere göre uyarlanmış kontrollü ısıtma ve soğutma döngülerini içerir ve kaplamanın zorlu çalışma koşulları altında maksimum performans ve dayanıklılık sunmasını sağlar.
Yıl
Etkinlik
1950s
Haynes 188 alaşımının ilk geliştirilmesi
1960s
Toz metalurjisi tekniklerinin tanıtılması
1970s
Uygulamaların genişletilmesi
1980s
Bileşim ve üretim iyileştirmeleri
1990s
Katmanlı üretimde artan kullanım
2000'ler-günümüz
Devam eden araştırma ve geliştirme
Haynes 188 Tozunun Eşsiz Özellikleri
Element
Ağırlık Yüzdesi
Kobalt
55-60
Nikel
15-20
Krom
18-22
Tungsten
10-12
Molibden
6-8
Karbon
0.10-0.20
Bor
0.03-0.05
Diğerleri
<1
Mülkiyet
Değer
Erime noktası
~1450°C (2640°F)
Yoğunluk
~8,4 g/cm³
Sertlik
~350-400 Brinell
Çekme mukavemeti
Oda sıcaklığında ~1000 MPa (145.000 psi)
Sürünme direnci
Yüksek sıcaklıklarda mükemmel
Yorulma direnci
Yüksek sıcaklıklarda iyi
Aşınma direnci
Mükemmel
Haynes 188 Tozunun Endüstrideki Uygulamaları
Uzay ve Havacılık
Kimyasal İşleme
Enerji Üretimi
Diğer Sanayi Sektörleri
Endüstri
Uygulamalar
Uzay ve Havacılık
Türbin kanatları, roket nozulları, yanma odaları
Kimyasal İşleme
Reaktörler, vanalar, ısı eşanjörleri
Enerji Üretimi
Nükleer enerji santralleri, fosil yakıt yanması
Diğer Sanayi Sektörleri
Petrokimya endüstrisi, otomotiv endüstrisi, tıbbi cihazlar
Haynes 188 Tozu için Üretim Süreçleri
Toz Üretimi
Konsolidasyon
Süreç
Açıklama
Atomizasyon
Alaşımın eritilmesi ve bir soğutma odasına püskürtülmesi
Plazma püskürtme
Alaşımın bir plazma torcu kullanılarak eritilmesi ve bir alt tabaka üzerine püskürtülmesi
Mekanik alaşımlama
Alaşım elementlerinin öğütülmesi ve harmanlanması
Sıcak presleme
Tozun yüksek sıcaklık ve basınçta sıkıştırılması
Sinterleme
Parçacıkları birbirine bağlamak için tozun ısıtılması
Gelecek Trendler ve Yenilikler
Haynes 188 Powder: En Önemli 5 Sorunuz Yanıtlandı
Geniş Kobalt Bazlı Toz yelpazesi hakkında daha fazla bilgi edinmek isterseniz, lütfen tablodaki isimlere tıklayın :