Production Methods of WMoTaNbZr Powder
WMoTaNbZr powder, a refractory metal alloy with exceptional properties, has gained significant attention in various industries. Its unique combination of high melting point, excellent corrosion resistance, and outstanding mechanical properties makes it a valuable material for applications ranging from aerospace and electronics to energy storage. To meet the growing demand for this versatile powder, several production methods have been developed. This chapter will delve into the most common techniques used to manufacture WMoTaNbZr powder, highlighting their advantages, limitations, and suitability for different applications.
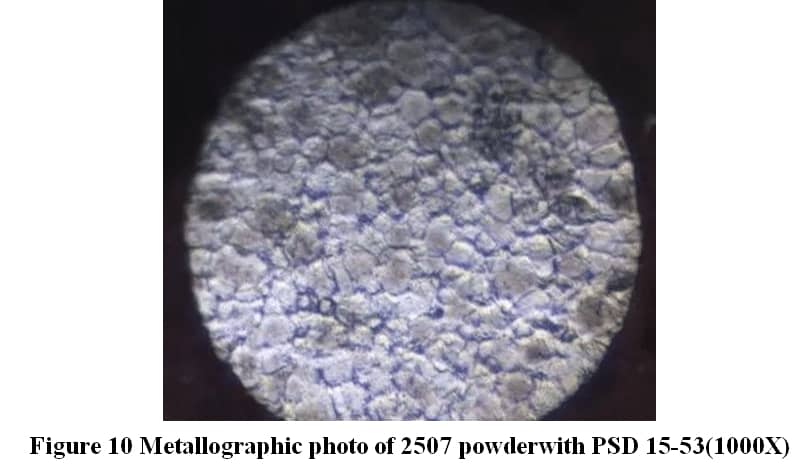
Toz Metalurjisi
Powder metallurgy (PM) is a widely used technique for producing WMoTaNbZr powder. It involves the consolidation of metal powders into desired shapes through a series of processes. The steps typically include:
- The starting materials, W, Mo, Ta, Nb, and Zr, are obtained in powder form. These powders can be produced using various methods, such as atomization, mechanical alloying, or chemical reduction.
- The individual powders are blended in the desired proportions to achieve the target composition of WMoTaNbZr.
- The mixed powders are compressed into green compacts using high pressure. This process forms the basic shape of the final product.
- The green compacts are heated to a high temperature in a controlled atmosphere. During sintering, the powder particles bond together to form a solid structure.
- PM can produce a wide range of shapes and sizes, making it suitable for various applications.
- The powder metallurgy process can yield high-purity WMoTaNbZr powder.
- PM can ensure consistent properties throughout the final product.
- PM can be relatively expensive, especially for large-scale production.
- PM products may have residual porosity, which can affect their mechanical properties.
Fiziksel Buhar Biriktirme (PVD)
PVD is another method used to produce WMoTaNbZr powder. In PVD, the metal is vaporized and deposited onto a substrate, forming a thin film. The deposited film can then be ground or crushed to obtain the desired powder. Common PVD techniques include:
- A target material is bombarded with ions, causing atoms to be ejected and deposited onto a substrate.
- The metal is heated to a high temperature, causing it to vaporize and condense on a substrate.
- PVD can produce very pure WMoTaNbZr powder.
- PVD can yield fine-grained powder with a narrow particle size distribution.
- PVD can ensure consistent properties throughout the powder.
- PVD is generally a slow process, making it less suitable for large-scale production.
- PVD can be expensive due to the specialized equipment required.
Kimyasal Buhar Biriktirme (CVD)
CVD is a process where a gaseous compound is decomposed onto a heated substrate, forming a solid deposit. In the case of WMoTaNbZr powder, the gaseous precursors can be metal halides or organometallic compounds.
- CVD can produce high-purity WMoTaNbZr powder.
- CVD can ensure consistent properties throughout the powder.
- CVD can be used to produce powder with complex shapes or coatings.
- CVD can be expensive due to the specialized equipment and precursors required.
- Some CVD processes involve the use of hazardous gases.
Comparison of Production Methods for WMoTaNbZr Powder
To ensure the quality and performance of WMoTaNbZr powder, it is essential to thoroughly characterize and analyze its properties. This chapter will discuss various techniques used to assess the microstructure, chemical composition, mechanical properties, and thermal properties of WMoTaNbZr powder. The microstructure of WMoTaNbZr powder plays a crucial role in determining its physical and mechanical properties. Techniques used to characterize the microstructure include: The chemical composition of WMoTaNbZr powder is critical for its performance. Techniques used to analyze the chemical composition include: The mechanical properties of WMoTaNbZr powder, such as hardness, strength, and ductility, are essential for its applications. Techniques used to measure mechanical properties include: The thermal properties of WMoTaNbZr powder, such as melting point and thermal conductivity, are important for applications involving high temperatures. Techniques used to measure thermal properties include: Characterization Techniques for WMoTaNbZr Powder WMoTaNbZr powder, with its unique combination of properties, has found numerous applications in the field of advanced materials. Its high melting point, excellent corrosion resistance, and outstanding mechanical properties make it a valuable material for various industries. This chapter will explore some of the key applications of WMoTaNbZr powder in advanced materials. WMoTaNbZr powder can be used to create protective coatings on various substrates, providing enhanced wear resistance, corrosion resistance, and thermal protection. These coatings are particularly valuable in applications such as: WMoTaNbZr powder is a promising material for additive manufacturing (3D printing) due to its high melting point and excellent mechanical properties. It can be used to produce complex components with intricate geometries and high strength-to-weight ratios. Applications include: WMoTaNbZr powder can be used to produce various electronic components and devices, including: WMoTaNbZr powder is used in a variety of applications in the aerospace and defense industries, such as: WMoTaNbZr powder has potential applications in energy storage and conversion technologies. For example, it can be used in: Applications of WMoTaNbZr Powder in Advanced Materials Despite its promising applications, the development and commercialization of WMoTaNbZr powder face several challenges. This chapter will discuss some of the key obstacles and outline potential research directions to address these issues. One of the major challenges associated with WMoTaNbZr powder is its relatively high cost. The production of this refractory metal alloy requires specialized equipment and high-temperature processing, which can significantly increase manufacturing costs. Additionally, scaling up production to meet the growing demand can be difficult due to the complex nature of the manufacturing processes. The production and use of WMoTaNbZr powder can have environmental implications, particularly in terms of energy consumption and emissions. The high temperatures required for processing can lead to significant energy consumption, while the release of hazardous materials during production and use can pose environmental risks. While WMoTaNbZr powder has found applications in various industries, there is a need for continuous research and development to identify new and emerging applications. Expanding the market for this material can help drive demand and stimulate further innovation. To fully understand the properties and behavior of WMoTaNbZr powder, it is essential to have advanced characterization and analysis techniques. Continued research and development in this area can provide valuable insights for improving the performance and reliability of this material. Challenges and Future Research Directions for WMoTaNbZr Powder
Yöntem
Avantajlar
Sınırlamalar
Toz Metalurjisi
Versatility, high purity, uniformity
Cost, porosity
Fiziksel Buhar Biriktirme (PVD)
High purity, fine particle size, uniformity
Low production rate, cost
Kimyasal Buhar Biriktirme (CVD)
High purity, uniformity, complex shapes
Cost, environmental concerns
Characterization and Analysis of WMoTaNbZr Powder
Microstructure and Particle Size Distribution
Chemical Composition and Purity
Mekanik Özellikler
Termal Özellikler
Mülkiyet
Teknikler
Microstructure and Particle Size Distribution
SEM, TEM, AFM, Particle Size Analysis
Chemical Composition and Purity
ICP-MS, XRF, EDX
Mekanik Özellikler
Microhardness Testing, Tensile Testing, Compression Testing
Termal Özellikler
DSC, Thermal Conductivity Measurement
Applications of WMoTaNbZr Powder in Advanced Materials
Coatings and Protective Layers
Katmanlı Üretim (3D Baskı)
Electronic Components and Devices
Aerospace and Defense Industries
Energy Storage and Conversion
Uygulama
Avantajlar
Coatings and Protective Layers
Wear resistance, corrosion resistance, thermal protection
Katmanlı Üretim
Complex shapes, high strength-to-weight ratio
Electronic Components and Devices
High stability, low temperature coefficient, excellent reliability
Aerospace and Defense Industries
High temperature resistance, lightweight, heat resistance
Energy Storage and Conversion
Improved performance, durability, efficiency
Challenges and Future Research Directions
Cost and Scalability
Environmental Impact and Sustainability
Development of New Applications and Markets
Advancements in Characterization and Analysis Techniques
Meydan Okuma
Geleceğe Yönelik Araştırma
Cost and Scalability
Develop more efficient production methods, identify lower-cost raw materials
Environmental Impact and Sustainability
Explore sustainable production processes, conduct environmental assessments
Development of New Applications and Markets
Investigate new application areas, collaborate with industry partners
Advancements in Characterization and Analysis Techniques
Develop new characterization techniques, improve existing methods
Geniş Yüksek Entropi Alaşımlı Toz yelpazesi hakkında daha fazla bilgi edinmek isterseniz, lütfen tablodaki isimlere tıklayın :
Paylaş
Xmetto Technology Co, LTD, merkezi Qingdao, Çin'de bulunan lider bir katmanlı üretim çözümleri sağlayıcısıdır. Şirketimiz, endüstriyel uygulamalar için 3D baskı ekipmanları ve yüksek performanslı metal tozları konusunda uzmanlaşmıştır.
İşletmeniz için en iyi fiyatı ve özelleştirilmiş Çözümü almak için sorgulayın!
İlgili Makaleler
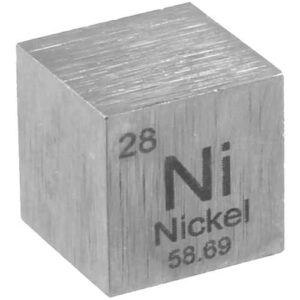
10 Saf Nikel Hakkında Şaşırtıcı Gerçekler: Özelliklerini ve Kullanım Alanlarını Keşfedin
Giriş: Saf Nikelin Çok Yönlülüğünü Ortaya Çıkarmak Olağanüstü korozyon direnci, mukavemeti ve yüksek erime noktası ile tanınan gümüşi beyaz bir metal olan saf nikel kritik bir rol oynamaktadır.
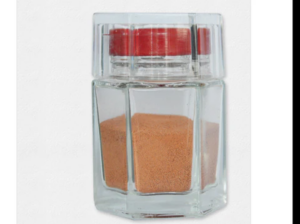
Bakır Esaslı Toz: Teknolojide 5 Şaşırtıcı Kullanım Alanı
Giriş: Bakır ile Olasılıklar Dünyasının Kilidini Açmak Antik aletlerden modern elektronik cihazlara kadar bakır, insan uygarlığının şekillenmesinde çok önemli bir rol oynamıştır. Bugün, bakır